Rheonics vibrational sensor technology: demystified
Rheonics sensors employ patented balanced torsional resonators.
Temperature, pressure and external vibrations offer the greatest challenges to accurate and repeatable density and viscosity measurement. Rheonics balanced torsional resonators together with proprietary 3rd generation electronics and algorithms makes our sensors accurate, reliable and repeatable under the harshest operating conditions.
- Ultra-stable resonators, built on a foundation of more than 30 years experience in materials, vibration dynamics and fluid-resonator interaction modeling that add up to the industry’s most robust, repeatable and accurate sensors.
- Sophisticated, patented 3rd generation electronics to drive our sensors and evaluate their response. Great electronics, combined with comprehensive computational model make our evaluation units the fastest, most accurate in the industry.
At the heart of every Rheonics sensor is a resonator. Rheonics sensors are always in tune with the fluids they’re measuring!
The resonator vibrates in the fluid; the fluid influences the resonator’s vibrations. By measuring its effect on the the resonator, we can determine the fluid’s density and viscosity.
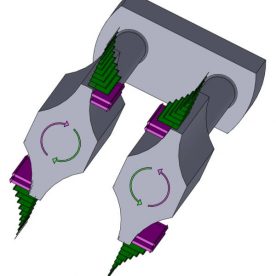
The denser the fluid, the lower the resonant frequency. A denser fluid increases the mass loading of the resonator.
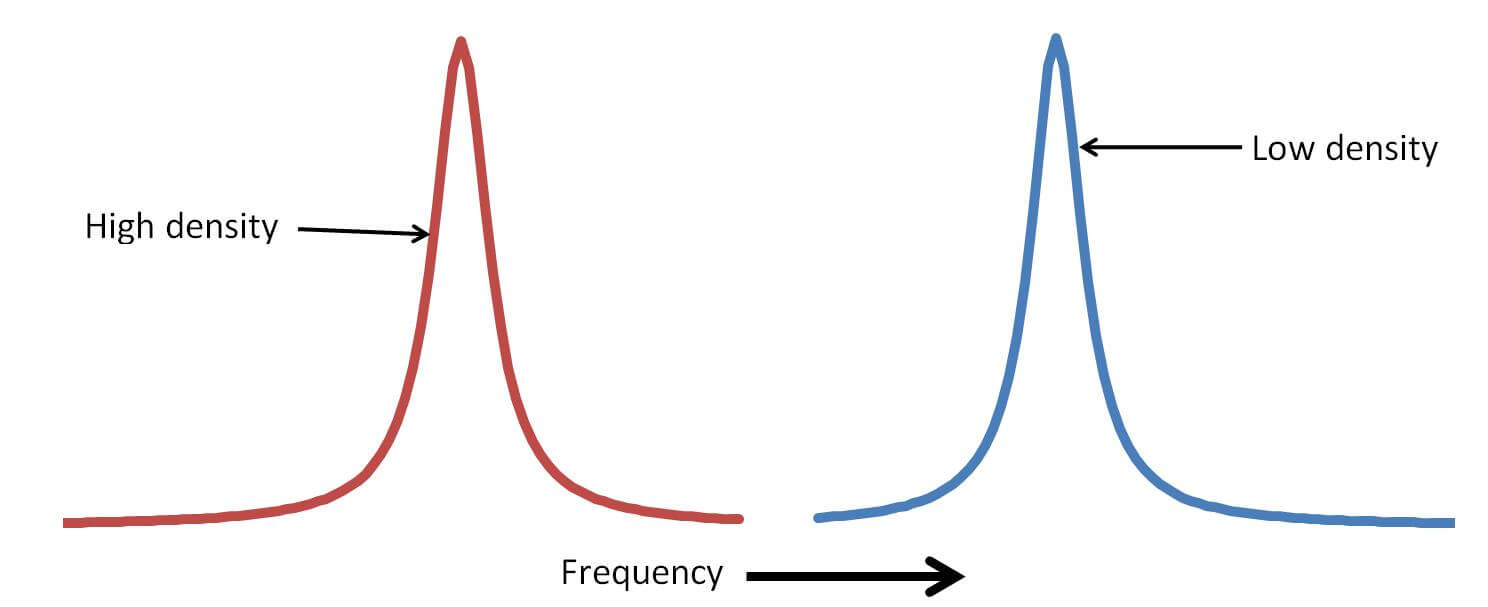
The more viscous the fluid, the broader and smaller the resonant peak of the sensor, Friction between the resonator and the fluid increases its damping.
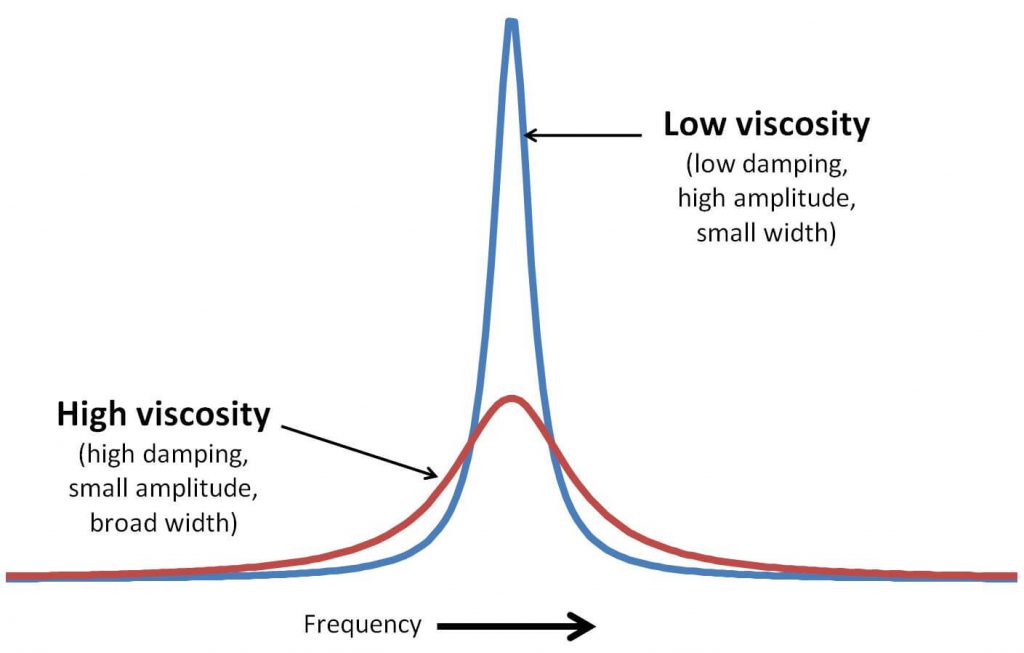
The measurable properties of the resonator – its resonant frequency and damping – are both influenced by the properties of the fluid.
Many types of fluid sensors use lateral vibrations. Vibrating wire viscometers, for instance rely on the displacement of the wire perpendicular to its long axis. Flexural tuning fork resonators have two tines that vibrate as cantilever beams, with motion perpendicular to the plane of symmetry of the tuning fork.
In general, sensors that vibrate laterally are harder to isolate from the structures in which they are mounted. Mounting forces, the mass of the mounting structures, and even temperature can influence the response of the resonators in ways that are unpredictable, and therefore influence the repeatability of measurements.
Rheonics sensors vibrate in torsion. Their active elements twist about their own axes, rather than vibrating laterally. Torsional sensors are easier to isolate from the structures in which they are mounted. They are also less disturbed by ambient vibrations than are lateral resonators
Shape of the resonator – determines the measurements
The shape of the resonator determines the way in which it responds to the fluid in which it is immersed. Rheonics’ SRV series of sensors are cylindrical, vibrating parallel to their own surfaces. They are influenced primarily by shearing forces, and are therefore relatively insensitive to mass loading effects. They are useful for measuring viscosity but not density.
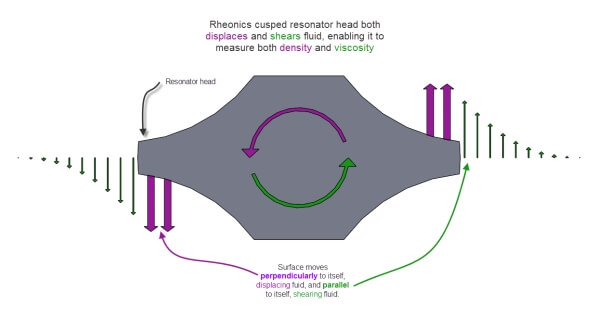
Rheonics’ DV series of sensors have flattened end masses. Parts of their surfaces vibrate parallel to themselves and therefore shear the fluid. These contribute to the damping of the resonator and determine its sensitivity to viscosity. Other parts of the surface vibrate perpendicular to themselves, and therefore displace the fluid. This results in mass loading of the sensor, and determines its sensitivity to density.
Resonant sensors fall into two further geometric categories – balanced and unbalanced.
A tuning fork is a typical balanced resonator. Its two tines vibrate in opposite directions, balancing out bending forces that are otherwise transmitted to the sensor’s mounting.
A single transversely vibrating beam ( a “half tuning fork” ) by comparison, exerts large reaction forces on its mounting, resulting in large energy loss compared to the balanced tuning fork geometry.
A vibrating wire, on the other hand, is an unbalanced resonator, and exerts substantial forces on its mounting structures.
In order to reduce the effects of mounting conditions on unbalanced resonators, their anchors must be relative large and massive compared to the size of the actual sensing element.
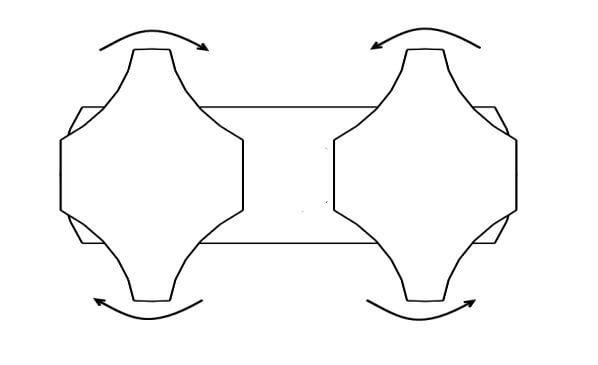
Insensitive to mounting conditions
Rheonics’ sensors use balanced resonators (patents pending). The DV series uses a torsional tuning fork configuration, in which the two tines twist in opposite directions. The SRV series uses a unique patented coaxial resonator, in which the two ends of the sensor twist in opposite directions, cancelling out reaction torques on their mounting.
Rheonics fluid sensing systems rely on patented technology that allows the use of one electronics platform – the evaluation unit – for all of our sensor products.
The core task of the evaluation unit is to drive and interrogate the resonant sensor in order to determine its resonant frequency and its damping. Once these two quantities have been determined, it is up to a sophisticated set of algorithms to convert these measurements into values for density and viscosity.
Our electronics platform is based on the phase shift method of evaluating the resonant frequency and damping of the resonant sensor, coupled with Rheonics’ patented gated phase-locked loop technology.
Sensor Technology, Working principle and Applications
Viscometers
Density Meters