Steps to System Integrators' Success
Rheonics works with System Integrators through a 4-step structured approach to ensure integration success for reliable factory operations.
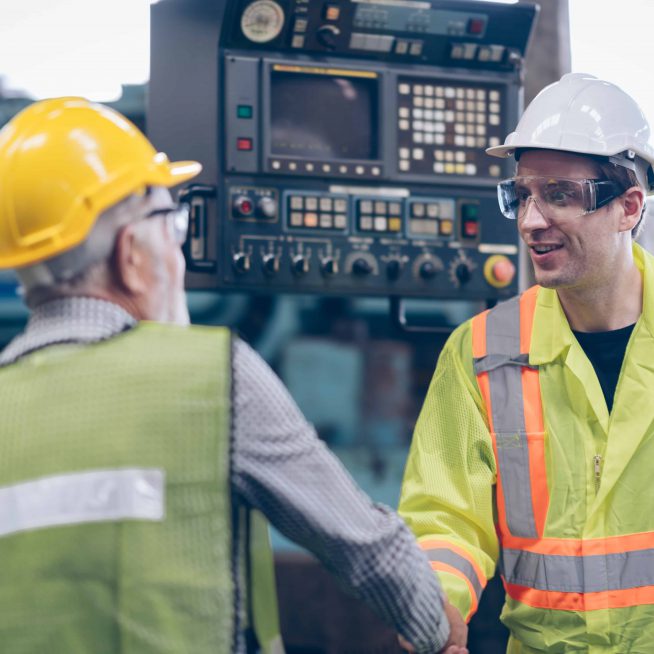
Rheonics works with machine builders and system integrators to empower factory engineers to equip their plants with digitalization, automation and IIoT technologies
As factory operators across industries strive for greater efficiency and profitability, they are accelerating adoption of Industry 4.0 and automation technologies. Through use of smart sensors, state of art controller and data analytics engines, they receive consistently accurate process measurement data in their applications. System integrator can help manufacturers improve their operational structure and equip them to use the latest automation technologies for tier factories and plants. Structural approach is necessary for the system integrators to minimize expenditure, implementation time, risks and to ensure end-users reap the maximum benefits of using the latest automation technologies.
![AdobeStock_245621373 (1) [Converted]](https://cdn.rheonics.com/wp-content/uploads/2021/01/AdobeStock_245621373-1-Converted.jpg)
Through our work with both end-users and system integrators, we have identified these 4 steps to achieve successful integration of automation technologies in most manufacturing processes:
Step 1: Identify
Identifying and understanding shortfalls of existing plant/facility operations through collaboration and co-innovation with a system integrator partner is the first step. Examples of common issues include:
- Gaps between production planning and actual performance
- Lack of experienced operators and staff
- Inconsistency in final product quality, even when using the same materials and workflow
- Customer complaints regarding quality, even when the products passes all criteria for delivery
- Need to maximize production while minimizing energy use and waste generation.
Benchmarking against best-in-market capabilities of similar facility requires thorough analysis and research. System integrators with domain knowledge and related experience can help in this analysis.
It’s advisable to use integrator with extensive expertise in your processes and plants, and to require the integrator to demonstrate where they have succeeded while working in situations similar to the end-user’s application.
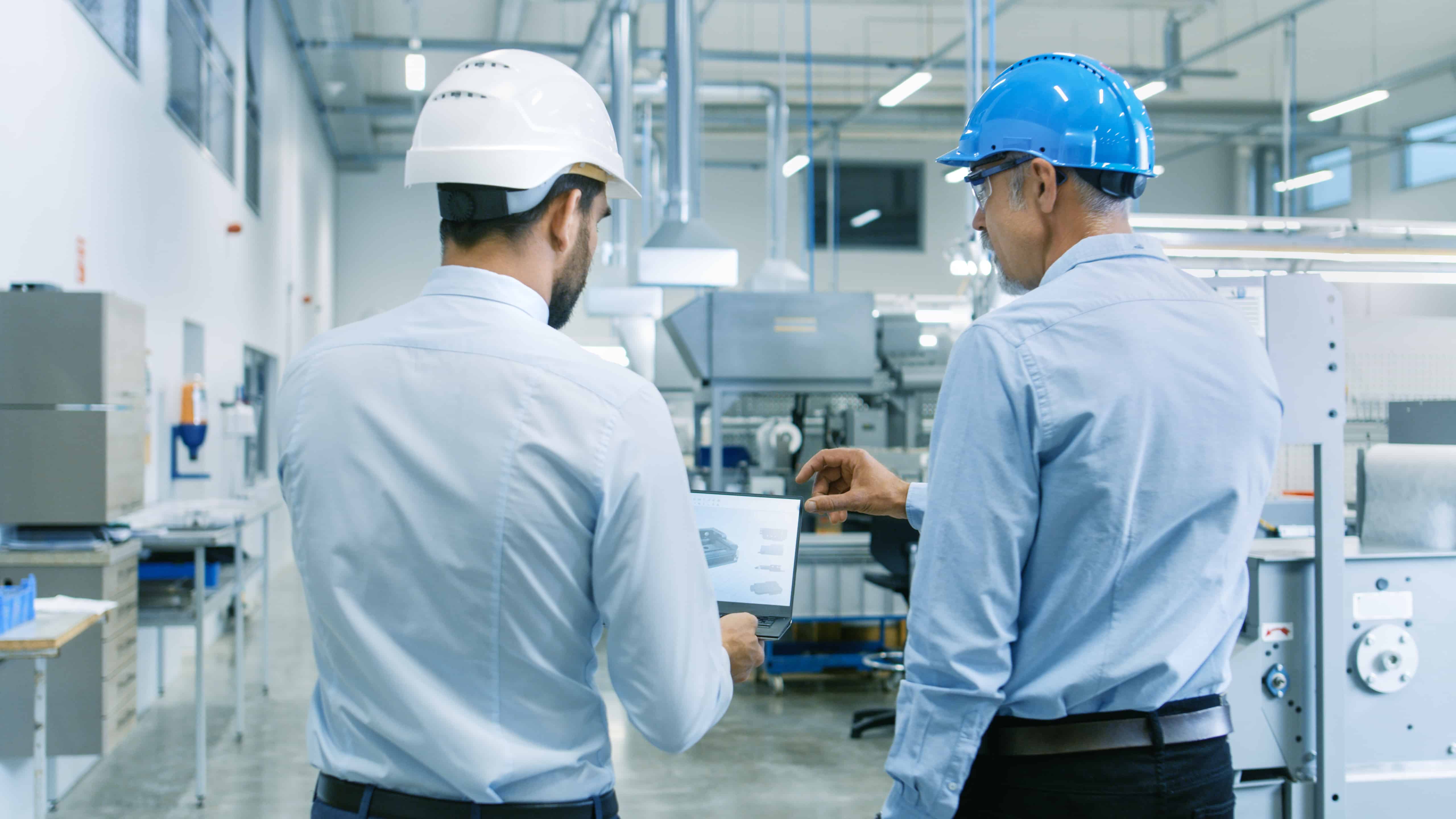
Step 2: Create and implement
Domain knowledge on the part of a system integrator partner again is critical because they must be able to understand and replicate their knowledge and implementation expertise to the desired case.
Here are some solutions often applied to solve process plant problems:
- Review and monitor production performance followed by feedback for continuous improvement
- Take into account the factory engineers’ requirements and implement solutions in consultation with the plant managers
- Integrate multiple process values influencing product quality into few Key Performance Indicator (KPI) to simplify monitoring by threshold management
- Comparative analysis of data across batches and clear communication of required recommendations and long term implications
- Support factory engineers’ long term production planning, maintenance and quality diagnosis
- Use advanced process control to optimize production
- Provide a clear view of product quality in real time by using inferred data.
System integrator’s experience in solving similar challenges elsewhere shortens the learning curve and prevents your company from making the same mistakes made by others when addressing these types of issues.
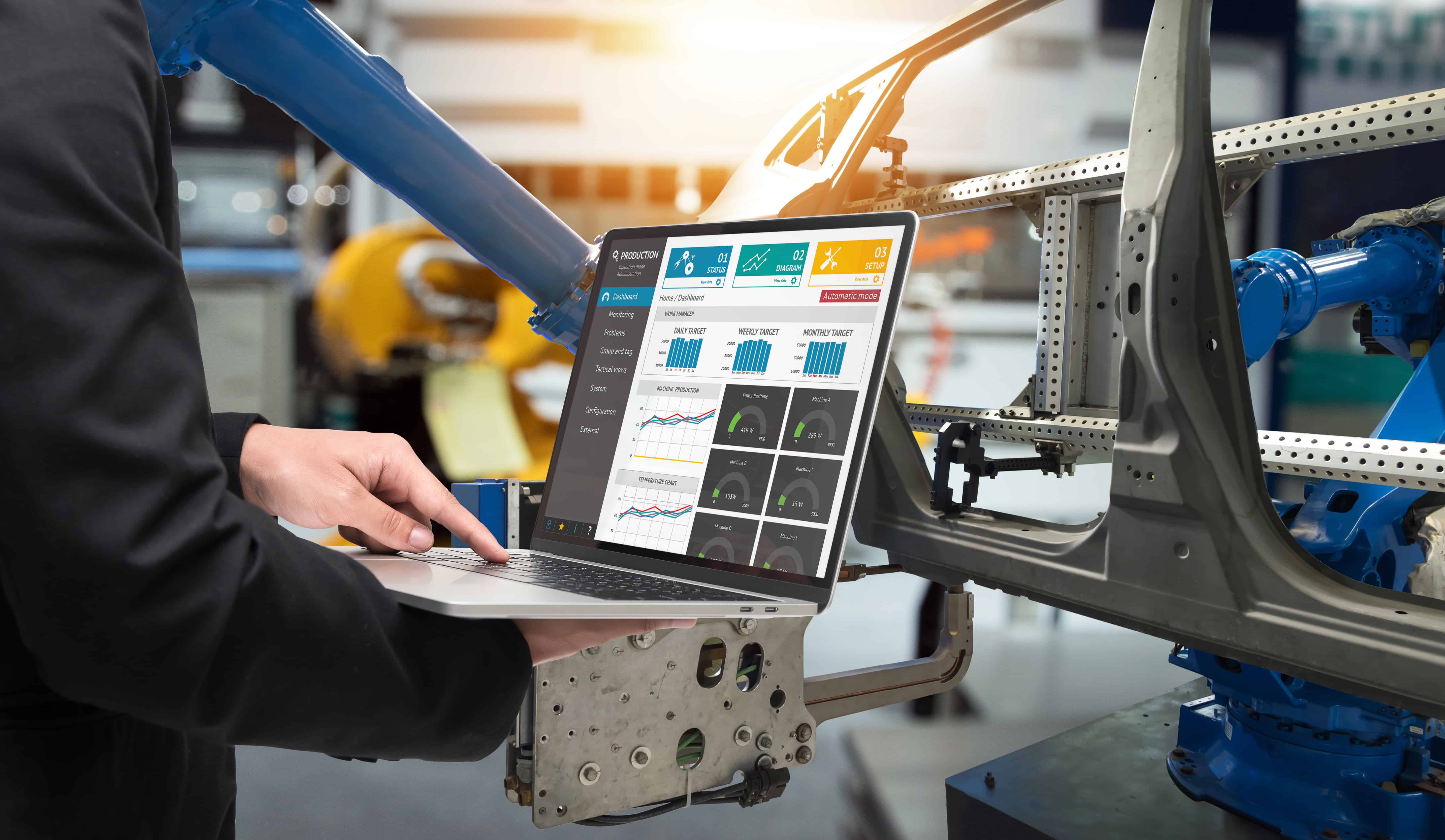
Step 3: Commissioning and Operations
Commissioning and post-installation support is essential, since it may not always be possible to troubleshoot and train the plant engineers in the short span of time during installation. System integrators need to support the factory engineers after commissioning to ensure the operational needs of end-users are completely fulfilled.
Production schedules are usually responsive to market demands and may not be uniform throughout the year. As production changes, issues can arise which were not evident after initial installation. To deal with any changes, the system integrator partner needs to be engaged for a few months after initial implementation to assure optimal operation, and to train the factory’s employees so they can execute the next step effectively.
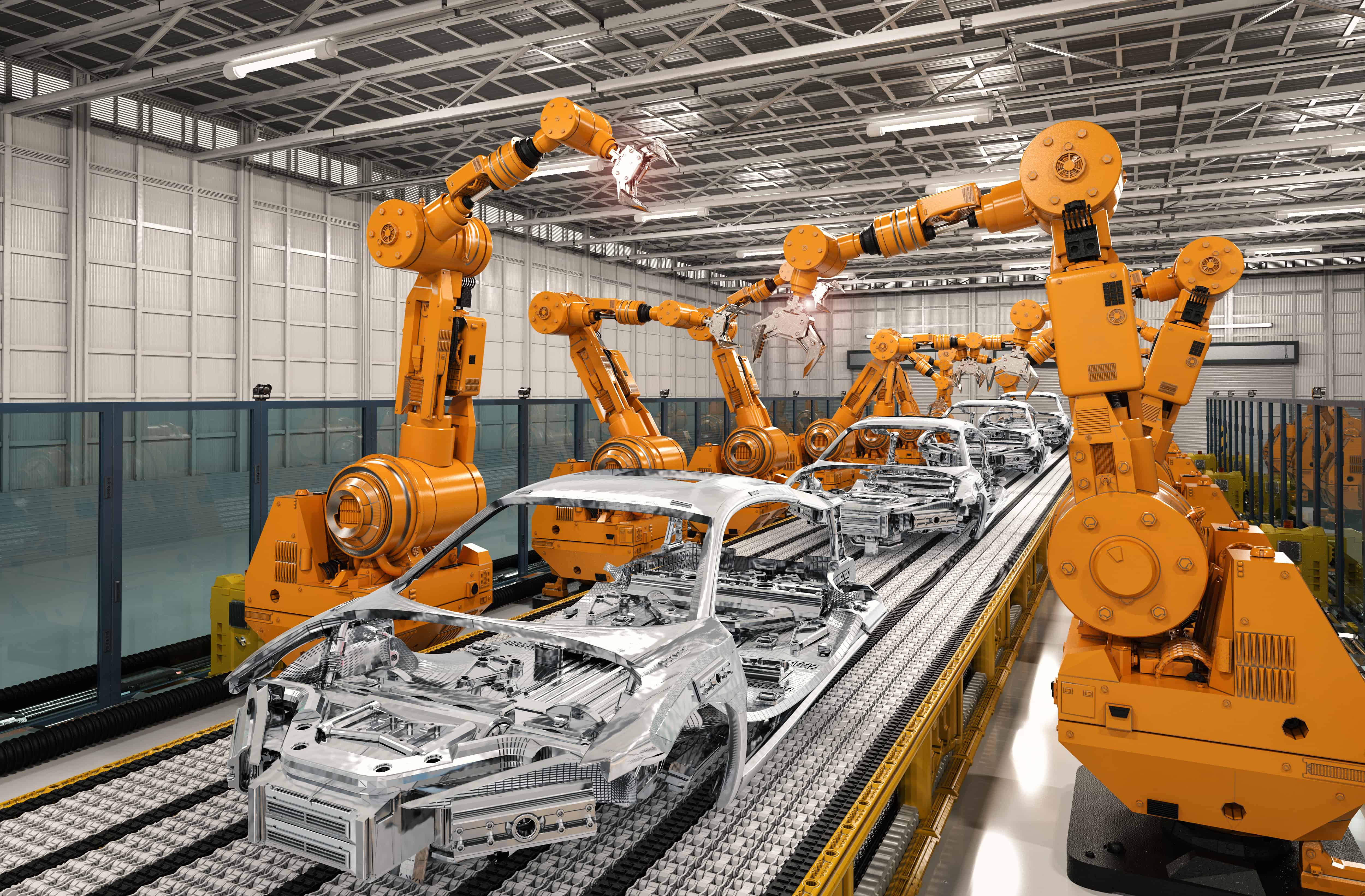
Step 4: Support, Sustain and improve
This step primarily is carried out by internal personnel, but the system integrator partner should remain available to provide assistance and maintain the value generation cycle.
The training program implemented as part of Step 3 is critical to sustaining success and making ongoing improvements. Plant personnel must be very familiar with the recently completed project so they can implement Step 4 correctly. Additionally, having an outside resource close at hand in the form of the system integrator used in Steps 1-3 is critical.
No matter how system integration services are labeled by suppliers, the most important factors for success of your project are always domain knowledge and industry experience. The more your system integrator knows about your processes and plants, the better the solution.
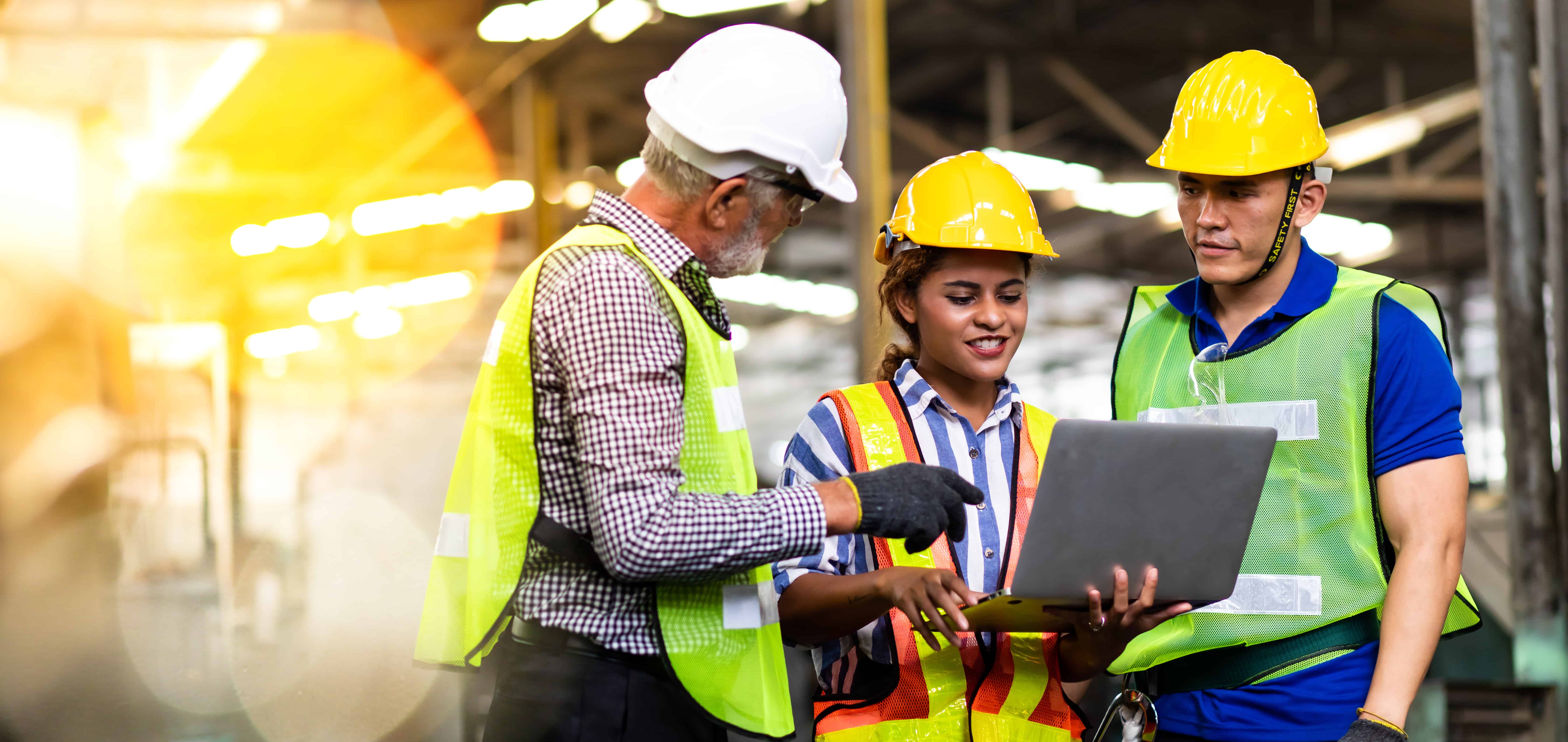
Rheonics looks forward to collaboration with System Integrators for delivering best and most advanced process instrumentation for the end users across different industries.
Manufacturers are constantly looking to reap full benefits of Industry 4.0, digitalization and factory automation, and we empower machine builders to achieve exactly what the factory users need for their processes. Rheonics provides a worldwide network of engineers, application experts and technical sales professionals to help you scope, select and troubleshoot automated solutions.
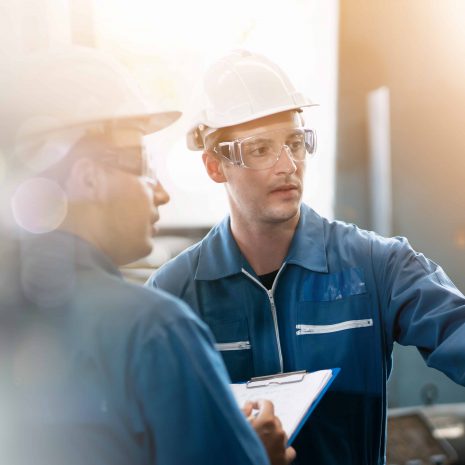
System Integrators
Rheonics solution are used in machines and integrated systems across broad range of industries.
Rheonics works with System Integrators and Machine Builders so they can deliver best-in-class density and viscosity management solutions to their customers. We make sure system integrators and end-users are provided up to date support and technical knowhow to ensure smooth integration & operation of density and viscosity management solutions.