Introduction
Batters mixes are widely used as a coating for deep-fried foods and in many other products including cakes, waffles, doughnuts, biscuits, meat, breads, pancakes, etc. When used as coating, the batter is typically applied by dipping, or spraying onto continuous baking drums and oven bands. Depending on the type of food product, the processing objectives and challenges may be different but one thing is fairly certain – the food companies strive to meet their requirements of consistency, quality and freshness, helping them develop innovative products, while lowering production costs and easing maintenance.
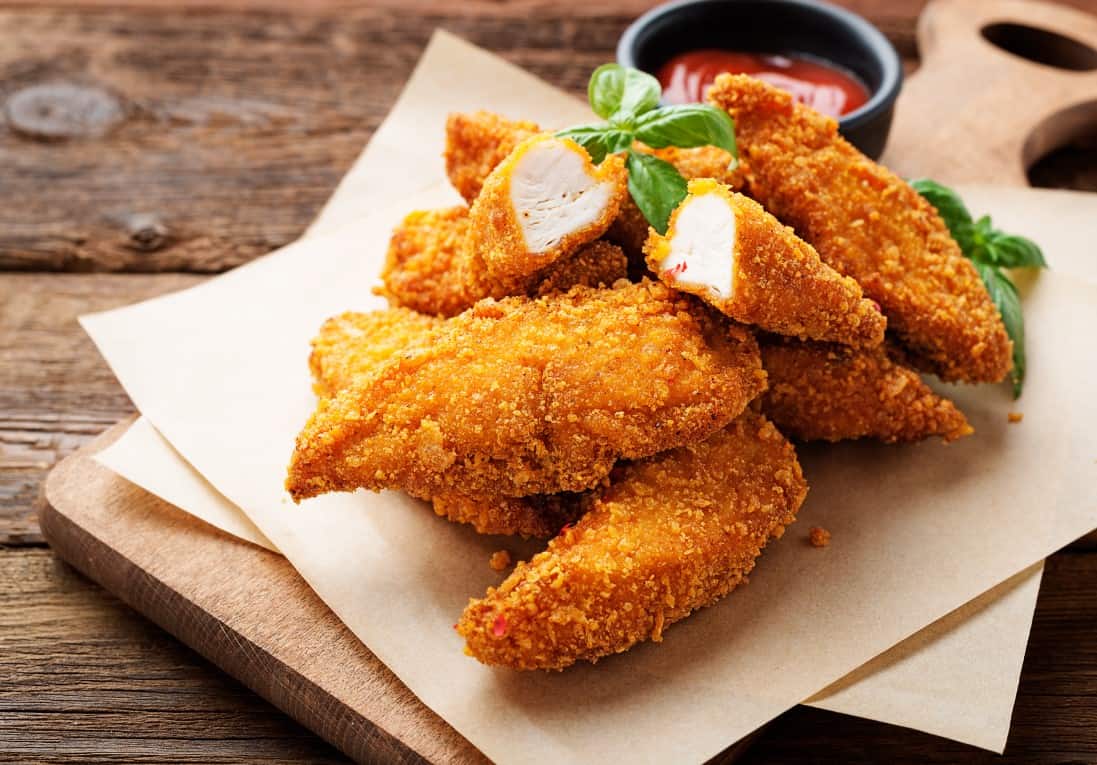
Application
Viscosity is crucial to production of batter mixes. Such systems typically consist of a number of dispersed phases such as flour, fat, water and air. Sufficient viscosity is required to stop phase separation during mixing, floor time and baking in the oven. For highly viscous batter systems, there is usually sufficient viscosity to stop phase separation and to trap and retain air (during bread production). However, for less viscous batter systems – wafers and puddings, can result in loss of air beaten into the batter during mixing and separation of solids which can be detrimental to the end product quality.
Cake batters need to be sufficiently viscous to prevent loss of gas bubbles during mixing, since these bubbles are recipients of the gas produced by raising agents and steam, which cause expansion and reduce batter density. Batter becomes thinner when heated up in the oven, thus increasing the likelihood of phase separation of the denser components, such as starch granules, which may sink to the bottom of the baking tin. The separation of recipe components therefore needs to be prevented by maintaining the right viscosity up to the point where the structuring is set.
The quality of foods such as soups, sauces, gravies, custards, flans, desserts, and baked products, to name a few, depend heavily on structure forming properties of materials such as starch which in turn can be controlled by monitoring its viscosity. Due to incorrect viscosity of the prepared mixture, after starch material is cooked, the granules swell and become fragile and can break down under shear. It can badly affect the characteristic eating quality of the food.
Viscosity is the key to achieve target properties in each of the following steps in the food industries involving batter production:
- Batter Preparation Unit (Mixer): This step is the preparation of batter mixes involving dosing correct amount of powder into the mixing system, where it will meet correct water supply. Generally, batter mixes are prepared on a batch basis and discharged to a holding tank prior to use. The prepared mix must be consistent and must have the correct viscosity characteristics for further processing steps as well as the end product quality.
- Applicator Unit (Coating): The prepared batter system in the batter mixer is passed through heat exchangers to get the optimal temperature which may be then applied/sprayed onto the food to be coated with the batter mix before further processing. Correct viscosity during the coating process is the key to the process efficiency and the end product quality.
Why is viscosity management critical in batter production and application?
The broad and significant factors which make viscosity management important in virtually every mixing application:
- Quality: Viscosity of the batter systems is an indicator of key target properties, thus making it critical to the quality. Depending upon the food product, the viscosity essentially determines key properties of the produced batter mix. Under mixing will give rise to non-homogeneity and over mixing will affect the end product quality, thus making continuous viscosity monitoring indispensable to desired quality.
- Consistency: To ensure consistency from batch to batch, maintain shape in deposition process and to maintain a consistent coat weight, viscosity control is essential.
- Reduced waste and cost savings: Over-mixing can not only change the state of end product but is a waste of raw materials, time and energy. Viscosity management in the mixing process can enable identifying the endpoint reliably and accurately, thus leading to significant reduction in rejects and wastes. Also, significant waste reduction is possible with accurate viscosity control during the batter coating applications.
- Efficiency: Hassle free, real time monitoring of mix viscosity can save a lot of time and effort which is involved in offline analysis of the sample and making process decisions based on that analysis.
- Environment: Lowering the amount of wastes is good for the environment.
Challenges
Mixing operators in the food industry recognize the need to monitor viscosity but making that measurement has challenged process engineers and quality departments over the years.
Challenges with Off-line viscosity measurements
Existing laboratory viscometers are of little value in process environments because viscosity is directly affected by temperature, shear rate and other variables that are very different off-line from what they are in-line. At best, flow cups are used to measure the viscosity of batter. Condition of the off-line viscosity measurement is often a non-agitated sample that may not give a true representation of the batter mix. Collecting samples to be tested in the laboratory and making process decisions based on the findings in the laboratory can be highly cumbersome, time-consuming and extremely inefficient. It is pretty inaccurate, inconsistent and non-repeatable even with an experienced operator.
Challenges with Rotational viscometers
Rotational viscometer measures mix viscosity by monitoring the torque required to rotate a spindle at a constant speed within the fluid. The viscosity measurement principle is as follows – the torque, generally measured by determining the reaction torque on the motor, is proportional to the viscous drag on the spindle, and thus to the viscosity of the fluid. This technique however poses more problems than it solves:
- Torque monitoring is carried out by measuring the supply current during the mixing process. Fluctuations in supplied power to the motor renders the measurements completely unreliable, making is difficult to keep costs at a controllable level and generates higher quantities of waste concrete. Controlling power fluctuations by switching to a more reliable power supply in form of a generator can be a very expensive option.
- Because the spindle is rotating, the wires attached to the torque sensor on the shaft would wind up and snap. Slip rings can be alternatives, but not ideal because of set-up times, costs and inevitable wear and tear.
Rheonics' Solutions
Automated and continuous in-line viscosity measurement is crucial to concrete mix. Rheonics offers the following solutions for the concrete mixing process:
- In-line Viscosity measurements: Rheonics’ SRV is a is a wide range, in-line viscosity measurement device with inbuilt fluid temperature measurement and is capable of detecting viscosity changes within any process stream in real time.
- In-line Viscosity and Density measurements: Rheonics’ SRD is an in-line simultaneous density and viscosity measurement instrument with inbuilt fluid temperature measurement. If density measurement is important for your operations, SRD is the best sensor to cater to your needs, with operational capabilities similar to the SRV along with accurate density measurements.
Automated in-line viscosity measurement through SRV or an SRD eliminates the variations in sample taking and lab techniques which are used for viscosity measurement by the traditional methods. Rheonics’ sensors are driven by patented torsional resonators. Rheonics balanced torsional resonators together with proprietary 3rd generation electronics and algorithms make these sensors accurate, reliable and repeatable under the harshest operating conditions. The sensor is located in-line so that it continuously measures the mix viscosity. The consistency of the concrete mix can be ensured by automation of the dosing system through a controller using continuous real-time viscosity measurements. Both the sensors have a compact form factor for simple OEM and retrofit installation. They require no maintenance or re-configurations. Using no consumables, SRV and SRD are extremely easy to operate.
Rheonics' Advantage
Hygienic, sanitary design
Rheonics SRV and SRD are available in tri-clamp and DIN 11851 connections besides custom process connections.
Both SRV & SRD conform to Food Contact Compliance requirements according to US FDA and EU regulations.
Compact form factor, no moving parts and require no maintenance
Rheonics’ SRV and SRD have a very small form factor for simple OEM and retrofit installation. They enable easy integration in any process stream. They are easy to clean and require no maintenance or re-configurations. They have a small footprint enabling in-line installation, avoiding any additional space or adapter requirement on the press/systems.
High stability and insensitive to mounting conditions: Any configuration possible
Rheonics SRV and SRD use unique patented co-axial resonator, in which two ends of the sensors twist in opposite directions, cancelling out reaction torques on their mounting and hence making them completely insensitive to mounting conditions and flow rates. These sensors can easily cope up with regular relocation. Sensor element sits directly in the fluid, with no special housing or protective cage required.
Instant accurate readouts on process conditions – Complete system overview and predictive control
Rheonics’ software is powerful, intuitive and convenient to use. Real-time viscosity can be monitored on a computer. Multiple sensors spread across the factory floor are managed from a single dashboard. There is no effect of pressure pulsation from pumping on sensor operation or measurement accuracy. In addition, the sensor is insensitive to any vibrations or electrical noise from external machinery.
Easy installation and no reconfigurations/recalibrations needed
Replace sensors without replacing or re-programming electronics
Drop-in replacements for both sensor and electronics without any firmware updates or calibration coefficient changes.
Easy mounting. Screws into ¾” NPT threaded in-line fittings, or Flanged connections.
No chambers, O-ring seals or gaskets.
Easily removed for cleaning or inspection.
SRV available with flange, DIN 11851 hygienic and tri-clamp connection for easy mounting and dis-mounting.
Low power consumption
24V DC power supply with less than 0.1 A current draw during normal operation (less than 3W)
Fast response time and temperature compensated viscosity
Ultra-fast and robust electronics, combined with comprehensive computational models, make Rheonics devices one of the fastest and most accurate in the industry. SRV and SRD give real-time, accurate viscosity (and density for SRD) measurements every second and are not affected by flow rate variations!
Wide operational capabilities
Rheonics’ instruments are built to make measurements in the most challenging conditions. SRV has the widest operational range in the market for inline process viscometer:
- Pressure range up to 5000 psi and higher
- Temperature range from -40 up to 300°C
- Viscosity range: 0.5 cP up to 50,000+ cP
SRD: Single instrument, triple function – Viscosity, Temperature and Density
Rheonics’ SRD is a unique product that replaces three different instruments for viscosity, density and temperature measurements. It eliminates the difficulty of co-locating three different instruments and delivers extremely accurate and repeatable measurements in harshest of conditions.
Achieve the right coat quality, cut down costs and enhance productivity
Integrate an SRV or SRD in the process line and ensure uniformity and consistency throughout the coating process. Achieve constant colours & thickness without worrying about colour or thickness variations. SRV (and SRD) constantly monitors and controls viscosity (and density in case of SRD) and prevents overuse of materials. Reliable and automatic supply ensures that processes run faster and saves operators’ time. Optimise the coating process with an SRV and experience lesser wastes, fewer customer complaints, fewer shut downs and material cost savings. And at the end of it all, it contributes to a better bottom line and a better environment!
Clean in place (CIP)
SRV (and SRD) monitors the cleanup of the lines by monitoring the viscosity (and density) of the cleaning fluid during the cleaning phase. Any small residue is detected by the sensor, enabling the operator to decide when the line is clean for purpose. Alternatively, SRV provides information to the automated cleaning system to ensure full and repeatable cleaning between runs.
Superior sensor design and technology
Sophisticated, patented 3rd generation electronics drive these sensors and evaluate their response. SRV and SRD are available with industry standard process connections like ¾” NPT and 1” Tri-clamp allowing operators to replace an existing temperature sensor in their process line with SRV/SRD giving highly valuable and actionable process fluid information like viscosity besides an accurate measurement of temperature using an in-build Pt1000 (DIN EN 60751 Class AA, A, B available).
Environment friendly
Reduce the use of VOC (volatile organic compounds) in your process reducing the energy required to recover it or disposal costs. Manufacture smart while saving costs, ensuring high quality and protecting the environment.
Electronics built to fit your needs
Available in both an explosion-proof transmitter housing and a small-form factor DIN rail mount, the sensor electronics enables easy integration into process pipelines and inside equipment cabinets of machines.
Easy to integrate
Multiple Analog and digital communication methods implemented in the sensor electronics makes connecting to industrial PLC and control systems straightforward and simple.
Implementation
Directly install the sensor to your process stream to do real time viscosity and density measurements. No bypass line is required: the sensor can be immersed in-line, flow rate and vibrations do not affect the measurement stability and accuracy. Optimize mixing performance by providing repeated, consecutive, and consistent tests on the fluid.
Rheonics Instrument Selection
Rheonics designs, manufactures and markets innovative fluid sensing and monitoring systems. Precision built in Switzerland, Rheonics’ in-line viscometers has the sensitivity demanded by the application and the reliability needed to survive in a harsh operating environment. Stable results – even under adverse flow conditions. No effect of pressure drop or flow rate. It is equally well suited to quality control measurements in the laboratory. No need to change any component or parameter to measure across full range.
Suggested product(s) for the Application
- Wide viscosity range – monitor the complete process
- Repeatable measurements in both Newtonian and non-Newtonian fluids, single phase and multi-phase fluids
- Hermetically sealed, all stainless steel 316L wetted parts
- Built in fluid temperature measurement
- Compact form-factor for simple installation in existing process lines
- Easy to clean, no maintenance or re-configurations needed
- Single instrument for process density, viscosity and temperature measurement
- Repeatable measurements in both newtonian and non-newtonian fluids, single phase and multi-phase fluids
- All metal (316L Stainless Steel) construction
- Built in fluid temperature measurement
- Compact form-factor for simple installation in existing pipes
- Easy to clean, no maintenance or re-configurations needed