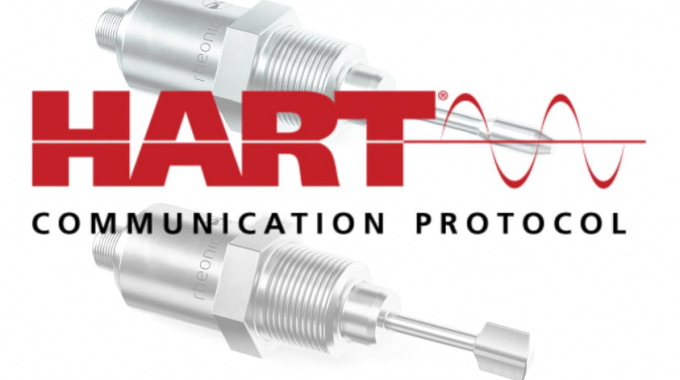
HART partnership between FieldComm Group and Rheonics
Rheonics is proud to announce its partnership with FieldComm Group. FieldComm Group owns the HART specifications and provides specification development, training, and product registration services associated with the technology. Our partnership will enable faster and more accurate data communication, leading to more efficient operations and improved safety. We look forward to a successful collaboration.
Our membership can be found at Current Members | FieldComm Group
-
Manufacturer (Hexadecimal): 0x615D
-
String Description (Company Name): RHEONICS
Figure 1. HART partnership between FieldComm Group and Rheonics
Benefits of HART Protocol
HART offers these advantages for the viscosity and density monitoring:
- Analog and Digital Communication: Simultaneous transmission of process data and digital information.
- Compatibility: Works with various industrial instruments and systems.
- Remote Configuration: Allows remote device setup and calibration.
- Enhanced Diagnostics: Provides detailed device status and maintenance alerts.
- Backward Compatibility: Integrates with existing 4-20 mA systems.
- Interoperability: Works with various control systems and data devices.
- Data Logging: Logs data and events for analysis and reporting.
- Long Cable Runs: Supports extended cable distances.
- Reduced Wiring Costs: Saves on installation expenses.
- Improved Safety: Minimizes the need for on-site troubleshooting.
- Reduced commissioning time, for example, by configuring all devices directly from the system and using configuration assemblies to enable plug-and-play operations.
- Global Acceptance: An internationally recognized standard.
What is the HART Protocol?
“HART” is an acronym for Highway Addressable Remote Transducer. The HART Protocol superimposes digital communication signals at a low level on top of a 4-20mA signal using the Frequency Shift Keying (FSK) standard.
The HART protocol is used worldwide to send and receive digital information on analog current loops (4-20 mA) between field instruments and distributed control systems.
How HART Protocol works?
Using the same 4-20mA wiring used for analog communications in Channel 1 from the Rheonics SME, a digital signal is encoded with a technique known as Frequency Shift Keying (FSK). Data from the digital signal includes PV, status, diagnostics, and additional measurements or calculations.
Figure 2. Signal modulation over 4-20mA [2]
In FSK, the digital information is encoded by shifting the frequency of the carrier signal between two predefined frequencies. In the case of HART, these frequencies are typically 1200 Hz (mark frequency) and 2200 Hz (space frequency). By toggling between these two frequencies, HART devices can transmit digital data over the analog current loop without interfering with the primary 4-20mA current signal used for process control. This allows for bi-directional communication, enabling configuration, monitoring, and diagnostics of field instruments in industrial applications.
Why do we have this protocol with our sensors?
The HART protocol has a crucial role to play in industrial automation, especially when it comes to DCS and PLCs. By connecting analog and digital communication, it offers a number of critical benefits.
DCS environments require HART integration so that various field devices can communicate seamlessly with the central control system. The DCS relies on real-time data to control and monitor processes, and HART’s electronic communication capability makes it possible to access complete device diagnostics and configurations remotely. As a result, faster decisions can be made, downtime is reduced, and overall system efficiency is increased.
With PLCs, HART can be used to integrate intelligent field instruments into automation systems. The ability of HART to transmit digital information alongside analog signals makes PLCs capable of receiving important device status information, remotely configuring devices, and automating complex processes. By integrating these systems, flexibility is increased and manual intervention is reduced, which ultimately enhances productivity.
HART communication is integrated in Rheonics viscosity and density sensors under correct configuration. Go to Rheonics RFQ pages and select C8: HART protocol in Additional FieldBus Communication Options.
Rheonics Expertise
A few typical applications where our customers are using HART protocol are:
- SRD sensor with HART where we can feed density measurements into another meter that requires periodic density updates in order to determine other variables through an algorithm
- Transmission of density (weight) of drilling mud over HART and WirelessHART (using converters) to control room
- The viscosity of batter mix that is applied to various appetizer food products.
- Plywood glue manufacturing and application – measure and transmit viscosity and temperature of glue
- Measure and transmit viscosity in process for water-based ink
- Measure and transmit density, viscosity and temperature of ceramic slurry from the slurry drum to the PLC and SCADA system in shell rooms
- Monitoring and transmission of density, viscosity and temperature to SCADA system over HART in Processing plants for food production as well as in the beverage industry and dairies
- Automation and control for water/wastewater treatment uses PLC with HART communication to get sewage water density and viscosity for nitrification, polyelectrolyte, and calamity detection
- and many more ..
What is available in HART?
For HART communication, Rheonics provides the following variables (PV, SV, TV, and QV) over Channel 1 analog output 4-20mA.
Process viscometer SRV default configuration | |
PV | Viscosity |
SV | Density |
TV | Temperature |
QV | Sensor Status |
Process density meter and viscometer SRD default configuration | |
PV | Density |
SV | Viscosity |
TV | Temperature |
QV | Sensor Status |
Resources
For more information about how Rheonics has implemented HART in all their devices visit: