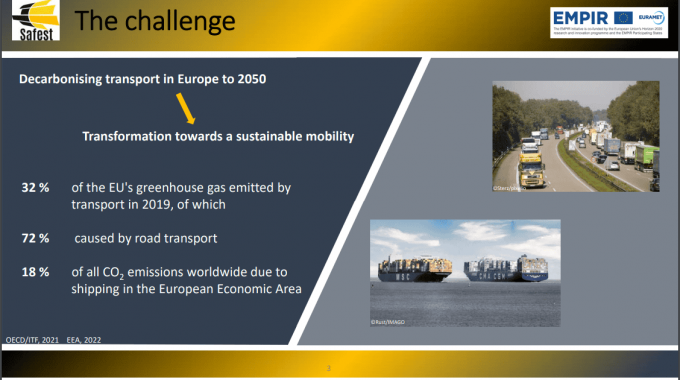
Rheonics process density meter for transportation fuel sustainability – SAFEST project by EMPIR EURAMET and Thermodynamics group at Imperial College London test
Rheonics inline density and viscosity sensors were used in the EMPIR EURAMET Safest project [1] and gave accurate viscosity and density measurements on test fluids mimicking fuels in laboratory settings [2]. The need for improved flow metrology in fuel lines is critical for sustainability in the road and maritime transport sector. The Safest project sought to compare commercial sensors for inline density and viscosity measuring. Rheonics sensors were found to give reliably accurate viscosity and density measurements [3].
Analysis of sensor results
Three universities contributed findings, each from a singular brand, for in-line density and viscosity measurement devices. Their experimental setups and methods vary greatly and can be found in full in the EMPIR EURAMET Safest project deliverables (D7) [3].
Conclusions from commercial sensor outcomes are compared in the report on a superficial level due to the varied protocols, however all three brands tested were individually deemed to give acceptable density measurements. The brands tested cover the main types of density meters on the market:
- Balanced Torsional Resonator (BTR)
- Vibrating tube (VT)
- Tuning fork (TF)
- Coriolis meter (CM)
Type | Manufacturer | Model | Quantities |
---|---|---|---|
BTR | Rheonics | SRV | Viscosity |
BTR | Rheonics | SRD | Density and Viscosity |
VT | Anton Paar | L-Dens 3300 | Density |
VT | Anton Paar | L-Dens 7400 | Density |
CM with VT | Emerson | CMFS050M | Density and Flow |
TF | Emerson | FVM | Density and Viscosity |
Imperial College experiments testing Rheonics sensors
Balanced torsional resonator based process density and viscosity sensors, SRD, from Rheonics are tested with a thermostatic bath containing the inline sensor chamber while flow rate of test fluid is controlled with an ISCO syringe pump. Experiments were performed at 15, 35, 55, and 75 °C, 1 – 100 bar, and 0 – 45 ml/min. Continuous flow is maintained and the system is equilibrated for 15 minutes prior to measurements. Despite this, the chamber never reaches the bath set-point temperature. Output viscosities from the SRD are considered reliable and accurate. Correction fits are applied and then the data matches reference data produced from Tait-Andrade equations (appendix of [3]). These correction fits become necessary due to observed temperature inhomogeneity in the system despite reaching an equilibrium. Deviation in temperature along the sensor length means viscosity in the chamber is not equal throughout. The same deviation exists for density however the SRD density measurements are deemed accurate and reliable without corrections herein. There can, however, be polynomial corrections applied here to match reference data more perfectly. Temperature inhomogeneity in the system can also cause deviations in density measurements when opposing ends of the sensor are not in thermal equilibrium, a longer probe could be used to ensure the internal resonator is fully immersed in a uniform temperature environment.
Rheonics process viscometer SRV is also evaluated and found to give acceptable measurements for viscosity and temperature inline.
Chemnitz University of Technology experiments testing Anton Paar sensors
Testing of vibrating tube density meters was performed with Anton Paar L-Dens 3300 and 7400 at Chemnitz University of Technology at 15, 25, and 35 °C, 1 – 10 bar, and 0 – 15 ml/min. These were also completed at small lab scale. At pressures below 2 bar, the measurement became impossible as the oscillation of the vibrating tube became unstable at low flow rates. Low flow rates, and static measurements, were used despite device specifications due to limited sample volumes. Device specifications stated these low flowrates would lead to sample heating within the tubes and this effect was observed (+3 °C). Nevertheless, both sensors were deemed to provide accurate density measurements with L-Dens 7400 slightly outperforming L-Dens 3300 but the experimentalists note the need to actually maintain dynamic process conditions for optimal accuracy.
Istituto Nazionale di Ricerca Metrologica (INRIM) experiments testing Emerson sensors
Two density and viscosity sensors from Emerson (Micro Motion ELITE CMFS050M and Micro Motion Fork Viscosity/Density Meters (FVM)) were tested at larger scales than the Rheonics and Anton Paar sensors in the above sections. Specifically, Emerson devices were tested at 20 – 40 °C, 2 – 8 bar, and 5 – 50 L/min. Different fluids were tested in different set-ups, which limits comparability.
INRIM experimental setup for water flow tests (image to the left) and for oil flow tests (image to the right) [3]
Ultimately, the verdict on these devices was left to the reader but corrections to account for pressure and temperature were critical in data accuracy.
Conclusion
All types of on-market sensors tested can be used to get density measurements but are subject to requiring correction factors when used outside manufacturer limits. Operation outside of limits, or with inhomogeneous flows, is not recommended, but the results of this report show that commercially available sensors continue to provide reasonably accurate data despite system imperfections. Rheonics and Anton Paar sensors were tested at low flow rates in low volumes while the Emerson sensors were studied at flow rates and volumes a few orders of magnitude higher. Better comparability between sensor performance would be possible if all three were tested on a broader range of flow and system volumes. However, for the varied scales investigated in the project, these studies prove there are on-market sensors available for fuel metrology at all scales from car to ship.
Rheonics review and recommendations
Achieving thermal equilibrium with the variety of sensors tested is a critical aspect of setting up fluid sensors. For Rheonics sensors specifically, the following system details can be considered:
- While low flowrates were used for the Rheonics sensors herein, the Rheonics SRV and SRD are also capable of measuring in flow environments up to 10 m/s, which corresponds to 1300 L/min (340 gal/min) and 5000 L/min (1320 gal/min) in 2” and 4” schedule 40 steel pipes, respectively. This range makes Rheonics sensors suitable for all flowrates studied for fuel sustainability in the EMPIR EURAMET Safest project [1].
- A longer insertion probe can be used to counteract thermal imbalance along the resonator probe as seen with the SRD [5] .
- Even with imperfect conditions, Rheonics SRV and SRD are reliable and accurate in-line viscosity and density meters for a broad range of flowrates and applications.
References
[2] Safest Project Deliverables
[3] Report on the advancement of in-line measurements
[4] Sustainable advanced flow meter calibration for the transport sector
[5] Maintaining the SRD’s temperature balance for high density accuracy