Optimizing flexographic, gravure and corrugated printing applications through inline viscosity monitoring and control
Introduction
Printing presses have numerous applications – newspapers, magazines, catalogues, packaging and labels. The global printing industry is forecast to reach $980 billion by 2018 according to market research firm Smithers Pira. The rapid growth is expected to be driven mainly by the growth in packaging and labels – analog printing for packaging is expected to grow by about 28% and digitally produced packaging is expected to increase by 375% by 2018. There are a wide variety of technologies that are used for printing applications. The main industrial printing techniques are Offset lithography, Flexography, Digital printing, Gravure, Corrugated and Screen printing. There are additional printing techniques developed for very specific applications. The core principle of each of the printing technique is the same – to skilfully deliver the ink on to the substrate ensuring the correct properties as per the process requirements.
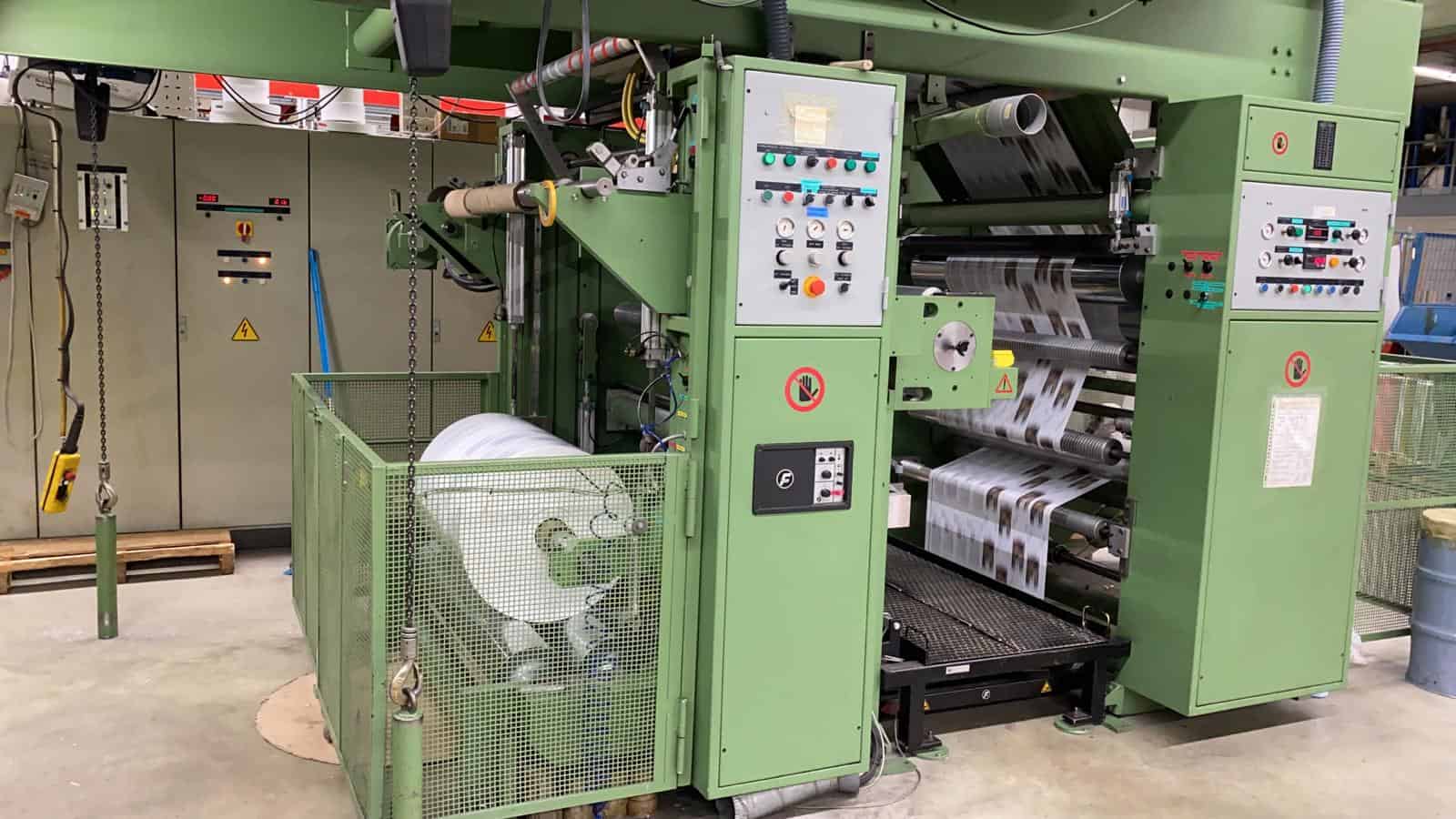
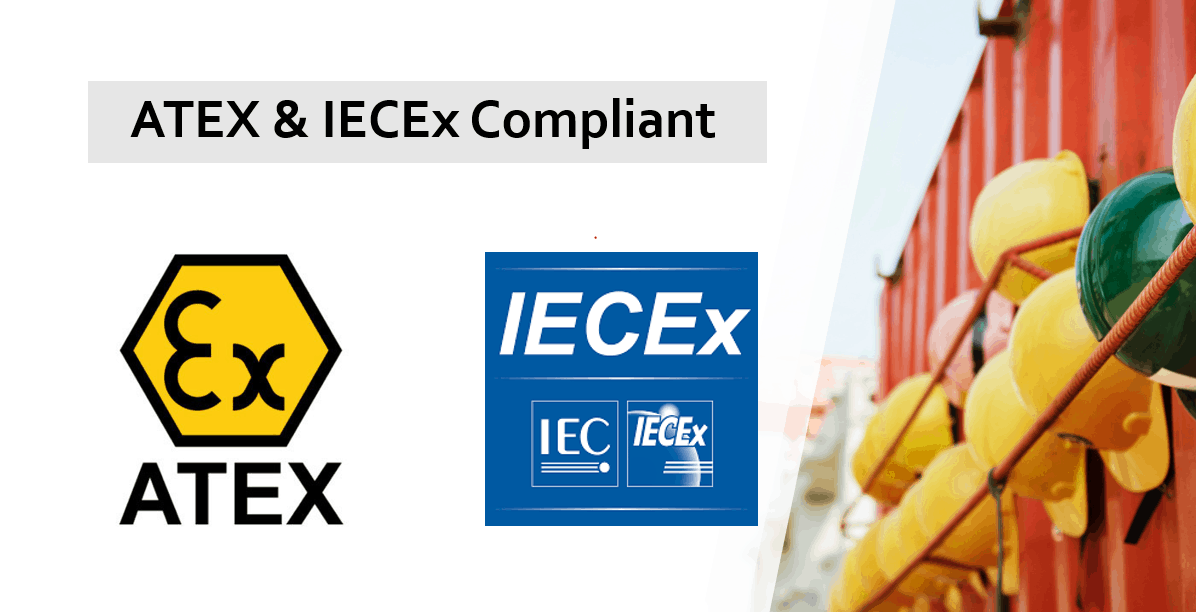
Application
In the press room, ink viscosity is highly critical. Measuring viscosity is important because knowing how quickly and easily the ink will flow will help determine how the ink performs on the press, and at what speeds the press will be able to operate at while using a particular ink. In virtually every printing application, correct ink viscosity is the key to correct quality. The viscosity of ink characterises multiple aspects of how well the ink will transfer onto its substrate. Properties of the ink viscosity can have several effects on ink absorption, colour strength and drying. Highly viscous inks result in tackiness and cause difficult image transfer onto the substrate, whereas low viscosity makes the ink more mobile and harder to control resulting in lost sharpness and dirty printing. The viscosity of ink increases when it is not being worked and decreases when there is a constant applied force. Before the ink is removed from a can, an offset ink is highly viscous. However, as the press rollers work the ink, it becomes less viscous and might negatively affect print quality if not appropriately controlled. The strong correlation between temperature and ink viscosity suggest that fluctuations in temperature can have drastic impact on the ink viscosity.
Real time, in-line viscosity monitoring and control in printing process is essential to improve performance and reduce costs in any printing process – flexographic, gravure or corrugated.
Why is viscosity management critical in printing press?
The broad and significant factors which make viscosity management critical in printing press are:
- Print Quality: Variation in viscosity causes significant change in both solvent and water-based ink properties affecting printability, fade resistance and drying.
- Reduce printing errors: Viscosity control can help alleviate the frequency of printing miscues.
- Colour: Colour consistency and colour density are highly critical to the right print quality. Controlling ink viscosity is the key to colour consistency because that is the factor subjected to the highest variability. The percent solids of fluid is the characteristic of the ink that gives it colour. Ink viscosity is an indicator to the percent solids of the fluid.
- Cost: Printing with incorrect viscosity harms more than just quality. Poor viscosity management drives up usage of expensive pigments and solvents, affecting the profit margins.
- Waste: Materials rejected due to poor quality can be reduced with proper viscosity management.
- Efficiency: Reliable ink supply can run the press faster and more efficiently. Eliminating manual viscosity control frees operators’ time and enables them to focus on other tasks.
- Environment: Lowering the use of pigment and solvent is good for the environment.
To ensure consistent high-quality printing, the change in ink viscosity through-out the process stream is monitored in real time, making measurements from a baseline rather than simply measuring absolute values, and making viscosity adjustments by adjusting solvents and temperature to keep it within specified limits.
Process Challenges
Printing press operators recognize the need to monitor viscosity but making that measurement outside laboratory has challenged process engineers and quality departments over the years. Existing laboratory viscometers are of little value in process environments because viscosity is directly affected by temperature, shear rate and other variables that are very different off-line from what they are in-line. Traditionally, operators have measured the viscosity of printing ink using the efflux cup. The procedure is messy and time-consuming, particularly if the ink needs to be filtered first. It is pretty inaccurate, inconsistent and non-repeatable even with an experienced operator.
Some companies use thermal management systems to keep point-of-application at a determined optimal temperature to achieve constant ink viscosity. But, temperature is not the only factor affecting viscosity. Shear rate, flow conditions, pressure and other variables can affect viscosity changes as well. Temperature controlled systems also have long installation times and a large footprint.
Conventional vibrational viscometers are unbalanced, requiring large masses to avoid large influence of mounting forces.
Rheonics' Solutions
Automated in-line viscosity measurement and control is crucial to control the ink viscosity. Rheonics offers the SRV, based on a balanced torsional resonator, for process control and optimization in the printing process:
In-line Viscosity measurements: Rheonics’ SRV is a wide range, in-line viscosity measurement device with inbuilt fluid temperature measurement and is capable of detecting viscosity changes within any process stream in real time.
Automated in-line viscosity measurement through SRV eliminates the variations in sample taking and lab techniques which are used for viscosity measurement by the traditional methods. The sensor is located in-line so that it continuously measures the ink viscosity. Printing consistency is achieved through automation of the dosing system through a controller using continuous real-time viscosity measurements. Using an SRV in a printing process line, ink transfer efficiency is improved improving productivity, profit margins and environmental goals. The SRV sensors have a compact form factor for simple OEM and retrofit installation. They require no maintenance or re-configurations. SRV offers accurate, repeatable results no matter how or where they are mounted, without any need for special chambers, rubber seals or mechanical protection. Using no consumables, SRV is extremely easy to operate.
InkSight ColorLock Software
• Proprietary advanced 5th generation AI system for simple click monitoring and control
• API for data acquisition and integration into press manufacturer’s HMI
• On-demand in-built remote support management of job run
Rheonics' Advantage
Compact form factor, no moving parts and require no maintenance
Rheonics’ SRV sensors have a very small form factor for simple OEM and retrofit installation. They enable easy integration in any process stream. They are easy to clean and require no maintenance or re-configurations. They have a small footprint enabling Inline installation in ink lines, avoiding any additional space or adapter requirement on the press and on ink carts.
High stability and insensitive to mounting conditions: Any configuration possible
Rheonics SRV sensors use unique patented co-axial resonator, in which two ends of the sensors twist in opposite directions, cancelling out reaction torques on their mounting and hence making them completely insensitive to mounting conditions and ink flow rates. These sensors can easily cope up with regular relocation. Sensor element sits directly in the fluid, with no special housing or protective cage required.
Easy installation and no reconfigurations/recalibrations needed
Replace sensors without replacing or reprogramming electronics, drop-in replacements for both sensor and electronics without any firmware updates or calibration coefficient changes. Easy mounting. Screws into ¾” NPT thread in ink line fitting. No chambers, O-ring seals or gaskets. Easily removed for cleaning or inspection. SRV available with flange and tri-clamp connection for easy mounting and dis-mounting.
Low power consumption
24V DC power supply with less than 0.1 A current draw during normal operation
Fast response time and temperature compensated viscosity
Ultra-fast and robust electronics, combined with comprehensive computational models, make Rheonics devices one of the fastest and most accurate in the industry. SRV gives real time, accurate viscosity measurements every second and are not affected by flow rate variations!
Wide operational capabilities
Rheonics’ instruments are built to make measurements in the most challenging conditions. SRV has the widest operational range in the market for inline process viscometer:
- Pressure range up to 5000 psi
- Temperature range from -40 up to 200°C
- Viscosity range: 0.5 cP up to 50,000 cP
Achieve the right print quality, cut down costs and enhance productivity
Integrate an SRV in the process line and ensure colour consistency throughout the printing process. Achieve constant colours without worrying about colour variations. SRV constantly monitors and controls viscosity and prevents overuse of expensive pigments and solvents. Reliable and automatic ink supply ensures that presses run faster and saves operators’ time. Optimise the printing process with an SRV and experience lesser reject rates, lesser wastes, fewer customer complaints, fewer press shut downs and material cost savings. And at the end of it all, it contributes to a better bottom line and a better environment!
Clean in place (CIP)
SRV monitors the cleanup of the ink lines by monitoring the viscosity of the solvent during the cleaning phase. Any small residue is detected by the sensor, enabling the operator to decide when the line is clean for purpose. Alternatively, SRV provides information to the automated cleaning system to ensure full and repeatable cleaning between runs.
Superior sensor design and technology
Sophisticated, patented 3rd generation electronics drive these sensors and evaluate their response. SRV is available with industry standard process connections like ¾” NPT and 1” Tri-clamp allowing operators to replace an existing temperature sensor in their process line with SRV giving highly valuable and actionable process fluid information like viscosity besides an accurate measurement of temperature using an in-build Pt1000 (DIN EN 60751 Class AA, A, B available).
Electronics built to fit your needs
Available in both an explosion-proof transmitter housing and a small-form factor DIN rail mount, the sensor electronics enables easy integration into process pipelines and inside equipment cabinets of machines.
Easy to integrate
Multiple Analog and digital communication methods implemented in the sensor electronics makes connecting to industrial PLC and control systems straightforward and simple.
ATEX & IECEx Compliance
Rheonics offers intrinsically safe sensors certified by ATEX and IECEx for use in hazardous environments. These sensors comply with the essential health and safety requirements relating to the design and construction of equipment and protective systems intended for use in potentially explosive atmospheres.
The intrinsically safe and explosion proof certifications held by Rheonics also allows for customization of an existing sensor, allowing our customers to avoid the time and costs associated with identifying and testing an alternative. Custom sensors can be provided for applications that require one unit up to thousands of units; with lead-times of weeks versus months.
Rheonics SRV is both ATEX and IECEx certified.
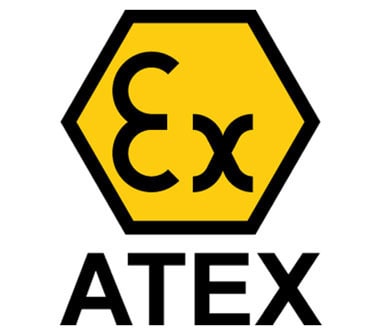
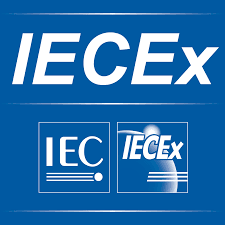
Implementation
Directly install the sensor to your process stream to do real time viscosity measurements. No bypass line is required: the sensor can be immersed in-line, flow rate and vibrations do not affect the measurement stability and accuracy. Optimize mixing performance by providing repeated, consecutive, and consistent tests on the fluid.
Rheonics Instrument Selection
Rheonics designs, manufactures and markets innovative fluid sensing and monitoring systems. Precision built in Switzerland, Rheonics’ in-line viscometers has the sensitivity demanded by the application and the reliability needed to survive in a harsh operating environment. Stable results – even under adverse flow conditions. No effect of pressure drop or flow rate. It is equally well suited to quality control measurements in the laboratory.
Suggested product(s) for the Application
- Wide viscosity range – monitor the complete process
- Repeatable measurements in both Newtonian and non-Newtonian fluids, single phase and multi-phase fluids
- Hermetically sealed, all stainless steel 316L wetted parts
- Built in fluid temperature measurement
- Compact form-factor for simple installation in existing process lines
- Easy to clean, no maintenance or re-configurations needed
Integrated Solution
-
Customized to your CI flexo, Rotogravure or Corrugated presses
- Simple operation -> Click a single button to lock to the correct ink viscosity
- Level 5 Autonomous Control throughout the print
- Consistent prints set to master
- Load jobs at a click : Zero setup time and Zero setup scrap
- Predictive tracking control for precise dilutions of solvent/pH water
- Excellent print control with both solvent and water based inks