
Rheonics passes surveillance audits for ATEX & IECEx after relocation to new facility
Rheonics – Switzerland division recently relocated to a new facility in order to expand and streamline its operations.
The address for the new facility is as follows:
Rheonics GmbH
Klosterstrasse 19
8406, Winterthur
Switzerland
Updates on ATEX, IECEx certifications
After relocating to a new facility, Rheonics successfully passed the surveillance audits and is pleased to announce the release of its new ATEX & IECEx certifications. The certifications project started with the goal to better serve our worldwide customers, in broad range of industries. Rheonics GmbH facility has successfully implemented and put to practice a Quality Management System (QMS) along the requirements of ISO 80079-34 & ISO 9001.
As a long time manufacturer of fluid-sensing solutions, Rheonics is continuously identifying and designing new solutions and protections that our customers will trust in their hazardous and explosive locations.
ATEX & IECEx Compliance
Rheonics offers intrinsically safe sensors certified by ATEX and IECEx for use in hazardous environments. These sensors comply with the essential health and safety requirements relating to the design and construction of equipment and protective systems intended for use in potentially explosive atmospheres.
The intrinsically safe and explosion proof certifications held by Rheonics also allows for customization of an existing sensor, allowing our customers to avoid the time and costs associated with identifying and testing an alternative. Custom sensors can be provided for applications that require one unit up to thousands of units; with lead-times of weeks versus months.
Rheonics SRV & SRD are both ATEX and IECEx certified by TÜV Rheinland.
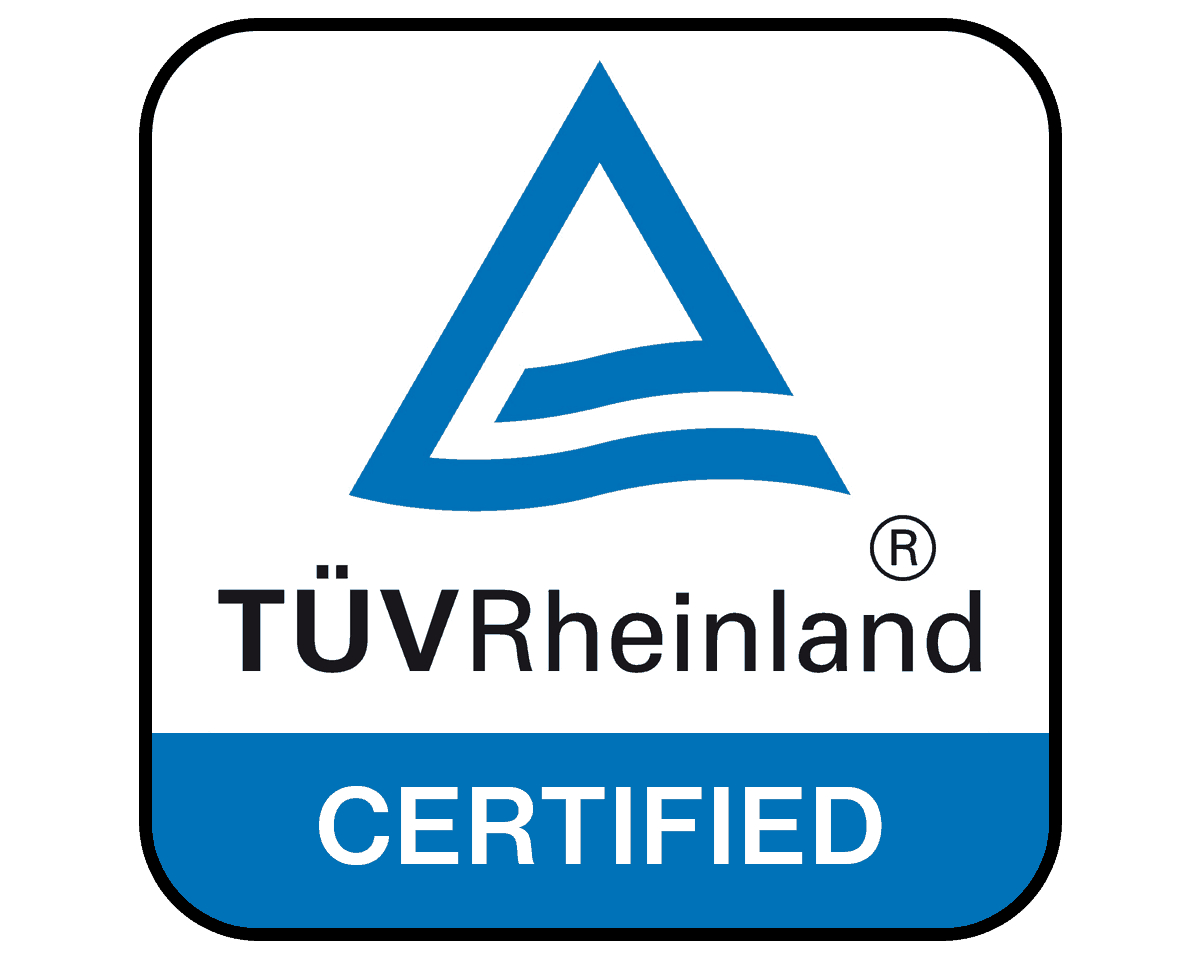
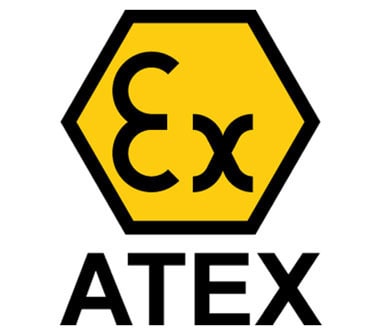
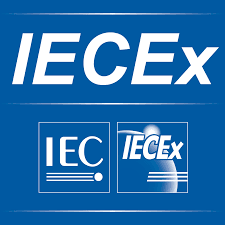
Certified Products
- Wide range viscosity measurement (also density with SRD) with built in fluid temperature measurement
- Hermetically sealed, all 316L stainless steel wetted parts
- Stable and repeatable measurements in non-Newtonian fluids like paints and coatings
- Small form-factor for simple installation in existing flow lines and nozzle heads
- Easy integration with existing data acquisition systems using digital and analog data communication
- Smart self-detection of sensing element cleanliness, easy to clean and verify calibration
Sensor Description and Installation conditions
Rheonics SRV sensors are used to measure and control the viscosity of fluids, mainly under process conditions. Rheonics SRD sensors measure, in addition, fluid density as well as true dynamic and kinematic viscosity. Each sensor has a symmetric torsional resonator as its sensitive element. The effect of the fluid in which it is immersed on its resonant response – its resonant frequency and damping – is measured and interpreted by the electronics unit with which it is supplied.
Both of these devices, hereafter referred to collectively as “SR” sensors, are delivered in a version that is intrinsically safe. That means that as long as the sensors are installed and operated as specified in the EX manual, they are incapable of igniting explosive atmospheres in which they operate, provided they are operated within the envelope of parameters described in the EX manual.
Each Rheonics SR sensor is delivered paired with an electronics unit that both operates the sensor and transmits its measurement values over one of a variety of interfaces. When operating Rheonics SR sensors in a hazardous area, one or more Zener diode barriers must be installed between the Rheonics SR sensor and its electronics unit. This barrier serves to limit the amount of current and voltage available to the sensor in case of a fault in its electronics unit and/or within the sensor itself.
The Zener diode barriers themselves must be situated either outside of any hazardous zone, or in the zone specified by the manufacturers as safe for the barriers. The Rheonics SR sensor’s electronics unit must be situated outside the hazardous zone.
Area classifications
Zone 0: Zone 0 is an area in which an explosive atmosphere is present continuously for long periods of time or will frequently occur.
Zone 1: Zone 1 is an area in which an explosive atmosphere is likely to occur occasionally in normal operation. It may exist because of repair, maintenance operations, or leakage.
Zone 2: Zone 2 is a place in which an explosive atmosphere is not likely to occur in normal operation but, if it does occur, will persist for a short period only. These areas only become hazardous in case of an accident or some unusual operating condition.
Industries and Applications
Some of the industries that are covered by our EX-certified products are the following:
- Oil + Gas refineries, Off-shore platform rigs and processing plants
- Automotive refueling stations or petrol/gas stations
- Chemical processing plants
- Coal mining
- Printing industries, paper and textiles
- Aviation, refueling and hangars
- Gas pipelines and distribution centers
- Sugar refineries
- Metal surface grinding, especially aluminum dusts and particles.
- Surface coating industries
- Waste treatment, sewerage plants
Examples of Applications in which Rheonics EX Sensors are deployed
Using real-time viscosity measurements in refinery operations for greater efficiency, agility and profitability
Processes in refineries where viscosity & density measurements and management play central role in refinery operations are the following: Accurate…
Wastewater management in beverage and food processing with inline viscosity monitoring
Food and beverage industry is one of the key industrial segments and major contributor to global economic and societal growth…
Monitoring and controlling viscosity of wire enamel in coating process
The global electrical insulation coatings market size in 2015 was USD 2 billion and is expected to grow significantly in…
Pharmaceutical printing process control
Product marking has come under increased scrutiny in the pharmaceutical industry due to pressure from three factors: regulations, aesthetics, and…
Downhole DV measurements in LWD, MWD, Wireline tools
The engineering of well logging sensors into the drill collars is simulating a revolution in logging and drilling. LWD, MWD…
Optimizing flexographic, gravure and corrugated printing applications through inline viscosity monitoring and control
Printing presses have numerous applications – newspapers, magazines, catalogues, packaging and labels. The global printing industry is forecast to reach…
Mud Weight Monitoring
As a part of the industry’s drive for continuous cost-effectiveness, drilling fluid performance and management have come under closer scrutiny…
Real-time engine oil condition monitoring
One of the largest areas of innovation and R&D in the automobile industry is the engine oil condition monitoring. Rapid…
Automotive painting and coating quality control and optimization
Through all the advancement in automotive design and manufacturing over the years, there has been one constant – vehicle’s aesthetics…
Battery production – Slurry Mixing and Coating
Lithium batteries keep both essentials and comfort of modern life running with safety and reliability. They have a long list…
Certificates and QANs
Here is the list of updated certificates available for viewing/download with the address of the new manufacturing facility.
Title | Summary | Link | Type |
---|---|---|---|
Certificate – ATEX Quality Assurance Notification (QAN) – German | ATEX-QAN (Quality Assurance Notification) in German – Requirements according to directive 2014/34/EU have been fulfilled | ||
Certificate – ATEX Quality Assurance Notification (QAN) – English | ATEX-QAN (Quality Assurance Notification) in English – Requirements according to directive 2014/34/EU have been fulfilled. | ||
Declaration of Conformity – CE Declaration of Conformity according to directive 2014/34/EU (ATEX) for SRV & SRD | Rheonics’ EU Declaration of Conformity according to directive 2014/34/EU (ATEX) and relevant standards for SRV, SRV-FPC, SRD & SRD-FPC | ||
Certificate – ATEX Certificate for SRV & SRD – Issue 02 | Certificate for Equipment and Protective Systems intended for use in Potentially Explosive Atmosphere – Directive 2014/34/EU – Issue 02 | ||
Certificate – IECEx Certificate of Conformity for SRV & SRD – Issue 02 | This certificate is issued as verification that a sample(s), representative of production, was assessed and tested and found to comply with the IEC Standards listed in the Certificate Issue 02 |