Treatment plants are faced with the challenge of stricter regulations and higher standards for finished water quality. New developments in control strategies and instrument design have overcome some of the previous limitations of monitoring and controlling the coagulation process. An online floc analyzer provides valuable information on the dynamics of particle aggregation subsequent to coagulation.
Optimizing coagulation will form floc that is large and easily settled. Fractal analysis has suggested that diffusion and collision of colloidal particles limit particle aggregation. So, proper mixing is a major factor influencing floc formation.
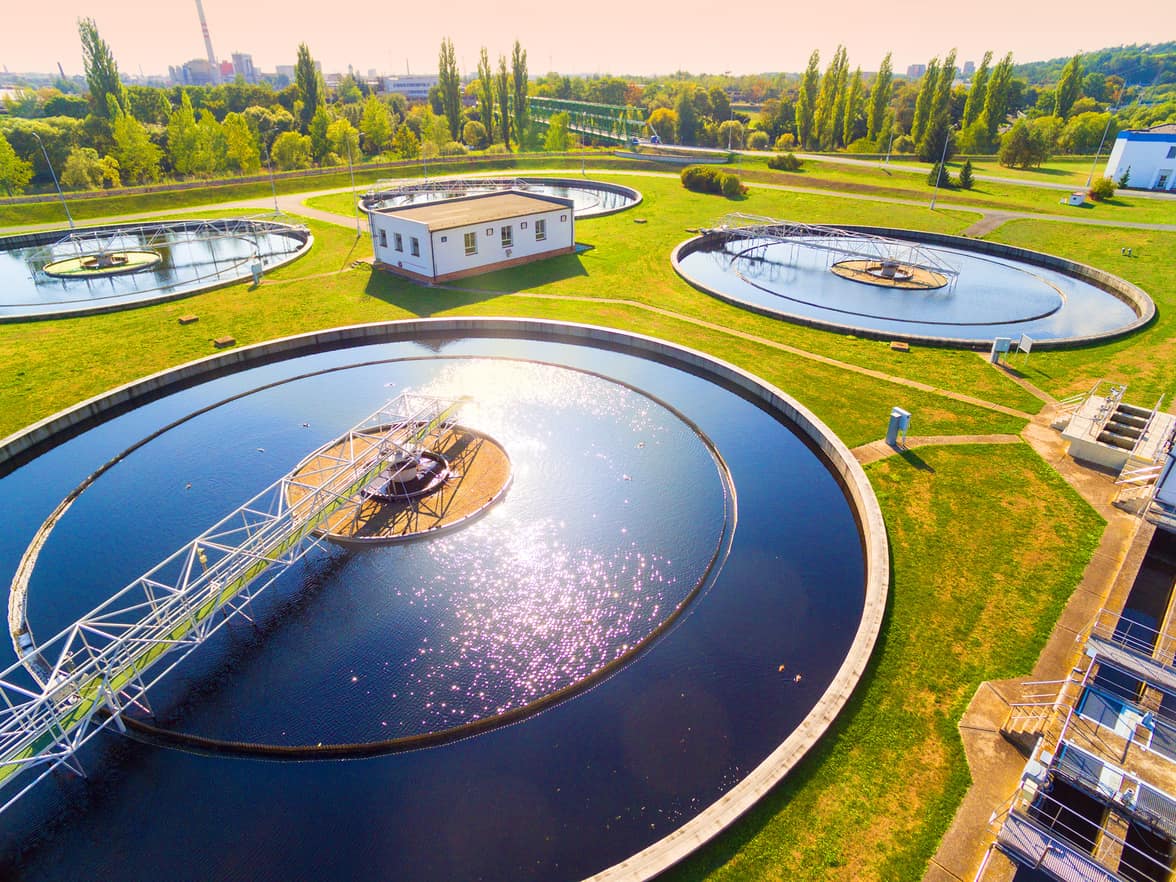
Application
Coagulation is an essential process for the removal of suspended and colloidal material from water and wastewater. Inline flocculation is a promising technique for the dewatering and remediation of oil sands tailings.
- To clean industry effluent and recycle it for further use
- To reduce the usage of fresh/potable water in Industries
- To cut expenditure on water procurement
- To meet the Standards for emission or discharge of environmental pollutants from various Industries set by the Government and avoid hefty penalties
- To safeguard environment against pollution and contribute in sustainable development
What is flocculation?
Flocculation is a water treatment process where solids form larger clusters, or flocs, to be removed from water. This process can happen spontaneously, or with the help of chemical agents. It is a common method of stormwater treatment, wastewater treatment, and in the purification of drinking water. One of the requirements for treated water leaving wastewater plants is the removal of suspended solids. Small solid particles affect the colour of the water and carry impurities into our natural water sources like rivers and the ocean.
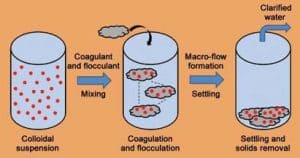
Coagulation and flocculation of a colloidal suspension upon addition of a coagulant-flocculant system after mixing with subsequent settling of the floc network
What are Flocculants?
Flocculants are compounds that stimulate the agglomeration of tiny particles in a solution, resulting in the formation of a floc, which subsequently floats to the top (flotation) or sinks to the bottom (sedimentation). Moreover, this may then be extracted from the liquid more readily. Inorganic & organic flocculants are available in a variety of charges, molecular weights, charge densities, & morphologies.
Consequences of incorrect concentration of the wastewater
Treatment plants are faced with the challenge of stricter regulations and higher standards for finished water quality.
Without the right concentration, there are:
- chances of catastrophic failure
- blocked treatment facility (sewage)
- frozen pipes, bursts
- improper water treatment
- improperly treated water is discharged leading to high penalty
New developments in control strategies and instrument design have overcome some of the previous limitations of monitoring and controlling the coagulation process. An online floc analyzer provides valuable information on the dynamics of particle aggregation subsequent to coagulation.
Optimizing coagulation will form floc that is large and easily settled. Fractal analysis has suggested that diffusion and collision of colloidal particles limit particle aggregation. So, proper mixing is a major factor influencing floc formation.
Industries:
Power Plant, Steel, Refineries, Mining, Food, Sugar, Distillery, Electronics, Fertilizers, Chemicals, Textile, Paper & Pulp, Cement, Hospitality, Commercial, Residential
Applications:
- Raw water clarification
- Colour removal
- Sludge dewatering
- De–oiling
- Industrial process applications
For waste treatment facilities to comply with stricter regulations and operate safely and efficiently, monitoring and control systems with the following characteristics are required:
- Can flexibly accommodate regulatory changes in monitoring subjects and limit values
- Monitoring and control points can be easily added at each process step
- The monitoring and control system can cope in real time with emergencies such as the discharge of toxic effluents into a river in a remote location.
- Seamlessly integrates with a centralized monitoring and control system, enabling integration of utility and production processes
- Can operate with high reliability and stability for long periods of time
Polyelectrolytes - the flocculation agents
Polyelectrolytes are chemical flocculants used in water treatment; they act mainly in the coagulation-flocculation stage and in the conditioning/thickening of the sludge line. Polyelectrolytes show many applications in fields, such as in water treatment as flocculation agents, in ceramic slurries as dispersant agents, and in concrete mixtures as super-plasticizers.
Polyelectrolytes are long chain organic polymers often having molecular weights in excess of one million and are either natural or synthetic in origin. The term “polyelectrolyte” was introduced to include those polymers which, by some ion-producing mechanism, can become converted to a polymer molecule having electrical charges along its length. The electrical charges arise from, the presence of ionizable functional groups along the polymer chain. Polyelectrolytes are, therefore, polymeric-electrolytes, i.e., having characteristics of both polymers and electrolytes.
Commercial polyelectrolytes used in the aggregation of suspended matter are water-soluble. They may come in granular forms, in form of powder, or as highly-viscous liquids. All existing polyelectrolytes have a tendency to degrade when stored over a period of time – For a particular product, such a period is usually stated by the manufacturer. In general, the more dilute a polyelectrolyte solution is, the faster the degradation, which probably involves the breaking up of the long chains, resulting in decreasing viscosity.
Extent of utilization of polyelectrolytes
The use and importance of polyelectrolytes is increasing rapidly. The number of manufacturers producing these materials is likewise increasing. Synthetic polyelectrolytes have found considerable applications in the following broad areas:
- Process industries
- Industrial wastewater treatment
- Water treatment
- Domestic wastewater treatment
Commercially available polyelectrolytes include PolyDimethylammonium chloride (PolyDADMAC), Polyacrylic acid (PAA), and Polystyrene sulfonate. Commercial grades of polyelectrolytes (PAAs) are available from Dow Chemical (Duramax, Tamol, Romax, Dowex), Rohm and Haas (Acusol, Acumer), BASF (Dispex®, Magnafloc®), and Arkema (Rheoslove, Terrablend). Specific uses of polyelectrolytes in process industries include clarification of raw sugar juice in the sugar industry; separation of gypsum from wet process phosphoric acid; settling improvement in coal-washer operation; increasing thickener capacity in wet process cement manufacture; separation of clay impurities from hot borax streams; improving the quality of metal deposition in the electrolytic refining or electrowinning of copper and zinc; improvement of thickening operations in uranium processing, and so on. Polyelectrolytes can also be used to treat industrial wastewater. The fight against river pollution is getting more and more intense, and industries need all the help they can get. Polyelectrolytes are becoming an increasingly important factor in resolving these pollution issues. In the future, polyelectrolytes will have a greater impact on industrial wastewater treatment than on municipal wastewater treatment. This might be due to the fact that industrial wastewater treatment plants are not subject to the same constraints as municipal wastewater treatment plants. As such, industrial waste treatment plant designers may be more focused on reducing overall treatment plant costs than on whether those savings result from capital investments or operating costs.
Preparation and dosing systems
Polyacrylamides are very high gramme-molecular weight polymers used as flocculants. These polymers are mainly available as a powder or an emulsion. They can be anionic or cationic. The main disadvantage of flocculation with polymers is the very small flocculation window, risking particles resuspension with few dosages increases.
Some of these products exist in the form of highly viscous solutions (5,000 to 10,000 centipoises) that can be pumped as supplied with secondary dilution at the feeding pump delivery.
The preparation process is based on three stages: dissolution, maturation and transfer.
- Dissolution. The polymer is humidified and dissolved by slow agitation, favouring the homogenization of the solution.
- The solution is kept in continuous and slow agitation.
- The level probes act so that the solution can be dosed automatically to the nest treatment.
With automation, the customer will be able to avoid manual interventions, as well as errors when it comes to dosage the product. This equipment manages to integrate the powdered polyelectrolytes in the solution to obtain a correct dispersion and performance of them within the water treatment process.
Polyelectrolyte solutions are extremely viscous and often only very small doses are required. It is therefore, essential that there is sufficient turbulence at the dosing point to ensure rapid and thorough mixing of the small amount of reagent with the main water flow. Dilute polyelectrolyte solutions are easier to disperse into the flow than concentrated solutions, but a balance must be struck otherwise the volume of polyelectrolyte solution added will become a significant proportion to the flow.
Automatic preparation unit: https://www.keiken-engineering.com/en/polyelectrolyte-preparation-equipment/
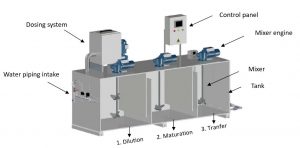
Automatic preparation unit (Ref: Keiken Engineering)
In-line dilution
In order to guarantee polymer effectiveness, it will almost always be necessary to dilute the solution prepared in order to achieve a uniform dispersion of the polymer through the water or previously coagulated sludge; therefore, this dilution will depend on polymer and sludge viscosity and on the mixing energy applied to the system. Consequently, the following target dilution levels will apply:
- 5 to 1 g · L–1in sludge treatment;
- 02 to 0.1 g · L–1in clarification.
This in-line dilution is carried out on the dispensing pump delivery. This solution is pumped to waste water plant, the solution is used to settle/coagulate the solids in wastewater. When the polyelectrolyte concentration is wrong then waste water can be released that can lead to penalty.
There are bench-scale testing and laboratory methods to determine the concentration:
- Pour Test
- Gravity Drainage Test
- Chopper Test
However, these methods are offline and cumbersome. They require operators to collect a sample of fluid, analyse them separately and then make process decisions. In comparison, inline devices that can display the mix properties and make automated corrected doses would be much more efficient, productive and reduce overall polymer consumption by exact dosing.
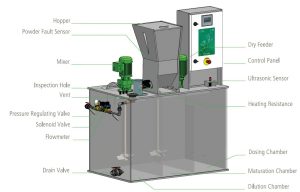
Polymer preparation Systems (Ref: PolySys CSL by Kozegho)
Viscosity – Indicator of Polymer Solution Efficiency
Polymer comes in three different forms – dry, solution (Mannich), and emulsion polymer. Most polymers used in wastewater industries are acrylamide-based and often called PAAM (polyacrylamide).
Emulsion polymers used for solids separation processes are hydrolyzed, of high molecular weight, and have very high viscosity. One of the most important characteristics of emulsion polymers is their fluidity and micron-sized polymer gels that enable operators to utilize in-line polymer mix/feed systems. They consist of polymer gels emulsified in 30% hydrocarbon oil. Depending on the content of water in the polymer gels, the active polymer in emulsion polymer ranges from 20% to 55%. Therefore, emulsion polymers cost more than dry polymer on a per pound basis. The polymer as delivered to a site is “neat” and includes water, oil, surfactants, and active polymer. However, the active content is the portion of the emulsion that actually conditions solids in downstream processes and it is the active content that should be considered when assessing appropriate polymer doses for solids processing systems. Emulsion polymers can be delivered in small 55-gallon drums, 270-gallon totes, or 4000 to 5000-gallon tanker loads.
The concept of two-stage mixing is well established in the polymer make-down process.
- First Stage: Very high energy mixing at the initial wetting stage to prevent “fisheye” formation
- Second Stage: Low energy mixing to minimize damaging the polymer molecules as they “uncoil” out of polymer gels/particles. Much longer residence time is required for the second stage than the first stage.
Quantity of friction as measured by the force resisting a flow in which parallel layers have at unit speed relative to one another. Polymer supplier data sheet provides a starting point for viscosity critical factor for polymer efficiency.
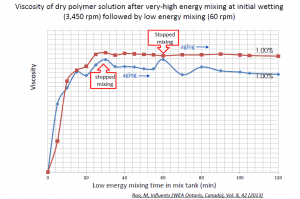
Viscosity Vs Mixing Time in polyelectrolyte preparation (Ref: https://www.wef.org/globalassets/assets-wef/3—resources/online-education/webcasts/presentation-handouts/25june20-final-deck-handouts.pdf)
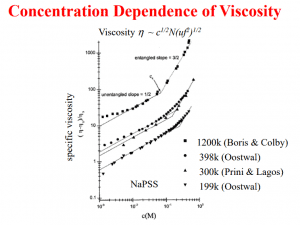
Concentration dependence of viscosity (Ref: http://boulderschool.yale.edu/sites/default/files/files/Polyelectrolytes_Lecture_3.pdf )
Rheonics’ solutions for polyelectrolyte dosing systems in wastewater treatment
Automated in-line viscosity measurement and control is crucial to control the viscosity during manufacturing process and ensure critical characteristics are in full compliance with requirements across multiple batches, without having to rely on offline measurement methods and sample taking techniques. Rheonics offers the following solutions for process control and optimisation,
Viscosity & Density Meters
- In-line Viscosity measurements: Rheonics’ SRV is a is a wide range, in-line viscosity measurement device capable of detecting viscosity changes within any process stream in real time.
- In-line Viscosity and Density measurements: Rheonics’ SRD is an in-line simultaneous density and viscosity measurement instrument. If density measurement is important for your operations, SRD is the best sensor to cater to your needs, with operational capabilities similar to the SRV along with accurate density measurements.
Integrated, turnkey quality management
Rheonics offers an integrated turn-key solution for quality management made of:
- In-line Viscosity measurements: Rheonics’ SRV – a wide range, in-line viscosity measurement device with in-built fluid temperature measurement
- Rheonics Process Monitor: an advanced predictive tracking controller to monitor and control in real-time variations of process conditions
- Rheonics RheoPulse with automatic dosing: A Level 4 autonomous system that ensures no compromise with set limits of viscosity and automatically activates by-pass valves or pumps to adaptively dose mixture components
The SRV sensor is located in-line so it continuously measures the viscosity (and density in case of SRD). Alerts can be configured to notify operator of necessary action or the entire management process can be fully automated with RPTC (Rheonics Predictive Tracking Controller). Using an SRV in an manufacturing process line, results in improved productivity, profit margins and achieves regulatory conformance. Rheonics sensors have a compact form factor for simple OEM and retrofit installation. They require zero maintenance or re-configurations. The sensors offer accurate, repeatable results no matter how or where they are mounted, without any need for special chambers, rubber seals or mechanical protection. Using no consumables and not requiring re-calibration, SRV and SRD are extremely easy to operate resulting in extremely low lifetime running costs.
Once the process environment is established, there is usually little effort required to maintain the integrity consistency of the systems – operators can rely on the tight control with Rheonics production quality management solution.
Rheonics' Advantage
Compact form factor, no moving parts and require no maintenance
Rheonics’ SRV and SRD have a very small form factor for simple OEM and retrofit installation. They enable easy integration in any process stream. They are easy to clean and require no maintenance or re-configurations. They have a small footprint enabling Inline installation in any process line, avoiding any additional space or adapter requirement.
High stability and insensitive to mounting conditions: Any configuration possible
Rheonics SRV and SRD use unique patented co-axial resonator, in which two ends of the sensors twist in opposite directions, cancelling out reaction torques on their mounting and hence making them completely insensitive to mounting conditions and flow rates. Sensor element sits directly in the fluid, with no special housing or protective cage requirements.
Instant accurate readouts on production quality – Complete system overview and predictive control
Rheonics’ software is powerful, intuitive and convenient to use. Real-time process fluid can be monitored on the integrated IPC or an external computer. Multiple sensors spread across the plant are managed from a single dashboard. No effect of pressure pulsation from pumping on sensor operation or measurement accuracy. No effect of vibration.
Inline measurements, no bypass line is needed
Directly install the sensor in your process stream to do real time viscosity (and density) measurements. No bypass line is required: the sensor can be immersed in-line; flow rate and vibrations do not affect the measurement stability and accuracy.
Easy installation and no reconfigurations/recalibrations needed – zero maintenance/down-times
In the unlikely event of a damaged sensor, replace sensors without replacing or re-programming electronics. Drop-in replacements for both sensor and electronics without any firmware updates or calibration changes. Easy mounting. Available with standard and custom process connections like NPT, Tri-Clamp, DIN 11851, Flange, Varinline and other sanitary and hygienic connections. No special chambers. Easily removed for cleaning or inspection. SRV is also available with DIN11851 and tri-clamp connection for easy mounting and dis-mounting. SRV probes are hermetically sealed for Clean-in-place (CIP) and supports high pressure wash with IP69K M12 connectors.
Low power consumption
24V DC power supply with less than 0.1 A current draw during normal operation.
Fast response time and temperature compensated viscosity
Ultra-fast and robust electronics, combined with comprehensive computational models, make Rheonics devices one of the fastest, versatile and most accurate in the industry. SRV and SRD give real-time, accurate viscosity (and density for SRD) measurements every second and are not affected by flow rate variations!
Wide operational capabilities
Rheonics’ instruments are built to make measurements in the most challenging conditions.
SRV is available with the widest operational range in the market for inline process viscometer:
- Pressure range up to 5000 psi
- Temperature range from -40 up to 200°C
- Viscosity range: 0.5 cP up to 50,000 cP (and higher)
SRD: Single instrument, triple function – Viscosity, Temperature and Density
Rheonics’ SRD is a unique product that replaces three different instruments for viscosity, density and temperature measurements. It eliminates the difficulty of co-locating three different instruments and delivers extremely accurate and repeatable measurements in harshest of conditions.
Superior sensor design and technology
Sophisticated, patented electronics is the brain of these sensors. SRV and SRD are available with industry standard process connections like ¾” NPT, DIN 11851, Flange and Tri-clamp allowing operators to replace an existing temperature sensor in their process line with SRV/SRD giving highly valuable and actionable process fluid information like viscosity besides an accurate measurement of temperature using an in-build Pt1000 (DIN EN 60751 Class AA, A, B available).
Electronics built to fit your needs
Available in both a transmitter housing and a small-form factor DIN rail mount, the sensor electronics enables easy integration into process lines and inside equipment cabinets of machines.
Easy to integrate
Multiple Analog and digital communication methods implemented in the sensor electronics makes connecting to industrial PLC and control systems straightforward and simple.
Analog and Digital Communication Options
Optional Digital Communication Options
ATEX & IECEx Compliance
Rheonics offers intrinsically safe sensors certified by ATEX and IECEx for use in hazardous environments. These sensors comply with the essential health and safety requirements relating to the design and construction of equipment and protective systems intended for use in potentially explosive atmospheres.
The intrinsically safe and explosion proof certifications held by Rheonics also allows for customization of an existing sensor, allowing our customers to avoid the time and costs associated with identifying and testing an alternative. Custom sensors can be provided for applications that require one unit up to thousands of units; with lead-times of weeks versus months.
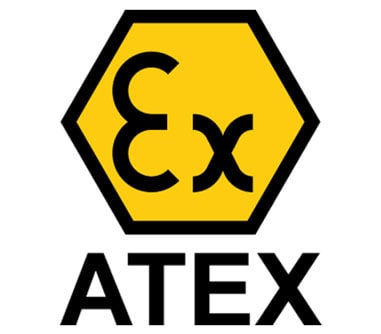
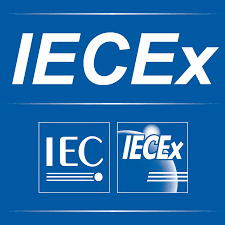
Rheonics Instrument Selection
Rheonics designs, manufactures and markets innovative fluid sensing and monitoring systems. Precision built in Switzerland, Rheonics’ in-line viscometers and density meters have the sensitivity demanded by the application and the reliability needed to survive in a harsh operating environment. Stable results – even under adverse flow conditions. No effect of pressure drop or flow rate. It is equally well suited to quality control measurements in the laboratory. No need to change any component or parameter to measure across full range.
Suggested product(s) for the Application
- Wide viscosity range – monitor the complete process
- Repeatable measurements in both Newtonian and non-Newtonian fluids, single phase and multi-phase fluids
- Hermetically sealed, all stainless steel 316L wetted parts
- Built in fluid temperature measurement
- Compact form-factor for simple installation in existing process lines
- Easy to clean, no maintenance or re-configurations needed
- Single instrument for process density, viscosity and temperature measurement
- Repeatable measurements in both newtonian and non-newtonian fluids, single phase and multi-phase fluids
- All metal (316L Stainless Steel) construction
- Built in fluid temperature measurement
- Compact form-factor for simple installation in existing pipes
- Easy to clean, no maintenance or re-configurations needed