Polyurethane production application
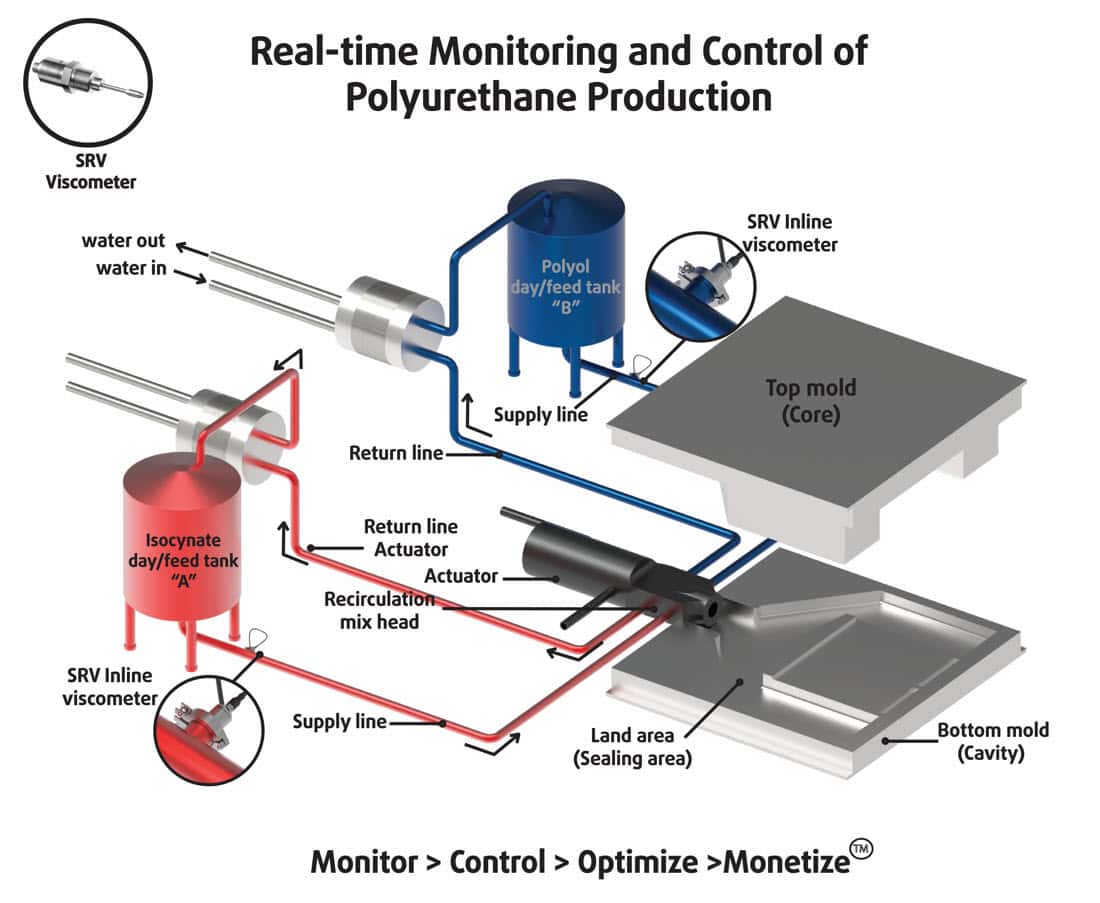
Polyurethane is a versatile material with a wide range of applications, including adhesives, sealants, coatings, foams, and elastomers. It is produced by reacting a polyol (a polyalcohol) with a diisocyanate (a compound with two isocyanate groups). The reaction can be carried out in a variety of ways, but the most common process is a two-step polymerization reaction:
Step 1: The polyol and diisocyanate are reacted to form a prepolymer. The prepolymer is a low-viscosity liquid that can be easily processed and transported.
Step 2: The prepolymer is then reacted with a chain extender (a short-chain polyol or diamine) to form the final polyurethane polymer. The chain extender controls the molecular weight and crosslinking of the polymer, which determines its properties.
Step 3: The mixture of the prepolymer and the chain extender is injected into molds depending on the customer’s requirements.
Step 4: The final product is stored, packaged, and distributed to the customer.
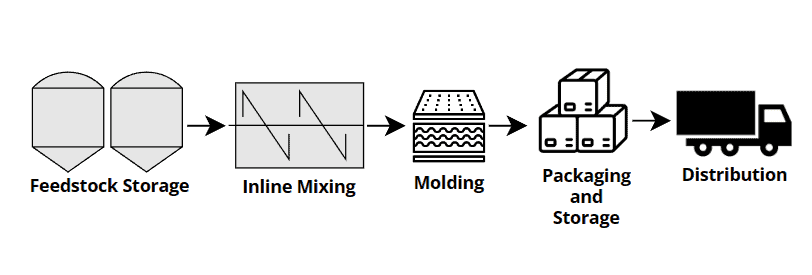
Polyurethane production process
Viscosity is an important parameter to monitor and control throughout the polyurethane production process. In step 1, the viscosity of the prepolymer affects its processibility. If the viscosity is too high, the prepolymer will be difficult to pump and mix. If the viscosity is too low, the prepolymer may not be able to support the weight of the fillers and additives that are added to it.
In step 2, the viscosity of the prepolymer and chain extender mixture affects the reaction kinetics. If the viscosity is too high, the reaction rate will be slow. If the viscosity is too low, the reaction rate may be too fast, which can lead to side reactions and defects in the final product.
SRV Inline viscometer is used to monitor and control the viscosity of the prepolymer and chain extender mixture at various points in the polyurethane production process. For example, The SRV is used to:
- Ensure that the prepolymer viscosity is within the specified range before it is fed into the reactor.
- Monitor the viscosity of the prepolymer and chain extender mixture during the reaction to ensure that the reaction is proceeding at the desired rate.
- Control the addition of a chain extender to ensure that the final polyurethane polymer has the desired molecular weight and crosslinking.
Inline process viscometers are typically installed in a pipe or pipeline carrying the prepolymer and chain extender mixture. The viscometer measures the viscosity of the mixture in real time and sends the data to a controller. The controller can then be used to adjust the feed rate of the reactants or to add other additives to control the viscosity.
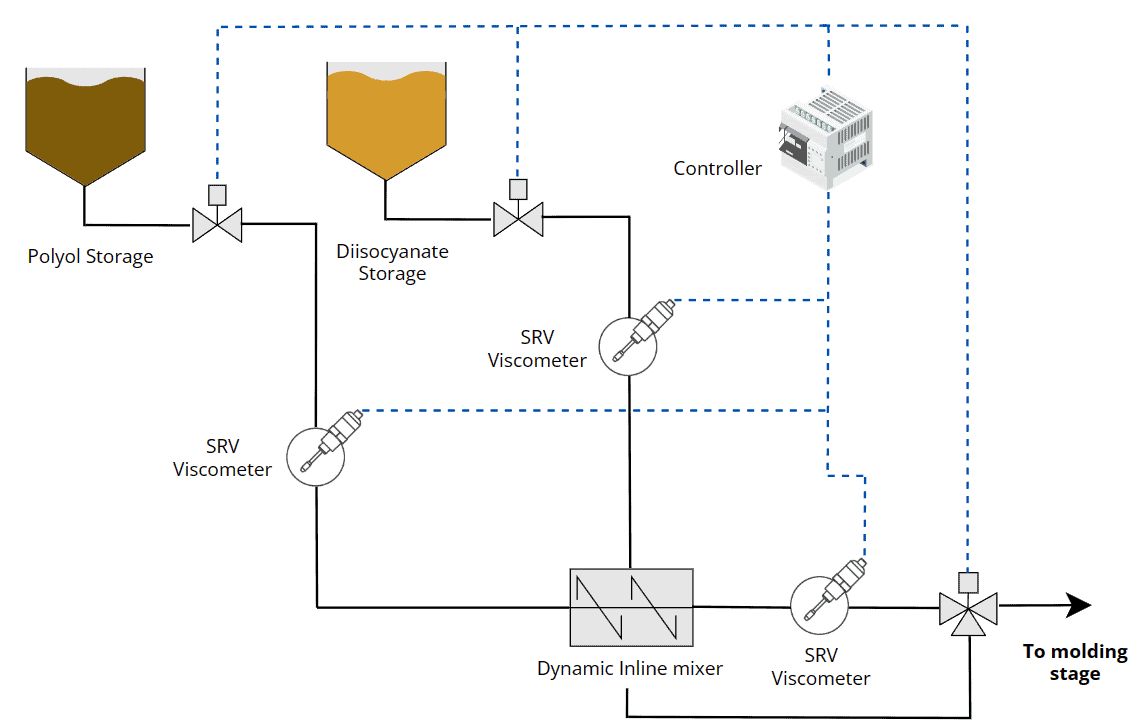
Inline process Viscometer SRV controls the viscosity of the feed products and the mixing result
Polyol Installation Line
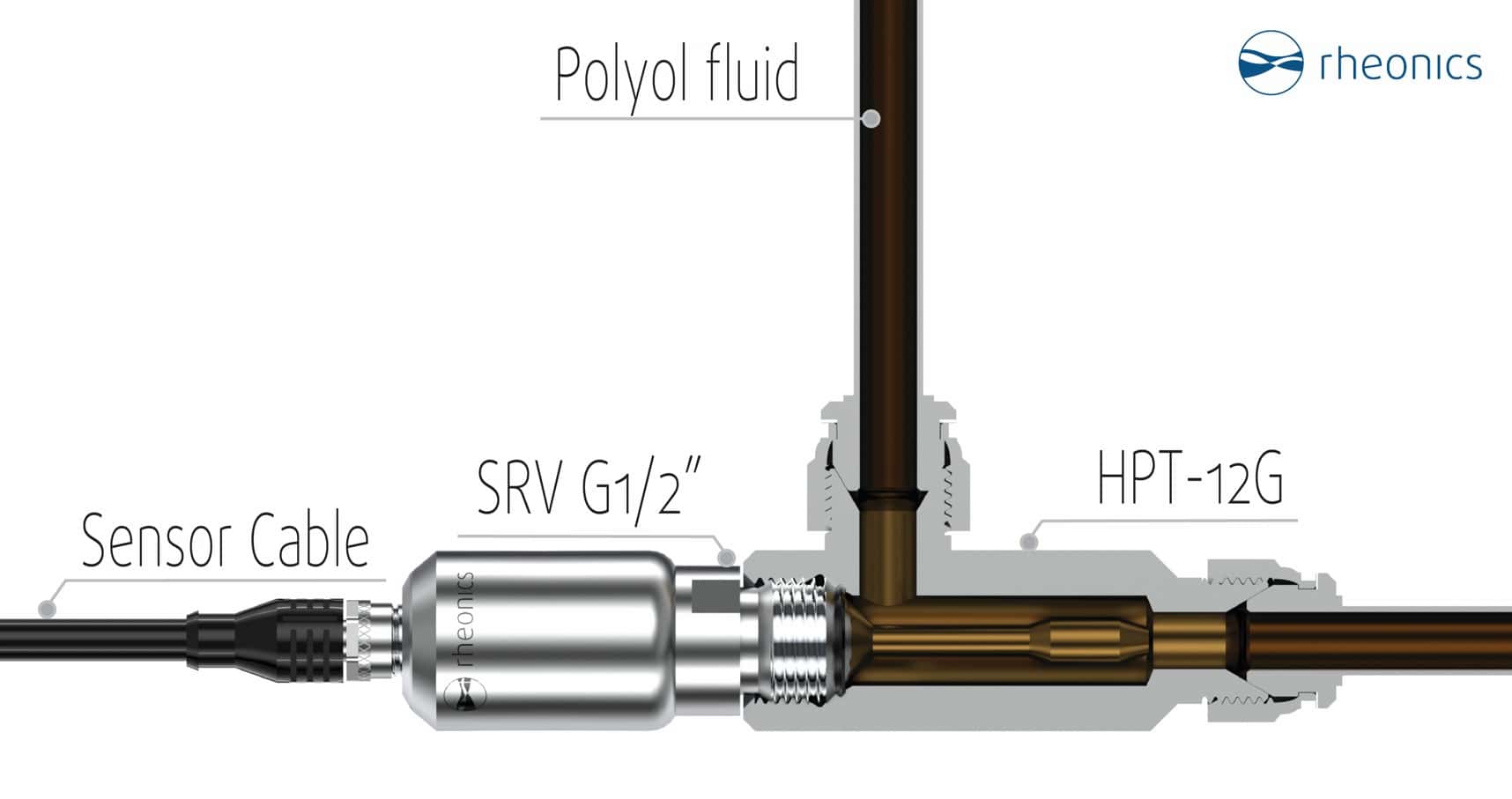
Isocyanate Installation Line
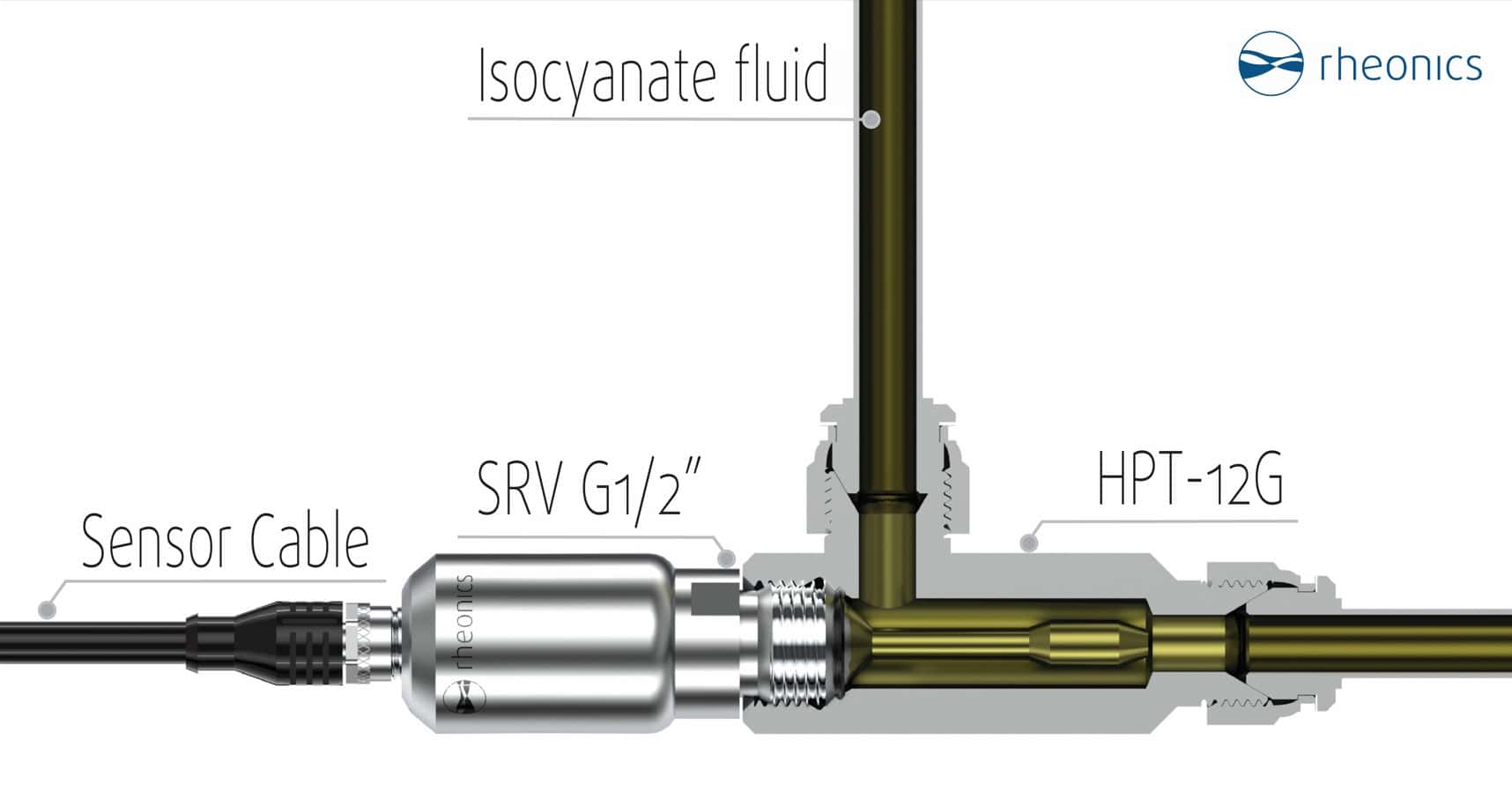
Key benefits to using SRV inline process viscometers in polyurethane production:
- Improved product quality: By monitoring and controlling viscosity, inline viscometers help to produce polyurethane polymers with consistent properties.
- This leads to improved product quality and performance.
Reduced waste: Tight quality control through real-time measurement from the viscosity sensor in the line reduces waste by preventing the production of out-of-spec products. - Increased efficiency: SRV Helps increase production efficiency by eliminating the need for manual sampling and testing.
Overall, inline process viscometers like the SRV are a valuable tool for monitoring and controlling viscosity in polyurethane production. Real-time monitoring and control of the incoming raw materials, mixing process and reaction improve product quality, reduce waste, and increase efficiency.
Suggested product(s) for the Application
- Wide viscosity range – monitor the complete process
- Repeatable measurements in both Newtonian and non-Newtonian fluids, single phase and multi-phase fluids
- Hermetically sealed, all stainless steel 316L wetted parts
- Built in fluid temperature measurement
- Compact form-factor for simple installation in existing process lines
- Easy to clean, no maintenance or re-configurations needed