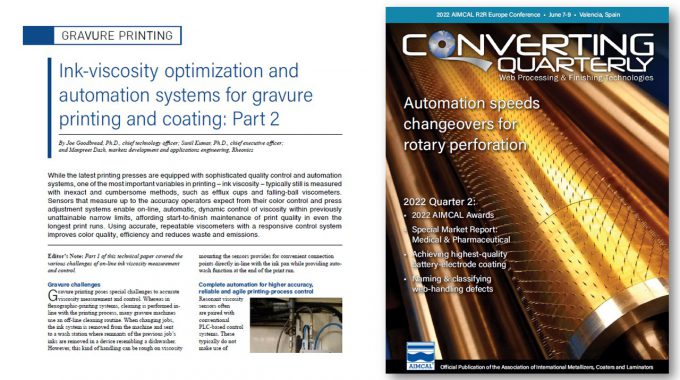
AIMCAL’s Converting Quarterly Magazine Q2 2022 features Rheonics Technology – “Ink viscosity optimization and automation – The key to quality, efficiency and sustainability in printing and coating”
Overview
Web processing & finishing focused magazine – Converting Quarterly (https://www.convertingquarterly.com/) publishes an in depth article about how SRV revolutionizes ink viscosity management in gravure printing and enables “getting it right the first time”. In this article, readers can understand how printers improve color quality, reduce setup time and scrap and achieve sustainability in their operations with complete automation of ink viscosity management.
Find the link to the publication.
To download the pdf copy of the article, please use the link below.
Part 1 of this technical paper covered the various challenges of on-line ink viscosity measurement and control.
Find the link to the publication.
Rheonics wins AIMCAL Technology of the Year Award 2022
The judges had a lengthy discussion about the merits of each Technology of the Year candidate. For the first time in memory, with two submissions with similar functions, they also consulted an expert in coating and material development processes. After considering that input, the judges decided the comprehensive nature of the Rheonics technology, as detailed in its technical writeup, deserved the Technology of the Year Award, but the InkSpec technology also warranted recognition. Noted one judge, “The Rheonics system offers control over a wide range of viscosities and has the potential to reduce waste due to off -spec color caused by changes in ink viscosity.”
“The Rheonics system offers control over a wide range of viscosities and has the potential to reduce waste due to off -spec color caused by changes in ink viscosity.”
Introduction to gravure challenges
Gravure printing poses special challenges to accurate viscosity measurement and control. Whereas in flexographic-printing systems, cleaning is performed inline with the printing process, many gravure machines use an off -line cleaning routine. When changing jobs, the ink system is removed from the machine and sent to a wash station where remnants of the previous job’s inks are removed in a device resembling a dishwasher. However, this kind of handling can be rough on viscosity sensors, changing their baseline and even damaging their mechanisms. For machines with removable ink systems, another kind of installation provides a compact, integrated sensor and control valve unit, which remains on the machine during job changes and is cleaned by an integrated, automated washdown system that removes all traces of the previous ink color from the sensor and associated piping. A special sensor operating mode can self-test the sensor’s condition, indicating when washdown is complete and also signaling the operator when the sensor becomes contaminated during a printing run. The adapter for mounting the sensors provides for convenient connection points directly in-line with the ink pan while providing autowash function at the end of the print run.
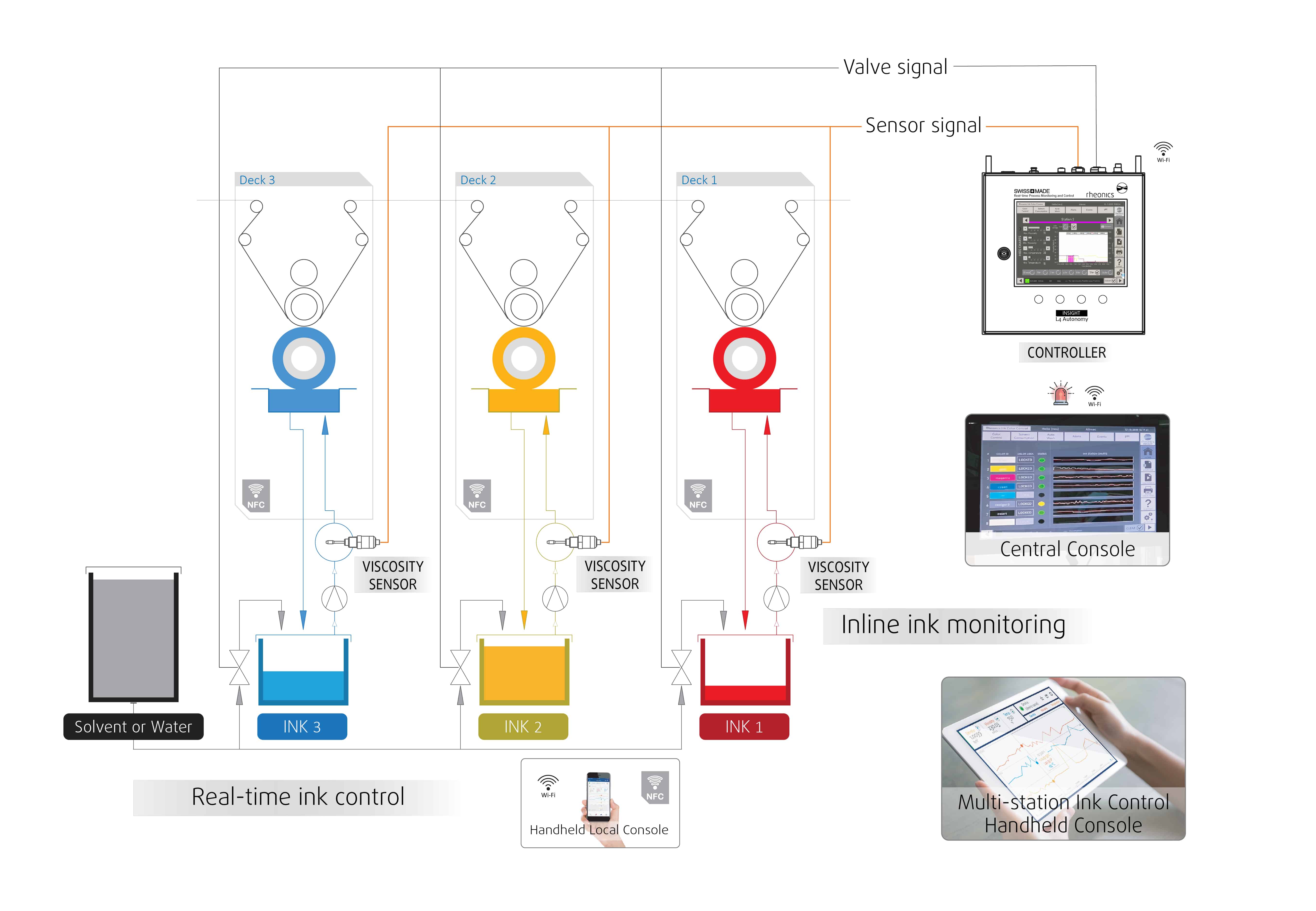
Topics Covered in the article
- Gravure challenges
- How viscosity affects the color precision and quality in printing? Benefits of tight viscosity control for print quality and ink economy
- Challenges with traditional viscosity measurement units
- Benefits of printing press automation (Industry 4.0) and predictive tracking control in terms of quality and efficiency improvements, VOC emissions and waste reductions
Some figures from the article (Part -2)
Unique advantages with the Rheonics SRV sensors
Rheonics sensors have built-in temperature measurement, permitting the temperature of the ink to be monitored. This permits the viscosity readings to compensated for temperature, which is essential for ensuring consistent production through typical daily and seasonal temperature variations.
There are many benefits to using an inline viscosity sensor like the SRV for printing applications. and some include:
- Works accurately in most coating systems with a broad range of ink compositions and viscosities – water-based, solvent-based, UV inks, metallic inks etc.
- Maintains the set ink viscosity, extremely responsive to fresh ink additions
- Rugged, hermetically sealed sensor head. The SRV can be cleaned inline with all standard CIP processes, or with a wetted rag, without the need for disassembly or recalibration
- No moving parts to age or foul with sediment
- Insensitive to particulate matter; no narrow gaps to foul with particulates
- All wetted parts are 316L stainless steel—meets sanitary norms with no corrosion problems
- Certified under ATEX and IECEx as intrinsically safe for use in hazardous environments
- Wide operational range and simple integration—Sensor electronics and communication options make it extremely easy to integrate and run in industrial PLC and control systems.
Some images of the RPS InkSight system
- Rheonics SmartView console integrated in printing machines
- Some pictures showing the SRV viscometers inline installation inside the press
- Standalone control cabinet
Related Articles
AIMCAL’s Converting Quarterly Magazine features Rheonics Technology – “Ink viscosity optimization and automation – The key to quality, efficiency and sustainability in printing and coating”
Web processing & finishing focused magazine - Converting Quarterly (https://www.convertingquarterly.com/) publishes an in depth article about how SRV revolutionizes ink viscosity management in gravure printing and enables "getting it right the first time". In this article, readers can understand how printers improve color quality, reduce setup time and scrap and achieve sustainability in their operations with complete automation of ink…
Rheonics awarded Sustainable Innovation Packaging – Innovation Prize 2021 by European Rotogravure Association
Rheonics wins a Sustainable Packaging Innovation Award by the European Rotogravure Association. Dr. Sunil Kumar received the award at the Annual & Packaging and Decorative Gravure Conference in Thessaloniki, Greece on 21-23 September, 2021. “Gravure – the sustainable print process” was the theme of the conference, which pointed out an encouraging perspective for gravure’s future. Our viscosity automation technology ensures…
Interprint, Inc. optimizes and automates printing operations in the decorative gravure market segment with the RPS InkSight auto viscosity control
Challenge Fluctuations in material throughput related to market demand can also be seen as a disturbance which needs to be compensated for to assure product quality. Solution Inclusion of automated supervisory process control in the manufacturing process becomes essential to automatically assure that critical quality attributes are consistently in agreement with the acceptance criteria in real-time.
Optimizing flexographic, gravure and corrugated printing applications through inline viscosity monitoring and control
Printing presses have numerous applications – newspapers, magazines, catalogues, packaging and labels. The global printing industry is forecast to reach $980 billion by 2018 according to market research firm Smithers Pira. The rapid growth is expected to be driven mainly by the growth in packaging and labels – analog printing for packaging is expected to grow by about 28% and…
All Rheonics products are designed to withstand harshest process environments, high temperature, high level of shock, vibrations, abrasives & chemicals.
Conclusion
As printing speeds increase, and profit margins get tighter, “getting it right the first time” becomes much more important. An error in initial viscosity setting can result in producing several thousand meters of waste in no time at all. Tight control with an accurate sensor, combined with a responsive control system, has enabled us to streamline our printing process while improving color quality and reducing waste.