Key advantages of viscosity management in liquid products filling lines:
- Accurate and efficient packaging line operations – significant savings in material costs
- Seamless product change-over: agility in dealing with different and new product variants and product provenance
- Compliance with regulations
- Optimizing CIP systems
Introduction
Packaging liquid, liquid with solid chunks, and gel like products consists of the packaging materials and packaging machines like filling lines. It includes rigid packaging formats such as bottles & containers and flexible packaging formats such as films, stand-up pouches, squeezable tubes, cartons, and bag-on-box. In many industries, packaging processes are automated using filling lines.
Liquid packaging application areas span multiple industries – food and beverage, cosmetics, household products, chemicals, medicines, FMCG products. Some examples by industry are:
- Food and Beverages: Sauces, Dairy products, juice, carbonated beverages, soups, coffee/tea, yogurt, milk, ice-cream, gelatin desserts, honey, jelly, syrups, aseptic food, butter, ghee, beer etc.
- Cosmetics: Creams, lotions, shampoos, facial, hair oils, sunscreens
- Medicines: Syrups, Drops, ointments
- FMCG: Toothpastes, sanitizers, handwashing liquids, dish washing liquids, liquid detergents
- Chemicals: Industrial, water treatment, adhesives, mining, catalyst, lab and other application uses.
Mechanisms for filling/packaging
One of the keys to a successful liquid packaging line is efficiency. For optimizing the efficiency of a packaging line, there are multiple factors to consider. It includes viscosity of the liquid, product characteristics, specific product challenges, ease of cleaning, accuracy, ease of flexibility and changeover, and using a reliable machine vendor.
All liquids flow differently. Understanding this is of utmost importance while designing a filling machine. Viscosity is the property that gives insights into the liquid’s flow behaviour. Therefore, it’s crucial to take note of the viscosity of the product you are handling. Filling methods differ in cost, accuracy, speed and hygiene. Not all methods are suitable for all liquids, for beverages need particular hygiene, expensive cosmetics require special precision, while engine oil has a different flow characteristic to, say, mineral water. A free-flowing product such as water that is low in viscosity will flow well through a gravity filler. This is because this type of machine relies on the power of gravity to push the product through.
Some products that are higher in viscosity will need assistance to be filled into the packaging. Lotions and other high viscosity liquids work well with piston fillers and pump fillers. Piston fillers have a versatile ability to handle liquids from aerated products to icings and sauces. Pump fillers work well with liquids of all viscosities and offer variety when it comes to the pump chosen. Pump fillers can utilize progressive cavity pumps, gear pumps, lube pumps, and various valves and fittings to meet the project’s needs.
What makes viscosity automation and control so important in building an efficient packaging line for liquid products?
One of the first aspects of a packaging line that a business needs to consider is the viscosity of the liquid going through the filling and packaging processes. The thickness of the liquid will be a huge determinant when it comes to selecting the right machinery to purchase and install. If equipment is used for the wrong viscosity level, it could significantly hinder productivity, and breakdowns are more likely to occur. Consider whether the liquid is water-thin, thicker or highly viscous, which can be determined using a viscosity chart when selecting machinery.
There are several advantages of inline, real-time viscosity monitoring and control in packaging line for fluid/liquid products:
Accurate and efficient packaging line operations – significant savings in material costs. Viscosity control makes liquid packaging lines more ‘accurate’ by ensuring consistent product and thus enables tighter control for right level of product to be dispensed. Viscosity quality control in production and transportation stages, preceding the filling operations can ensure that the exact quantity of liquid is dispensed, with minimal amount of process variabilities which can possibly arise from the packaging line equipment such as nozzles and valves. This results in significant material savings for the company, considering the scale of operations.
In order to comply with regulations penalizing underfilling, during production manufacturers often exceed the minimum quantity in packaging. However, such safety overfilling can be costly. For example, a mid sized milk producer fills around 100,000 bottles of coconut milk per day. By reducing the overfill in individual bottles by a few grams, the company could potentially save several million euros a year. Manufacturers of complete bottling plants should therefore offer systems that measure the fill quantities with high precision and keep overfilling to an absolute minimum.
Seamless product change-over: agility in dealing with different and new product variants and product provenance. Factory engineers get a more accurate picture of how the new formulations or recipe changes will react and how they might need to adjust current systems and control parameters. Real-time monitoring facilitates transition of a batch-based process to continuous operation, saving significant operational and capital costs through re-use of the same lines for multiple products. The packaging line engineers can respond quickly to ever-changing consumer demands, optimise output and reduce system costs.
Source: Pepsico Inc.
Viscosity data helps the packaging line engineers adjust the parameters to ensure they maintain tight control of the dispensing process unaffected by change in product properties, especially the flowability which is dependent on the viscosity. Additionally, the decisions of adapting the machine parameters and variables (nozzles, pumps, valves controls) can be reliably driven and automated by the viscosity data, hence ensuring changeover time is restricted to the minimum.
Compliance with regulations. When it comes to food and beverage products, quality, safety and confidence are absolutely critical. Accuracy and repeatability of the dispensing process needs to be tightly controlled, since EU, WHO norms and other GMP guidelines state permissible tolerance levels depending on product/industry types. The challenge for all these processes is the same: the packaging must contain the stated quantity of product. If the fill quantity in bottles is too low, for example, this contravenes EU Pre-packaging Directive 76/211/EEC and German Pre-packaged Product Act (§22 FPackV). These stipulate the percentage by which a production batch may fall short of the specified minimum fill quantity. Here, “misconduct” can lead to penalties that include the shutdown of production.
This means viscosity automation is critical to ensure the filling process stays efficient to avert risks of scraps, rejects and penalties – which can be significantly high in continuous liquid filling factories packaging tonnes of materials every hour!
Other Considerations for efficiency of a liquid packaging line
Ease of cleaning. Another important aspect is the ability to clean the equipment easily and without issue. The easier machinery is to clean, the less time is needed to spend cleaning parts and machines, and the faster it can be up and running again. Machinery that’s easy to disassemble will help keep the cleaning process efficient. One example of this is for the customer to purchase equipment that offers either a manual or automatic clean in place (CIP), which is the most efficient way to clean a filler. CIP will cycle the cleaning solution through the machine to ensure that all wetted parts are clean.
Image Source: TetraPak
Ease of flexibility, changeover and scalability. The machinery’s ease of changeover and flexibility are also integral to an efficient packaging system. This means that equipment should be able to accommodate multiple types of containers or liquids without the need to change parts. Some manufacturers have machinery that’s capable of handling multiple bottle sizes through the use of a single piece of equipment as long as the liquids’ viscosity is consistent. Machinery should also be easy to upgrade, which is particularly important as business grows.
Key value of viscosity automation solutions in packaging line
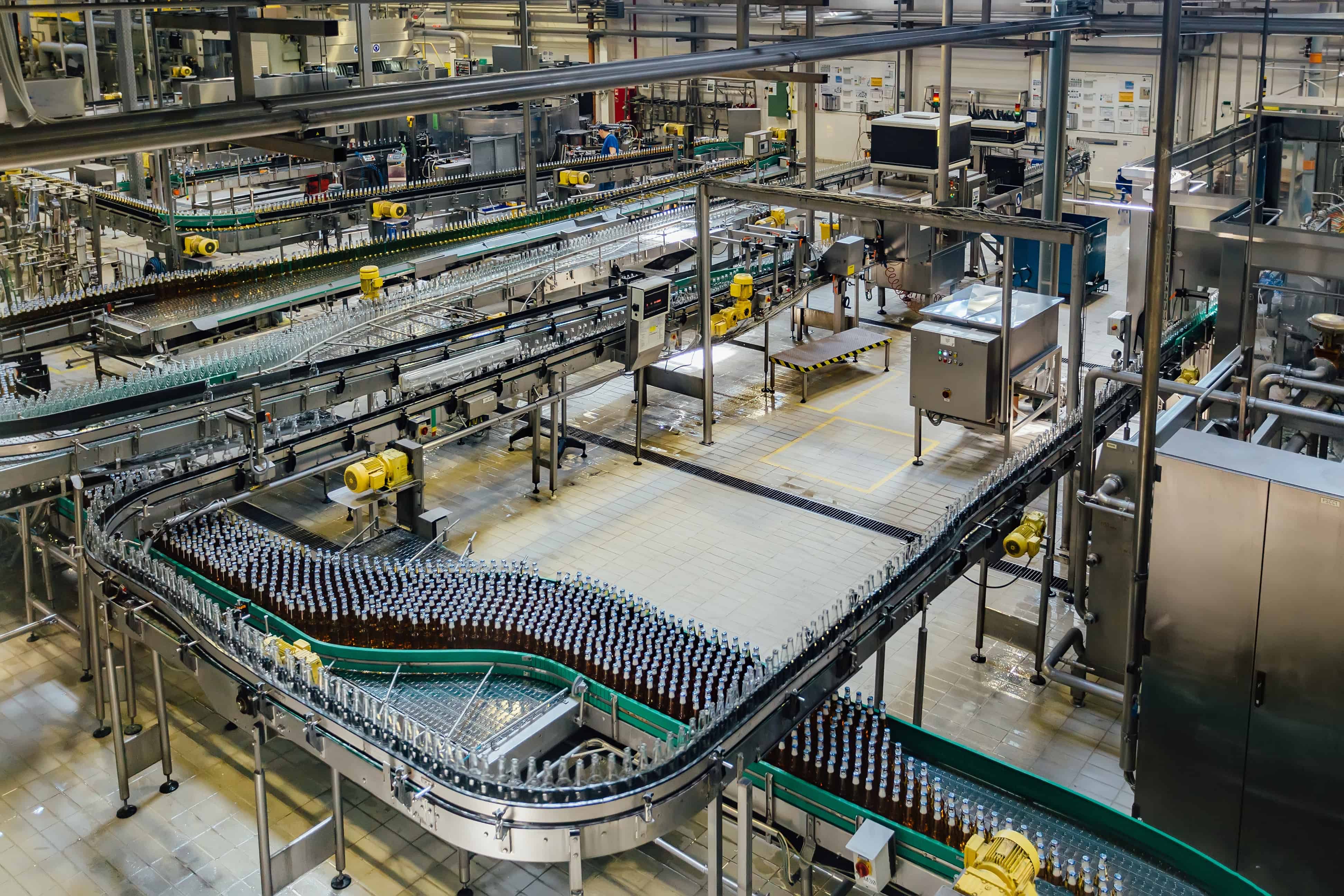
The broad and significant factors which make viscosity management important in virtually every filling application:
- Quality: Viscosity monitoring of the liquid product in the processing and transportation stages preceding the filling operation can ensure that prior to filling, the product quality/consistency is adequate.
- Repeatability across batches: To ensure consistency from batch to batch, and to maintain a consistent level/weight, viscosity control is essential.
- Reduced waste and cost savings: Accurate filling operations means that the exact amount of product is delivered during packaging, saving tonnes of extra materials which could potentially be additionally used up otherwise. It also means reduced scraps and rejects, even in the tightest regulations, thus minimizing costs.
- Efficiency: Hassle free, real time monitoring of viscosity can save a lot of time and effort which is involved in offline analysis of the sample and making process decisions based on that analysis.
- Environment: Viscosity automation can optimize the CIP/SIP processes. Lowering the amount of use of cleaning fluids/materials is good for the environment.
- Smart factory – digitalization and automation benefits: The process data acquired by the sensors can be used in multitude of other ways – machine maintenance scheduling, QC diagnosis, root cause analysis, information exchange across facilities for decentralizing decisions and much more. The ability to load different jobs/models for different fluids by using viscosity information transforms into benefits of paramount importance, enabling companies reap benefits of Industry 4.0 and automation technologies. They become more adaptable to ever changing consumer needs. Learn more using the link below.
Digital food processing – driver for manufacturers embrace of Industry 4.0
Temperature fluctuations, mixing equipment condition, type and conditions of substrates, batter formulations, process step interactions and mixing time parameters can all alter the product quality and performance across batches in batter mixing and coating. In thin-margin sectors like baked goods, batter-coated foods, and confectionery, the…
Viscosity measurement and process challenges
Engineers and plant operators in packaging lines realize the need to make viscosity measurements and to intervene through appropriate corrective actions for achieving high-quality and consistent, predictable flowability of the liquid/semi-liquid product. However, making these measurements have challenged them over the years.
Offline grab-samples are simply unreliable and not suited for liquid packaging operations
Monitoring the viscosity of a fluid in a process often means taking a sample of the fluid from a tank or pipeline, and bringing the sample to a laboratory where its flow and rheological properties are measured on a laboratory viscometer or rheometer. Based on the findings, the process operator must be informed whether the fluid is at the desired viscosity, or if further action is required then new measurements must be made after intervention. This system is called off-line or manual control, with several obvious disadvantages – it is time-consuming and often inaccurate even with experienced operators. Most often the results are too late to save a batch.
The alternative is to use an in-line viscometer that will continuously monitor the viscosity of the process fluid throughout the process. This instrument gives an output signal which, if displayed, provides the operator with the necessary information to control the process. Alternatively, viscometer outputs are connected to a PLC (Programmable Logic controller) / DCS (Digital Control System) for automatic process control.
Issues with conventional viscometers for inline installation
Traditional process viscometers encounter problems related to the fluid flow in pipeline and tank-mixing installations. In general, these older generation viscometers do not function properly in turbulent flow. Rotational instruments will only operate up to a certain maximum flow rate. The flow has to be controlled for pressure drop viscometers. Flow related problems for these types are avoided by installing the viscometer on by-pass line and conditioning the sample flow to suit the instrument. Instrument response time is then related to the flow conditions, as an adequate sample renewal rate is required for effective control. Furthermore, instruments used in a process environment have to be robust and able to resist any corrosive materials that they may encounter, especially during cleaning.
Rheonics’ Solutions for improving packaging line efficiency and agility
Automated in-line viscosity measurement and control is crucial to monitor/control viscosity during filling operations and ensure the packaging line machine parameters are adjusted according to the product viscosity. Rheonics offers the following solutions for process control and efficiency optimisation in the packaging line.
Viscosity & Density Meters
- In-line Viscosity measurements: Rheonics’ SRV is a is a wide range, in-line viscosity measurement device capable of delivering viscosity measurements (along with temperature measurements) and detecting viscosity changes within any process stream in real time.
- In-line Viscosity and Density measurements: Rheonics’ SRD is an in-line simultaneous density and viscosity measurement instrument (along with temperature measurements). If density measurement is important for your operations, SRD can cater to your needs, with operational capabilities similar to the SRV along with accurate density measurements.
These instrument gives an output signal and reading on a software panel which, if displayed, provides the operator with the necessary information to control the process. Alternatively, it may be possible to send the output to an automatic process controller. Integrated control systems enable the viscosity/density information in the process line to be used effectively.
Integrated, turnkey quality management for filling line operations
Rheonics offers an integrated turn-key solution for quality management made of:
- In-line Viscosity measurements: Rheonics’ SRV – a wide range, in-line viscosity measurement device with in-built fluid temperature measurement
- Rheonics Process Monitor: an advanced predictive tracking controller to monitor and control in real-time variations of process conditions
- Rheonics RheoPulse with automatic dosing: A Level 4 autonomous system that ensures no compromise with set limits of viscosity and automatically activates by-pass valves or pumps to adaptively dose mixture components in the processing stages preceding the filling operations.
Rheonics Process Monitor
The SRV sensor is located in-line so it continuously measures the viscosity (and density in case of SRD). Alerts can be configured to notify operator of necessary action or the entire management process can be fully automated with RPTC (Rheonics Predictive Tracking Controller). Using an SRV in the filling line, results in improved productivity, profit margins and achieves regulatory conformance. Rheonics sensors have a compact form factor for simple OEM, retrofit installation and easy scale up across all the lines in the factory. They require zero maintenance or re-configurations. The sensors offer accurate, repeatable results no matter how or where they are mounted, without any need for special chambers, rubber seals or mechanical protection. Using no consumables and not requiring re-calibration, SRV and SRD are extremely easy to operate resulting in extremely low lifetime running costs. As a machine builder or automation system integrator, you can learn more about the ease of integrating rheonics sensor in your line on our dedicated System Integrators page.
Once the process environment is established, there is usually little effort required to maintain the integrity consistency of the systems – operators can rely on the tight control with Rheonics liquid packaging line management solution.
Inline probe-style density meters have an edge in weight-based automated filling
For precise automated filling (for example – Volumetric method), it can be especially important to monitor and control density. Density can fluctuate due to air bubbles in the liquid and changes in the temperature or recipe.
Coriolis flow meters give mass flow measurements but they have certain disadvantages such as:
- Time consuming calibration procedures and difficult installation
- Difficulty in cleaning: Coriolis flow meters are difficult to clean, especially when the fluid has considerable solids content. It makes them unsuitable to meet the hygienic standards inside factories.
- Longer filling times: With weighing technology or mass flow measurement, it takes around five seconds to fill a bottle. Flow rate measurement suffers the largest fluctuation in filling speed, with the time varying between two and five seconds.
On the other hand, Rheonics SRD are designed and built for the easiest integration in a continuous production environment. They have no special chambers and can be easily removed for cleaning or inspection. SRD probes are hermetically sealed for Clean-in-place (CIP) and supports high pressure wash with IP69K M12 connectors. SRD is a unique product that replaces three different instruments for viscosity, density and temperature measurements.
Packaging lines can make the best use of advances in automation technology by Rheonics
Rheonics automation systems include features beyond the legacy systems such as embedded advanced process control algorithms, statistical monitoring, smart device monitoring and asset health monitoring. They bring the process and asset condition data to both operations and maintenance, enabling new and efficient ways to integrate work processes and improve timeliness and accuracy of decisions, critical considering the speed and scale of operations within a liquid products packaging line.
Making CIP systems more intelligent
Rheonics SRV (and SRD) are not just CIP/SIP compliant, but they also monitor the clean-up of the fluid lines by monitoring the viscosity (and density) of the cleaner/solvent during the cleaning phase. Any small residue is detected by the sensor, enabling the operator to decide when the line is clean/fit for purpose. Alternatively, SRV (and SRD) provides information to the automated cleaning system to ensure full and repeatable cleaning between runs, thus ensuring full compliance to sanitary standards of food/pharmaceutical manufacturing facilities. Learn more about how rheonics viscosity systems optimize CIP systems to shorten cleaning times/downtimes. It also means significant savings in cleaning fluids/materials. Learn More how SRV is CIP compatible and better yet helps optimize the CIP process.
Rheonics' Advantage
Compact form factor, no moving parts and require no maintenance
Rheonics’ SRV and SRD have a very small form factor for simple OEM and retrofit installation. They enable easy integration in any process stream. They are easy to clean and require no maintenance or re-configurations. They have a small footprint enabling Inline installation in any process line, avoiding any additional space or adapter requirement.
Hygienic, sanitary design
Rheonics SRV and SRD are available in tri-clamp and DIN 11851 connections besides custom process connections.
Both SRV & SRD conform to Food Contact Compliance requirements according to US FDA and EU regulations.
High stability and insensitive to mounting conditions: Any configuration possible
Rheonics SRV and SRD use unique patented co-axial resonator, in which two ends of the sensors twist in opposite directions, cancelling out reaction torques on their mounting and hence making them completely insensitive to mounting conditions and flow rates. Sensor element sits directly in the fluid, with no special housing or protective cage requirements.
Instant accurate readouts on ‘flowability’ – Complete system overview and predictive control
Rheonics’ RheoPulse software is powerful, intuitive and convenient to use. Real-time process fluid can be monitored on the integrated IPC or an external computer. Multiple sensors spread across the plant are managed from a single dashboard. No effect of pressure pulsation from pumping on sensor operation or measurement accuracy. No effect of vibration.
Inline measurements, no bypass line is needed
Directly install the sensor in your process stream to do real time viscosity (and density) measurements. No bypass line is required: the sensor can be immersed in-line; flow rate and vibrations do not affect the measurement stability and accuracy.
Easy installation and no reconfigurations/recalibrations needed – zero maintenance/down-times
In the unlikely event of a damaged sensor, replace sensors without replacing or re-programming electronics. Drop-in replacements for both sensor and electronics without any firmware updates or calibration changes. Easy mounting. Available with standard and custom process connections like NPT, Tri-Clamp, DIN 11851, Flange, Varinline and other sanitary and hygienic connections. No special chambers. Easily removed for cleaning or inspection. SRV is also available with DIN11851 and tri-clamp connection for easy mounting and dis-mounting. SRV probes are hermetically sealed for Clean-in-place (CIP) and supports high pressure wash with IP69K M12 connectors.
Rheonics instruments have stainless steel probes, and optionally provide protective coatings for special situations.
Low power consumption
24V DC power supply with less than 0.1 A current draw during normal operation.
Fast response time and temperature compensated viscosity
Ultra-fast and robust electronics, combined with comprehensive computational models, make Rheonics devices one of the fastest, versatile and most accurate in the industry. SRV and SRD give real-time, accurate viscosity (and density for SRD) measurements every second and are not affected by flow rate variations!
Wide operational capabilities
Rheonics’ instruments are built to make measurements in the most challenging conditions.
SRV is available with the widest operational range in the market for inline process viscometer:
- Pressure range up to 5000 psi
- Temperature range from -40 up to 200°C
- Viscosity range: 0.5 cP up to 50,000 cP (and higher)
SRD: Single instrument, triple function – Viscosity, Temperature and Density
Rheonics’ SRD is a unique product that replaces three different instruments for viscosity, density and temperature measurements. It eliminates the difficulty of co-locating three different instruments and delivers extremely accurate and repeatable measurements in harshest of conditions.
Manage dispensing/filling more efficiently, cut down costs and enhance productivity
Integrate an SRV in the process line and ensure consistency over the years. SRV constantly monitors and controls viscosity (and density in case of SRD) and activates valves adaptively for dosing the mixture constituents. Optimise the process with an SRV and experience fewer shutdowns, lower energy consumption, lesser non-compliances and material cost savings. And at the end of it all, it contributes to a better bottom line and a better environment!
Clean in place (CIP) and Sterilization in place (SIP)
SRV (and SRD) monitors the cleanup of the fluid lines by monitoring the viscosity (and density) of the cleaner/solvent during the cleaning phase. Any small residue is detected by the sensor, enabling the operator to decide when the line is clean/fit for purpose. Alternatively, SRV (and SRD) provides information to the automated cleaning system to ensure full and repeatable cleaning between runs, thus ensuring full compliance to sanitary standards of food manufacturing facilities.
What is CIP? Optimizing CIP (Clean In Place) Systems with inline viscosity & density measurements
What is CIP? In CIP systems, cleaning takes place without dismantling the system. CIP refers to all those mechanical and chemical systems that are necessary to prepare equipment for food processing, either after a processing run that has produced normal…
Superior sensor design and technology
Sophisticated, patented electronics is the brain of these sensors. SRV and SRD are available with industry standard process connections like ¾” NPT, DIN 11851, Flange and Tri-clamp allowing operators to replace an existing temperature sensor in their process line with SRV/SRD giving highly valuable and actionable process fluid information like viscosity besides an accurate measurement of temperature using an in-build Pt1000 (DIN EN 60751 Class AA, A, B available).
Electronics built to fit your needs
Available in both a transmitter housing and a small-form factor DIN rail mount, the sensor electronics enables easy integration into process lines and inside equipment cabinets of machines.
Easy to integrate
Multiple Analog and digital communication methods implemented in the sensor electronics makes connecting to industrial PLC and control systems straightforward and simple.
Analog and Digital Communication Options
Optional Digital Communication Options
ATEX & IECEx Compliance
Rheonics offers intrinsically safe sensors certified by ATEX and IECEx for use in hazardous environments. These sensors comply with the essential health and safety requirements relating to the design and construction of equipment and protective systems intended for use in potentially explosive atmospheres.
The intrinsically safe and explosion proof certifications held by Rheonics also allows for customization of an existing sensor, allowing our customers to avoid the time and costs associated with identifying and testing an alternative. Custom sensors can be provided for applications that require one unit up to thousands of units; with lead-times of weeks versus months.
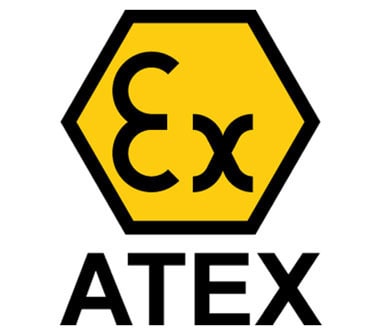
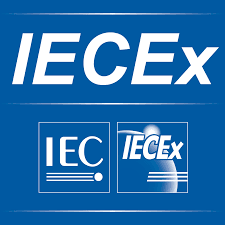
Implementation
Directly install the sensor in your process stream to do real-time viscosity and density measurements. No bypass line is required: the sensor can be immersed in-line; flow rate and vibrations do not affect the measurement stability and accuracy. Optimize mixing performance by providing repeated, consecutive, and consistent tests on the fluid.
In-line Quality control locations
- In tanks
- In the connecting pipes between various processing containers
Instruments/Sensors
SRV Viscometer OR an SRD for additional density
Rheonics Instrument Selection
Rheonics designs, manufactures and markets innovative fluid sensing and monitoring systems. Precision built in Switzerland, Rheonics’ in-line viscometers and density meters have the sensitivity demanded by the application and the reliability needed to survive in a harsh operating environment. Stable results – even under adverse flow conditions. No effect of pressure drop or flow rate. It is equally well suited to quality control measurements in the laboratory. No need to change any component or parameter to measure across full range.
Suggested product(s) for the Application
- Wide viscosity range – monitor the complete process
- Repeatable measurements in both Newtonian and non-Newtonian fluids, single phase and multi-phase fluids
- Hermetically sealed, all stainless steel 316L wetted parts
- Built in fluid temperature measurement
- Compact form-factor for simple installation in existing process lines
- Easy to clean, no maintenance or re-configurations needed
- Single instrument for process density, viscosity and temperature measurement
- Repeatable measurements in both newtonian and non-newtonian fluids, single phase and multi-phase fluids
- All metal (316L Stainless Steel) construction
- Built in fluid temperature measurement
- Compact form-factor for simple installation in existing pipes
- Easy to clean, no maintenance or re-configurations needed