Introduction
As a part of the industry’s drive for continuous cost-effectiveness, drilling fluid performance and management have come under closer scrutiny. Drilling fluids play sophisticated roles in the drilling process: stabilizing the wellbore without damaging the formation, pressure control, bit and drill string lubrication, shale stability, fluid-loss control and cuttings retrieval. Mud contributes to 5-15% of drilling costs but may cause 100% of drilling problems. High-angle wells, high temperatures and long, horizontal sections through pay zones make even more rigorous demands on drilling fluids. Accurate mud monitoring is critical to ensure development of a profitable field.
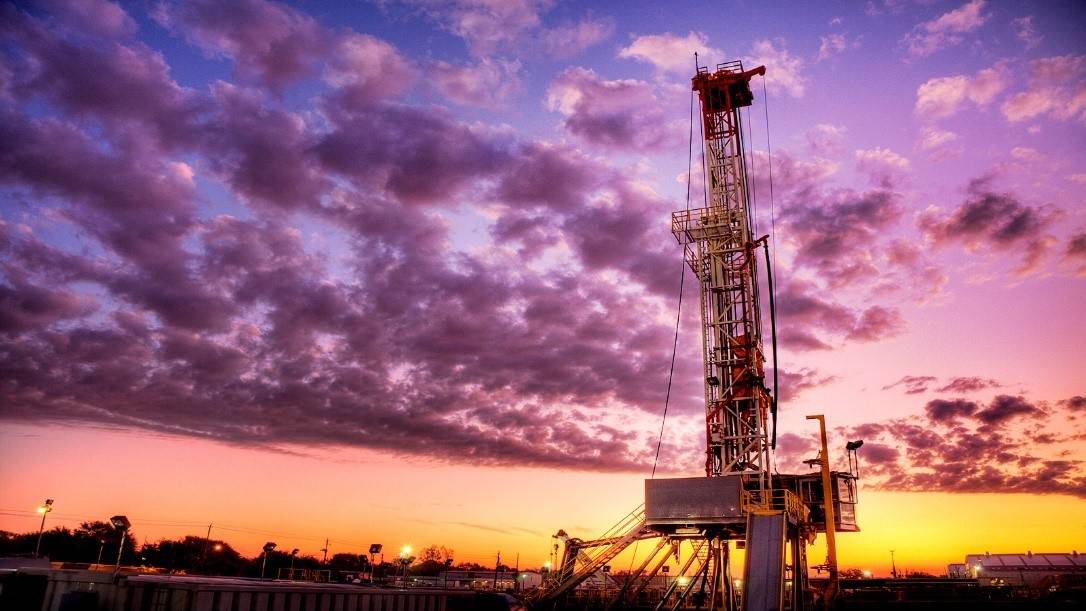
Application
Viscosity and density are the basic mud properties. Viscosity of mud measures carrying capacity and gel development. A high viscosity drilling fluid is desirable to carry the cuttings to surface and suspend weighting agents in the mud. But if viscosity is too high, friction may impede the circulation of mud, decrease drilling rate, wastes fuel, causes loss of circulation and hamper the solids removal equipment. The flow regime of mud in the annulus is also affected by its viscosity. Density measures hydrostatic pressure in the borehole and solids content of unweighted muds. Proper density ensures sufficient hydrostatic pressure required to prevent the borehole wall from caving in and to keep formation fluid from entering the wellbore. But too high mud weight decreases rate of drilling and increases chances of differential sticking, fracturing the well, causes equipment wear, loss of circulation and increased mud cost. Abrasive solids cause excessive wear on pumps, drill string and bit. The drilling rate is reduced; a thick filter cake is deposited on permeable formations, and the pump does unnecessary work recirculating solids that have been allowed to collect in the mud. Mud weight affects filter cake properties and formation damage as well.
For HPHT wells, proper planning and execution of drilling operations requires complete and accurate knowledge of the behavior of drilling fluid density and viscosity as the pressure and temperature change during the drilling operation. Prediction of the drilling mud density at various pressures and temperatures is, therefore, very useful for mud and drilling engineers in planning drilling operations.
Challenges
- Quality Control: Managing the Bottom Hole Pressure within a narrow window helps mitigate critical drilling events and improves well production. It is done by minimizing amount of drilling fluid pushed into the production formation that could later impede flow of hydrocarbons to the well bore. Many operators’ critical downhole decisions are based on drilling fluid data that could be 24 hours old and may not accurately reflect current fluid conditions in the wellbore. Lack of repeated, consecutive, and consistent tests on the fluid, using fluid properties before and after the issues are identified cause the problems to get escalated.
- Operations and Maintenance: Managing quality and quantity of drilling fluid is an essential element in improving safety and productivity of operations. The offline measurements of viscosity and density lack accuracy and repeatability. Measuring viscosity and density with traditional instrumentation is slow, labor intensive, time consuming and prone to inaccuracies. Traditional measurement devices need extensive maintenance, special logistics and frequent repair which can interrupt operations and increase the cost.
- Safety, health and environment: Radiation based density measurements are time consuming and prone to catastrophic accidents. Sudden influx of formation fluids into well bore are a significant safety hazard that can lead to personal injury or rig damage. Job site exposure to hazardous materials can include chemicals and nuclear measurement devices for operations personnel. Drilling fluids disposal is highly regulated in relation to achieving desirable blends, fluid properties and accurate accounting of volumes disposed through injection.
The challenges associated with balancing flow and hydrostatic pressure in some wells has resulted in the development of Managed Pressure Drilling (MPD) systems. MPD allows a more precise control of the bottom hole pressure. This is typically achieved through a closed, pressurized fluid system in which drilling fluid pumps, fluid density and backpressure control on the fluid returns are used to dynamically set and control the well bore pressure. Critical decision making and appropriate course of action on the oilfield depend on accurate drilling fluid data. Drilling performance is optimized by the ability to recognize changes in drilling fluid, analyze the data trends, and act upon what is causing the changes in real-time.
Rheonics' Solutions
Automated in-line process viscosity and density measurements enable continuous monitoring of mud density and viscosity. Rheonics’ SRD is a wide range, in-line density-viscosity measurement instrument with inbuilt fluid temperature measurement and is capable of detecting density and viscosity changes within any process stream in real time. It offers accurate flow measurements over a wide turndown ratio in drilling returns and Managed Pressure Drilling applications.
Single instrument, dual function
Rheonics’ SRD is a unique product that replaces two alternatives and offers better performance while operating at true reservoir conditions. It eliminates the difficulty of co-locating two different instruments.
Enhanced control of well bore pressure
Rheonics’ SRD provides better control of drilling fluid properties within design parameters. Continuous, reliable and accurate mud density measurements with the SRD assures precise control of Bottom Hole Pressure. This helps prevent drilling mud from entering the production zone and restricting hydrocarbon when well is put into production and provides tighter BHP control during underbalanced operations.
Reliable operations for continuous and cost-effective drilling programs
Rheonics’ SRD sensors use patented balanced resonators to ensure consistent, reproducible measurements no matter how the sensor is mounted. Great electronics, combined with comprehensive computational models, make the evaluation units one of the fastest and most accurate in the industry. The accuracy of the sensors in the study of slurries containing entrained gases, sand and cuttings augments its ability to detect well bore stability problems. Continuous, accurate, real time mud density measurements offer an effective means to control mud costs associated with the quantity of additives used and effective detection and management of lost circulation. The simplicity in the design and operation of the sensors mean little or no maintenance costs.
Improved safety standards
Rheonics’ SRDs capability to detect smallest of changes in mud properties helps to provide essential data for early kick detection and control. Continuous, reliable measurement of mud properties-density and viscosity, even in slurries ensure accurate metering of disposal volumes. The SRD is entirely non-nuclear, and mercury free, thereby eliminating exposure of personnel to hazardous materials. There are no concerns for regulatory compliance and waste management of nuclear sources. The SRD raises safety standards during operations and is easy on the environment.
Superior sensor design and technology
Rheonics’ SRD has a very small form factor for simple OEM and retrofit installation. It enables easy integration in any process stream with extreme ease. Using unique patented co-axial resonator, it is completely insensitive to mounting conditions. It is easy to clean, and it requires no maintenance or re-configurations. Rheonics’ software is powerful, intuitive and convenient to use.
Electronics built to fit your needs
Available in both an explosion-proof transmitter housing and a small-form factor DIN rail mount, the sensor electronics enables easy integration into process pipelines and inside equipment cabinets of machines.
Easy to integrate
Multiple Analog and digital communication methods implemented in the sensor electronics makes connecting to industrial PLC and control systems straightforward and simple.
Read more on Rheonics solution for how drilling mud monitoring and control in this blog and article:
Related application notes and blogs
Getting Frac Fluid Rheology Right!
Hydraulic fracturing (also called as fracking, fracing, hydrofracturing) involves high-pressure injection of ‘fracing fluid’ (primarily water, containing sand or other proppants suspended…
Downhole DV measurements in LWD, MWD, Wireline tools
The engineering of well logging sensors into the drill collars is simulating a revolution in logging and drilling. LWD, MWD…
Mud Weight Monitoring
As a part of the industry’s drive for continuous cost-effectiveness, drilling fluid performance and management have come under closer scrutiny.…
ATEX & IECEx Compliance
Rheonics offers intrinsically safe sensors certified by ATEX and IECEx for use in hazardous environments. These sensors comply with the essential health and safety requirements relating to the design and construction of equipment and protective systems intended for use in potentially explosive atmospheres.
The intrinsically safe and explosion proof certifications held by Rheonics also allows for customization of an existing sensor, allowing our customers to avoid the time and costs associated with identifying and testing an alternative. Custom sensors can be provided for applications that require one unit up to thousands of units; with lead-times of weeks versus months.
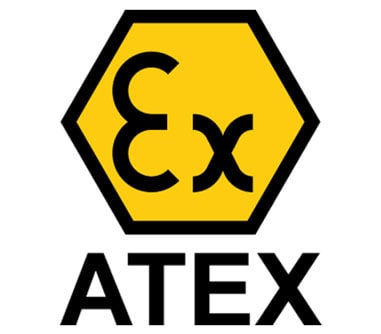
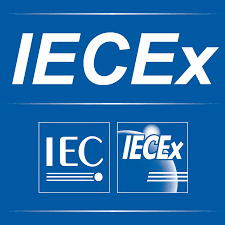
Implementation
Directly install the sensor to your process stream to do real time viscosity and density measurements. No bypass line is required: the sensor can be immersed in-line, flow rate and vibrations do not affect the measurement stability and accuracy. Optimize drilling performance by providing repeated, consecutive, and consistent tests on drilling fluids.
Rheonics Instrument Selection
Rheonics designs, manufactures and markets innovative fluid sensing and monitoring systems. Precision built in Switzerland, Rheonics’ SRD has the sensitivity demanded by the application and the reliability needed to survive in a harsh operating environment. Stable results – even under adverse flow conditions. No effect of pressure drop or flow rate. It is equally well suited to quality control measurements in the laboratory.
Rheonics designs, manufactures and markets innovative fluid sensing and monitoring systems. Precision built in Switzerland, Rheonics’ SRD has the sensitivity demanded by the application and the reliability needed to survive in a harsh operating environment. Stable results – even under adverse flow conditions. No effect of pressure drop or flow rate. It is equally well suited to quality control measurements in the laboratory.
Suggested product(s) for the Application
- Single instrument for process density, viscosity and temperature measurement
- Repeatable measurements in both newtonian and non-newtonian fluids, single phase and multi-phase fluids
- All metal (316L Stainless Steel) construction
- Built in fluid temperature measurement
- Compact form-factor for simple installation in existing pipes
- Easy to clean, no maintenance or re-configurations needed
- Viscosity range: 0.5 up to 3,000 cP (higher range available)
- Density range: 0.4 to 1.5 g/cc