Processes in refineries where viscosity & density measurements and management play central role in refinery operations are the following:
- Accurate blending operations
- Refinery Oil Movement: Ensuring the right quality and quantity during transfers
- Improving refinery operations: Process unit mass balances and loss control
- Understanding the chemistry of crude oil blending for optimizations
An Overview of the Refining Process | Reference: American Petroleum Institute (https://www.api.org/)
Introduction
Crude oil availability and pricing are changing constantly. Under these dynamic circumstances, maintaining or increasing capacity while reducing costs becomes ever more complex for refineries. As operators navigate the road to greater efficiency and profitability, they depend on receiving consistently accurate process measurement data in all applications.
Petroleum remains one of the most important hydrocarbons in the global marketplace. It remains the primary source for liquid and transportation fuels, and a crucial raw material for the polymer industry. Viscosity is an important fluid characteristic for many reasons. It can be a functional property, or it can be correlated to an exclusive attribute. It can be related to utilization efficiency. More importantly, viscosity is an indication of how a fluid is handled—pumped, filtered and stirred.
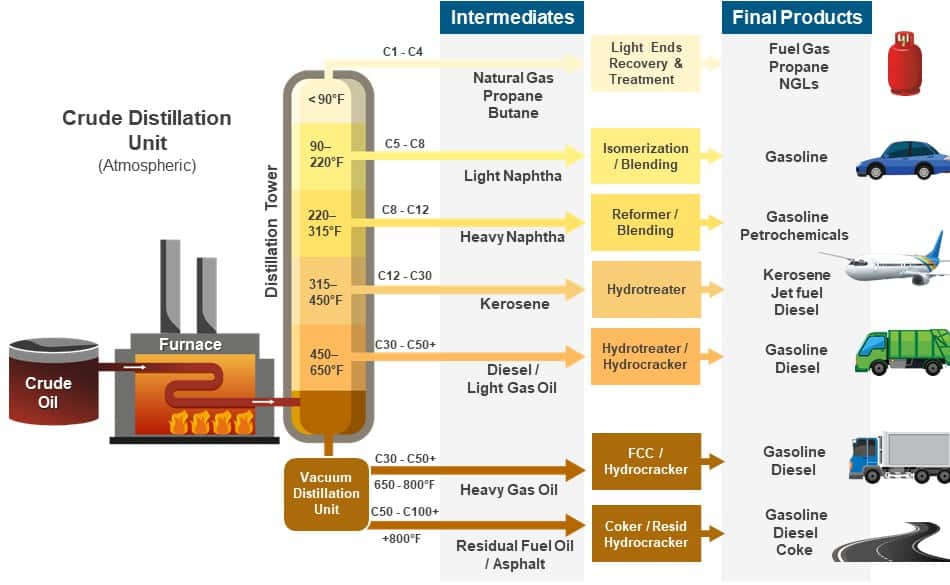
Refining Processes and Products | Source: Valero Energy (https://www.valero.com/)
Refined Petroleum Products and Their Uses
Each refined petroleum product obtained from crude oil has a specific use:
- Liquefied petroleum gas (LPG), also known as butane and propane, is used as an automotive fuel or packaged in bottles and used for household purposes.
- Gasoline and diesel are used as fuels for motor vehicles.
- Kerosene is used as jet fuel.
- Naphtha is a major petrochemical feedstock.
- Heating oil is used to heat
- Base oils are used to make lubricants.
- Asphalt, sometimes called bitumen, is used to pave roads.
Application
Crude oil is classified as light or heavy oil based on different physical properties, such as molecular weight, viscosity, density, and API gravity. Viscosity and density play very important roles in oil production, transportation through pipelines, and oil recovery processes.
Viscosity is one of the most critical measurement performed in a refinery. All customers buy refinery products distinguished by their viscosity grades, based on internationally accepted norms such as ASTM. Viscosity is central to determination of product quality. Also, it is critical to protection of process machinery such as pumps and compressors.
Refined products have been defined by their viscosity. Methods and technologies have been developed over time to give operators more control over their operations. Today, improvements in the measurement and control of viscosity are leading to massive increases in profitability for refiners. The difficulty and high costs of viscosity and density measurements at reservoir conditions are the main reasons for the lack of such data at other temperatures. Additionally, viscosity and density are important guidelines for numerical simulations to determine the economics and success of the Enhanced oil recovery (EOR) project.
Where do viscosity measurements add value in the chain?
Broadly the processes in refineries where viscosity measurements and management play central role in refinery operations are the following:
- Blending
- Transfers/Transportation
- Detection
- Metering
- R&D, Blending Chemistry
Accurate blending operations
Blending is the mixing of crude oils, condensates, or bitumen – all with varying properties and values – into one stream to make a new type of crude oil better suited for transport and refinery processing. The blending operation in refinery has many considerations. It is driven by –
- wellhead production volumes & quantities;
- logistics i.e. moving volumes to market using pipe, rail, barge;
- refinery feed slate requirements and process unit configurations.
The primary concern is the accurate proportions of each product blended into any given recipe. This blend accuracy depends on many variables within the system. The primary measuring device determines the overall system accuracy; thus, meter selection is of great importance.
Blending two or more crude oils to achieve the right balance of feed qualities can introduce unknown issues with crude incompatibilities. This in turn can introduce accelerated fouling, and thus additional energy costs with the crude unit fired heater and potential earlier shutdown for exchanger cleaning.
More often than not, it can be very difficult to differentiate between a leak and acceptable deviations from the model due to changing conditions in the pipeline, measurement errors and changes with temperatures and pressures. Reliable instrumentation is required to detect any change in the process stream and to enable operator to react effectively to any such change. There are several benefits with using instrumentation to monitor properties of blend in real-time and suitably choosing corrective interventions when necessary:
- Improvement in refinery specific product yields when processing shale oils and bitumen
- Suitable end-point detection of the mixing/blending operations to conserve energy and ensure quality
- Consistent feed stream quality to refineries processing unconventional heavy crude oils and domestic shale oils.
- More agility in dealing with variants: Using the crude oil and bitumen pricing variations in the market to advantage.
- Reduction in associated fouling and corrosion with improved emulsion level detection.
- Blending quality control with real time process automation instruments can reduce refinery upgradation needs.
Refineries utilize in-line viscosity measurements to enhance production consistency. The viscometer is located in a bypass line of a mainline, and is used to maintain the diluent addition to achieve the ideal customer specification the first time. Refineries using analyser driven blending system have capabilities to determine important properties of each crude oil. This enables blending adjustments to be made that can impact desired product quality and quantities. Scheduling is also improved by having visibility into incoming crude characteristics and additional onsite analysis before being charged to the crude unit.
Refinery Oil Movement: Ensuring the right quality and quantity during transfers
Custody transfer refers to the transactions involving transporting physical substance from one operator to another. Quality control during such operations is useful for assurance of the parties involved in the transaction.
Crude oil production must meet specific density, viscosity, and water cut specifications for custody transfer defined by pipeline companies. Not meeting these conditions prior to shipping can lead to significant reprocessing fees and operation downtime. Engineers are looking for a complete solution that enables accurate compliance measurement. They need to ensure crude oil quality meets or exceeds all required process conditions before a shipment leaves the facility or custody transfer point.
Onshore metering is one of the terminal activities where quality compliance with viscosity and density measurements are useful. When the crude oil comes ashore, it is metered. This impacts taxation or custody transfer payments. Comparable systems are used between buyer and seller and data is compared. Transfers between platform, pipeline and onshore storage & distribution are measurement opportunities, since each buyer wants to be certain of what has been supplied. Density measurements are useful for these estimations and calculations.
The major consideration for metering systems is the meter type for the application, with the primary factor for selecting a meter being viscosity and air vulnerability. Other influences need to be considered such as piping, vibrations, electrical installation, flow conditioning, chemical compatibility, system hydraulics, and past experience. A complete list of equipment choices includes the meter, strainer, control valve, and an air elimination system, which requires significant consideration as it must prevent any air from entering the metering system.
Improving refinery operations: Process unit mass balances and loss control
Process unit mass balances can be a challenge due to measurement errors. Without accurate measurement, real losses cannot be identified and optimization models become unreliable. Many refiners rely on volumetric and lab density measurements for their balances even though both measurements are impacted by changing process conditions. Inline density meter significantly improve balances by measuring online density, which can replace lab density measurements to give a more accurate calculation.
Understanding the chemistry of crude oil blending for optimizations
In addition to the proper infrastructure for blending at the terminal, understanding the chemistry of crude oil blending is critical. There are approximately 150+ crude oils traded internationally and these crude oils vary in characteristics, quality and properties. Crude oils, bitumen, and condensate blending operations depend on their physical and chemical properties to meet the refiner’s specifications.
Viscosity and density are important physical properties of crude oil. However, there is a dearth of practical models for the calculation of these properties for heavy oil at elevated temperatures. Viscosity and density meters can enable engineers to obtain exact models that can successfully predict these two important fluid properties and optimize blending processes for different fluids across a wide range of temperatures.
On-line characterization of crude oil qualities provides an effective tool to utilize crude oils to receive the highest refining margin at lowest cost. This obliges refineries and blending stations frequently to change the crude oil quality, according to the refinery equipment and the global market prices of different crude oils.
Issues with traditional approach
For viscosity measurements in refineries, off-line measurement using the ASTM-D445 method is the traditional approach. Apart from the manual tasks and intensive maintenance involved, there is some major drawback to using the capillary tubes in the lab. They only give a snapshot of a very specific instant in time; the moment the sample was drawn. Real-time production fluid behaviors are not accurately characterized by lab measurements. When measurements are only done every 8-12 hours, there is always a chance of missing something. Returning to on-spec performance in refinery processes can easily take 10 hours or more. Refiners can burn through $100,000+ to $500,000 per occurrence.
Drawbacks with separate instruments for density and viscosity
Operators typically use separate instruments to measure density and viscosity. There are major issues in using two different instruments:
- Most traditional instruments used for density and viscosity measurement need separate fluid samples for analysis, using up large quantities of an extremely valuable fluid sample that cannot be reused
- Equal temperature and pressure conditions are hard to achieve in two separate instruments, leading to measurement errors
- Difficult to co-locate large, bulky density meters and viscometer due to space and mounting constraints
- Requires significant integration work in hardware and software to synchronize measurement data and ensure compliance
In refinery applications where producing off-spec material can cost hundreds of thousands of dollars per day, refiners are increasingly relying on real time continuous in-line measurements to extend traditional off-line lab tests to assure product quality. Technologies that are commonly used for in-line viscosity measurements are capillary, vibrational, and oscillating piston. All require conditioning of the fluid being tested so that it is as consistent as the lab samples are in terms of temperature, flow, and particles. The ROI for in-line viscosity control is measured in days for asphalts and lubrications oils. Rheonics’ torsional resonator principle is the preferred technology of in-line viscometers due to its inherent accuracy and reliability advantages over competing approaches. For refinery operations hard pressed to keep up with demand, this difference is critical.
Rheonics’ Solutions for Quality control and assurance of refinery processes
Automated in-line viscosity monitoring and control is crucial to viscosity control during blending and ensuring critical characteristics fully comply with requirements across multiple batches, without having to rely on offline measurement methods and sample taking techniques. Rheonics offers the following solutions for process control and optimization in the formulation, processing, scale-up, and testing.
Viscosity & Density Meters
- In-line Viscosity measurements: Rheonics’ SRV is a is a wide range, in-line viscosity measurement device capable of detecting viscosity changes within any process stream in real time.
- In-line Viscosity and Density measurements: Rheonics’ SRD is an in-line simultaneous density and viscosity measurement instrument. If density measurement is important for your operations, SRD is the best sensor to cater to your needs, with operational capabilities similar to the SRV along with accurate density measurements.
Integrated, turnkey quality management for refinery operations
Rheonics offers an integrated turn-key solution for quality management made of:
- In-line Viscosity measurements: Rheonics’ SRV – a wide range, in-line viscosity measurement device with in-built fluid temperature measurement
- Rheonics Process Monitor: an advanced predictive tracking controller to monitor and control in real-time variations of process conditions
- Rheonics RheoPulse with automatic dosing: A Level 4 autonomous system that ensures no compromise with set limits of viscosity and automatically activates by-pass valves or pumps to adaptively dose mixture components
The SRV sensor is located in-line so it continuously measures the viscosity (and density in case of SRD). Alerts can be configured to notify operator of necessary action or the entire management process can be fully automated with RPTC (Rheonics Predictive Tracking Controller). Using an SRV in the blending process line, results in improved productivity, profit margins and achieves regulatory conformance. Rheonics sensors have a compact form factor for simple OEM and retrofit installation. They require zero maintenance or re-configurations. The sensors offer accurate, repeatable results no matter how or where they are mounted, without any need for special chambers, rubber seals or mechanical protection. Using no consumables and not requiring re-calibration, SRV and SRD are extremely easy to operate resulting in extremely low lifetime running costs.
Once the process environment is established, there is usually little effort required to maintain the integrity consistency of the systems – operators can rely on the tight control with Rheonics refinery quality management solution.
Refineries can make the best use of advances in automation technology by Rheonics
Rheonics automation systems include features beyond the legacy systems such as embedded advanced process control algorithms, statistical monitoring, smart device monitoring and asset health monitoring. They bring the process and asset condition data to both operations and maintenance, enabling new and efficient ways to integrate work processes and improve timeliness and accuracy of decisions.
Rheonics' Advantage
Compact form factor, no moving parts and require no maintenance
Rheonics’ SRV and SRD have a very small form factor for simple OEM and retrofit installation. They enable easy integration in any process stream. They are easy to clean and require no maintenance or re-configurations. They have a small footprint enabling Inline installation in any process line, avoiding any additional space or adapter requirement.
High stability and insensitive to mounting conditions: Any configuration possible
Rheonics SRV and SRD use unique patented co-axial resonator, in which two ends of the sensors twist in opposite directions, cancelling out reaction torques on their mounting and hence making them completely insensitive to mounting conditions and flow rates. Sensor element sits directly in the fluid, with no special housing or protective cage requirements.
Instant accurate readouts on production quality – Complete system overview and predictive control
Rheonics’ RheoPulse software is powerful, intuitive and convenient to use. Real-time process fluid can be monitored on the integrated IPC or an external computer. Multiple sensors spread across the plant are managed from a single dashboard. No effect of pressure pulsation from pumping on sensor operation or measurement accuracy. No effect of vibration.
Inline measurements, no bypass line is needed
Directly install the sensor in your process stream to do real time viscosity (and density) measurements. No bypass line is required: the sensor can be immersed in-line; flow rate and vibrations do not affect the measurement stability and accuracy.
Easy installation and no reconfigurations/recalibrations needed – zero maintenance/down-times
In the unlikely event of a damaged sensor, replace sensors without replacing or re-programming electronics. Drop-in replacements for both sensor and electronics without any firmware updates or calibration changes. Easy mounting. Available with standard and custom process connections like NPT, Tri-Clamp, DIN 11851, Flange, Varinline and other sanitary and hygienic connections. No special chambers. Easily removed for cleaning or inspection. SRV is also available with DIN11851 and tri-clamp connection for easy mounting and dis-mounting. SRV probes are hermetically sealed for Clean-in-place (CIP) and supports high pressure wash with IP69K M12 connectors.
Rheonics instruments have stainless steel probes, and optionally provide protective coatings for special situations.
Low power consumption
24V DC power supply with less than 0.1 A current draw during normal operation.
Fast response time and temperature compensated viscosity
Ultra-fast and robust electronics, combined with comprehensive computational models, make Rheonics devices one of the fastest, versatile and most accurate in the industry. SRV and SRD give real-time, accurate viscosity (and density for SRD) measurements every second and are not affected by flow rate variations!
Wide operational capabilities
Rheonics’ instruments are built to make measurements in the most challenging conditions.
SRV is available with the widest operational range in the market for inline process viscometer:
- Pressure range up to 5000 psi
- Temperature range from -40 up to 200°C
- Viscosity range: 0.5 cP up to 50,000 cP (and higher)
SRD: Single instrument, triple function – Viscosity, Temperature and Density
Rheonics’ SRD is a unique product that replaces three different instruments for viscosity, density and temperature measurements. It eliminates the difficulty of co-locating three different instruments and delivers extremely accurate and repeatable measurements in harshest of conditions.
Manage blending more efficiently, cut down costs and enhance productivity
Integrate an SRV in the process line and ensure consistency over the years. SRV constantly monitors and controls viscosity (and density in case of SRD) and activates valves adaptively for dosing the mixture constituents. Optimise the process with an SRV and experience fewer shutdowns, lower energy consumption, lesser non-compliances and material cost savings. And at the end of it all, it contributes to a better bottom line and a better environment!
Superior sensor design and technology
Sophisticated, patented electronics is the brain of these sensors. SRV and SRD are available with industry standard process connections like ¾” NPT, DIN 11851, Flange and Tri-clamp allowing operators to replace an existing temperature sensor in their process line with SRV/SRD giving highly valuable and actionable process fluid information like viscosity besides an accurate measurement of temperature using an in-build Pt1000 (DIN EN 60751 Class AA, A, B available).
Electronics built to fit your needs
Available in both a transmitter housing and a small-form factor DIN rail mount, the sensor electronics enables easy integration into process lines and inside equipment cabinets of machines.
Easy to integrate
Multiple Analog and digital communication methods implemented in the sensor electronics makes connecting to industrial PLC and control systems straightforward and simple.
Analog and Digital Communication Options
Optional Digital Communication Options
ATEX & IECEx Compliance
Rheonics offers intrinsically safe sensors certified by ATEX and IECEx for use in hazardous environments. These sensors comply with the essential health and safety requirements relating to the design and construction of equipment and protective systems intended for use in potentially explosive atmospheres.
The intrinsically safe and explosion proof certifications held by Rheonics also allows for customization of an existing sensor, allowing our customers to avoid the time and costs associated with identifying and testing an alternative. Custom sensors can be provided for applications that require one unit up to thousands of units; with lead-times of weeks versus months.
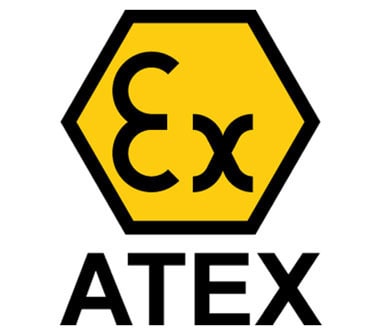
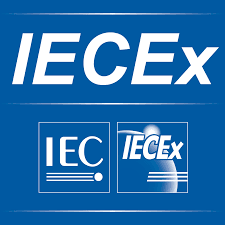
Implementation
Directly install the sensor in your process stream to do real-time viscosity and density measurements. No bypass line is required: the sensor can be immersed in-line; flow rate and vibrations do not affect the measurement stability and accuracy. Optimize mixing performance by providing repeated, consecutive, and consistent tests on the fluid.
In-line Quality control locations
- In tanks
- In the connecting pipes between various processing containers
Instruments/Sensors
SRV Viscometer OR an SRD for additional density
Rheonics Instrument Selection
Rheonics designs, manufactures and markets innovative fluid sensing and monitoring systems. Precision built in Switzerland, Rheonics’ in-line viscometers and density meters have the sensitivity demanded by the application and the reliability needed to survive in a harsh operating environment. Stable results – even under adverse flow conditions. No effect of pressure drop or flow rate. It is equally well suited to quality control measurements in the laboratory. No need to change any component or parameter to measure across full range.
Suggested product(s) for the Application
- Wide viscosity range – monitor the complete process
- Repeatable measurements in both Newtonian and non-Newtonian fluids, single phase and multi-phase fluids
- Hermetically sealed, all stainless steel 316L wetted parts
- Built in fluid temperature measurement
- Compact form-factor for simple installation in existing process lines
- Easy to clean, no maintenance or re-configurations needed
- Single instrument for process density, viscosity and temperature measurement
- Repeatable measurements in both newtonian and non-newtonian fluids, single phase and multi-phase fluids
- All metal (316L Stainless Steel) construction
- Built in fluid temperature measurement
- Compact form-factor for simple installation in existing pipes
- Easy to clean, no maintenance or re-configurations needed