The ability to monitor and control slurry viscosity is key to investment casting. Process instrumentation must remain deposit-free to ensure reliable measurements. This self-cleaning process innovation prevents deposit formation on Rheonics inline density meter and viscometer.
Introduction
Investment casting is a manufacturing process that uses wax molds dipped in ceramic slurries to make shells for creating precision metal parts for a multitude of industries. Figure 1 shows the basic steps found in investment casting processes. The properties of the ceramic slurry dictate the surface finish of the final metal parts and are critical for layer thickness from each dip of the wax mold. Monitoring and controlling viscosity of ceramic slurries in investment casting is therefore critical to control slurry properties for quality manufacturing of components in investment casting. Commonly, manual tests such as Zahn cups and plate weight are used to monitor the slurry consistency and confirm process and quality control benchmarks. These measurements are intermittent and done off-line leading to differences in flow and temperature conditions than those found within the slurry tanks. Additional concerns in these measures arise when operator variability and distinction of end-point in a test is left to the user’s discretion. In recent years, Rheonics inline density meters and viscometers have been used for continuous monitoring of density and viscosity alongside intermittent manual tests like Zahn cups or plate weight. When used with Rheonics RPS SlurryTrack the inline density and viscosity monitoring can additionally be used for system control. The Rheonics inline viscosity meter can also be used to monitor without density measurements.
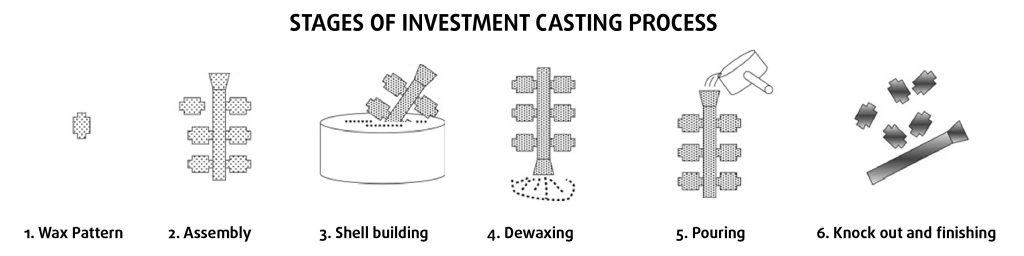
Viscosity and density in casting slurries
Slurry viscosity plays a key role in investment casting with viscosity known to affect:
- coating thickness
- adhesion to fine details,
- mixing efficiency,
- defect formation,
- surface finish,
- shell strength,
- permeability,
- bending strength,
- thermal conductivity, and more.
The importance of slurry viscosity is further explored in https://rheonics.com/solutions-item/monitoring-and-controlling-viscosity-of-ceramic-slurries-in-investment-casting/. Tighter viscosity control has been found to improve the ease and quality of shell building, and yields improved cast goods with fewer defects and less waste. Early detection of abnormal viscosity can prevent gelling of binder materials and therefore reduce the chances of slurry wastage.
Process Challenges: deposit build-up on sensors
This case study seeks to provide insights on the scenario when a Rheonics inline density meter and viscometer installed in a ceramic slurry develops a build up of ceramic shell on the measurement probe. While shell building is the overall goal of investment casting slurries, a built-up shell on sensor probes can lead to upward drifting measurements or necessitate frequent cleanings. Deposits forming on the sensor are not seen for all slurries, and therefore this solution is only needed when surface deposits are affecting measurements. Deposits on the sensor probe can be either tenacious or transient. Tenacious deposits means the build up increases over time and cannot be removed from the sensor with simple measures: flow changes, rinsing, or temperature. With transient build up, those simple measures can breakup and remove the built-up deposits. Both these types of buildup can have a negative effect on the reliability of viscosity measurements and have been seen to cause disruption to the continuous process control benefits that Rheonics in-line density and viscometers provide for slurry quality management.
Rheonics application innovation
In these tricky slurries, process measurement tools may struggle to remain free of deposits. Rheonics has taken inspiration from a dog shaking to dry off, to develop a self-cleaning probe that remains free of deposits. This CleanWaveTM technology is incorporated into a Rheonics inline process density meter and viscometer to produce a sensor that resists shell forming: SlurrySense!
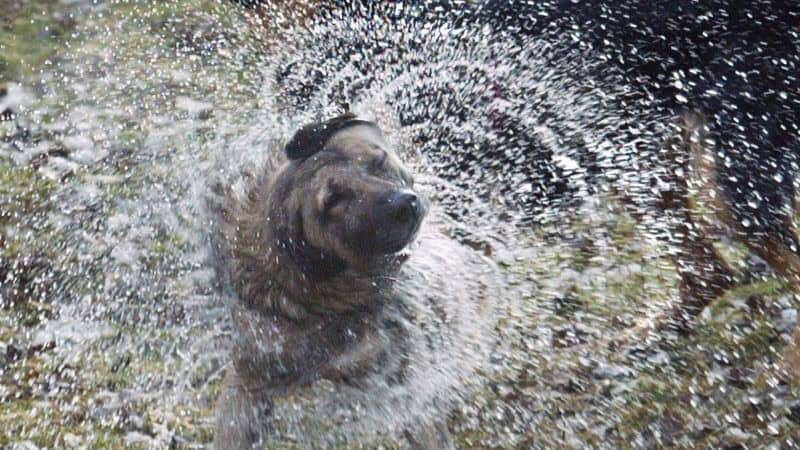
Rheonics SlurrySense with CleanWaveTM allows for continuous viscosity and density monitoring of process solution slurries without concern for deposits! With continuous monitoring, one can adapt diluent addition or detect gelling in real-time before scheduled operator Zahn or plate weight tests. Being able to detect viscosity and density changes in real-time opens the shell room to process control and automation solutions.
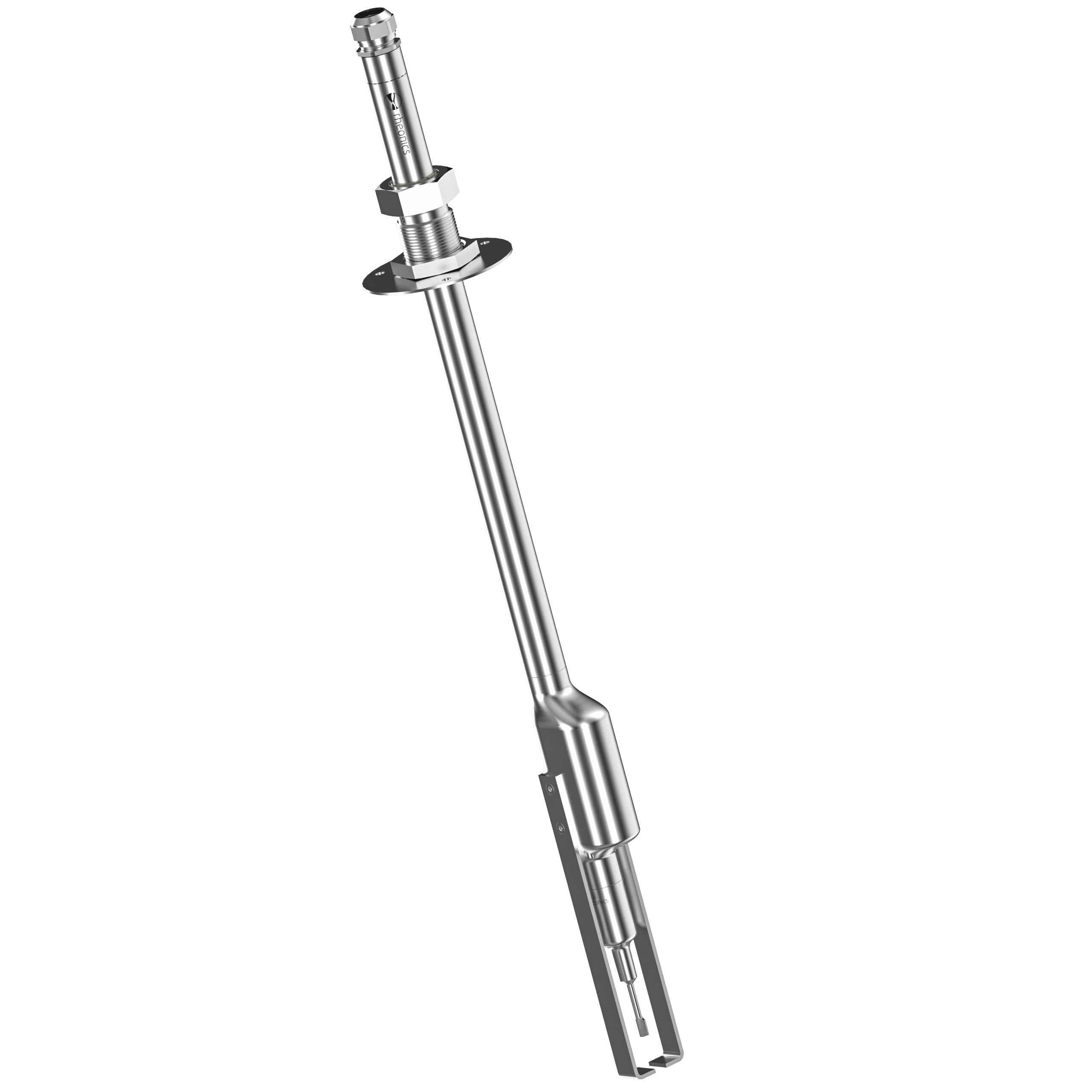
SlurrySense is located directly in the slurry tank, providing continuous readings of slurry viscosity and density that can be integrated with Rheonics RPS SlurryTrack software to control viscosity with a single click to lock onto a viscosity setpoint. SlurrySense provides all the benefits of a Rheonics SRD and solves the cleaning challenge of deposit formation!
- Robust accuracy
- Long-lasting repeatability
- No maintenance needed
- No recalibration
- No cleaning required
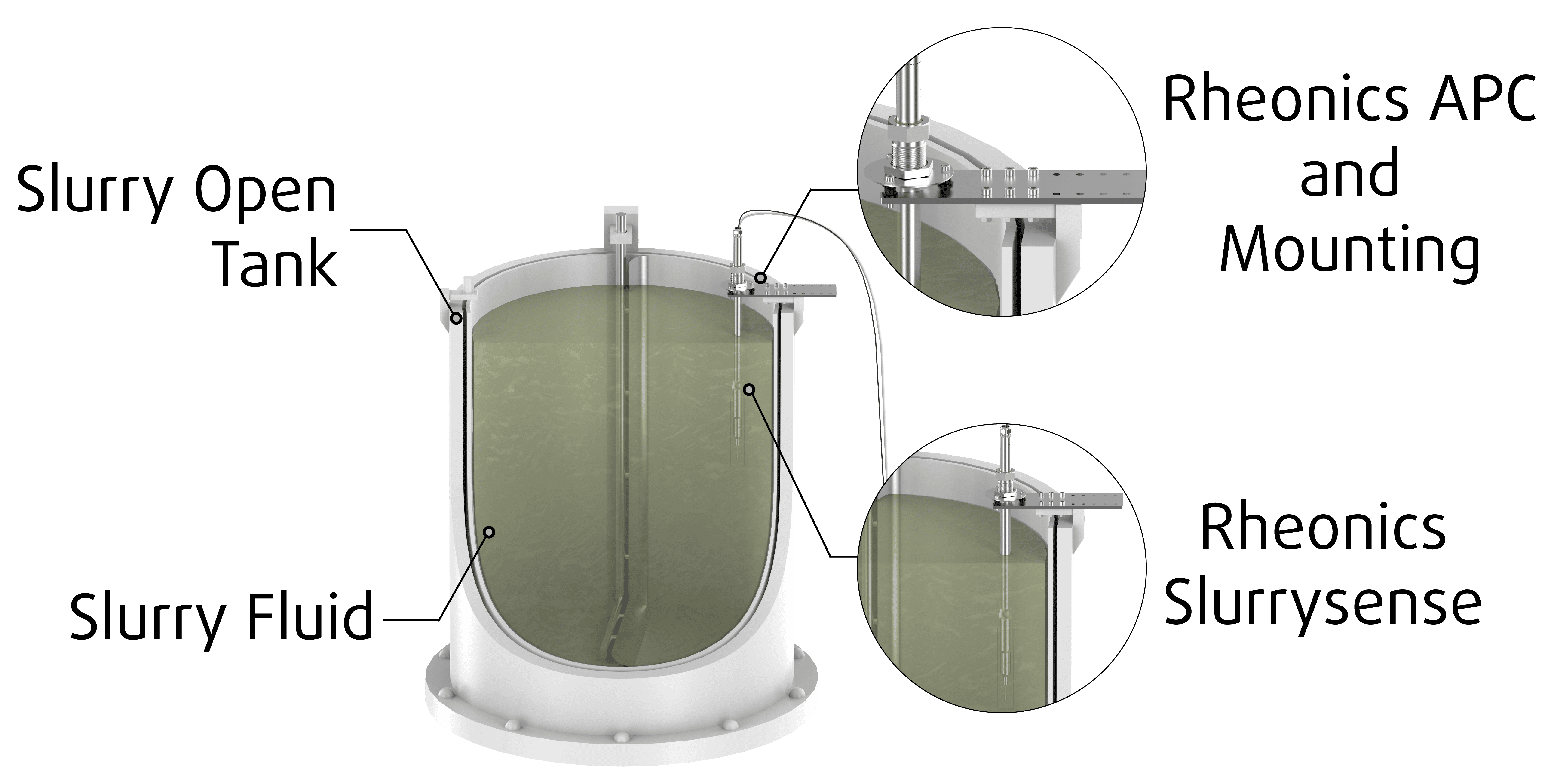