Introduction
The engineering of well logging sensors into the drill collars is simulating a revolution in logging and drilling. LWD, MWD and traditional wireline fluid sampling systems provide the driller comprehensive real-time information, and enable a geologist to study the formation while the invasion is taking place. The growing number of directional, extended-reach and highly deviated wells means that MWD/LWD technologies are often indispensable for an efficient wellbore placement. Operators ask for a lot in their logging-while-drilling (LWD) and measurement-while-drilling (MWD) tools, which consume a sizeable chunk of the budget. It is expected to afford savings for oil companies by increasing the efficiency and effectiveness of their drilling programs. Using fluid analysis results, oil companies decide how to complete a well, develop a field, design surface facilities and ramp up production.
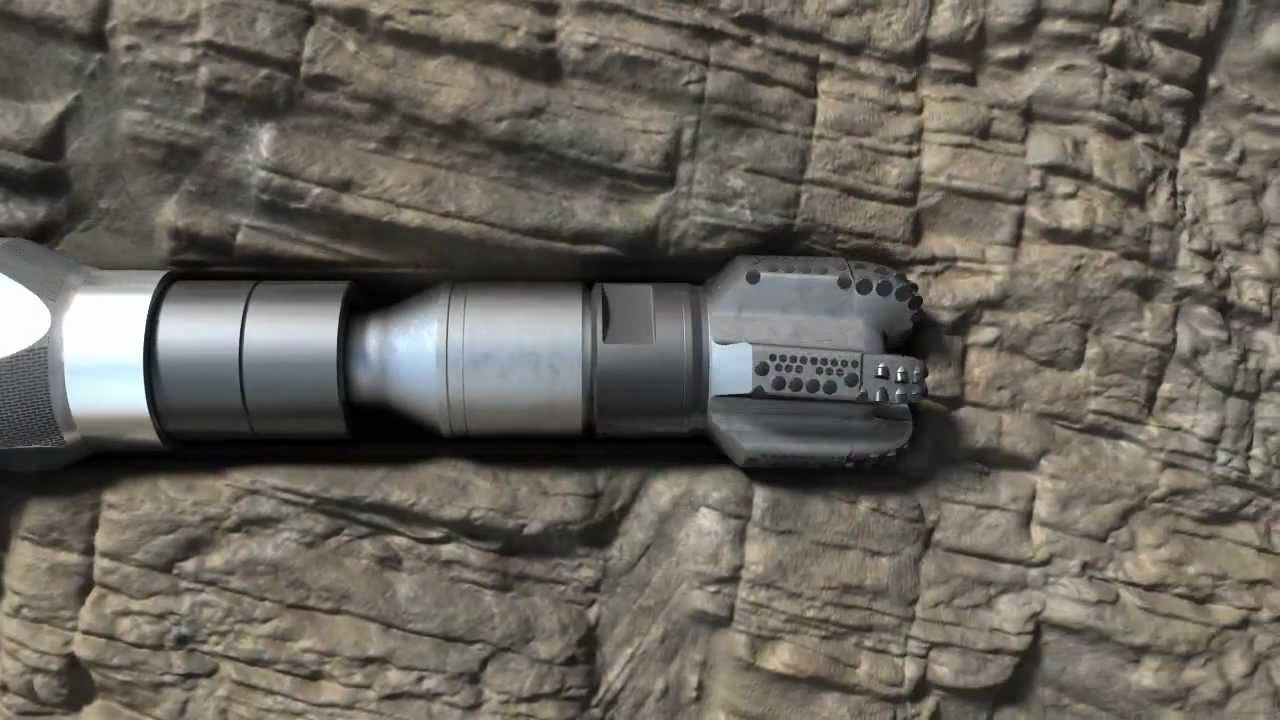
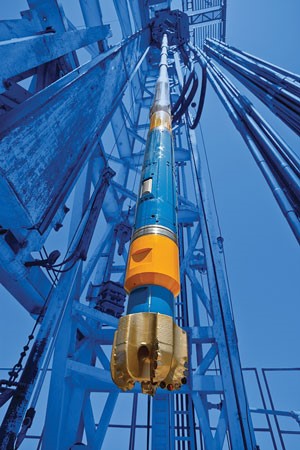
Application
The ability to characterize fluids as they are being produced is of great significance for reservoir studies. However, drilling environments are getting increasingly harsher and posing serious requirements on the downhole tools. LWD, MWD and wireline tools consist of sensors, electronics (and transmission in case of MWD) packages and provide information on directional survey, drilling mechanics and formation properties. After discovery of a reservoir, the need of characterization of the composition and physical properties of produced fluids is essential for the optimization of oil production. Real-time information about changes in flow characteristics and fluid composition during production requires downhole measurements that are able to probe the properties of the fluid in time scales shorter than those of the characteristic flow speeds.
Knowledge of formation fluid viscosity and density are key to reservoir management, oil production, completion design and to determine their field commerciality. Productivity and fluid displacement efficiency are directly related to fluid mobility, which in turn depend on its viscosity. Therefore, viscosity is a critical parameter for estimating the economic value of a hydrocarbon reservoir and also for analyzing compositional gradients and vertical and horizontal reservoir connectivity. Viscosity not only controls productivity and displacement efficiency of the reservoir, but also plays a major role when designing subsea hardware and pipelines and for managing flow assurance related concerns.
Drilling fluids are essential chemicals that are used for any oil well exploration activities like removal of cuttings from underneath the borehole, suspend and transport cuttings and to lubricate the drilling surface. One of the main functions of an oil drilling fluid is to impound the fluids formed during drilling to their surface beds and the density that it needs in order to effectively carry out this function is dependent on the subsurface formation pressures. Density measurements are used to calculate how freely oil and other fluids can flow through the formation, as well as the volume of hydrocarbons present in the rock and, with other data, the value of the whole reservoir and reservoir reserves. Density measures hydrostatic pressure in the borehole and solids content of unweighted muds. Proper density ensures sufficient hydrostatic pressure required to prevent the borehole wall from caving in and to keep formation fluid from entering the wellbore. But too high mud weight decreases rate of drilling and increases chances of differential sticking, fracturing the well, causes equipment wear, loss of circulation and increased mud cost. Density is the most crucial property of drilling fluids that needs to be measured and maintained effectively.
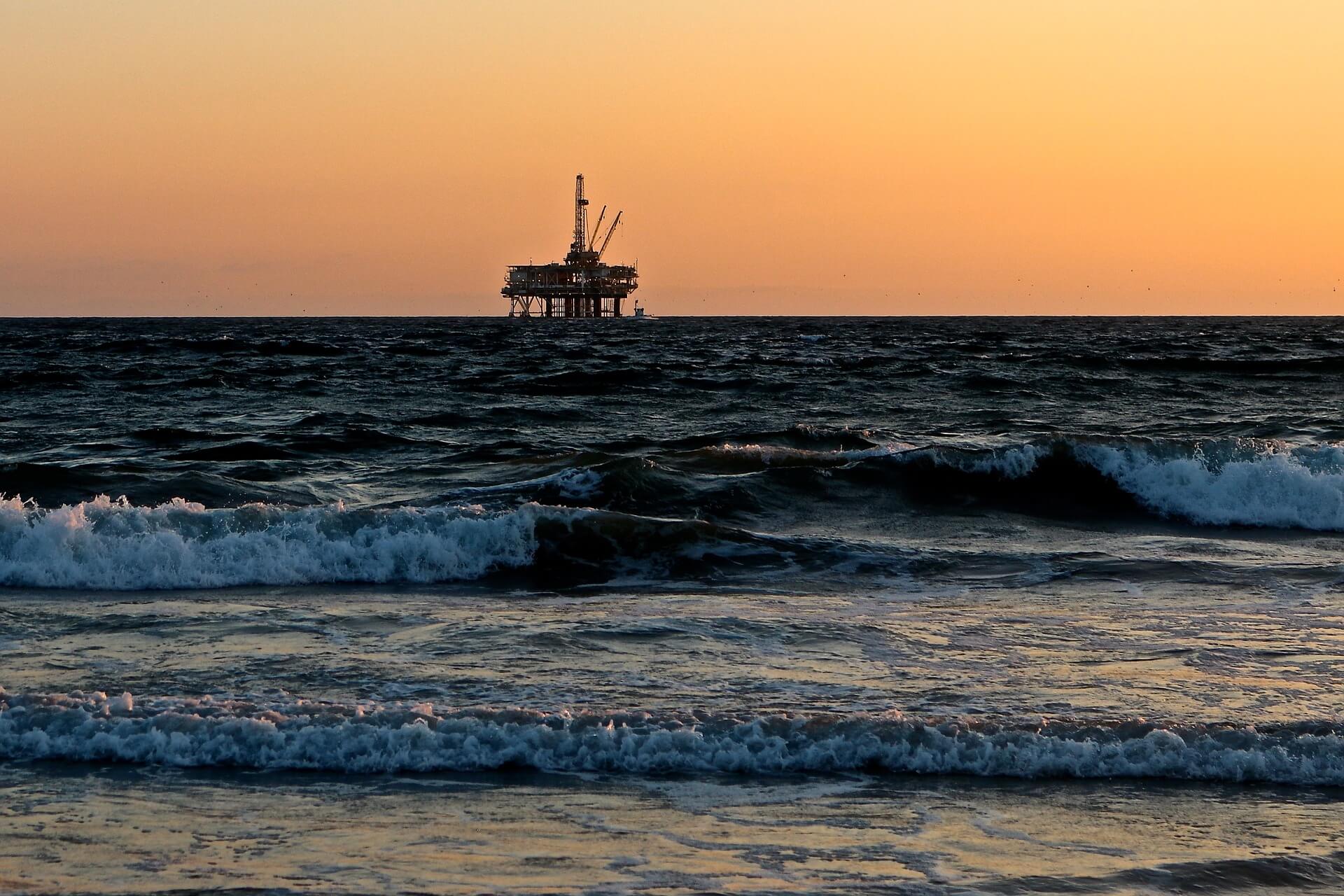
Problem Statement
Key requirements of density and viscosity measurement solutions in LWD, MWD and wireline tools are as follows:
- Remain unaffected by Bottom Hole Assembly Vibration: Downhole shock and vibration continue to be problematic, and the challenge is exacerbated by the increase in number of extended-reach and ultra-deep-water wells and the LWD/MWD tools are expected to be up for this challenge.
- Operate at High Pressures, High Temperatures: Components of LWD/MWD tools need to be operate at up to 200°C and 30,000 psi as dictated by the market requirements and in the field of reservoir management.
- Support high quality Fluid Sampling and Analysis: Analyzing fluid samples at reservoir conditions helps validate sample quality and enables mapping of vertical variations in fluid properties, allowing interpreters to determine zonal connectivity and define reservoir architecture early in field life. The systems need to deliver superior downhole measurements (such as density and viscosity) to support real-time identification and analysis of formation fluid properties in very short time scales.
- Reliability: The biggest value impact from LWD/MWD is to get it right the first time. The tools need to undergo all sorts of destruction testing, vibration testing, pressure testing before being used in downhole applications. Reduction in number of electronics boards and redundancy, and taking advantage of advances in computer/electronics industry to have smaller size of sensors that are less impacted by huge shocks and vibrations they experience downhole is extremely essential.
Process Challenges
Operators typically separate instruments to measure density and viscosity. There are major issues in using two different instruments:
- Most traditional instruments used for density and viscosity measurement need separate fluid samples for analysis which are extracted from downhole fluid sample cylinders, using up large quantities of an extremely valuable fluid sample that cannot be reused
- Same temperature and pressure conditions are harder to achieve in separate instruments, leading to measurement errors
- Difficult to co-locate large, bulky density meters and viscometer due to space and mounting constraints in LWD/MWD/wireline setups
- Needs significant integration work in hardware and software to synchronize measurement data and ensure compliance
Rheonics’ Density-Viscosity Measurement Integration in LWD/MWD/Wireline services
Deep water alone can make the acquisition of complete and reliable downhole data problematic, but add in the extreme temperatures and pressures and the difficulties/costs escalate considerably. Extreme HP/HT adversely impacts wireline and MWD/LWD tool reliability and performance. High temperatures damage tool electronics, affect sensor accuracy and precision, and can lead to premature tool failure if equipment is ill-designed for this service. Very high pressures and temperatures, shocks and vibrations, limited availability of power and severe space constraints on drilling rigs call for novel approaches to measurement instruments. This serves as the charter for Rheonics’ DV solutions for drilling applications.
Rheonics offers a technology platform composed of the sensor (DV) and electronics and offers integration and development services for simultaneous density and viscosity measurements in LWD, MWD and wireline logging tools – to acquire formation evaluation and drilling optimization data during drilling operations to guide well placement and to provide data for survey management and development planning.
Differentiating Rheonics is the development of high-temperature-rated downhole density and viscosity measurement tools that enable the successful drilling and evaluation of deep-water wells. New tool designs and electronics provide greater control in extreme temperature reservoirs, thus reducing the uncertainties of “drilling blind.” Key features of Rheonics’ custom built DV measurement solutions for integration in LWD/MWD/Wireline are as follows:
- Unaffected by BHA vibrations
- Operate well at HPHT conditions
- Drive high quality analysis of sampled fluid through most accurate and fastest density and viscosity measurements
- Extremely reliable in downhole conditions and deliver correct data every time; can sustain heavy shock and vibrations and are indifferent to mounting conditions
- Single instrument for density and viscosity measurements; requires extremely minimal quantity of fluid sample
- Extremely small form factor enabling easier integration
Operating Principle
The rheonics’ DVM measures viscosity and density by means of a torsional tuning fork resonator with flattened tine ends, which is immersed in the fluid under test. The more viscous the fluid, the higher the mechanical damping of the resonator, and the denser the fluid, the lower its resonant frequency. From the damping and resonant frequency, the density and viscosity may be calculated by means of rheonics’ proprietary algorithms. Thanks to rheonics’ coupled torsional resonator design (US patent number 9518906), the transducer is perfectly balanced, while maintaining excellent mechanical isolation from the sensor’s mounting. Damping and resonant frequency are measured by the rheonics sensing and evaluation electronics (US patent number 8291750). Based on rheonics’ proven gated phase-locked loop technology, the electronics unit offers stable and repeatable, high-accuracy readings over the full range of specified temperatures and fluid properties.
To know in detail about the technology of the rheonics’ torsional balanced resonators please refer to the whitepaper.
The Rheonics’ Advantage
Robust built and superior sensor technology
Rheonics’ DV has a compact form factor and uses patented balanced resonators to ensure consistent, reproducible measurements no matter how the DV is mounted. DV uses ultra-stable resonators, built using decades of experience in materials, vibrational dynamics and fluid-resonator interaction modelling that add up to the industry’s most robust, repeatable and well characterised sensors. These sensors are insensitive to mounting conditions, shocks and vibrations and have undergone all sorts of destruction, vibration and pressure testing.
Single instrument, dual function
Rheonics’ DV is a unique product that replaces two alternatives and offers better performance while operating at true reservoir conditions. It eliminates the difficulty of co-locating two different instruments for density and viscosity (and temperature as well).
Accurate, fast and reliable measurements
Sophisticated, patented 3rd generation electronics drive these sensors and evaluate their response. Great electronics, combined with comprehensive computational models, make the evaluation units one of the fastest and most accurate in the industry. DVM gives real time density and viscosity measurements in less than 2 seconds!
Accurate, fast and reliable measurements
Rheonics’ DVM are ultra-stable resonators. Sophisticated, patented 3rd generation electronics drive these sensors and evaluate their response. Great electronics, combined with comprehensive computational models, make the evaluation units one of the fastest and most accurate in the industry. DVM gives real time density and viscosity measurements in less than 2 seconds!
Widest operational capability
Rheonics’ extensive instrument capabilities enable users to carry out measurements in challenging reservoir conditions. It has the widest operational range in the market:
- Pressure range up to 30,000 psi
- Temperature range from -40 to 200°C
- Viscosity range: 0.02 to 300 cP
- Density range: 0 to 3 g/cc
Minimal sample size requirement
Minimal reservoir fluid is used for testing in the DV since there is no requirement of a separate line or sampling system. Safe and cost-effective to operate, DV requires only 0.7ml of sample to measure viscosity and density across the complete P,T range saving time and money.
Hassle free and convenient operation
DV eliminates the need for separate instruments for measuring density and viscosity which call for appreciably larger sample volumes, numerous reconfigurations and cumbersome fluid transfer systems. It can continuously track change of viscosity and density of live oil sample across the complete run and does not require any hardware change or reconfiguration. Rheonics’ software is powerful, intuitive and convenient to use. Using no mercury, timer or multiple pistons, DV is easy on the operations and environment.
Rheonics’ value proposition: The best in the industry
The following is a comparison of existing technologies of viscometers and density meters with Rheonics’ DV (torsional balanced resonator) in HPHT conditions.
Electronics built to fit your needs
Available in both an explosion-proof transmitter housing and a small-form factor DIN rail mount, the sensor electronics enables easy integration into process pipelines and inside equipment cabinets of machines.
Easy to integrate
Multiple Analog and digital communication methods implemented in the sensor electronics makes connecting to industrial PLC and control systems straightforward and simple.
Rheonics Instrument Selection
Precision built in Switzerland, the Rheonics’ DV is designed to match the application needs in the most challenging environment. Track the change of viscosity and density of the live oil sample across the complete run. No need to change any component or parameter to measure across full range.
Suggested solution for the Application
- Single unit for simultaneous density and viscosity measurement installed directly in LWD/MWD/Wireline setup
- Repeatable measurements in both newtonian and non-newtonian fluids
- No need to change any component or parameter to measure across full range
- Built in fluid temperature measurement
- Calibrated using NIST reference fluids up to +/- 1% viscosity accuracy (absolute) and Density accuracy: 0.001 g/cc or better
- Viscosity range: 0.2 to 300 cP (lower available)
- Density range: 0 to 1.5 g/cc (higher available)
- Maximum temperature : 200 °C