Rheonics viscometer and density meters for slurries
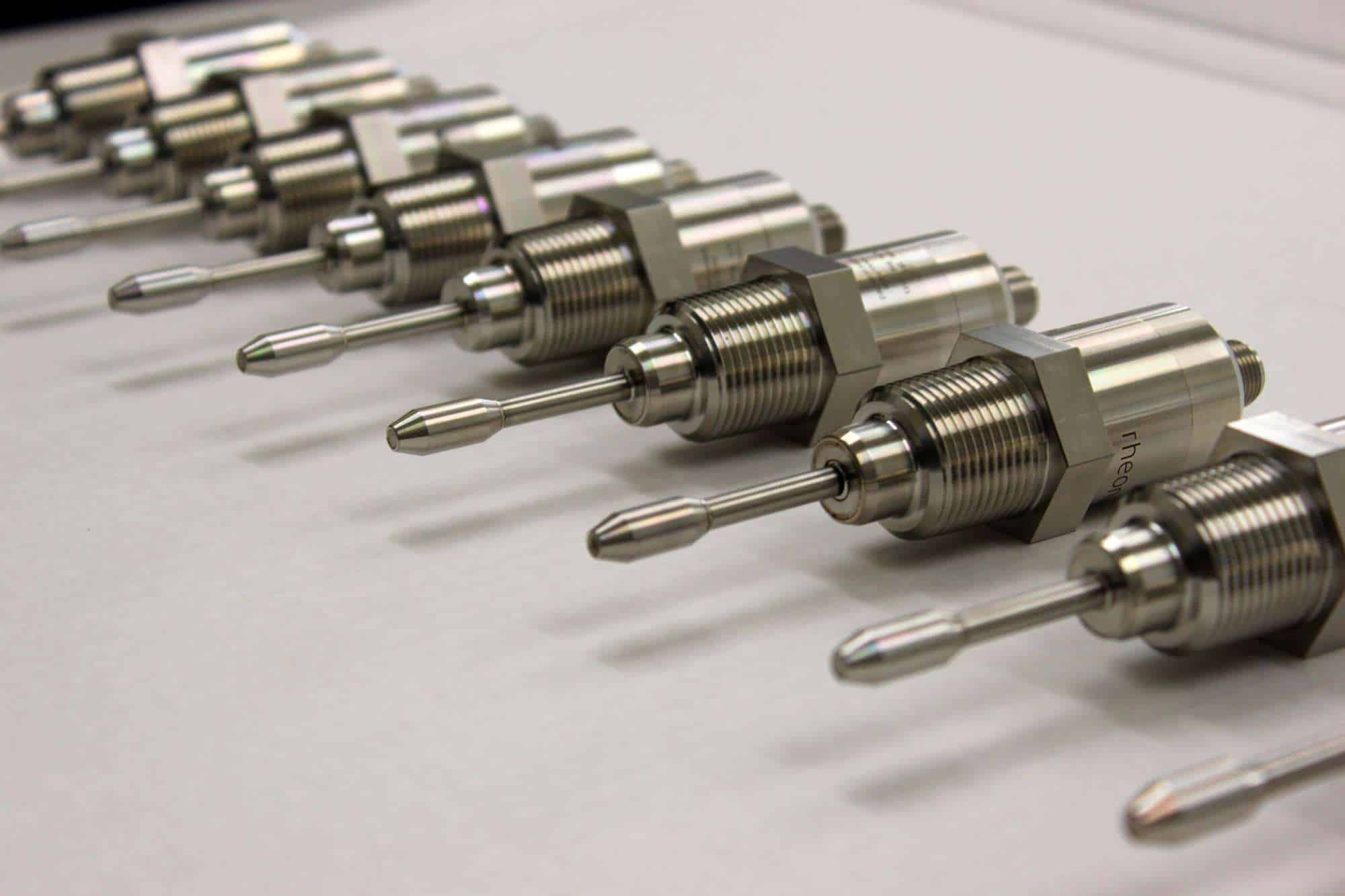
Slurry is a mixture of liquid and solid materials, that can have a fluid- or solid-like behavior depending on the percentage of the materials that compose it. This term is broadly used in multiple industries and manufacturing processes. However, all slurries can be studied from their rheology properties, which indicate important characteristics such as cohesion, stability, ease of mixing, etc.
Rheonics sensors can be used to monitor and control the viscosity and density parameters of industrial slurries. Some common slurries are described below.
Semiconductor Chemical Mechanical Polishing (CMP) slurry
CMP slurry is a water-based solution that contains chemicals and abrasive nanoparticles. It is used in precision surface polishing or planarization process through mechanical (abrasion) and chemical (etching) actions. It enables manufacturers to reduce the sizes of chips and create smoother and flawless wafer flat surfaces. It ultimately helps to improve performance and cut the costs of semiconductors. The process consists of a rotating disk with a slurry layer in which the wafer surface is placed, rotated and pressed against.
Challenges:
- The CMP process’s increasing complexity has made slurry quality standards more stringent.
- It is hard to continuously monitor and control the properties of the slurry throughout the entire process (including transport, handling, blending, filtration and dispensing).
- Monitoring of viscosity can determine the particle size and distribution properties of the slurry (consistency).
- Density has an impact on the uniformity of the slurry and helps as an indicator of the slurry components and blend properties.
Rheonics solution:
Rheonics offers inline viscosity readings with the SRV sensor and inline density and viscosity readings with the SRD. These solutions enable an automated in-line viscosity measurement and control, crucial to control the viscosity during CMP processes and ensure critical characteristics are in full compliance with requirements across multiple batches, without having to rely on offline measurement methods and sample-taking techniques.
More information: Semiconductor CMP (chemical mechanical polishing) slurry quality control through density and viscosity monitoring
Investment casting slurry
Description: Also known as ceramic slurry, it is used in the investment casting manufacturing process. A wax pattern is coated with the slurry, that once hardened, creates a mold with an internal geometry after the wax melts. Then molten metal is poured into the cavity and it solidifies. Finally, the mold is broken out resulting in a metal piece with specific geometry.
Challenges:
- Investment shells must comply with process specifications.
- The viscosity of the slurry will highly impact the surface finish, consistency, thermal conductivity, strength and other relevant characteristics of the shell
- External factors like temperature, shear rate and others, affect viscosity.
- Offline measurement techniques are time-consuming and cost-ineffective.
- Traditional Zhan cups instruments for viscosity measurement are inaccurate, inconsistent and non-repeatable.
Rheonics solution:
Rheonics offers automated inline sensors for viscosity and density for control and monitoring process variables. The inline SRV sensor is used to measure a wide viscosity range detecting minimal changes in viscosity. If density is of relevance, the inline SRD is the best solution to monitor a wide range of density and viscosity simultaneously during slurry production.
More information: Monitoring and controlling viscosity of ceramic slurries in investment casting
Drilling mud slurry
Description:
Drilling fluids or muds are key to a successful drilling process often used in oil and natural gas wells. The drilling fluid is necessary when the drilling occurs and when it stops. During drilling, the fluid or mud reduces working stresses, working as lubrication and cooling of the drill. When the drilling stops, the fluid avoids the well’s cuttings from refilling the wellhole applying the required pressure on the well’s walls.
Challenges:
- Properties such as the density and viscosity of the drilling fluid or mud must be within the designed specifications.
- Density is key to determine the mud weight, related to the pressure applied on the walls of the well.
- Viscosity varies during the process, when drilling you want a fluid-behavior mud to favor the movement, whereas when drilling stops, you require a more solid behavior to avoid cuttings from refilling the hole.
- Measuring viscosity and density with traditional instrumentation is slow, labor-intensive, time-consuming and prone to inaccuracies.
Rheonics solution:
Rheonics enables continuous, accurate, real-time mud density and viscosity data measured by the single inline Rheonics SRD sensor. This drilling fluid data offers an effective means to control mud and its costs. Drilling performance is optimized by the ability to recognize changes in the drilling fluid, analyze data trends and act upon what is causing changes in real time.
More information: Mud Weight Monitoring
Battery electrode slurry
Description: This slurry is a mixture of active material, conducting material and polymeric binder with a solvent, th
at is scattered in a copper or aluminum film. It is involved in the production of lithium-ion batteries during the mixing and coating processes.
Challenges:
- The physical properties of the slurry will define the dispersion of constituents and their states, which are key for the design and development of mixing and coating processes during the production of lithium-ion batteries.
- Maximum homogeneity of the slurry
- Uniform coating thickness with the correct layer density
- Precise slurry viscosity to ensure resistance to sedimentation
- Electrode density affects the cycle performance and capacity loss in lithium-ion batteries.
Rheonics solution: Rheonics SRV and SRD have a very small and compact design for simple OEM and retrofit installation, causing an insignificant pressure drop in the line. The viscosity (SRV and SRD) and density (SRD) readings from the sensors are extremely accurate and highly repeatable useful for monitoring and control.
More information: Battery production – Slurry Mixing and Coating
Suggested product(s) for the Application
- Wide viscosity range – monitor the complete process
- Repeatable measurements in both Newtonian and non-Newtonian fluids, single phase and multi-phase fluids
- Hermetically sealed, all stainless steel 316L wetted parts
- Built in fluid temperature measurement
- Compact form-factor for simple installation in existing process lines
- Easy to clean, no maintenance or re-configurations needed
- Single instrument for process density, viscosity and temperature measurement
- Repeatable measurements in both newtonian and non-newtonian fluids, single phase and multi-phase fluids
- All metal (316L Stainless Steel) construction
- Built in fluid temperature measurement
- Compact form-factor for simple installation in existing pipes
- Easy to clean, no maintenance or re-configurations needed