Battery production – Density and Viscosity Quality Control of Battery Slurry Mixing and Coating Lines
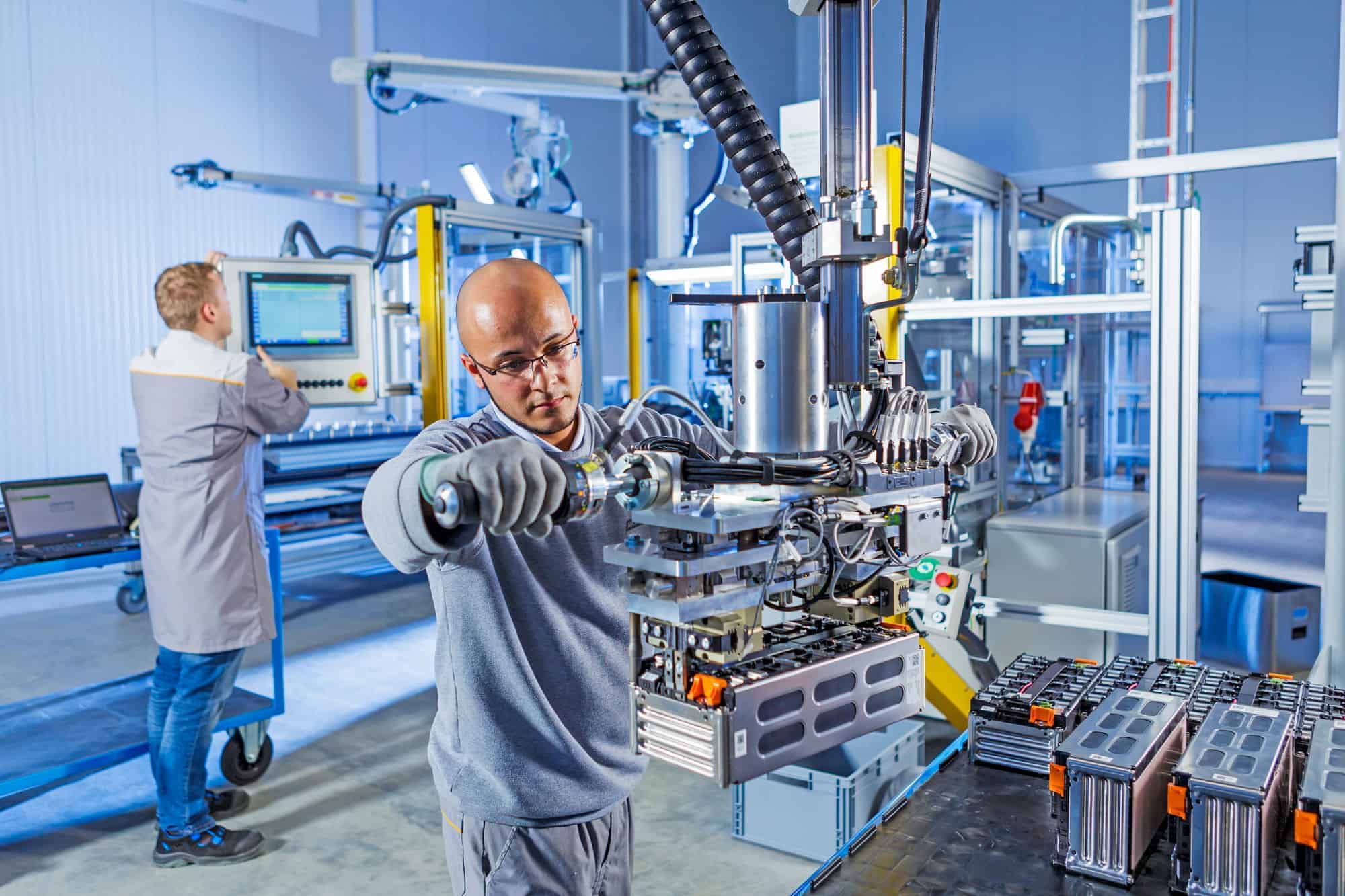
Introduction
Lithium batteries keep both essentials and comfort of modern life running with safety and reliability. They have a long list of real-world applications – consumer electronics power, Electric Vehicle (EV) power, solar power storage, UPS, alarm systems in remote locations, mobility equipment and portable power packs. Currently, this battery technology is on the verge of carrying the revolution in road transport and energy storage of renewable energy. Battery performance and lifetime constitute a bottleneck for electric vehicles as well as stationary electric energy storage systems to penetrate the market. One thing is already perfectly clear: the processes throughout battery manufacturing operation need to be optimised in order to achieve target properties and sustain quality.
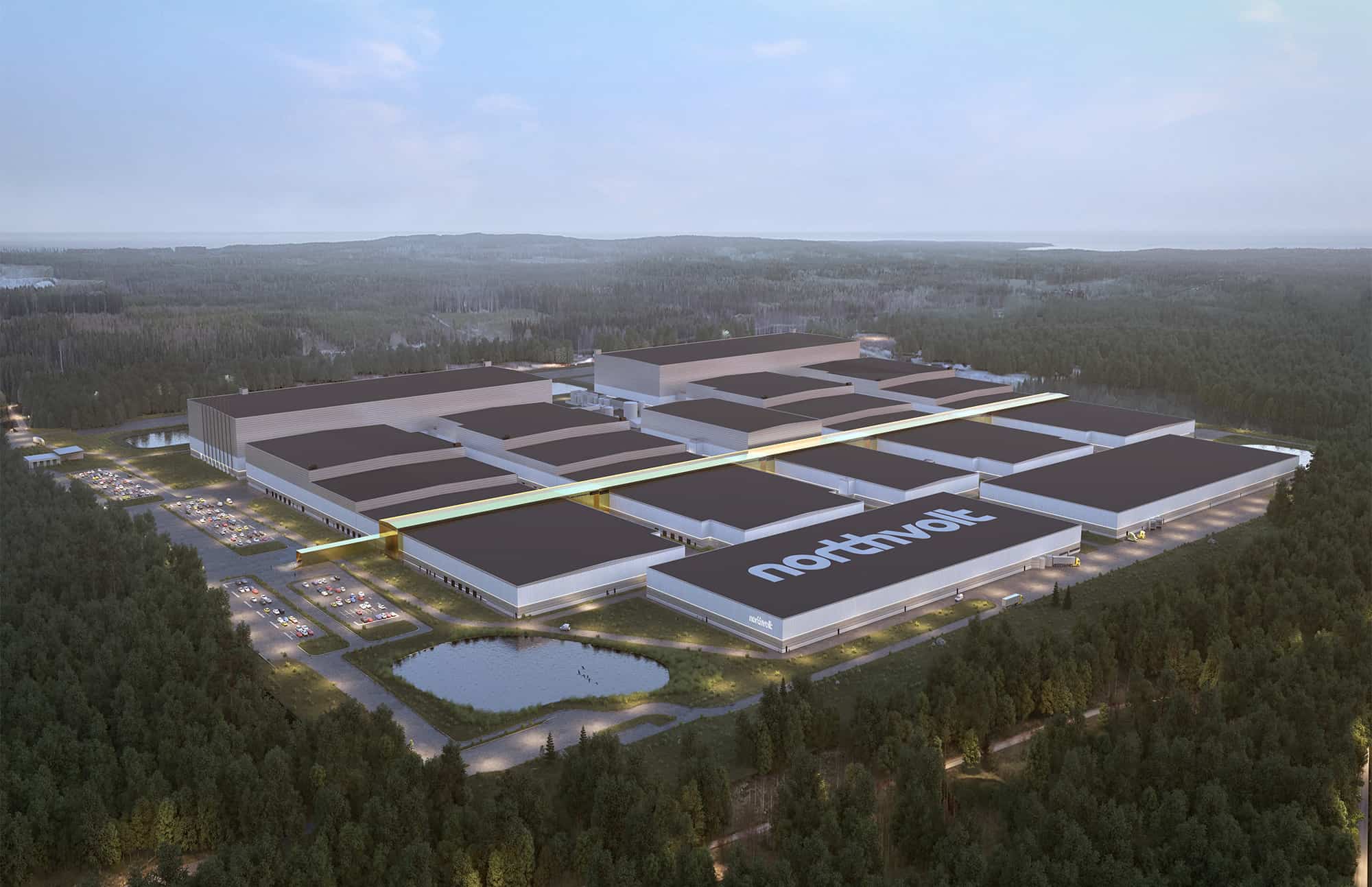
Goals of battery producers
Sustainability – Reduced consumption of energy and raw materials
Battery manufacturers aim to reduce their environmental footprint as much as possible. A circular manufacturing approach, using clean energy to power battery cell manufacturing, and conscientious sourcing of raw materials are required.
Some are looking for ways to recycle end-of-life batteries and recycle the materials back into manufacturing to “close the loop”.
Stable, competitive production process
All battery solutions have the cell as the “least common denominator”. For higher capacity, a battery is made up of many small cells connected in series and parallel. In the world of battery manufacturing, this is especially true – no battery pack is stronger than its weakest cell.
There can be a significant difference in the cycle life and quality of the best and the worst cells. By repeating and stabilizing manufacturing processes, battery solutions in demanding applications will be of higher quality.
Increasing production capacity
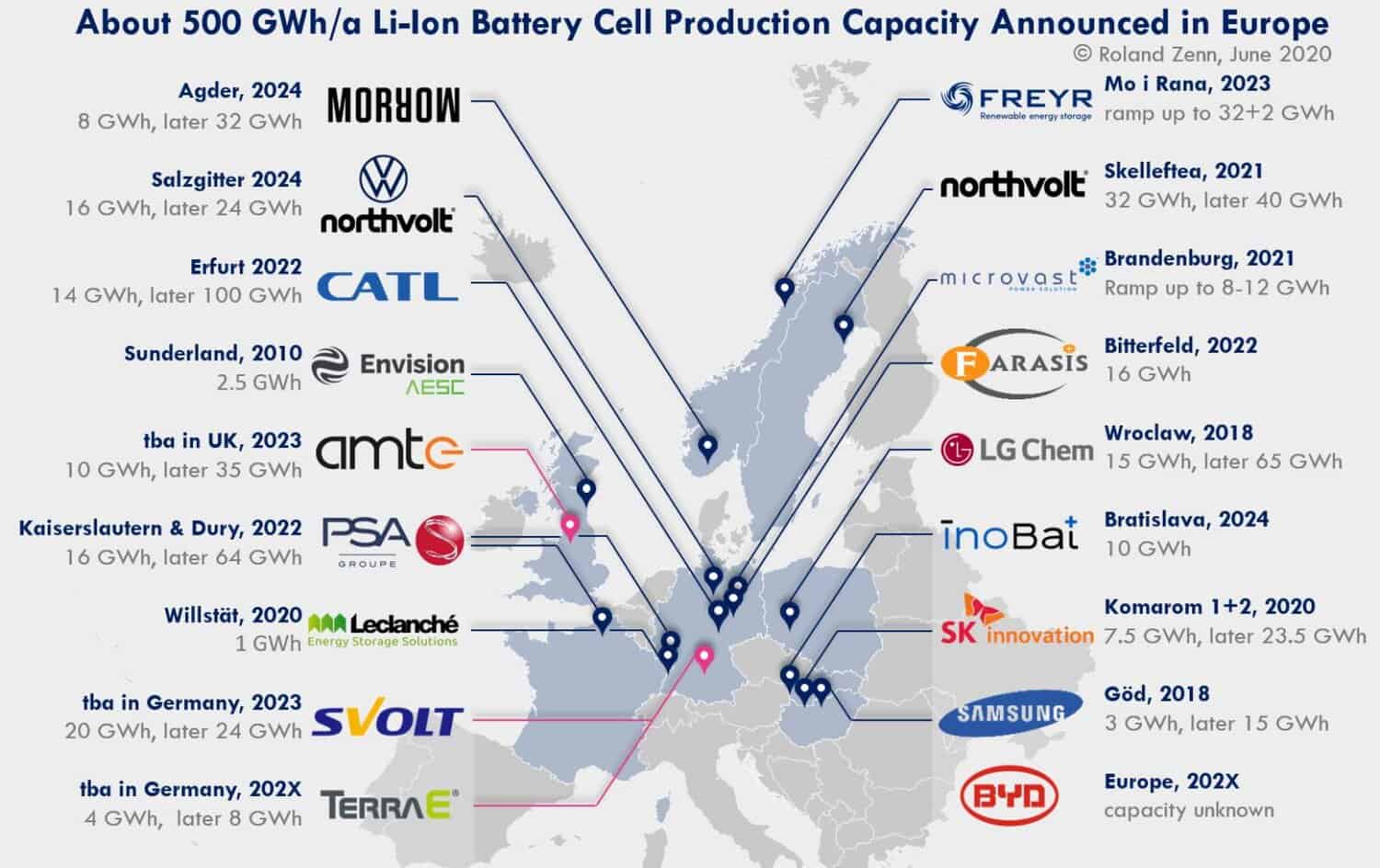
Battery GigaFactories in Europe | https://www.orovel.net/insights/li-on-battery-gigafactories-in-europe-june-2020
Battery Production
The first step in the assembly of cell is the deposition of a suspension containing the active material, conducting material and polymeric binder in a solvent on to a copper film or an aluminium film (slurry preparation and coating). This is followed by drying, calendaring and sizing of the electrodes. To deliver desirable electrochemical performance, the multistep manufacturing process of battery electrodes need to be closely controlled. Slurries are a very complex suspension system containing large percentage of solid particles of different chemicals, sizes and shapes in a highly viscous media. A thorough mixing of slurry is essential for homogeneity. Rheological properties of slurries affect important attributes: slurry stability, ease of mixing and coating performance, which impact finished electrodes. Composition and applied processing conditions can have an impact on the rheology of the resulting suspension. Density and viscosity quantify flow properties and characterise the degree of structure within the sample and the extent to which solid- or liquid-like behaviour dominates. In electrode manufacturing process, viscosity of in-process constituents is especially significant and plays a critical role battery fabrication processes such as coating. Viscosity of the polymeric binder solution affects coating performance. It influences the ease with which the powders are dispersed within it, the power required for mixing and the speed of application of uniform coating. The Porous Electrode Theory(PET) suggests the relevance of positive electrode density on overall performance of Lithium-ion battery cells, validated by experiments. Cells with high positive electrode density show a slightly higher discharge capacity at low current rates but at high current rates, cells with a low positive electrode density show a better performance.
Steps in the battery manufacturing process
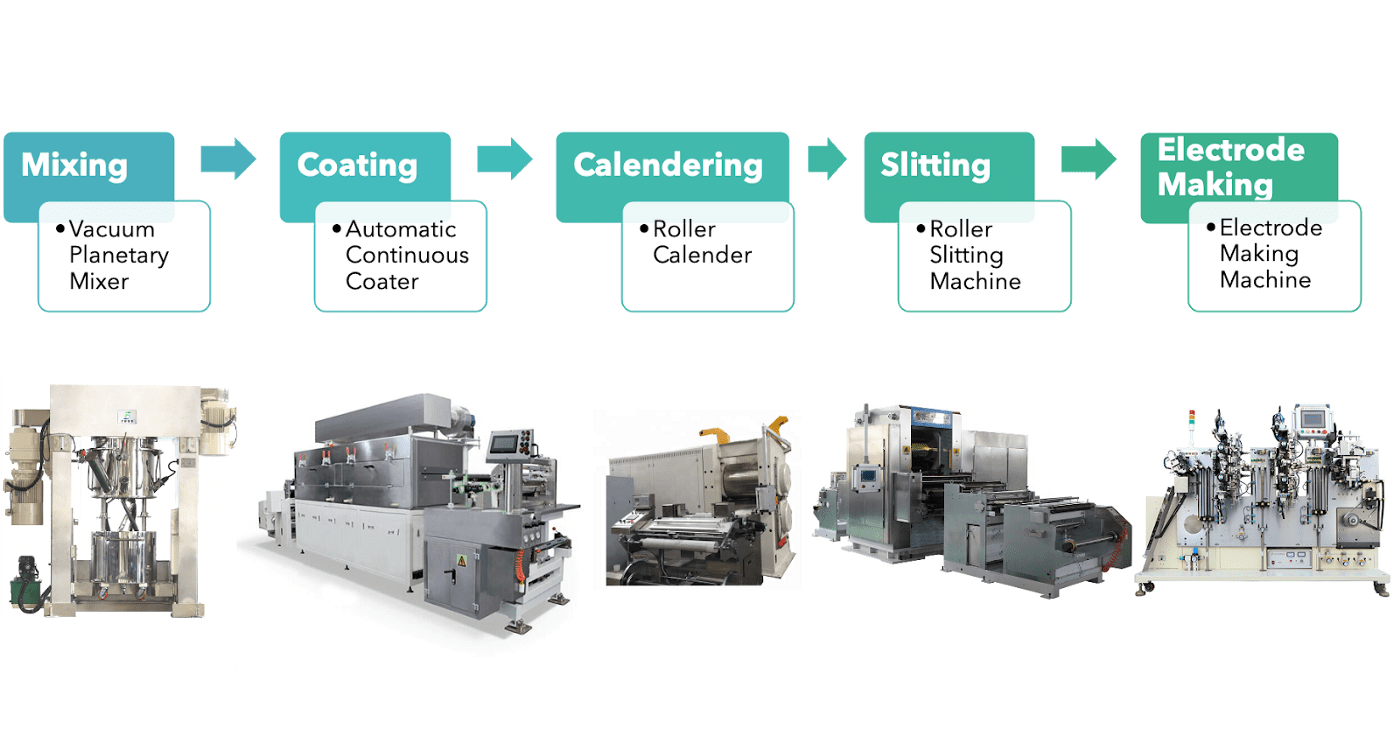
BatteryBits on Medium | https://medium.com/batterybits/battery-manufacturing-basics-from-catls-cell-production-line-part-1-d6bb6aa0b499
Problem Statement
The dispersion of slurry constituents and their states, which determine the physical properties of slurries, are critical in design and development of mixing and coating processes for producing lithium ion batteries.
- Conventional production methods for Lithium-Ion Battery (LIB) electrode slurries are based on batch or quasi continuous processes.
- Continuous mixing process consists of controlled dosing of all the liquid and solid components and micro distribution of the solid particles in the liquid phase.
The sensitive chemistry of the cells means that time and cost savings cannot come at the expense of quality, which needs to remain very high. Controlling density and viscosity to optimise the batch processes ensures consistency, quality and significant material cost savings. Process control and traceability of the continuous mixing process can be improved with inline monitoring and control of density and viscosity. Automation supported by in-line integration makes it possible to optimise all the processes throughout the production lines to make battery manufacturing faster to meet growing demands.
Process Challenges
Monitoring and controlling of important electrode slurry parameters – density and viscosity are extremely relevant in development and manufacture of high performance electrodes and its fabrication. Key reasons:
- During mixing of slurry, unneeded agitation deteriorates and degrades internal structures with time. The target is to achieve thorough mixing of constituents with maximum homogeneity and without breakup of particles. Density control ensures correct material composition and constituent fraction and viscosity control ensures consistency of the slurry preparation process.
- A high viscosity slurry causes problems in the coating process and poor dispersibility results in low film uniformity. Uniformity of the coating thickness and the layer density are crucial to guarantee control over the life time (recharge cycle time) and ion transfer rate of the battery, while regulating the layer thickness enables a smaller battery to be created. Viscosity control is essential to achieve homogeneous coating thickness and minimal coating thickness deviations.
- Higher viscosity of battery slurry increases resistance to sedimentation on standing and delivers a thicker electrode film on coating. The higher viscosity may also render the coating process harder to control, possibly leading to an irregular coating and variable layer density, which in turn brings about a variable ion transfer rate and hence unpredictable battery life time (and unpredictable recharge cycle time).
- Electrode density has effect on cycle performance and irreversible capacity loss in lithium-ion batteries. It needs to be monitored and controlled within appropriate ranges based on the requirement in the calendaring process.
Rheonics' Proposition
Automated in-line viscosity measurement and control is crucial to control the electrode slurry parameters in the slurry preparation and coating and drying stages of the battery manufacturing process, whereas electrode density needs to be closely monitored in the calendaring stage for better battery performance. Rheonics offers the following solutions for process control and optimisation in the multistep battery manufacturing process:
- In-line Viscosity measurements: Rheonics’ SRV is a is a wide range, in-line viscosity measurement device with inbuilt fluid temperature measurement and is capable of detecting viscosity changes within any process stream in real time.
- In-line Viscosity and Density measurements: Rheonics’ SRD is an in-line simultaneous density and viscosity measurement instrument with inbuilt fluid temperature measurement. If density measurement is important for your operations, SRD is the best sensor to cater to your needs, with operational capabilities similar to the SRV along with accurate density measurements.
Rheonics' Advantage
Compact form-factor
Rheonics’ SRV and SRD have a very small form factor for simple OEM and retrofit installation. It enables easy integration in any process stream with extreme ease.
No pressure drop in the process line
Rheonics’ SRV and SRD causes insignificant pressure drop in the process line. The viscosity and density measurements are extremely accurate and highly repeatable in Newtonian as well as non-Newtonian, single and multi-phase fluids.
Insensitive to mounting conditions: Any configuration possible
Rheonics SRV and SRD use unique patented co-axial resonator, in which two ends of the sensors twist in opposite directions, cancelling out reaction torques on their mounting and hence making them completely insensitive to mounting conditions.
Accurate, fast and reliable measurements
Sophisticated, patented 3rd generation electronics drive these sensors and evaluate their response. Ultra-fast and robust electronics, combined with comprehensive computational models, make Rheonics devices one of the fastest and most accurate in the industry. SRV and SRD give real time, accurate viscosity (and density with SRD) measurements every second and are not affected by flow rate variations!
Superior sensor design and technology
Rheonics’ SRD and SRV have a very small form factor for simple OEM and retrofit installation. It enables easy integration in any process stream with extreme ease. They are easy to clean and require no maintenance or re-configurations and are perfectly compatible with industrial communication systems. Both sensors are available with industry standard process connections like ¾” NPT and 1” Tri-clamp allowing operators to replace an existing temperature sensor in their process line with SRV or SRD giving highly valuable and actionable process fluid information like density and viscosity besides an accurate measurement of temperature using an in-build Pt1000 (DIN EN 60751 Class AA, A, B available).
SRD: Single instrument, triple function
Rheonics’ SRD is a unique product that replaces three different instruments for viscosity, density and temperature measurements. It eliminates the difficulty of co-locating three different instruments and delivers extremely accurate and repeatable measurements in harshest of conditions.
Electronics built to fit your needs
Available in both an explosion-proof transmitter housing and a small-form factor DIN rail mount, the sensor electronics enables easy integration into process pipelines and inside equipment cabinets of machines.
Easy to integrate
Multiple Analog and digital communication methods implemented in the sensor electronics makes connecting to industrial PLC and control systems straightforward and simple.
ATEX & IECEx Compliance
Rheonics offers intrinsically safe sensors certified by ATEX and IECEx for use in hazardous environments. These sensors comply with the essential health and safety requirements relating to the design and construction of equipment and protective systems intended for use in potentially explosive atmospheres.
The intrinsically safe and explosion proof certifications held by Rheonics also allows for customization of an existing sensor, allowing our customers to avoid the time and costs associated with identifying and testing an alternative. Custom sensors can be provided for applications that require one unit up to thousands of units; with lead-times of weeks versus months.
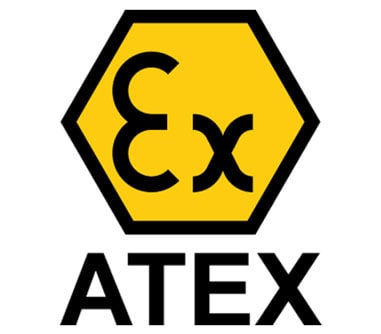
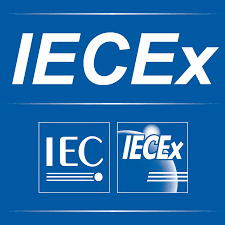
Implementation
Directly install the sensor to your process stream to do real time viscosity and density measurements. No bypass line is required: the sensor can be immersed in-line, flow rate and vibrations do not affect the measurement stability and accuracy. Optimize mixing performance by providing repeated, consecutive, and consistent tests on the fluid.
Rheonics' solution integration in electrode manufacturing process
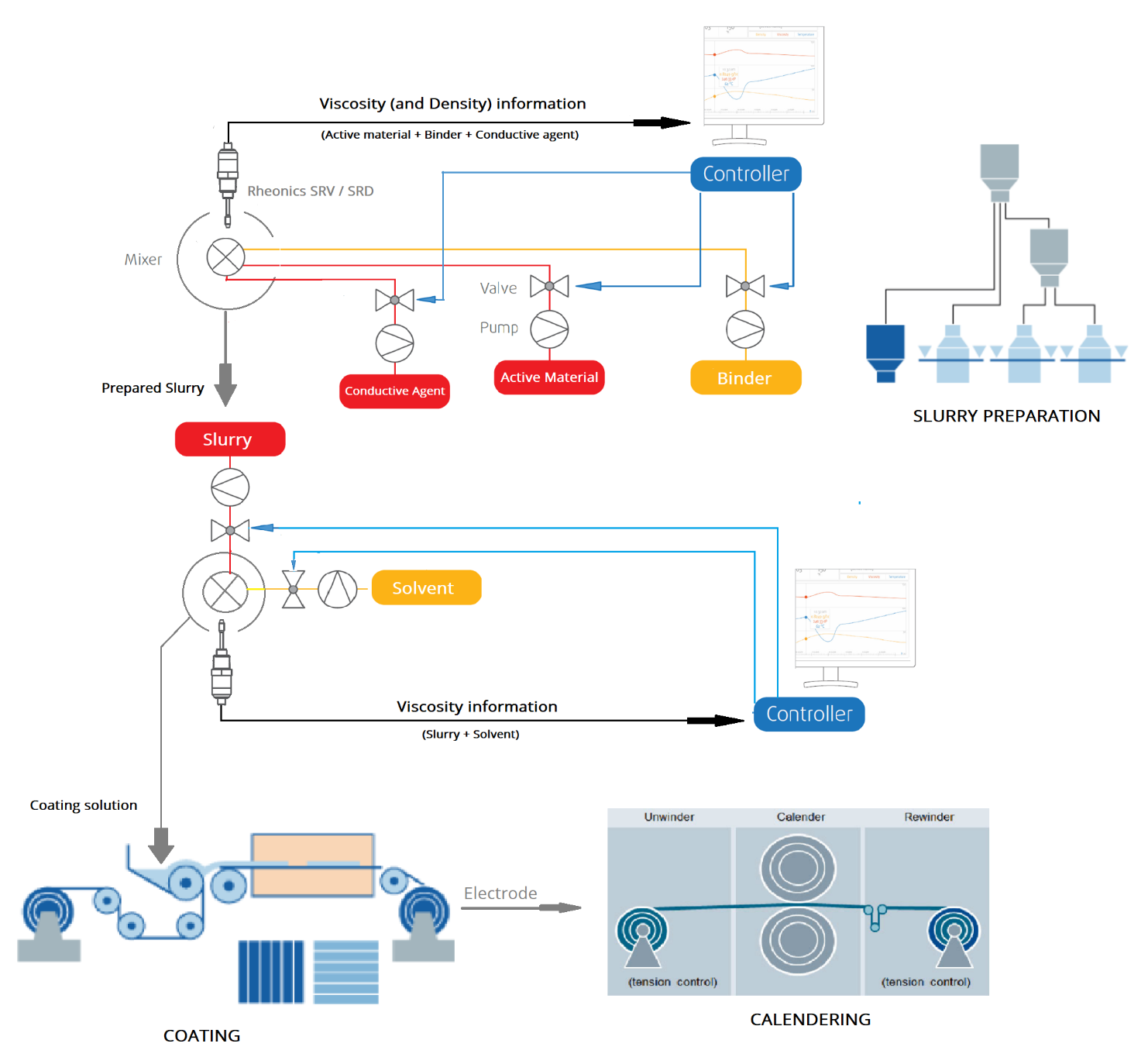
Suggested products for the Application
• Wide viscosity range – monitor the complete process
• Repeatable measurements in both newtonian and non-newtonian fluids, single phase and multi-phase fluids
• All metal (316L Stainless Steel) construction
• Built in fluid temperature measurement
• Compact form-factor for simple installation in existing process lines
• Easy to clean, no maintenance or re-configurations needed
• Single instrument for process density, viscosity and temperature measurement
• Repeatable measurements in both newtonian and non-newtonian fluids, single phase and multi-phase fluids
• All metal (316L Stainless Steel) construction
• Built in fluid temperature measurement
• Compact form-factor for simple installation in existing pipes
• Easy to clean, no maintenance or re-configurations needed