Introduction
Food and beverage industry is one of the key industrial segments and major contributor to global economic and societal growth. In the EU, it constitutes the largest manufacturing sector in terms of turnover, value add, and employment. However, the sector has been associated with various environmental issues including high levels of water consumption and wastewater production. Sources of wastewater production in the food industry include breweries, manufacturers of beverages, vegetable oils, milk/dairy products, starch, confectioneries, sauces and juices. Increasingly stringent discharge standards require removal of pollutants from wastewater to very low levels while environmental and financial sustainability goals require minimizing energy and resource consumption. Utilities require technology that helps them improve process efficiency while maintaining or reducing operation and maintenance (O&M) costs.
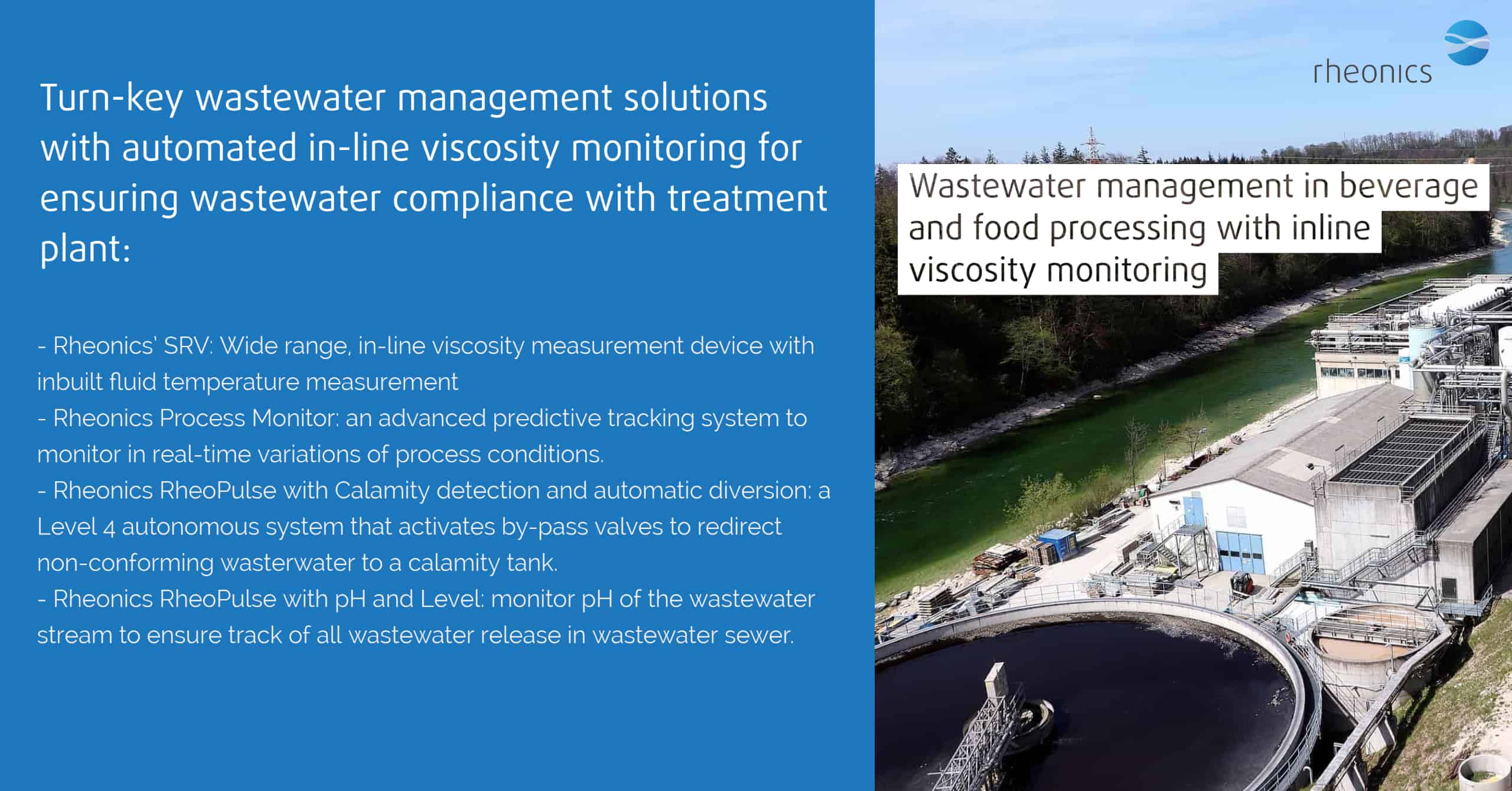
Wastewater discharged from food processing factories vary depending on products and production procedures. In factories like accompanying dish (soups, sauces, ready meals) makers and beverage makers (juices, drinks), due to change of products and/or production method, the wastewater fluctuates in characteristics and volume. Almost all the wastewater in food processing factories is treated using a biological treatment process. The characteristics of wastewater from food processing factories are characterized by high BOD, SS, and oil concentrations as well as emitting smells from acidification. When aerobic or anaerobic biological processes are applied to wastewater treatment in food processing factories, removing oils and solids prior to the biological process is important for preventing them from disturbing the treatment.
Process Requirements
Industries need to ensure that their wastewater is properly treated and meets the specifications/limits of their local Publicly Owned Treatment Works (POTW)/municipal sewage treatment plant. It is critical for the plant managers to follow procedures, and features designed to minimize pollutants discharged to the sanitary sewer or released to the environment. The following are some of the requirements applicable to the wastewater treatment division of industrial facilities in the food processing industry.
Meet discharge limits
All food processing plants and breweries that send their wastewater to the sewer system must make sure their wastewater meets local discharge limits and prohibitions. Different POTWs often have different requirements, depending on the location.
- Total Suspended Solids (TSS) – Solids such as spent yeast, grains, hops and trub capable of settling can restrict or block flow in sewer lines. A company or facility that discharges solids which cause a sewage backup is liable for any damages.
- pH – The pH of wastewater must typically remain between 5.0 and 12.5. In general, brewery wastewater is acidic. However, cleaning processes can cause high and low spikes. Brewery operations must maintain compliance with pH discharge limits. Wastewater that is too acidic (low pH) or too alkaline (high pH) can seriously corrode the sewer system and affect the wastewater treatment facility’s ability to treat the wastewater, so the pH must be controlled.
- Temperature – High temperature brewery wastewater can cause issues at wastewater treatment plants.
Continuous monitoring point
To ensure their wastewater meets requirements, the plants may be required by their municipality to have an easily accessible monitoring point. They must be able to monitor or collect samples that represent the discharge from the plant operations in a location that is separate from sanitary and restaurant drains. While small breweries may not always have a separate monitoring point, the municipality generally reserves the authority to require one and it is generally recommended.
Control Product losses/off-spec product
Sending excessive amounts of high strength waste to the sewer can disrupt the sewer system and/or increase a facility’s high strength surcharge fees. Plants need to minimize the volume of unused and off-spec product discharged to the public sewer whenever possible. If there is no other alternative than the sewer, the discharge still must meet local limits.
Chemical storage and spill prevention
Food processing factories typically provide secondary containment for chemical solutions such as cleaning and sterilization chemicals and waste materials to prevent the entry of these materials into the sewage system in case of accidental spills. A spill at a brewery will not be poisonous or contain hazardous wastes and will be things like beer, wort, yeast, caustic, or acid. They all present their problems, and they’re all major events when spilled in large amounts.
A spill that is primarily BOD, such as beer, wort, or yeast should be isolated in the calamity tank and hauled off site and applied as fertilizer. The other option is to slowly discharge this water to sewer every day for several days or weeks. Dilution does not fix the problem. A large spill of acid or caustic should be isolated in the calamity tank and neutralized with caustic or acid. Once neutralized it can be discharged to sewer or the industrial pre-treatment facility.
How can real-time viscosity and density measurements can enable better wastewater management in the food and beverage industry?
Continuous, inline process density & viscosity monitoring to guarantee a high standard in wastewater treatment
The BOD, COD and concentration of solids can be measured using different methods, direct or indirect. Typically, analysis is conducted offline by collecting samples and using laboratory test methods. These off-line methods can be time consuming and prone to delays and sometime inefficient in detecting critical events in a process line.
Wastewater treatment plants (WWTP’s) of breweries can monitor real-time density and viscosity of their wastewater stream to ensure their discharge does not have high BOD, COD peaks, TSS or accidental release of other substances, commonly referred to as a calamity event. Not only density and viscosity bear strong correlation with the BOD, COD, TSS and other substances, but also, they are the properties which greatly affect flow behaviour of the slurry. Hence, inline & continuous detection of viscosity and/or density and any unexpected trend in monitoring can enable operators take automatic or manual corrective actions. This measuring method can help to reduce the overall operating costs and makes it easier to comply with conditions for discharge consent. Upset process conditions – resulting in the destruction of the biological process – can be prevented and unintended spillage of raw material can be detected immediately. The process waste water can be diverted to ‘Calamity Tanks’ in occurrence of a process calamity event, for suitable discharge without unnecessary problems which could arise in treatment plants or non-compliance with municipality discharge regulations.
Calamity detection and automatic diversion of non-compliant discharge to calamity tanks
Measurement Challenges
Existing laboratory viscometers are of little value in process environments because viscosity is directly affected by temperature, shear rate and other variables that are very different off-line from what they are in-line. Traditionally, operators have measured the viscosity using the efflux cup or Zahn cup or other laboratory devices. The procedure is messy and time-consuming, inaccurate, inconsistent and non-repeatable even with an experienced operator.
Further, for calamity detection and fast response the plant needs real-time monitoring of its wastewater stream to take immediate corrective action. This is not possible without an inline sensor. Depending on taking a sample and running it in lab would be too late to take corrective action. Similarly, sensor/analysers installed on by-pass lines will miss out on detecting events if there is uneven mixing or blockage on the by-pass line – both extremely common issues with existing BOD, COD sensors that must be installed on by-pass lines.
Rheonics' Solutions
Automated in-line viscosity monitoring is crucial for ensuring wastewater compliance with treatment plant or municipal sewer requirements. Rheonics offers a turn-key wastewater management solutions, made of:
- In-line Viscosity measurements: Rheonics’ SRV is a is a wide range, in-line viscosity measurement device with inbuilt fluid temperature measurement and is capable of detecting viscosity changes within any process stream in real time.
- Rheonics Process Monitor: an advanced predictive tracking system to monitor in real-time variations of process conditions.
- Rheonics RheoPulse with Calamity detection and automatic diversion: a Level 4 autonomous system that ensures no wastewater compliance with set limits and automatically activates by-pass valves to redirect non-conforming wasterwater to a calamity tank.
- Rheonics RheoPulse with pH and Level: optionally available to monitor pH of the wastewater stream to ensure track and trace of all wastewater release in municipal wastewater sewer.
The SRV sensor is located in-line so that it continuously measures the wastewater viscosity (and density in case of SRD). Alerts can be configured to notify operator of necessary action or the entire management process can be fully automated with RPTC (Rheonics Predictive Tracking Controller). Using an SRV in a wastewater process line, results in improved social responsibility, productivity, profit margins and achieves regulatory conformance. The sensors have a compact form factor for simple OEM and retrofit installation. They require no maintenance or re-configurations. The sensors offer accurate, repeatable results no matter how or where they are mounted, without any need for special chambers, rubber seals or mechanical protection. Using no consumables and not requiring re-calibration, SRV and SRD are extremely easy to operate resulting in extremely low lifetime running costs.
Once the process environment is established, there is usually little effort required to maintain the integrity consistency of the systems – operators can rely on the tight control with Rheonics wastewater management solution.
Rheonics' Advantage
Compact form factor, no moving parts and require no maintenance
Rheonics’ SRV and SRD have a very small form factor for simple OEM and retrofit installation. They enable easy integration in any process stream. They are easy to clean and require no maintenance or re-configurations. They have a small footprint enabling Inline installation in large wastewater lines, avoiding any additional space or adapter requirement.
High stability and insensitive to mounting conditions: Any configuration possible
Rheonics SRV and SRD use unique patented co-axial resonator, in which two ends of the sensors twist in opposite directions, cancelling out reaction torques on their mounting and hence making them completely insensitive to mounting conditions and flow rates. These sensors can easily cope up with regular relocation. Sensor element sits directly in the fluid, with no special housing or protective cage required.
Instant accurate readouts on printing conditions – Complete system overview and predictive control
Rheonics’ RheoPulse software is powerful, intuitive and convenient to use. Real-time wastewater can be monitored on the integrated IPC or an external computer. Multiple sensors spread across the plant are managed from a single dashboard. No effect of pressure pulsation from pumping on sensor operation or measurement accuracy. No effect of vibration.
Inline measurements, no bypass line is needed
Directly install the sensor in your process stream to do real time viscosity (and density) measurements. No bypass line is required: the sensor can be immersed in-line; flow rate and vibrations do not affect the measurement stability and accuracy.
Easy installation and no reconfigurations/recalibrations needed – zero maintenance/down-times
In the unlikely event of a damaged sensor, replace sensors without replacing or reprogramming electronics. Drop-in replacements for both sensor and electronics without any firmware updates or calibration coefficient changes. Easy mounting. Screws into ¾” NPT thread weldolets. No chambers, O-ring seals or gaskets. Easily removed for cleaning or inspection. SRV is also available with flange and tri-clamp connection for easy mounting and dis-mounting.
Low power consumption
24V DC power supply with less than 0.1 A current draw during normal operation.
Fast response time and temperature compensated viscosity
Ultra-fast and robust electronics, combined with comprehensive computational models, make Rheonics devices one of the fastest and most accurate in the industry. SRV and SRD give real time, accurate viscosity (and density for SRD) measurements every second and are not affected by flow rate variations!
Wide operational capabilities
Rheonics’ instruments are built to make measurements in the most challenging conditions. SRV is available with the widest operational range in the market for inline process viscometer:
- Pressure range up to 5000 psi
- Temperature range from -40 up to 200°C
- Viscosity range: 0.5 cP up to 50,000 cP
SRD: Single instrument, triple function – Viscosity, Temperature and Density
Rheonics’ SRD is a unique product that replaces three different instruments for viscosity, density and temperature measurements. It eliminates the difficulty of co-locating three different instruments and delivers extremely accurate and repeatable measurements in harshest of conditions.
Manage wastewater more efficiently, cut down costs and enhance productivity
Integrate an SRV in the process line and ensure consistency over the years. SRV constantly monitors and controls viscosity (and density in case of SRD) and activates diversion to the calamity tank in case of an accidental spill, which could be fatal for treatment plants and possible non-compliance to the municipality norms. Optimise the wastewater management process with an SRV and experience fewer shutdowns, lesser non-compliances and material cost savings. And at the end of it all, it contributes to a better bottom line and a better environment!
Clean in place (CIP)
SRV (and SRD) monitors the cleanup of the fluid lines by monitoring the viscosity (and density) of the cleaner/solvent during the cleaning phase. Any small residue is detected by the sensor, enabling the operator to decide when the line is clean/fit for purpose. Alternatively, SRV (and SRD) provides information to the automated cleaning system to ensure full and repeatable cleaning between runs, thus ensuring full compliance in terms of sanitary standards of food manufacturing facilities.
Superior sensor design and technology
Sophisticated, patented 3rd generation electronics drive these sensors and evaluate their response. SRV and SRD are available with industry standard process connections like ¾” NPT, DIN 11851, Flange and Tri-clamp allowing operators to replace an existing temperature sensor in their process line with SRV/SRD giving highly valuable and actionable process fluid information like viscosity besides an accurate measurement of temperature using an in-build Pt1000 (DIN EN 60751 Class AA, A, B available).
Electronics built to fit your needs
Available in both an explosion-proof transmitter housing and a small-form factor DIN rail mount, the sensor electronics enables easy integration into process pipelines and inside equipment cabinets of machines.
Easy to integrate
Multiple Analog and digital communication methods implemented in the sensor electronics makes connecting to industrial PLC and control systems straightforward and simple.
ATEX & IECEx Compliance
Rheonics offers intrinsically safe sensors certified by ATEX and IECEx for use in hazardous environments. These sensors comply with the essential health and safety requirements relating to the design and construction of equipment and protective systems intended for use in potentially explosive atmospheres.
The intrinsically safe and explosion proof certifications held by Rheonics also allows for customization of an existing sensor, allowing our customers to avoid the time and costs associated with identifying and testing an alternative. Custom sensors can be provided for applications that require one unit up to thousands of units; with lead-times of weeks versus months.
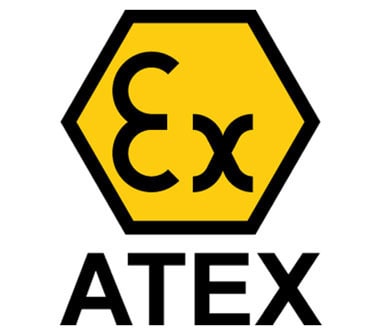
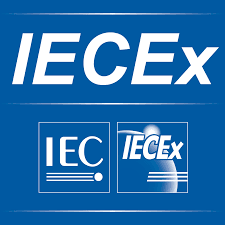
Implementation
Directly install the sensor to your process stream to do real time viscosity and density measurements. No by-pass line is required: the sensor can be immersed in-line. Flow rate and vibrations do not affect the measurement stability and accuracy. Optimize coating performance by providing repeated, consecutive, and consistent tests on the fluid.
Rheonics Instrument Selection
Rheonics designs, manufactures and markets innovative fluid sensing and monitoring systems. Precision built in Switzerland, Rheonics’ in-line viscometers and density meters have the sensitivity demanded by the application and the reliability needed to survive in a harsh operating environment. Stable results – even under adverse flow conditions. No effect of pressure drop or flow rate. It is equally well suited to quality control measurements in the laboratory. No need to change any component or parameter to measure across full range.
Suggested product(s) for the Application
- Wide viscosity range – monitor the complete process
- Repeatable measurements in both Newtonian and non-Newtonian fluids, single phase and multi-phase fluids
- Hermetically sealed, all stainless steel 316L wetted parts
- Built in fluid temperature measurement
- Compact form-factor for simple installation in existing process lines
- Easy to clean, no maintenance or re-configurations needed
- Single instrument for process density, viscosity and temperature measurement
- Repeatable measurements in both newtonian and non-newtonian fluids, single phase and multi-phase fluids
- All metal (316L Stainless Steel) construction
- Built in fluid temperature measurement
- Compact form-factor for simple installation in existing pipes
- Easy to clean, no maintenance or re-configurations needed