Introduction
Investment castings are one of the most popular production methods for metal parts today. Investment casting process, also termed as a lost wax process, is relatively simple, which enables rapid production rates while ensuring consistent dimensional accuracy. Parts that are typically made by investment casting include those with complex geometry such as turbine blades or firearm components. High temperature applications are also common, which includes parts for the oil & gas drilling, automotive, aircraft, and military industries. Transmission forks are now manufactured using investment casting instead of forging and complex machining. It offers weight reduction, less machining, improved delivery time and lower inventory carrying costs.
The global investment casting market size was estimated at USD 14.35 billion in 2018 and is expected to grow at a CAGR of 4.6% till 2025 as per a market research report by Grand View Research. There are numerous applications where investment castings are predominantly used – aerospace, power generation, firearm, automotive, military, commercial, food service, oil and gas, and energy industries use these components the most. Increasing penetration of investment castings in manufacturing of advanced components like compressor, engine parts, gearbox components, and others is likely to boost the market demand even further.
Despite huge application areas and moderate demand from the end-use sectors, this industry is facing challenges related to efficiency, lead time, and capacity utilization. Industry leaders are moving towards adoption of more advanced technologies such as automation, industrial internet of things (IIoT) and simulation techniques. Automation in the investment casting processes is helping manufacturers reduce lead times, enhance capacity utilisation and optimise efficiency.
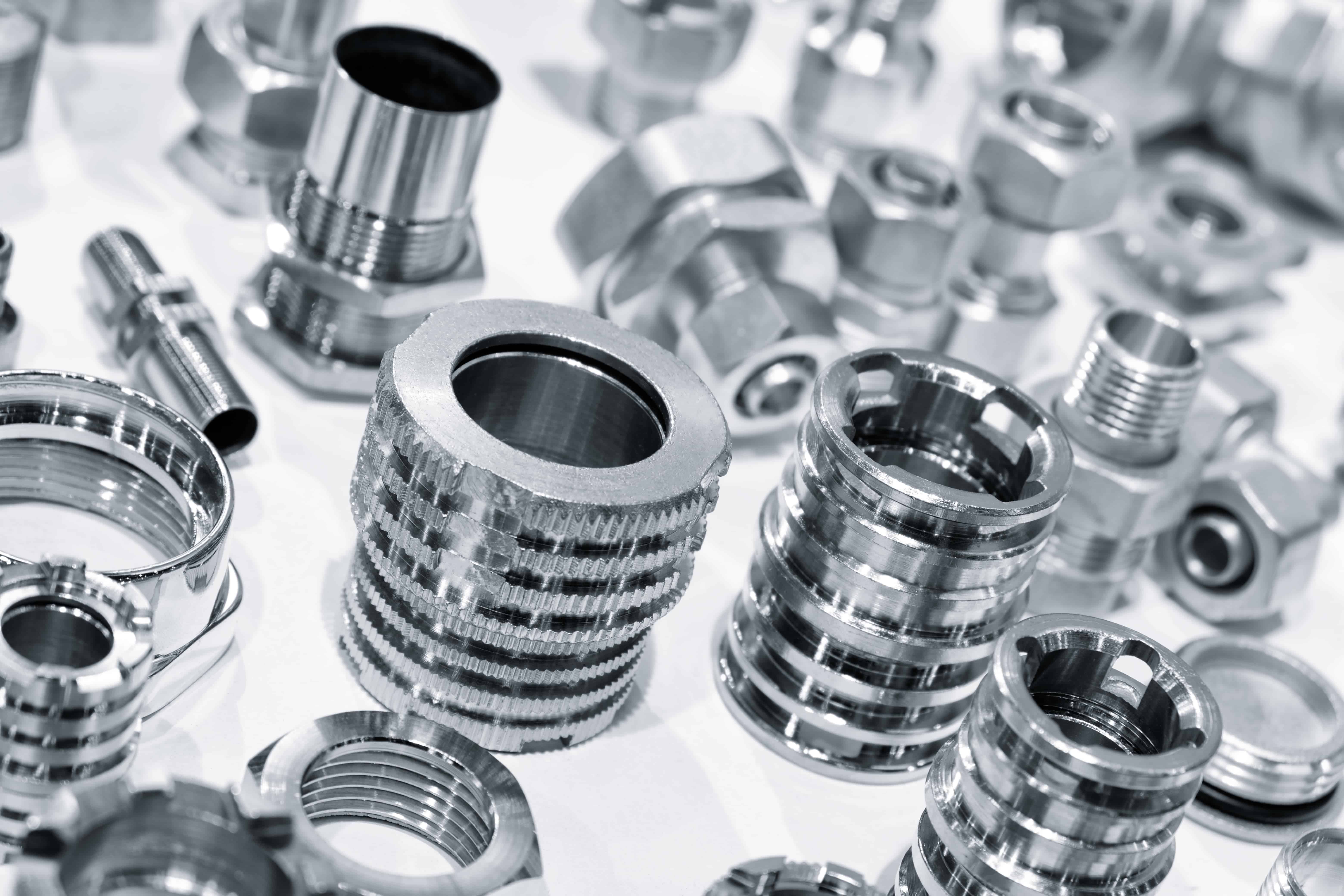
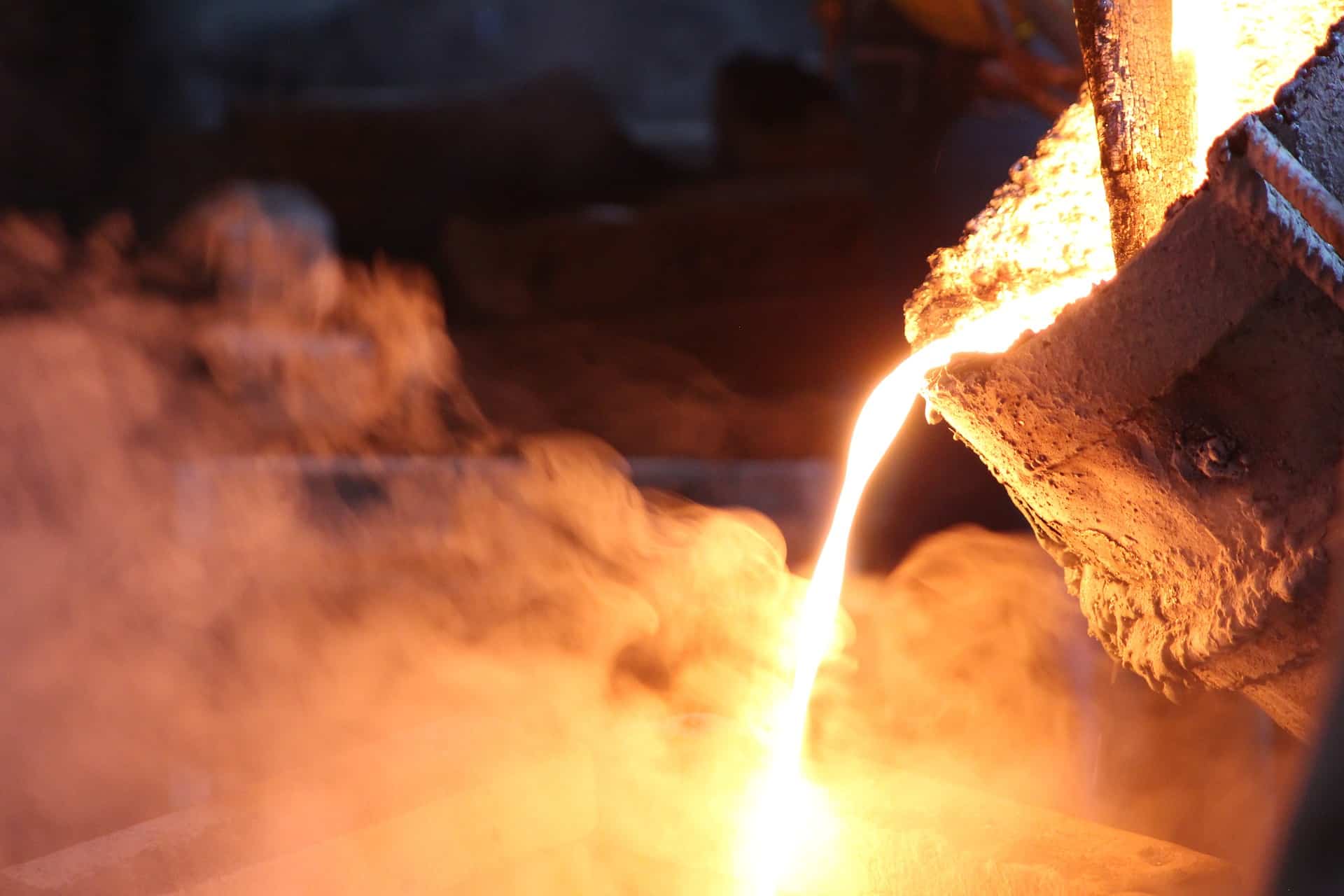
Application
Investment casting is a manufacturing process in which a wax pattern is coated with a refractory ceramic material. Once the ceramic material is hardened, its internal geometry takes the shape of the casting. The wax is melted out and molten metal is poured into the cavity where the wax pattern was. The metal solidifies within the ceramic mold and then the metal casing is broken out.
The coating of refractory ceramic material (ceramic slurry) can be done in single or multiple stages, the latter often including a first encapsulating stage with high precision control of coating thickness and density. The substrate parts may be permanent or removable after coating and solidification to leave the coating as a free-standing part (investment casting). Complex substrate surface geometries and internal re-entrant surfaces can be controllably coated. Ceramic casting presents special challenges of achieving reliable slurry characteristics and measuring them reliably, including viscosity measurement for its own sake and as an indicator of other characteristics. After coating, the ceramic parts are fired to attain ultimate strength, dimensions and morphology as finished products. Yields of usable products are dependent on reliable coating.
The quality of the ceramic shell depends on the slurry composition and the process by which it is built. Typical ingredients in an investment casting slurry include: colloidal silica, water and/or polymers, wetting agents, anti-foaming agents, and refractory flours. All of these ingredients play an important role in the behaviour of the slurry and the resulting properties of the shell. The raw materials (refractory, binder, wetting agent, and antifoam) used to make slurry play a major role in determining the overall final ceramic shell characteristics. Suitable choice of the ceramic materials can lead to smooth surface finish, and high accuracy of the metal castings.
Slurry viscosity
A good slurry composition alone cannot guarantee production of smooth and defect free shell if the slurry is prepared in an inadequate manner. Control methodologies for slurry vary considerably across foundries, depending on the associated product lines and required specifications. The goal of slurry preparation is to produce stable slurries that must meet a given set of slurry parameters. To be considered stable, the slurries need to be thoroughly mixed and their viscosity values must be stable.
Slurry control is one of the most important operations of the investment casting process, with viscosity of the slurry being a critical parameter. The viscosity of the slurry is a measurement of the flow characteristics of the slurry, and is one of the most widely used control tests in industry. Key points on how slurry viscosity is critical in investment casting process are the following:
- Slurry viscosity depends on the composition (filler to binder ratio) as well as the ageing time and is an important indicator of the slurry stability. It is initially high when slurries are mixed; however, as mixing continues and the refractory material is wetted and air is released, the viscosity decreases and asymptotically approaches a stable value.
- Surface finish will be an important characteristic of the casting, therefore the surface quality of ceramic shell for investment casting of metal alloys must be adequate. The surface finish is highly dependent on the viscosity of the primary slurry and the overall stability of the slurry mixture.
- Viscosity is an effective indicator of the particle size distribution of the slurry. Particle size distribution changes of ceramic flour (powder) can affect slurry properties including slurry density, rheology, and coating thickness. Shell properties that can be affected are permeability, thermal characteristics, thickness, edge coverage, and strength. For critical applications like Titanium and DS/SC casting, control of particle size can mean the difference between success and failure. Continuous viscosity monitoring and making required adjustments to the slurry is essential in order to achieve right properties of the ceramic shell and eventually the investment castings.
- Continuous process control is essential for achieving target bending strength of the investment shell. Increase in slurry viscosity increases the bending strength of the investment shell, but decreases beyond a limiting viscosity. It can be attributed to larger content of refractory flour for a given binder content.
- Selection of any refractory filler material for shell making is dependent on a wide variety of factors which can affect the properties of investment slurry, shell and casting and also the economy of the process. In general zircon flour is used as a primary slurry material in the ceramic shell investment casting process, but it is very costly. Therefore, continuous monitoring and control of viscosity can keep costs of the processes low with significant material savings, reduced solvent use and optimal energy usage during the mixing process.
- An appropriate slurry viscosity should be maintained to avoid shell problems such as cracking. The primary coat must withstand pressure from expanding wax as it is heated during the wax removal stage as well as survive the rigors of handling during the shell building process
Slurry viscosity is an important design parameter and it is very important to ensure that it stays within the predetermined range throughout the coating step to provide a uniform coating thickness and desirable shell properties. When the viscosity fluctuates out of specification, the coating of ceramic slurry will be uneven which eventually will lead to poor quality and affects the properties of the investment shell. Shell properties that can be affected with the slurry viscosity are surface roughness, thermal conductivity, chemical reactivity, permeability and shell strength. Highly viscous coating solutions result in tackiness and cause difficulty in transfer onto the substrate, whereas low viscosity makes it more mobile and harder to control and also results in increased solvent usage. The viscosity increases when it is not being worked and decreases when there is a constant applied force. The strong correlation between temperature and slurry viscosity suggest that fluctuations in temperature can have drastic impact on the viscosity, and thus the coating process in general.
In order to have a uniform coating and so as not to waste materials and optimise energy usage, it is therefore highly desirable that the slurry viscosity be regulated automatically to a substantially constant value. Real-time, in-line viscosity monitoring and control in the coating process is essential to improve performance and reduce costs in almost every coating process of investment casting. Process operators realise the need of a viscometer that monitors viscosity and temperature, and could use temperature-compensated viscosity as the key process variable to ensure consistency and reduce reject rates of the final investment castings.
pH of slurry and its effect on risk of gelling
In the coating process, slurry is maintained in process at a consistent viscosity with the gel reaction occurring. This is achieved by adding excess water such that the silica content is reduced. In effect, dilution means that the silica particles are further apart, and therefore interact less frequently, and a degree of stability is maintained. However, an ever-decreasing content of silica, and increasing binder viscosity is never a good thing and eventually the slurry either loses its binding power because the silica is so reduced, or the poor flow characteristic leads to poor shell build resulting in casting defects.
Lowering the pH reduces the repulsive forces that keep colloidal particles apart and may cause the particles to collide and gel, therefore pH of slurries is critical and a key determinant for the quality of the slurry. In general, as the pH of a slurry approaches its minimum or maximum recommended limits, the slurry is at a greater risk of gelling. Refractory materials, waxes, and water may all have components that reduce the pH of slurries. Microbe growth also reduces the pH of slurries. Microbes may be controlled with additions of biocides, while the choice of waxes and refractory materials may not be as easily controlled. The pH of slurries may be increased through additions of diluted ammonium hydroxide and triethanolamine. Therefore, continuous monitoring and control of the pH value through feedback control of the slurry can reduce the risk of gelling.
Why viscosity (and pH) monitoring & control is critical in slurry coating process of investment casting?
The broad and significant benefits with viscosity and pH management in slurry coating process of investment casting are:
- Investment shell and casting quality: Investment shells must comply with finished product specifications, and process control is critical to achieve the same. Variation in viscosity causes significant change in the coating quality. The surface finish is highly dependent on the viscosity of the primary slurry and the overall stability of the slurry mixture. In-line viscosity monitoring and control can help achieve the required coating quality.
- Reduce defects: Viscosity control can help alleviate the frequency of miscues in the coating process – sticking and picking, twinning, peeling, splitting, cracking, roughness, blistering, bridging and surface erosion and reduce poor flow characteristic which lead to poor shell build resulting in casting defects.
- Better yield: Ensuring consistency throughout the coating process significantly reduces reject rates saving cost and time and assists in continuous casting processes. Offline measurement techniques are tedious and unreliable, and involve huge delays in the production process besides incurring high personnel costs to sample and run tests.
- Correct properties: Poor coating quality can adversely affect the desirable properties of the investment shells – surface roughness, thermal conductivity, chemical reactivity, permeability and shell strength in turn affecting the quality of the investment castings. All these properties depend on the how well the coating process is controlled, hence controlling viscosity is critical.
- Efficient processes: Automation in the viscosity and pH sensing and control in investment casting processes can help manufacturers reduce lead times, enhance capacity utilisation and optimise efficiency.
- Cost: Coating with incorrect viscosity harms more than just quality. Poor viscosity management drives up usage of powder, binder and solvents, affecting the profit margins. Continuous viscosity measurements during the mixing process can ensure homogeneity, optimise energy usage and reduce use of solvent.
- Waste: Materials rejected due to poor quality can be reduced with proper viscosity management.
- Efficiency: Eliminating manual viscosity control frees operators’ time and enables them to focus on other tasks.
- Environment friendly: Lowering the use of pigment and solvent is good for the environment.
- Regulatory compliance: Global and national regulations guide the overall properties of the investment castings. Failure to adhere due to variability in production could lead to significant damages and loss of customers besides liabilities arising from defective workmanship in production process.
To ensure consistent high-quality, uniform coating, the change in viscosity through-out the process stream is monitored in real time, making measurements from a baseline rather than simply measuring absolute values, and making viscosity adjustments by adjusting solvents and compensating for temperature to keep the complete coating process within specified limits. With continuous online viscosity monitoring, the initial shell formation can be controlled more effectively, therefore significantly improving the metallurgical properties of the final product.
Process Challenges
Operators in castings market recognize the need to monitor viscosity but making that measurement outside laboratory has challenged process engineers and quality departments over the years. Existing laboratory viscometers are of little value in process environments because viscosity is directly affected by temperature, shear rate and other variables that are very different off-line from what they are in-line. Conventional methods of controlling viscosity of slurry coating have proven inadequate even in applications where wide variation in viscosity is permitted.
Traditionally, operators in investment casting industry have measured the viscosity of slurry using the Zahn flow cup. The measurement is reported as the time elapsed for the cup volume to flow through a hole in the bottom of the cup. The end point of the test must be chosen so that it is consistent from test to test. The procedure is messy and time-consuming. It is inaccurate, inconsistent and non-repeatable even with an experienced operator. In the continuous casting process, the interval sampling causes excessive delays. The viscosity of slurry can’t be adjusted in real time. Besides, the various containers containing the slurry are open; due to changes in ambient temperature, humidity and other factors, such as temperature, dry climate, solvents are likely to be volatile, so cup based viscosity measurement technique becomes ineffective.
Viscosity and other characteristics relatable to it (e.g. shear rate and weight percent of solids) vary with depth in a tank containing substantial amounts of ceramic slurry, conditions of movement of slurry (generally induced to maintain homogeneity), capture by cast parts and replenishment or adjustments. There are several approaches to measuring viscosity online through instrument probes inserted into the casting bath at various depths, but they have been prone to drift and error over the course of casting operations and some may need frequent removal, cleaning or replacement, down time and recalibration of the probes and instruments. Some probes can be cleaned in situ but are subject to malfunction due to exposure to undesirable and variable coating of transducer elements.
Rheonics' Solutions
Automated in-line viscosity measurement and control is crucial to control the coating formulation and application viscosity. Rheonics offers the following solutions, based on a balanced torsional resonator, for process control and optimisation in the coating process:
- Online Viscosity measurements: Rheonics’ SRV is a wide range, in-line viscosity measurement device with in-built fluid temperature measurement and is capable of detecting viscosity changes within any process stream in real time.
- Online Viscosity and Density measurements: Rheonics’ SRD is an in-line simultaneous density and viscosity measurement instrument with in-built fluid temperature measurement. If density measurement is important for your operations, SRD is the best sensor to cater to your needs, with operational capabilities similar to the SRV along with accurate density measurements.
The sensor are hermetically encapsulated and hence performance is unaffected by turbulence and fluid non-homogeneity. Automated online viscosity measurement through SRV or an SRD eliminates the variations in sample taking and lab techniques. The sensor is installed either in the coating bucket or the line through which the coating is pumped to the applicator, continuously measuring the formulated system viscosity (and density in case of SRD). Coating consistency is achieved through automation of the dosing system through a process controller based on real-time viscosity, and temperature measurements. Using an SRV/SRD in a coating process line, coat transfer efficiency is improved improving productivity, profit margins and environmental/regulatory goals. The sensors have a compact form factor for simple OEM and retrofit installation. They require no maintenance or re-configurations. The sensors offer accurate, repeatable results no matter how or where they are mounted, without any need for special chambers, rubber seals or mechanical protection. Using no consumables, SRV and SRD are extremely easy to operate with zero maintenance.
Rheonics offers an integrated standalone viscosity and pH monitoring and control system. The Rheonics Slurry Monitoring and Control system uses in-line viscometers with in-line pH probes to monitor slurry viscosity and pH in real-time. Solvent and additive valves are operated to add the correct dose to ensure absolute control of the slurry characteristics throughout the mixing and coating process.
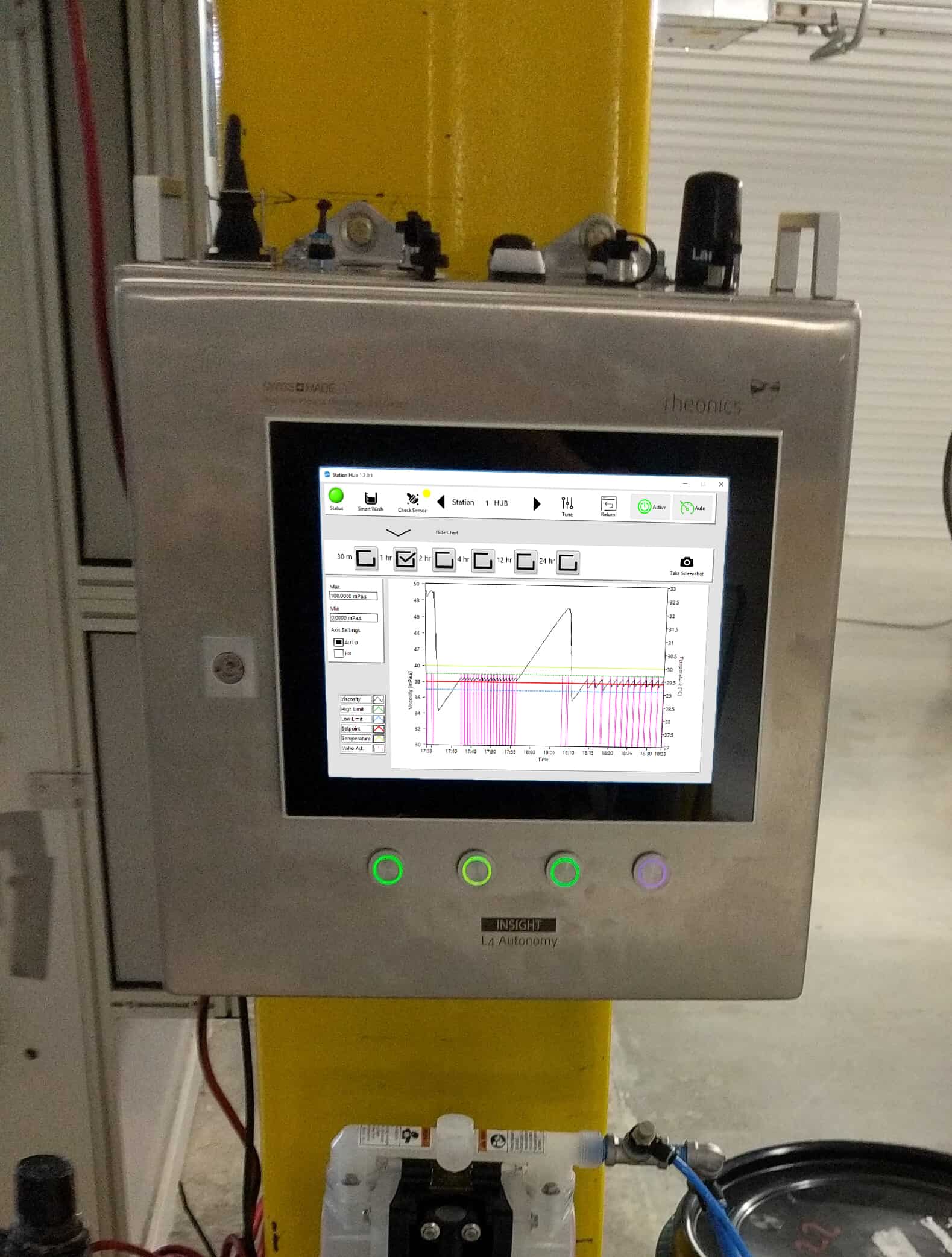
Rheonics' Advantage
Compact form factor, no moving parts and require no maintenance
Rheonics’ SRV and SRD have a very small form factor for simple OEM and retrofit installation. They enable easy integration in any process stream. They are easy to clean and require no maintenance or re-configurations. Their small footprint enables simple in-line installation, avoiding any additional space or adapter requirement on the coater.
High stability and insensitive to mounting conditions: Any configuration possible
Rheonics SRV and SRD use unique patented co-axial resonator, in which two ends of the sensors twist in opposite directions, cancelling out reaction torques on their mounting and hence making them completely insensitive to mounting conditions and flow rates. These sensors can easily cope up with regular relocation. Sensor element sits directly in the fluid, with no special housing or protective cage required.
Instant accurate readouts on conditions – Complete system overview and predictive control
Rheonics’ software is powerful, intuitive and convenient to use. Real-time viscosity can be monitored on a computer. Multiple sensors spread across the factory floor are managed from a single dashboard. No effect of pressure pulsation from pumping on sensor operation or measurement accuracy. In addition, the sensor is insensitive to any vibrations or electrical noise from external machinery.
Easy installation and no reconfigurations/recalibrations needed
Replace sensors without replacing or re-programming electronics with lowest facility modification and implementation cost.
Drop-in replacements for both sensor and electronics without any firmware updates or calibration coefficient changes.
Easy mounting. Screws into ¾” NPT threaded in-line fittings, or Flanged connections.
No chambers, O-ring seals or gaskets.
Easily removed for cleaning or inspection.
SRV available with flange, DIN 11851 hygienic and tri-clamp connection for easy mounting and dis-mounting.
Low power consumption
24V DC power supply with less than 0.1 A current draw during normal operation (less than 3W)
Fast response time and temperature compensated viscosity
Ultra-fast and robust electronics, combined with comprehensive computational models, make Rheonics devices one of the fastest and most accurate in the industry. SRV and SRD give real-time, accurate viscosity (and density for SRD) measurements every second and are not affected by flow rate variations!
Wide operational capabilities
Rheonics’ instruments are built to make measurements in the most challenging conditions. SRV has the widest operational range in the market for inline process viscometer:
- Pressure range up to 5000 psi and higher
- Temperature range from -40 up to 300°C
- Viscosity range: 0.5 cP up to 50,000+ cP
SRD: Single instrument, triple function – Viscosity, Temperature and Density
Rheonics’ SRD is a unique product that replaces three different instruments for viscosity, density and temperature measurements. It eliminates the difficulty of co-locating three different instruments and delivers extremely accurate and repeatable measurements in harshest of conditions.
Achieve the right coat quality, cut down costs and enhance productivity
Integrate an SRV/SRD in the process line and ensure uniformity and consistency throughout the coating process. Achieve constant slurry quality without worrying about pH variations. SRV (and SRD) constantly monitors and controls viscosity (and density in case of SRD) and prevents overuse of expensive pigments and solvents. Reliable and automatic control ensures that processes run faster and saves operators’ time. Optimise the coating process with an SRV and experience lesser reject rates, lesser wastes, fewer customer complaints, fewer press shut downs and material cost savings. And at the end of it all, it contributes to a better bottom line and a better environment!
Clean in place (CIP)
SRV (and SRD) monitors the cleanup of the ink lines by monitoring the viscosity (and density) of the solvent during the cleaning phase. Any small residue is detected by the sensor, enabling the operator to decide when the line is clean for purpose. Alternatively, SRV provides information to the automated cleaning system to ensure full and repeatable cleaning between runs. The sensor probes are unaffected by any exposure and produce repeatable results even in the harshest of conditions.
Superior sensor design and technology
Sophisticated, patented 3rd generation electronics drive these sensors and evaluate their response. SRV and SRD are available with industry standard process connections like ¾” NPT and 1” Tri-clamp allowing operators to replace an existing temperature sensor in their process line with SRV/SRD giving highly valuable and actionable process fluid information like viscosity besides an accurate measurement of temperature using an in-build Pt1000 (DIN EN 60751 Class AA, A, B available).
Environment friendly
Reduce the use of VOC (volatile organic compounds) in your process reducing the energy required to recover it or disposal costs. Manufacture smart while saving costs, ensuring high quality and protecting the environment.
Electronics built to fit your needs
Available in both an explosion-proof transmitter housing and a small-form factor DIN rail mount, the sensor electronics enables easy integration into process pipelines and inside equipment cabinets of machines.
Easy to integrate
Multiple Analog and digital communication methods implemented in the sensor electronics makes connecting to industrial PLC and control systems straightforward and simple.
ATEX & IECEx Compliance
Rheonics offers intrinsically safe sensors certified by ATEX and IECEx for use in hazardous environments. These sensors comply with the essential health and safety requirements relating to the design and construction of equipment and protective systems intended for use in potentially explosive atmospheres.
The intrinsically safe and explosion proof certifications held by Rheonics also allows for customization of an existing sensor, allowing our customers to avoid the time and costs associated with identifying and testing an alternative. Custom sensors can be provided for applications that require one unit up to thousands of units; with lead-times of weeks versus months.
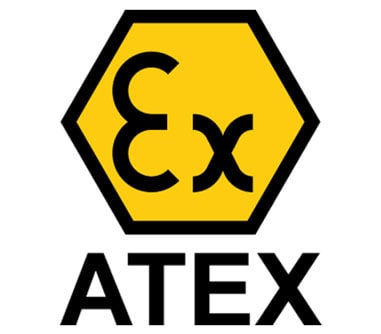
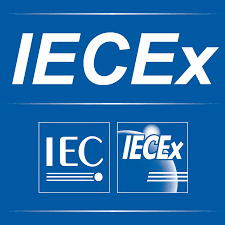
Implementation
Directly install the sensor to your process stream to do real time viscosity and density measurements. No by-pass line is required: the sensor can be immersed in-line. Flow rate and vibrations do not affect the measurement stability and accuracy. Optimize slurry mixing and coating performance during shell building by providing repeated, consecutive, and consistent tests on the fluid.
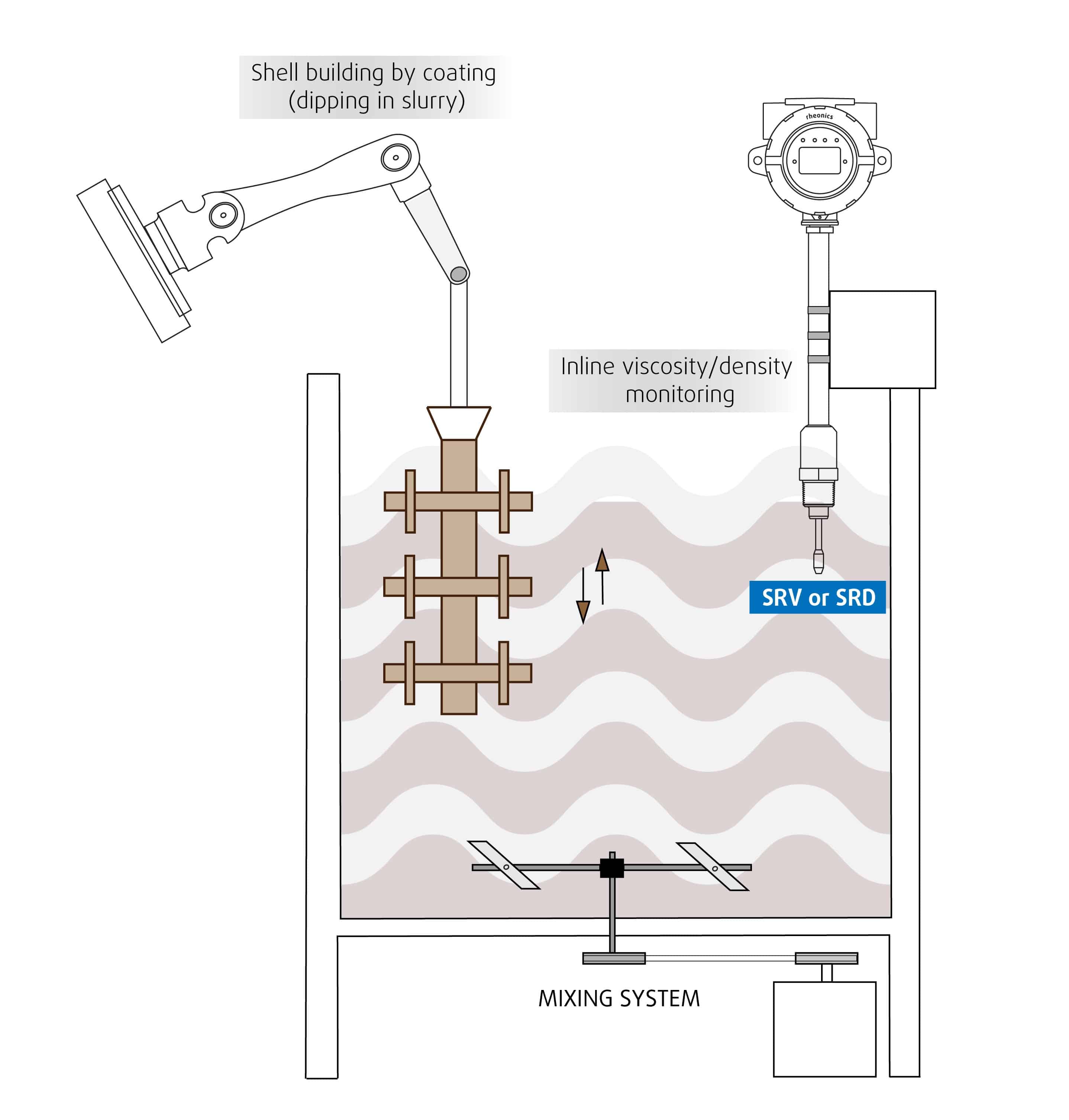
SRV/SRD in ceramic slurry mixing tanks during mixing and coating for shell building – Schematic with possible mount location of the sensor
Application Updates - From Rheonics Blog
Rheonics Technical Session & Booth at WCIC Expo, Investment Casting Institute – August 2022 at Anaheim, California, USA
Topic Viscosity control for consistent casting shell building Date & Time August 22, 2022 @ 13:30 - 14:00, Anaheim, California,…
Rheonics Technical Webinar – ICI (Investment Casting Institute) – Foundry 4.0 – High Quality, Defects-Free Effective Shell Building
Topic Foundry 4.0 – High quality, defects-free, effective shell building needs real-time viscosity monitoring and control of ceramic slurries Date…
INCAST features Rheonics – “Foundry 4.0 – Smart Precision Casting Needs Viscosity Control of Ceramic Slurries”
Investment casting industry focused magazine - INCAST Mag (https://www.investmentcasting.org/current-issue.html) publishes a feature article covering the Rheonics inline viscometer SRV and…
Smart foundries – drivers for casters’ embrace of Industry 4.0 and digitalization
Many parameters can alter the ceramic slurry quality in investment casting across batches - Temperature and humidity fluctuations, mixing equipment…
Rheonics is now member of Investment Casting Institute
We are pleased to inform you that we are now members of the Investment Casting Institute! As members of the ICI,…
Rheonics Instrument Selection
Rheonics designs, manufactures and markets innovative fluid sensing and monitoring systems. Precision built in Switzerland, Rheonics’ in-line viscometers and density meters have the sensitivity demanded by the application and the reliability needed to survive in a harsh operating environment. Stable results – even under adverse flow conditions. No effect of pressure drop or flow rate. It is equally well suited to quality control measurements in the laboratory. No need to change any component or parameter to measure across full range.
Suggested product(s) for the Application
- Wide viscosity range – monitor the complete process
- Repeatable measurements in both Newtonian and non-Newtonian fluids, single phase and multi-phase fluids
- Hermetically sealed, all stainless steel 316L wetted parts
- Built in fluid temperature measurement
- Compact form-factor for simple installation in existing process lines
- Easy to clean, no maintenance or re-configurations needed
- Single instrument for process density, viscosity and temperature measurement
- Repeatable measurements in both newtonian and non-newtonian fluids, single phase and multi-phase fluids
- All metal (316L Stainless Steel) construction
- Built in fluid temperature measurement
- Compact form-factor for simple installation in existing pipes
- Easy to clean, no maintenance or re-configurations needed