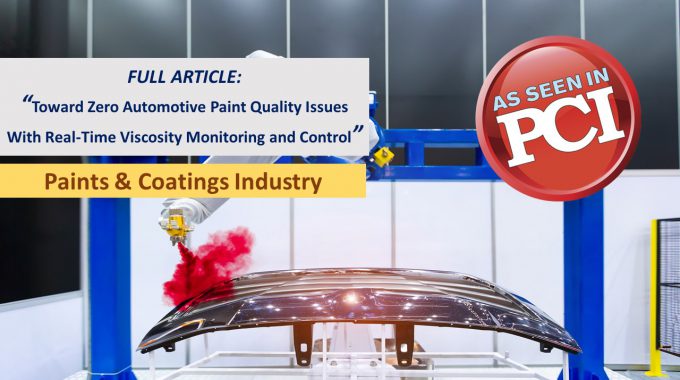
Paint & Coatings Industry Magazine: Toward Zero Automotive Paint Quality Issues With Real-Time Viscosity Monitoring and Control
Toward Zero Automotive Paint Quality Issues with Real-Time Viscosity Monitoring and Control
Through all the advancement in automotive design and manufacturing over the years, there has been one constant – vehicle aesthetics is a critical factor in consumers’ purchasing decisions. Finish consistency, quality and variety play the foremost role during a purchase. Automotive coating and finishing processes use advanced technologies to produce durable surfaces, high-quality finishes, while maximizing efficiency and meeting environmental regulations. Paint and coating quantity and quality have an obvious impact on manufacturing, sales and maintenance costs. Quality issues can quickly lead to customer dissatisfaction, expensive recalls and liability issues. 1 However, ensuring correct paint and coating quality is easy and as simple as a single button click.
Correct paint viscosity is the key to good finish quality. Performance parameters are all linked directly to the viscosity of the liquid coating at the point of application. These include coating film build, paint transfer efficiency, coating thickness and deposition, color match, finished surface qualities and chemical resistance. Viscosity is the main factor influencing the thickness and adherence of the coating. Proper viscosity control assures the quality and lifetime of the coat, helping meet the highest demands on the quality and productivity of the painting process.
In modern automotive coating processes, anti-chip coating, primer surfacer, basecoat and clearcoat are typically applied by spraying, thereby requiring the use of atomizers. The quality of atomization influences the quality of the sprayed coating. Spray application requires a viscosity as low as possible to optimize atomization. However, if viscosity is too low, film sagging will result on vertical surfaces, leading to unevenness in coating. This requires finishes with complex rheological properties. They must have low viscosity during spraying, and much higher viscosity when the material lands on the surface to be coated. In addition, paint viscosity depends on temperature, so that maintaining finish quality requires compensating the viscosity for the ambient process temperature.
Traditionally, viscosity in spray-painting operations is done using an efflux cup. The operator fills the cup with paint and measures the time necessary for the cup to empty. The longer the time, the higher the viscosity. This is usually done at intervals of 15 minutes or more, so that deviations in paint viscosity can only be detected after a considerable amount of paint has been sprayed. Also, temperature control of cup measurements is difficult if not impossible, leading to possibly large discrepancies between measured values and actual viscosity at the point of application.
In contrast, monitoring a coating’s viscosity inline results in higher coating quality, increased yields, significant savings in the use of coatings and solvents, and minimize the downtime of the coating process, compared to traditional off-line measurements with the efflux cup.
Variation in temperature leads to viscosity changes in the paint materials, resulting in structural differences or sagging. In most paint systems there is a tendency of sedimentation of the contained binder and pigment components. Inhomogeneous paint material inevitably leads to an inadequate painting result. Settled paint components may lead to blockages and to the gradual blocking of lines. Flaked paint components result in soiling of the paint film. Table 1 shows some of the typical car paint and coating defects, and their causes.
Coating consistency across painting lines in the factory can be achieved even under varying temperatures and evaporation conditions through automation of the dosing system with a controller using continuous, real-time viscosity measurements.
Paint and Coating Process Challenges
Automotive companies and coaters recognize the need to monitor viscosity, but making that measurement outside the laboratory has challenged process engineers and quality departments over the years. Existing laboratory rotational viscometers, rheometers and temperature monitoring systems are of little value in process environments. Viscosity is directly affected by temperature, shear rate, flow conditions, pressure and other variables that are very different for laboratory samples than what they are in the actual process. Traditional instrumentation like flow cups, dip cups, rotational viscometers, cone and plate viscometers, and bubble viscometers are slow, labor intensive, time consuming and prone to inaccuracies.
Paints are typically shear-thinning, having lower viscosity at higher shear rates. This is beneficial for paint performance, since it is important that the paint is applied as a uniform coat and that it stays in place once applied. But conventional viscometers do not reach the high shear rates found in the spray process, so can only indirectly give information about the performance of the paint at the point of application. Temperature is also a crucial variable in determining viscosity, but cup measurements have neither temperature measurement nor control, so cannot be directly compared with actual spraying temperature. This can lead to variations in coating quality as the process temperature varies.
Accurate and Responsive In-Line Viscosity Measurement
Automated in-line viscosity measurement enables continuous monitoring of paint at the point of application. It enables control of the paint viscosity to assure uniform quality of the finished product. Rheonics’ SRV Viscometer 2 is a balanced torsional resonator-based 3 compact in-line process viscometer with built-in fluid temperature measurement (Figure 1). With a measurement time of one second, it detects viscosity fluctuations in the process stream in real time, allowing corrective action to be taken as soon as deviations occur. Inline viscosity management with the Rheonics SRV can help alleviate most common car coating issues like orange peel, clouding and mottling, color variations and solvent pop that can negatively impact the quality of automobile’s finish.
FIGURE 1: Rheonics inline viscometer, SRV.
The SRV’s compact form factor enables direct installation in the paint line, close to the point of application. The system remains closed; paint doesn’t need to be handled or transferred to make a viscosity measurement. Small form factor sensors, suitable for hazardous environments, make installation and maintenance convenient. There are no consumables, sampling, and no clean-up is necessary. The measurement is continuous, giving a clear viscosity signal that can be used for monitoring and controlling paint viscosity and for logging viscosity to help in diagnosing quality issues.
Rheonics resonant sensors have intrinsically high shear rates, well up onto the high shear plateau of typical paint systems. These resonant sensors measure viscosities that reflect the behavior of paints at their application shear rates, rather than giving indirect measurements that must be corrected by trial-and-error to reflect actual painting conditions.
Delivers Temperature-Compensated Viscosity Readings
Rheonics sensors have built-in temperature measurement, permitting the temperature of the paint to be monitored at the point of application. This permits adjustment of the viscosity readings to a temperature-compensated viscosity value, which is essential for estimating pigment loading from real-time measurements.
Unique benefits with the SRV for automotive paint and coating applications include:
- Works accurately with both solvent-based and water-based paints and coatings.
- Rugged, hermetically sealed sensor head. The SRV can be cleaned inline or with a solvent wetted rag, no need for disassembly or re-calibration.
- No moving parts to age or foul with paint sediment.
- Unaffected by mounting conditions – can be mounted in any part of the painting system.
- Insensitive to particulate matter; no problem of fouling or any narrow gaps in the sensor.
- All wetted parts are 316L stainless steel – no corrosion problems with commercial paints, additives or solvents.
- Certified under ATEX and IECEx as
intrinsically safe – can be used in all
solvent-based operations. - Wide operational range and simple integration – Sensor electronics and communication options make it extremely easy to integrate and run in industrial PLC and control systems.
- Powerful software – Rheonics PaintTrack software is convenient and intuitive, and is powered by a proprietary, advanced, fifth-generation AI system for simple click lock and run. It supports multiple HMIs for operator, production supervisor, quality manager and management view. Designed for automated instrument control and data acquisition in factory environment (Figure 2).
FIGURE 2: Rheonics inline viscometer and PaintTrack system showing the inline integration of viscometer in the automotive coating process.
Complete System Overview and Predictive Control
Rheonics resonant sensors, together with Rheonics PaintTrack control system and software, make possible on-line control of temperature-compensated viscosity of primers and coats in multiple painting lines. Coating consistency across painting lines in the factory can be achieved even under varying temperatures and evaporation conditions through automation of the dosing system with a controller using continuous, real-time viscosity measurements.
Key benefits of the PaintTrack control system and software include:
- Reduce and eliminate setup times and scrap by loading pre-run jobs for repeat orders.
- Improve painting quality and reduce costs: Achieve color consistency, reduce coating errors by ensuring correct paint properties during the process.
- Complete automation for improved productivity and efficiency: Maximize paint operation speed, decrease reliance on manual machine adjustments and manual measurement techniques.
- Robust accuracy and repeatability: No maintenance, no recalibration = no attention needed.
- Temperature-compensated viscosity with proprietary Predictive Tracking Control: Solution that precisely locks color and coat quality from start to finish on every job with repeatable results.
- You can take the cup out of the equation: Coating process is set to scientific standards, 100 times greater accuracy and resolution than average efflux cups.
Conclusion
- Vibrational viscometers, such as the Rheonics SRV, come closer to matching the high shear rates in spray paint application than do rotational or cup viscometers. Therefore, measurements with the SRV come closest to predicting the behavior of paint under actual spraying conditions.
- Inline viscosity control with the SRV and Rheonics PaintTrack enables continuous viscosity control, making necessary dilutions in real time. Coating quality is guaranteed from the beginning of a new drum to its end.
- Rheonics SRV and PaintTrack control true temperature-compensated viscosity, a key predictor of pigment content and final coating quality.
References
- https://www.autoblog.com/2020/05/04/tesla-model-y-paint-issues-fix-detail-video/
- SRV inline viscometer: https://rheonics.com/products/inline-viscometer-srv/
- SRV operating principle: https://rheonics.com/whitepapers/
Overview
Paint & Coatings industry focused magazine – PCI (https://www.pcimag.com/) publishes a feature article covering the Rheonics inline viscometer SRV and PaintTrack. The article discusses how coating consistency across painting lines in the factory can be achieved even under varying temperatures and evaporation conditions through automation of the dosing system with a controller using continuous, real-time viscosity measurements.
Find the link to the the publication.
Related Application Note
Automotive painting and coating quality control and optimization
Through all the advancement in automotive design and manufacturing over the years, there has been one constant – vehicle’s aesthetics is a critical factor in a consumer’s purchasing decision. Vehicles’ finish consistency, quality and variety play the foremost role during…