The mining industry has always been known for its complexity and hard environments. From ore extraction to final product recovery, customers must confront different processes that usually involve abrasive slurries, alternating solid concentrations, and chemically aggressive environments. These conditions make process stability a constant challenge, and process measurements a necessary tool. Real-time viscosity and density measurements enable monitoring and control of slurry behavior for optimized product recovery processes.
Table of Content
- Introduction
- Rheonics Type-SR Inline Viscosity and Density Sensors Overview
- Relevant parameters
- Viscosity & Density as Process Indicator
- Key Mining Applications
- Process Conditions and Best Practices
- References
Introduction
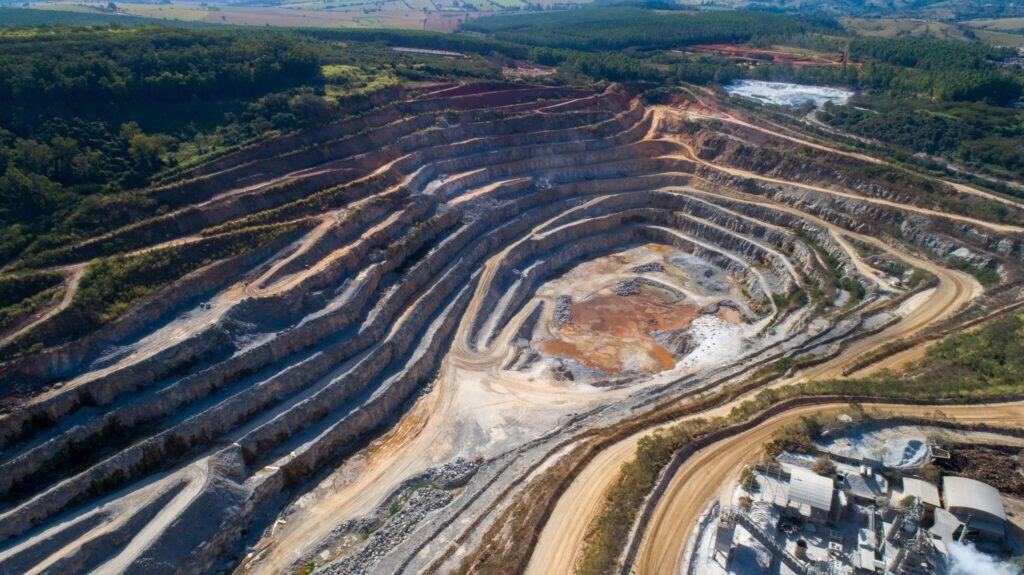
The mining industry has always been known for its complexity and hard environments. From ore extraction to final product recovery, customers must confront different processes that usually involve abrasive slurries, alternating solid concentrations, and chemically aggressive environments. These conditions make process stability a constant challenge, and process measurements a necessary tool.
This industry is always on the lookout for controlling concentration, texture, composition, and flowability properties of their processes. These parameters can affect their equipment performance, metal recovery efficiency, smart energy usage, and safety conditions. These desired conditions are often indirectly observed or controlled using density and viscosity as key indicators.
Usually, traditional lab-based sampling is used, but these provide occasional insights that are not able to capture real-time changes. On the other hand, inline measurements give continuous and real-time visibility of the process, allowing to have a faster response.
Rheonics Type-SR Inline Viscosity and Density Sensors Overview
Rheonics Type-SR sensors (SRV and SRD) measure viscosity, density, and temperature in line for process control and monitoring. SRV measures viscosity, while SRD measures density and viscosity.
These sensors are factory calibrated and do not need recalibration over their operational lifetime. However, clients may require calibration or verification for instruments used in their industry as part of their Quality Control. Optional re-adjustments or offset corrections can be performed if needed to match specific references. For more details, see Calibration of inline process viscometer SRV in field and factory.
Rheonics sensors technology is based on a balanced torsional resonator (BTR). This patented technology has a significant advantage over competitors since it allows the sensors to be compact, lightweight, and unaffected by external vibrations.
Rheonics SRV and SRD are well proven in mining industry applications. For example, common use cases are monitoring of ore slurry transport, flotation, water management, drilling mud (also in deep seam mining), or thickening stages. Accurate and continuous monitoring helps optimize concentration control, metal recovery efficiency, and overall process stability in abrasive and chemically aggressive environments.

Relevant parameters
Viscosity and density measurements are used in the mining industry for process monitoring, as well as to track other related parameters of interest. These include:
Solids concentration (% w/w or % solids)
One of the most critical control variables in mineral processing. It directly impacts grinding efficiency, flotation recovery, and tailings management.
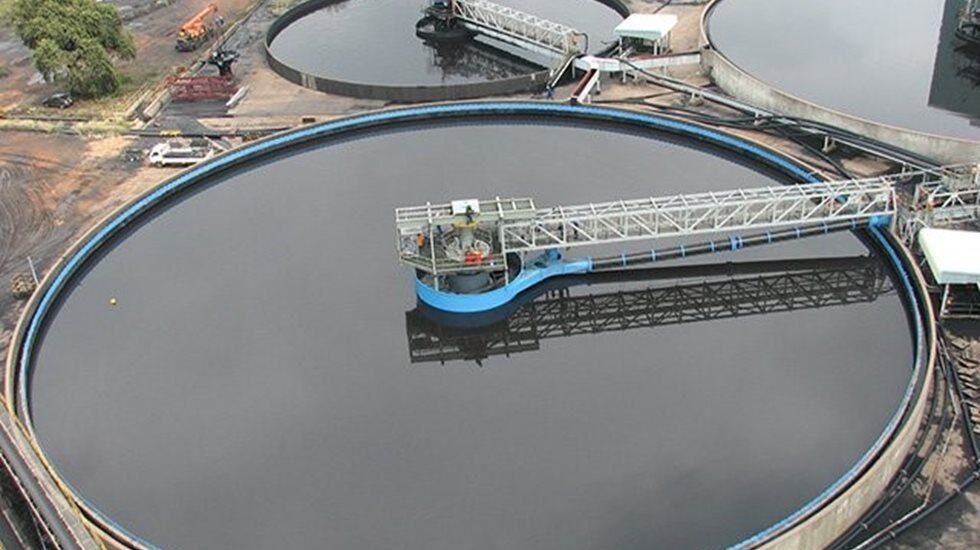
- Thickeners
- Hydrocyclones
- Flotation cells
- SAG/ball mills
- Tailings tanks
Slurry texture or flowability
Important for proper transport and processing. If a slurry is too thick or too thin, it can lead to blockages, pump damage, or poor separation performance.
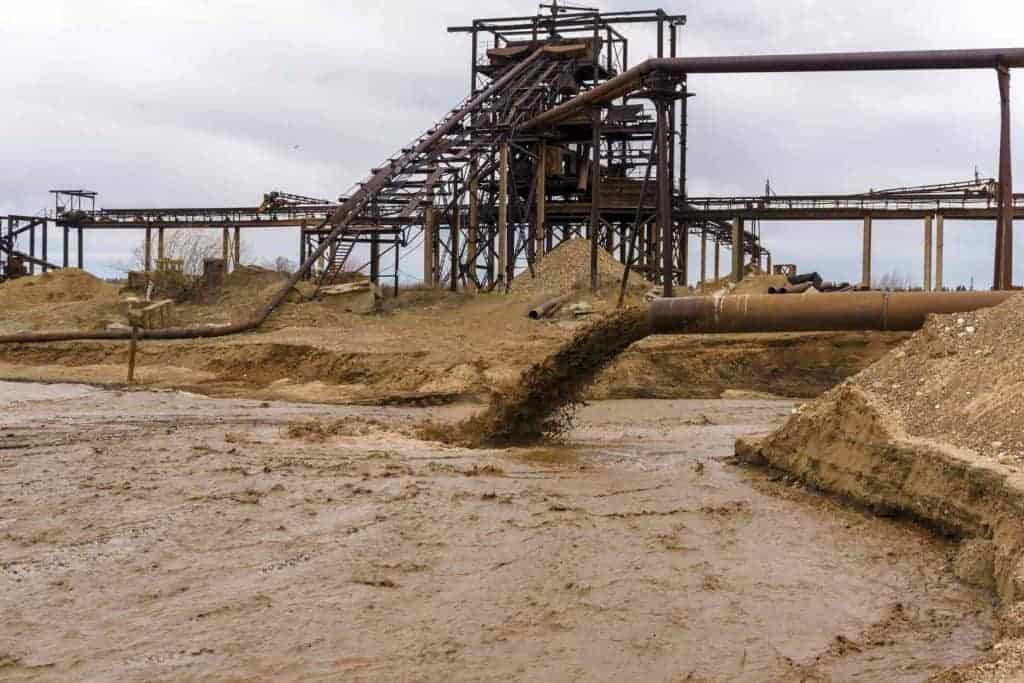
- Slurry transport pipelines
- Slurry pumps
- Mill feeders
- Wet crushing
- Mixing tanks with agitators
Chemical composition or mixing homogeneity
It is a key indicator in leaching, flotation, pH control, reagent dosing, and flocculation. Inconsistencies in these properties can signal poor mixing, incomplete dissolution, or layering, affecting recovery and increasing reagent consumption
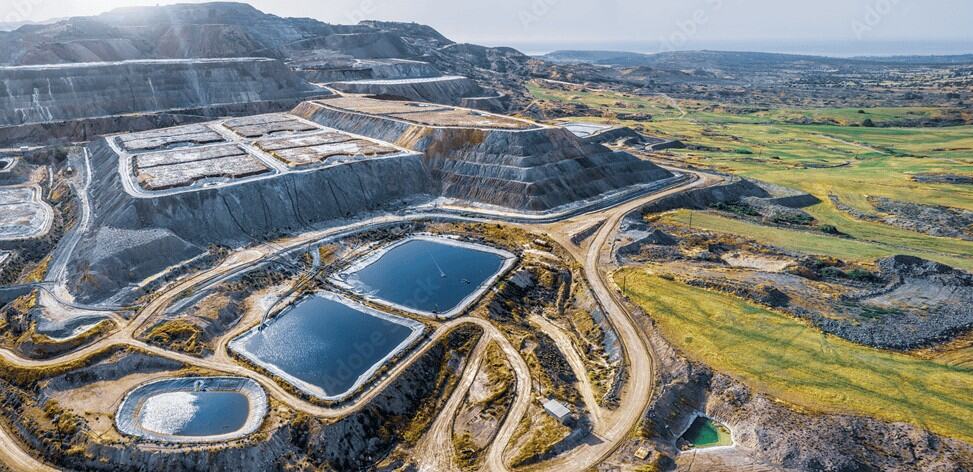
Examples:
- Leaching tanks
- Flocculation
- Reagent dosing
- Neutralization / pH control
- Agitation in flotation cells
- Reagent preparation tanks
Viscosity & Density as Process Indicator
SRV Inline Viscosity Meter
This sensor measures a wide range of viscosity and temperature in real-time and is suitable for installation in tanks to monitor mixing processes and in pipelines for continuous measurement of flowing fluid. Rheonics SRV is specially suited for high-speed mixing processes and is unaffected by the presence of bubbles in the fluid or external vibrations.
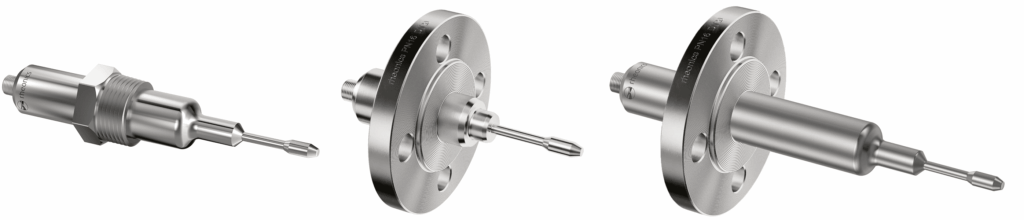
Viscosity measures a fluid’s resistance to flow. In slurries, viscosity is influenced by:
- Solids content
- Particle size distribution
- Shape and chemical interaction of particles
- Temperature
As viscosity increases, the slurry becomes harder to pump, mix, or transport. Viscosity measurements allow operators to:
- Detect when slurries are becoming too thick, risking blockages or pump overload.
- Monitor shear behavior and identify issues like particle agglomeration or thinning.
- Understand and control the overall flow behavior (rheology) under different process conditions.
SRD Inline Density and Viscosity Meter
This sensor adds density to viscosity and temperature measurement in real time. It is best suited for installation in pipelines and tanks with a constant and low mixing speed. Adding density to the measurements allows further fluid concentration calculations; however, it has a narrower measurement viscosity range compared to the SRV, and high concentrations of bubbles can add noise to readings due to the density measurement. SRD is also not affected by external vibrations.
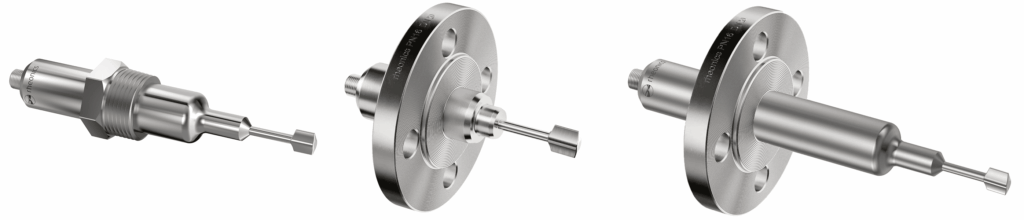
Density refers to the mass of a material per unit volume. In the context of slurries, it is strongly correlated with the percentage of solids present. As the solids concentration increases, so does the density.
Density measurements allow operators to:
- Track solids content continuously.
- Detect dilution issues or changes in composition.
- Control processes like thickening, flotation, and grinding with better accuracy.
In addition, the SRD electronics support custom calculations of process variables, based on real-time inputs of density, viscosity, and temperature.
Key Mining Applications
Drilling & Blasting
Drilling and blasting are the first steps in mineral extraction, breaking rock into manageable sizes
Poor fragmentation leads to increased energy consumption in downstream crushing and higher equipment wear.
- High density in explosive emulsions or slurries (water gels) can reduce blast effectiveness
- High viscosity in explosive emulsions or slurries (water gels) can obstruct proper flow.
Rheonics sensors installation on mixing lines or tanks of drilling fluids and explosive emulsions allows to:
- Maintain optimal explosive emulsion or slurries properties
- Improve explosive performance and blast quality
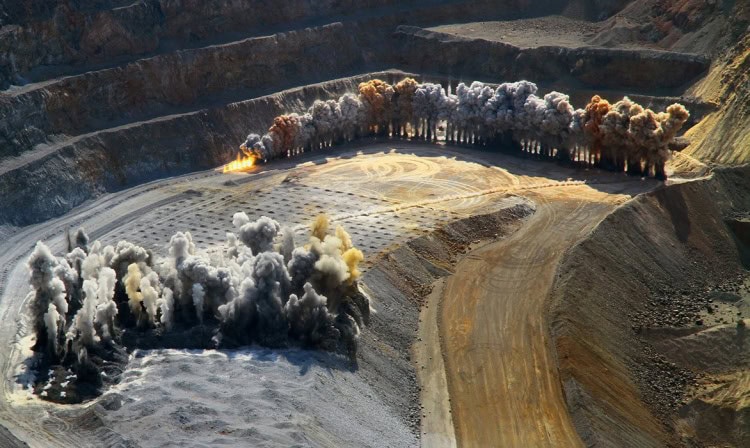
KPIs of interest | Impact with Rheonics Instruments |
---|---|
Explosive Consistency Deviation (%) | Reduced by controlling mixing and pumping |
Drill Penetration Rate (m/hr) | Improved by maintaining drilling fluid optimal properties |
Rock Fragmentation Uniformity (Index) | Enhanced due to better explosive performance |
Drill Bit Wear Rate (Hours/bit) | Reduced through better lubrication and lower mechanical stress during drilling |
Grinding & Classification
Crushing and grinding are the first steps in mineral processing, where ore is reduced in size to facilitate forward extraction processes.
This stage’s efficiency directly impacts the success of downstream operations like flotation and leaching.
- High density can overload the mill and waste energy.
- Low density leads to poor grinding and not optimal particle size.
- High viscosity reduces media motion and dampens grinding action.
Rheonics sensors installation on the slurry feed and discharge pipelines of mills and cyclones in grinding circuits allows to:
- Adjust water addition or feed rate.
- Prevent mill overloading
- Optimize energy usage
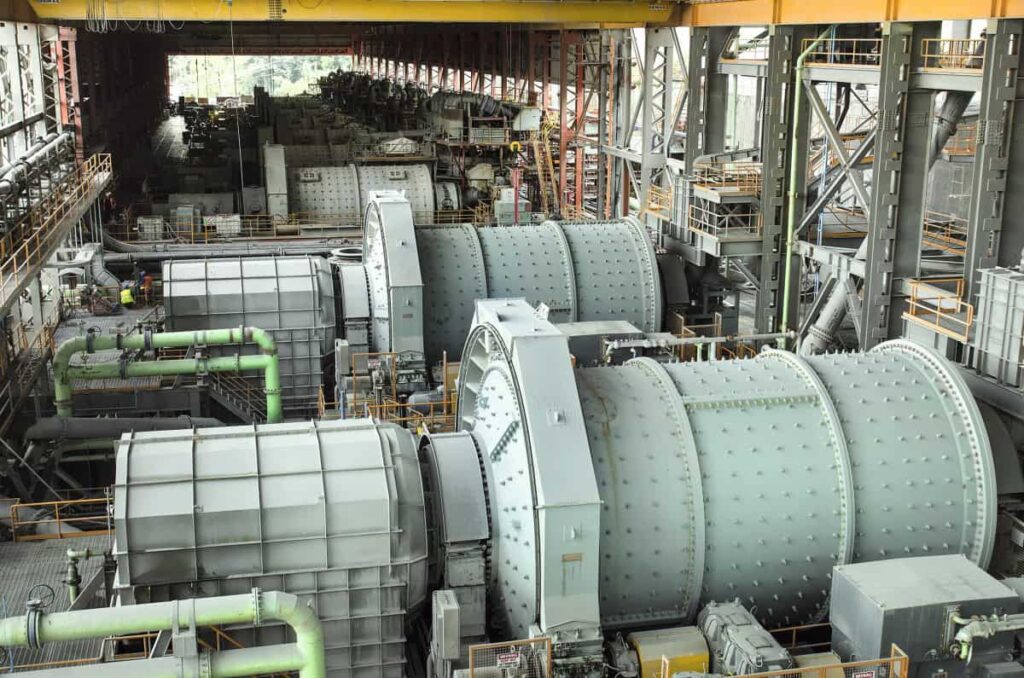
KPIs of interest | Impact with Rheonics Instruments |
---|---|
Specific Energy Consumption (kWh/ton) | Reduced via optimal slurry conditions |
Passing Desired Product Size (%) | Increased due to stable grinding performance |
Product Size Variation (Ratio) | Lower variability, better downstream control |
Mill Throughput (tons/hour) | Increased by avoiding process instability and downtime |
Flotation & Separation
Flotation is a vital separation step in mineral processing, used to selectively recover valuable minerals.
Poor separation and middlings formation can result in higher reagent use and lower recovery.
- High density affects air dispersion and reagent effectiveness.
- High viscosity might limit bubble-particle attachment.
Rheonics sensors installation in flotation feed lines, within flotation cells, or in tailings discharge in flotation circuits allows to:
- Adjust water, air, and reagent dosing.
- Ensure pulp conditions for selective flotation.
- Improve froth stability and mineral recovery.
- Prevent overuse of reagents and reduce losses to tailings.
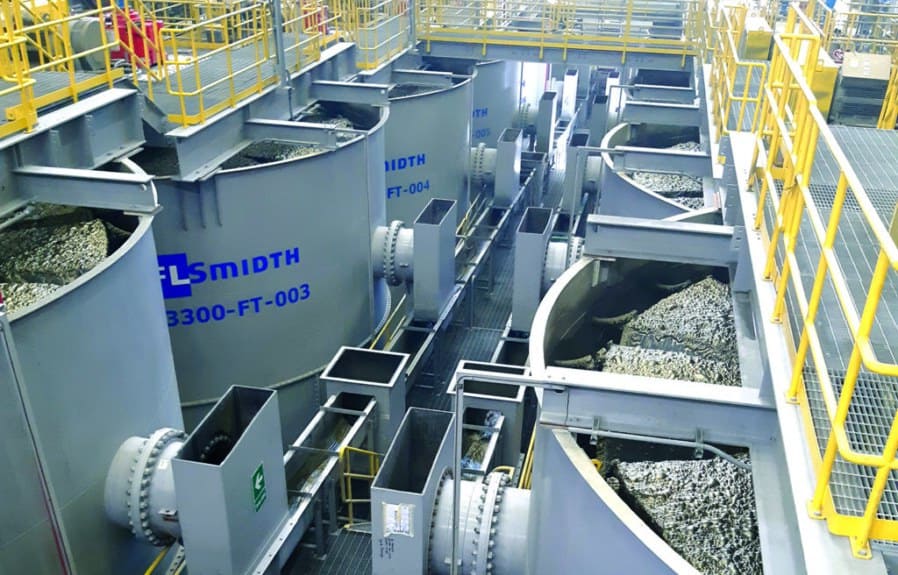
KPIs of interest | Impact with Rheonics Instruments |
---|---|
Valuable Mineral Recovery (%) | Increased via enhanced bubble-particle interactions |
Reagent Consumption (kg/ton) | Reduced due to optimized dosing |
Concentrate Grade (%) | Improved due to better separation selectivity |
Losses to Tailings (%) | Decreased by minimizing valuable mineral carryover |
Leaching & Acid Management
Leaching is a vital hydrometallurgical technique where valuable metals are extracted from ore by dissolving them into a chemical solution.
If the leach solution is not properly controlled, the metal recovery drops.
- High density can reduce retention time, limiting mineral dissolution.
- Excessive viscosity might slow reagent diffusion and metal transport.
Rheonics sensors installation in slurry pipes or directly in leaching tanks allows to:
- Optimize retention time and reagent concentration
- Enhance metal recovery
- Reduce leaching cycle duration
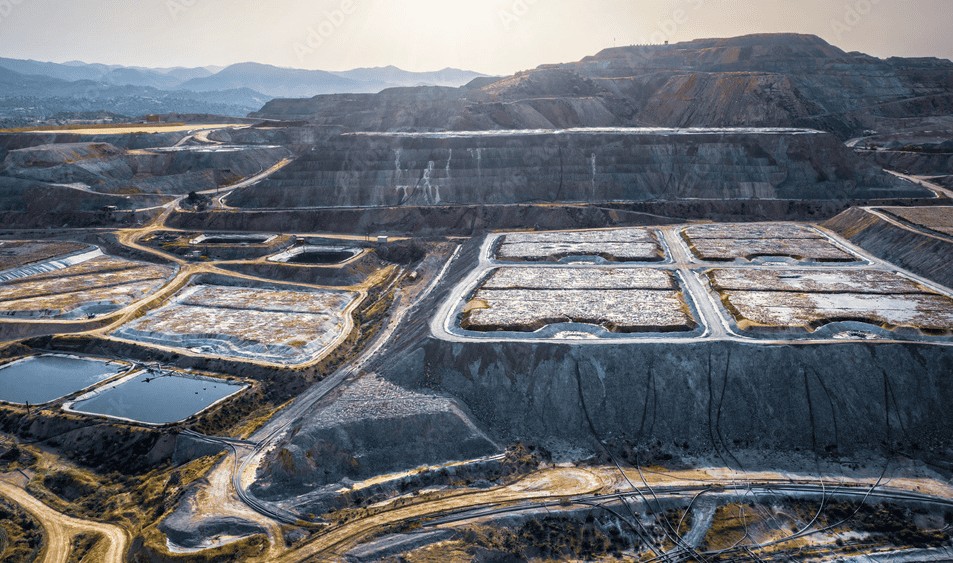
KPIs of interest | Impact with Rheonics Instruments |
---|---|
Target Metal Extraction Rate (%) | Increased due to optimized reagent contact and dissolution |
Leaching Cycle Duration (Hours) | Reduced by allowing faster completion of the leaching reaction |
Leaching Reagent Consumption (kg/ton) | Decreased due to optimized dosing |
Thickening & Dewatering
Thickening and dewatering are essential in mineral processing, reducing slurry volume by removing excess water.
Poor control may lead to inefficient water recovery and unstable tailings for disposal.
- Slurry density can indicate good thickening performance
- Excessive viscosity can slow sedimentation, making water separation difficult
Rheonics sensors installation in slurry feed lines, thickening tanks, underflow and overflow streams allows to:
- Optimize slurry feed rates and flocculant dosing
- Ensure that the underflow slurry achieves the desired solids concentration
- Maximize water recovery
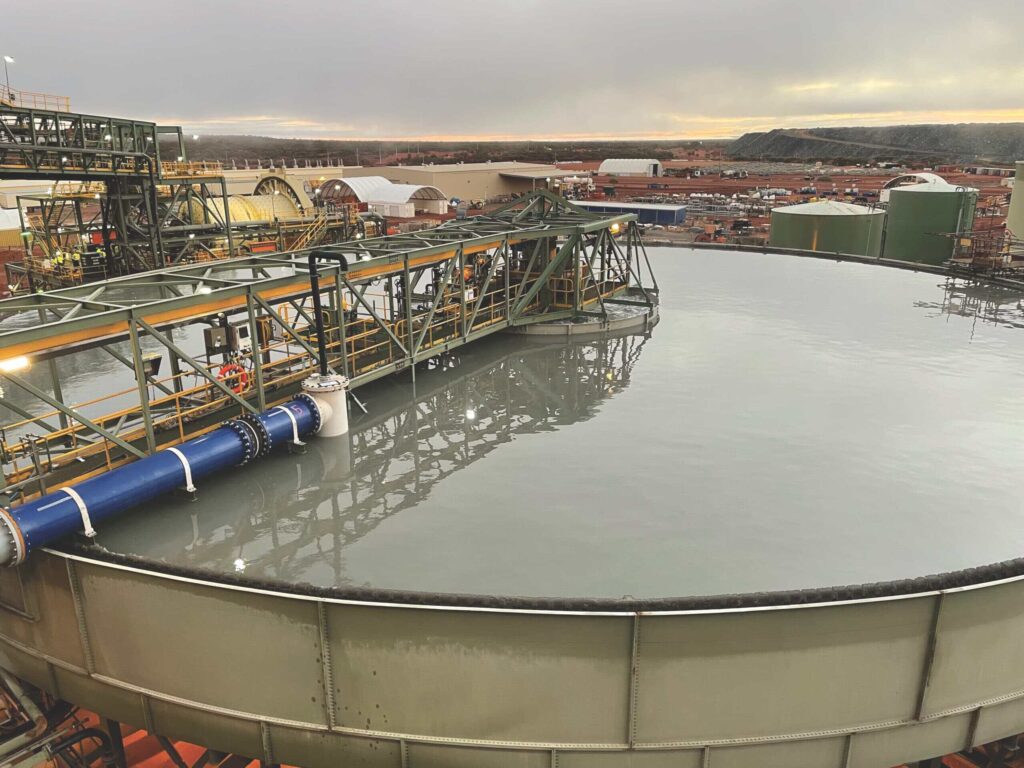
KPIs of interest | Impact with Rheonics Instruments |
---|---|
Underflow Solids Concentration (%) | Improved leading to more efficient tailings transport and disposal |
Water Recovery Rate (%) | Increased through optimized settling and enhanced separation efficiency |
Tailings Management
Tailings management is essential, ensuring safe and environmentally responsible handling of the waste generated during mineral processing.
If slurry properties are not properly controlled, operational risks and costs increase.
- High density variations can affect tailings stability and long-term safety.
- High viscosity raises pumping energy consumption and may cause pipeline blockages.
Rheonics sensors installation in tailings pipelines or ponds allows to:
- Detect flow issues early and prevent pipeline blockage
- Support geotechnical monitoring of tailings deposition
- Optimize pumping energy usage
- Effective water recovery from tailings ponds by identifying sedimentation levels
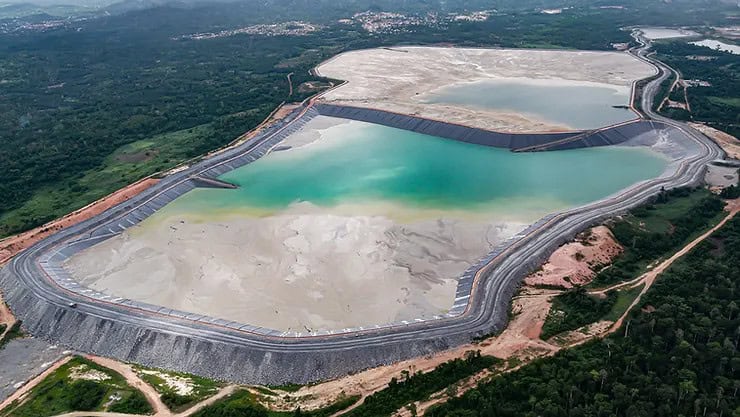
KPIs of interest | Impact with Rheonics Instruments |
---|---|
Tailings Pipeline Blockage Frequency (Incidents/year) | Reduced due to proactive monitoring to prevent blockages |
Specific Energy Consumption for Pumping (kWh/ton) | Decreased by optimizing the pumping parameters |
Tailings Slurry Density Variation (%) | Reduced by improving the Tailing Storage Facility (TSF) stability and deposition consistency |
Water Recovery Efficiency (%) | Improved by monitoring sedimentation levels |
Lubrication management
Lubrication management ensures the continuous operation of heavy mining equipment, including haul trucks, shovels, and drills.
Poor lubricant condition can increase engine wear or even equipment failure, leading to:
- Reduced equipment lifespan
- Unexpected downtime and costly repairs
Rheonics sensors installation in lubrication systems or oil analysis setups to continuously monitor, allows to:
- Enable condition-based maintenance
- Early detection of lubricant degradation
- Improve equipment reliability and reduce maintenance costs
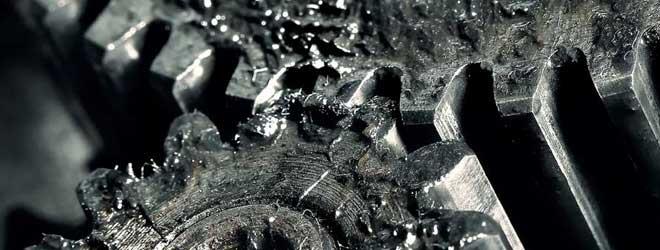
KPIs of interest | Impact with Rheonics Instruments |
---|---|
Equipment Downtime due to Lubrication Failures (Hours/month) | Reduced through early detection of lubricant breakdown |
Lubricant Consumption (Liters/month) | Decrease through optimized change intervals |
Component Replacement Frequency (Ratio) | Reduced as proper lubrication extends part life and reduces wear |
Process Conditions and Best Practices
Abrasion by Erosion
In mining operations, abrasive slurries can erode sensor probes over time. In that case, it should be considered that only the sensor probe needs replacement; the electronics and cable can remain in place. Lifespan will depend on particle size, flow velocity, and slurry composition. Rheonics probes also include an abrasion monitoring feature, alerting users before failure occurs to ensure continuous operation.
Flow speed limit
Rheonics SRV and SRD probes are generally compatible with flow speeds up to 10 m/s, since mining slurries can be pumped near such high velocities to prevent settling, it is recommended to install the probe parallel to flow direction in elbows, as this can reduce mechanical impact, however, speeds in this range can still add too much noise to readings. For more details, see Rheonics Type-SR sensors for high flow rate and high viscous applications
Particles in fluid
Rheonics sensors can handle micron-sized soft particles with minimal impact on accuracy, and any added signal noise can be filtered by the electronics. However, slurries with large particles (millimeter-scale or above) can cause reading instability and mechanical damage to the sensor. So pre-screening or installation away from these particles should be considered.
References
[1] Metso. “Beginner’s Guide to Thickeners”. https://www.metso.com/insights/blog/mining-and-metals/beginners-guide-to-thickeners/
[2] FluidFlow. “Slurry Piping Systems in Mining & Mineral Processing Industries”. https://blog.fluidflowinfo.com/slurry-piping-systems-in-mining-mineral-processing-industries/
[3] Emerson. “Enhancing Safety and Operational Performance in Heap Leach Mining Operations”. https://www.emerson.com/sv-se/automation/measurement-instrumentation/common-applications/enhancing-safety-and-operational-performance-in-heap-leach-mining-operations
[4] Mineser. “Drilling and Blasting”. https://mineser.de/eng/page/33/drilling-and-blasting/
[5] AT Minerals. “Trends in the Mining Industry”. https://www.at-minerals.com/en/artikel/at_Trends_in_der_Minenindustrie-3596021.html
[6] MiningDoc. “Optimize Flotation Performance by Adjusting Particle Size Distribution”. https://www.miningdoc.tech/2025/06/03/optimize-flotation-performance-by-adjusting-particle-size-distribution/
[7] Mining Technology. “Innovators in Extraction by Leaching”.https://www.mining-technology.com/data-insights/innovators-extraction-by-leaching-mining-2/
[8] Australian Mining. “Thickener Upgrade: Where Financial and Sustainability Overlap”. https://www.australianmining.com.au/thickener-upgrade-where-financial-and-sustainability-overlap/
[9] JOUAV. “Mine Tailings Monitoring with Drones”. https://www.jouav.com/blog/mine-tailings.html
[10] Machinery Lubrication. “Open Gear Lubrication”. https://www.machinerylubrication.com/Read/242/open-gear-lubrication