Introduction
Emulsions are used in almost every aspect of daily lives. Their processing and development expands across many industries – chemicals, coating, food, cosmetics, adhesives, industrial fluids, pharmaceutical products, oil & gas.
What are emulsions?
It is a stable mixture of two immiscible liquids, one of which is uniformly dispersed in the other in the form of small droplets or particles. Emulsions are mixtures of fluids that are immiscible. Usually one fluid is present as small droplets in another phase. There are emulsions of oil in water, called oil-in-water emulsions (abbreviated as O/W), but also emulsions of water in oil (W/O). The droplet phase is called the dispersed phase, the surrounding phase the continuous phase. The interaction of its dispersed and continuous phases greatly influence the material properties of the emulsion. Emulsions can be characterized using a diverse range of analytical techniques. Some examples of common emulsions are:
- Milk is an emulsion of milk fat in an aqueous solution containing many different proteins, lactose and salts. In raw milk the fat is present in the form of milk fat globules, which are surrounded by a membrane. When this milk is homogenized in the factory, these globules are broken, and the fat is dispersed into smaller droplets, also stabilized by proteins.
- Margarine is an emulsion of water droplets in fat, stabilised by a packing of needle-like crystals of fat inside the continuous fat phase.
- Cream is a concentrated emulsion of milk fat in an aqueous phase; the concentration depends on the type of cream.
- Ice cream is a very complex product; amongst others it contains droplets of milk fat, but it also contains crystals of sugar, ice crystals and bubbles of air.
- Salad dressings are made by emulsifying vegetable oil in an aqueous mixture that contains vinegar. When made at home, this emulsion is rather unstable: the droplets coalesce relatively quickly, so one has to shake it before use. Commercial variants are usually stabilized by other components.
- Mayonnaise is a very concentrated emulsion of oil droplets in water, stabilised by proteins from egg yolk. The emulsion is so concentrated (70–80 vol.%) that the oil droplets are squeezed together. This squeezing together causes the nice consistency of mayonnaise.
- Egg yolk is an emulsion of egg fat (and cholesterol) in an aqueous solution, stabilised by a mixture of phospholipids.
- Food products. Salad dressings, gravies and other sauces, whipped dessert toppings, peanut butter, and ice cream are also examples of emulsions of various edible fats and oils. In addition to affecting the physical form of food products, emulsions impact taste because emulsified oils coat the tongue, imparting “mouth-feel.”
- Waterborne paints and coatings are usually emulsions of polymer-based binder particles. They are made by making an emulsion of droplets of monomers in water, after which the monomers are polymerized to form solid particles. When applied, the water and possibly other solvents evaporate, and the binder particles fuse to form a solid layer.
- Bitumen, a heavy fraction produced in the refining of petroleum, is usually too viscous to be applied directly. Therefore, bitumen is emulsified in water at high The resulting O/W emulsions have a much lower viscosity, and therefore are easier to apply. When applied (on the road or on a roof), the emulsion breaks, and the bitumen particles fuse into one layer.
- Medicines & Drugs. Starch/Gelatin Blend Microparticles are prepared by the water-in-oil emulsion solvent diffusion method. The in vitro drug release content significantly depends on the starch blend ratio and the crosslinker ratio. Starch/gelatin blend microparticles should be a useful controlled release delivery carrier for water-soluble drugs. In the pharmaceutical industry, emulsions are used to make medicines more palatable, to improve effectiveness by controlling dosage of active ingredients, delayed release drugs and to provide improved aesthetics for topical drugs such as ointments.
- Oils and hydrocarbons. Two third parts of the worldwide crude oils are produced in an emulsified way; these emulsions are mainly of the water-in-oil type due to the production processes.
- Insecticides and pesticides. In the agricultural industry, emulsions are used as delivery vehicles for insecticides, fungicides and pesticides and are applied usually by spraying through mechanical equipment.
- In cosmetics, emulsions are the delivery vehicle for many hair and skin conditioning agents. Anionic and non-ionic emulsions are used to deliver various oils and waxes which provide moisturization, smoothness and softness to hair and skin. Other examples are face creams, body lotions, shampoos, shower gels, toothpastes, soaps and fragrances.
- Lubricants, slurries, additives, machine oils, polymer emulsions, glues, starch solutions, mineral filler slurries, textile emulsions, submicron emulsions and silicone emulsions.
- Battery Materials. Water-based binders for batteries are developed by utilizing advanced polymer technologies, to enable the formation of negative electrodes in lithium-ion secondary batteries and nickel-hydrogen secondary batteries. Compared to conventional battery binders (PVDF), these binders have excellent binding properties, electrolyte resistance and cycle properties.
Polyelectrolyte solutions (Flocculants) for waste water treatment. Polyacrylamides are very high gramme-molecular weight polymers used as flocculants. These polymers are mainly available as a powder or an emulsion. They can be anionic or cationic. Some of these products exist in the form of highly viscous solutions (5,000 to 10,000 centipoises) that can be pumped as supplied with secondary dilution at the feeding pump delivery.
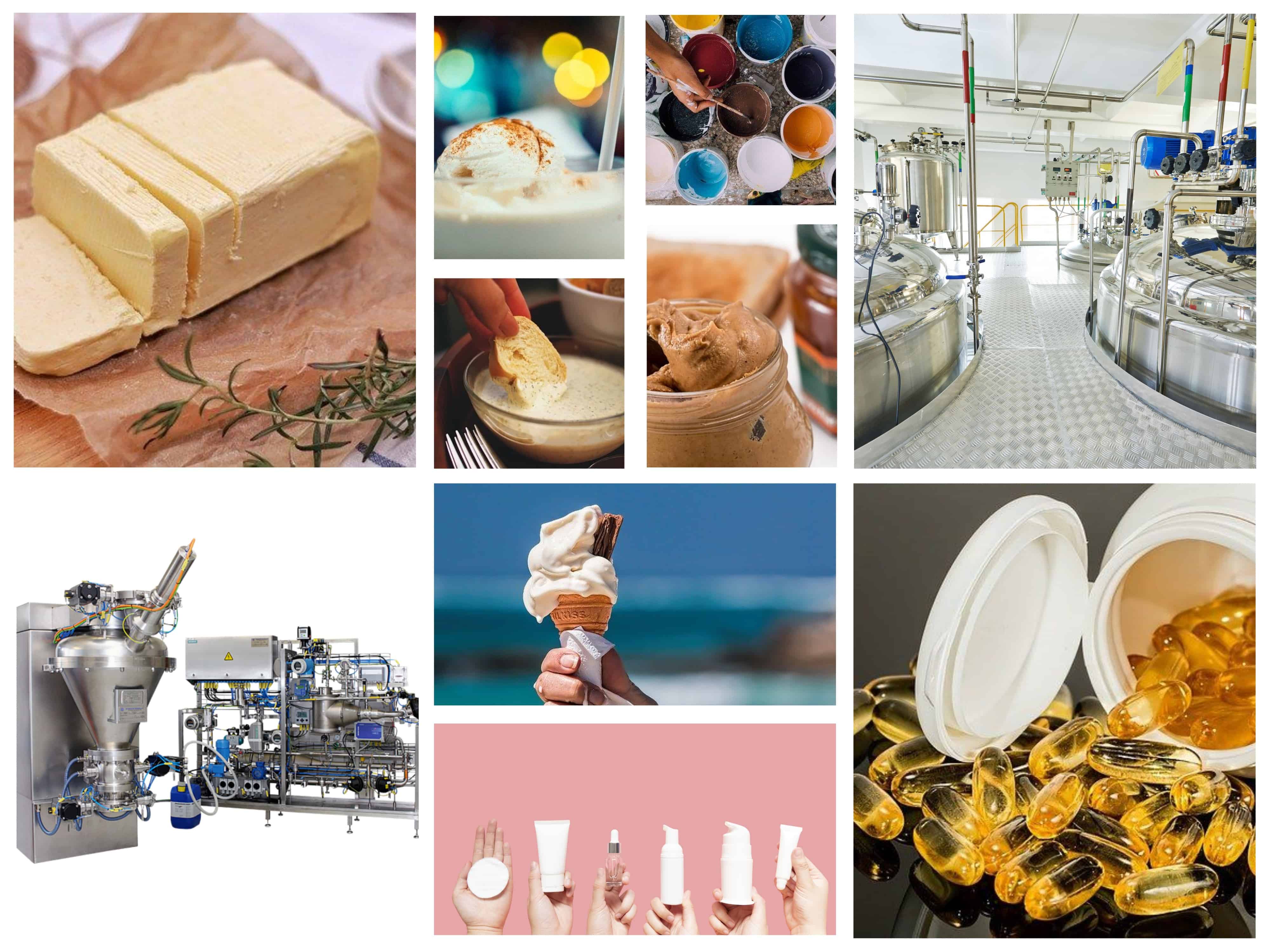
Application of emulsions
Emulsions are widely used as precursors and end-products. This is due to infinite number of possible combinations of emulsions systems. The task of fully characterizing their structure is important step to their commercialization. New emulsion types are constantly under development. A recent advancement is the micro-emulsion, a special type of emulsion characterized by extremely small particle size, transparency and enhanced stability as compared to conventional systems. As science continues to respond to industry needs, more new and unconventional emulsions combinations are being developed rapidly.
Formulation & testing of emulsions
The interfacial tension forces try to keep the two phases separate, the goal in preparing emulsions is to reduce the interfacial tension to promote a more intimate blending of the two phases. This is accomplished in two primary ways – by reducing the viscosity of the internal phase and through the use of chemical additives. Heating the product is the simplest way to achieve a viscosity reduction because most liquids become less viscous when they are heated. The viscosity decrease is usually accompanied by a decrease in the interfacial tension, leading to better emulsification.
A stable emulsion of two immiscible liquids is rare, and often some type of chemical assistance is required. Usually, a chemical that is active at the interface between the two phases is used. Such an additive is referred to as an emulsifier or a surfactant (this stands for surface-active agent). The commercial preparation of most emulsions involves the application of both a chemical emulsifier and a mechanical device, such as a colloid mill or in-line mixer, to produce a dispersed phase with a droplet size small enough to result in a finished product with the desired properties.
Characterizing emulsion properties and relevance
Emulsion stability is critical in their processing and formulation. Emulsions are often perceived as something simple, macroscale that can be seen, felt, and even tasted but in reality, it is the nanoscale properties of the droplets dispersed in an emulsion that are the main contributors to the emulsion’s bulk properties. Specifically, the size and charge of the emulsified droplets directly affect stability, taste, safety, look and feel, and function. Thus, it is of utmost importance to be able to accurately and quickly measure these properties of emulsions.
These properties are highly relevant to emulsion processing, and some of these properties are interlinked:
- Mean particle size
- Particle size distribution
- Internal-phase viscosity
- Continuous-phase viscosity
- Emulsifier level
- Oil-phase concentration
- Continuous-phase pH
- Emulsion optical properties
The concentrations in question are relevant because they influence the type and stability of the final emulsion. In general, the phase that is present in the greater concentration will tend to be the continuous phase.
Emulsion processing methods – how are emulsions made?
To create an emulsion, the ingredients are first combined to form a crude premix emulsion. This premix can be created in several ways:
- The emulsifier is dissolved in the continuous phase, and then the internal phase is slowly added with good agitation (most common method).
- The emulsifier can be dissolved in the internal phase before slowly adding that blend to the continuous phase under agitation.
- The emulsifier can be dissolved in the internal phase before slowly adding the continuous phase to form the premix. This means usually produces the best results but it requires a lot of time and vigorous mixing because it involves bringing a preliminary W/O emulsion through the inversion stage to eventually form the desired O/W type.
- Another method is using a mix-order control method specifically developed. This technique permits the injection of the product components directly into the product stream at different steps along a multistage mixing chamber.
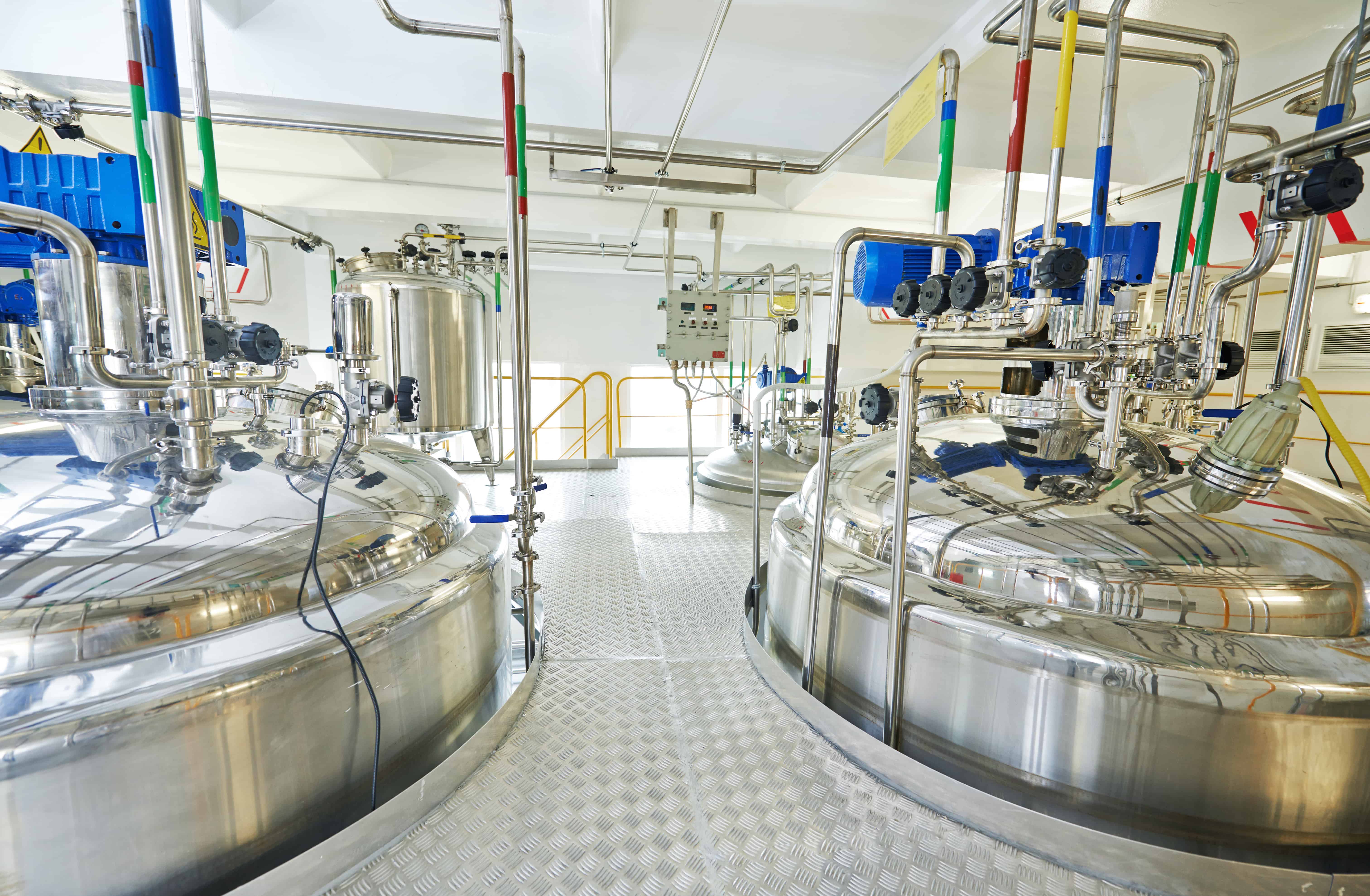
The first method produces good results if a mechanical shearing device such as a colloid mill or an in-line mixer is used in the finishing step, the first premix method usually produces good results.
Having assured a well-formulated and stable premix, the colloid mill or in-line mixer can finish the job of emulsifying. The zone of intense hydraulic shear forces within the colloid mill or in-line mixer head breaks the internal phase droplets apart and creates the small particle size that is generally desired. If sufficient emulsifier is used for the enormous increase in surface area generated by this process, the final product should exhibit enhanced stability.
In some cases, a good emulsion can be produced with a moderate level of applied mechanical energy, but a poor emulsion results if the energy level is increased. The increase in applied energy causes additional particle size reduction, but without adjustment to the emulsifier concentration, the smaller particles are not stable. This is known as overworking the emulsion. Processing equipment, such as in-line mixers that offer Shear Zone Management (multiple, customizable, high-shear action zones) and Mix Order Control (adaptable mixing chambers to introduce process material at different positions in the shear zone), provides critical advantages for commercial emulsion development and processing.
Reduction in dispersed phase viscosity enhances emulsion formation, but what effects can be expected from changes in the continuous-phase viscosity? A reduction in viscosity should lead to easier emulsion formation because of a reduced interfacial tension. While this is true, another factor must be considered. An increase in continuous-phase viscosity will greatly improve emulsion stability by retarding the inevitable rise of the oil droplets to the top. In most circumstances, this more stable finished product is the overriding concern, and a decision to gain this advantage at the expense of overcoming a higher interfacial tension in the mechanical processing step is gladly accepted.
Monitoring and controlling the viscosity of the emulsification process becomes critical to achieving a repeatable, efficient process.
Quality Control of emulsion processing and application
With the emulsions’ physical properties, the information to verify the results with a reliable quality control (QC) process is extremely essential to ensure the dispersing & homogenizing processes are producing reliable results across batches.
Creaming is the phenomenon in which the dispersed phase separates out, forming a layer on the top of the continuous phase. It is notable that in creaming, the dispersed phase remains in globules state so that it can be re-dispersed on shaking. Creaming can be minimized if the viscosity of the continuous phase is increased. The easiest method is to put the emulsion on a shelf and observe it for creaming over time. A minimum acceptable shelf life can be a QC specification. Unfortunately, the price for this simplicity is that a poor batch might not be discovered until after the product reaches the customer. To overcome this, the creaming process can be accelerated by heating the emulsion or by centrifuging it. These results must then be related to a corresponding static creaming rate at room temperature. All these creaming-rate measurements are simple, but they are not precise.
Various factors can affect emulsion stability. Common issues with emulsion instabilities are coalescence, flocculation, creaming & breaking. Therefore, it becomes important to monitor its properties in real-time and make adaptive adjustments:
- Emulsifier concentration
- Oil/Water ratio
- Stirring intensity
- Mixing temperature
- Mixing time
Given that the viscosity of the emulsion is not a static parameter but is varying due to process requirement as well as from the processing itself, it is crucial to monitor and control viscosity during the complete processing cycle.
How can real-time viscosity monitoring ensure emulsion quality?
The need to characterize emulsion properties are critical in formulation, scale-up, processing and testing of emulsions as well as for the design and development of equipment used in these processes.
Viscosity is key to finding a way to measure emulsion quality so that some degree of consistency from one batch to another can be maintained.
- Conventional production methods for emulsions are based on quasi continuous processes
- Continuous mixing process consists of controlled dosing of components, adapting and adjusting to the fluid conditions in real-time which can be affected by multiple parameters
Increase overall throughput and efficiency of homogenization processes
Ultra-high shear rotor/stator systems speed up cycle time by reducing the number of passes required through a high-pressure homogenizer, an inherently low-throughput, high-energy device. Since homogenizers are also generally maintenance-intensive, an efficient ‘pre-mixer’ generates significant savings in the overall cost of production. In certain applications, ultra-high shear mixers even offer a viable alternative to homogenizers.
The sensitive chemistry of the emulsions means that time and cost savings cannot come at the expense of quality, which needs to remain very high. Monitoring & controlling viscosity to optimise the batch processes ensures consistency, quality and significant material cost savings and accurate end point detection/stability estimation of the mixing process for a particular batch. Process control and traceability of the continuous mixing process can be improved with inline monitoring and control of viscosity, which also ensure high level of product consistency, repeatability in the processes and significantly lower reject rates.
Other uses of viscosity measurements include using the data provided by the equipment in formulations and research and development of formulations to exhibit target properties and for an effective characterization. In addition, for pharmaceuticals and food manufacturing, traceability of the process is important for regulatory bodies and inline measurements achieve complete track and trace of the products across the production cycle.
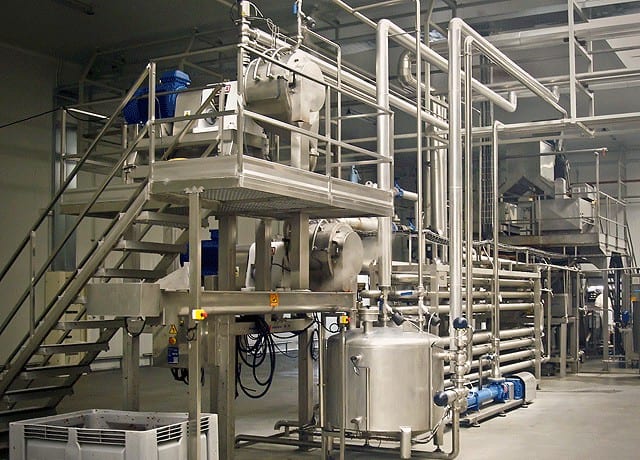
Rheonics’ Solutions for Quality control and assurance of Emulsion processes
Automated in-line viscosity measurement and control is crucial to control the viscosity during emulsion processing and ensure critical characteristics are in full compliance with requirements across multiple batches, without having to rely on offline measurement methods and sample taking techniques. Rheonics offers the following solutions for process control and optimisation in the emulsion formulation, processing, scale-up and testing.
Viscosity & Density Meters
- In-line Viscosity measurements: Rheonics’ SRV is a is a wide range, in-line viscosity measurement device capable of detecting viscosity changes within any process stream in real time.
- In-line Viscosity and Density measurements: Rheonics’ SRD is an in-line simultaneous density and viscosity measurement instrument. If density measurement is important for your operations, SRD is the best sensor to cater to your needs, with operational capabilities similar to the SRV along with accurate density measurements.
Integrated, turnkey emulsions quality management
Rheonics offers an integrated turn-key solution for emulsion production quality management made of:
- In-line Viscosity measurements: Rheonics’ SRV – a wide range, in-line viscosity measurement device with in-built fluid temperature measurement
- Rheonics Process Monitor: an advanced predictive tracking controller to monitor and control in real-time variations of process conditions
- Rheonics RheoPulse with automatic dosing: A Level 4 autonomous system that ensures no compromise with set limits of viscosity and automatically activates by-pass valves or pumps to adaptively dose mixture components
The SRV sensor is located in-line so it continuously measures the viscosity (and density in case of SRD). Alerts can be configured to notify operator of necessary action or the entire management process can be fully automated with RPTC (Rheonics Predictive Tracking Controller). Using an SRV in an emulsion preparation process line, results in improved productivity, profit margins and achieves regulatory conformance. Rheonics sensors have a compact form factor for simple OEM and retrofit installation. They require zero maintenance or re-configurations. The sensors offer accurate, repeatable results no matter how or where they are mounted, without any need for special chambers, rubber seals or mechanical protection. Using no consumables and not requiring re-calibration, SRV and SRD are extremely easy to operate resulting in extremely low lifetime running costs.
Once the process environment is established, there is usually little effort required to maintain the integrity consistency of the systems – operators can rely on the tight control with Rheonics emulsions production quality management solution.
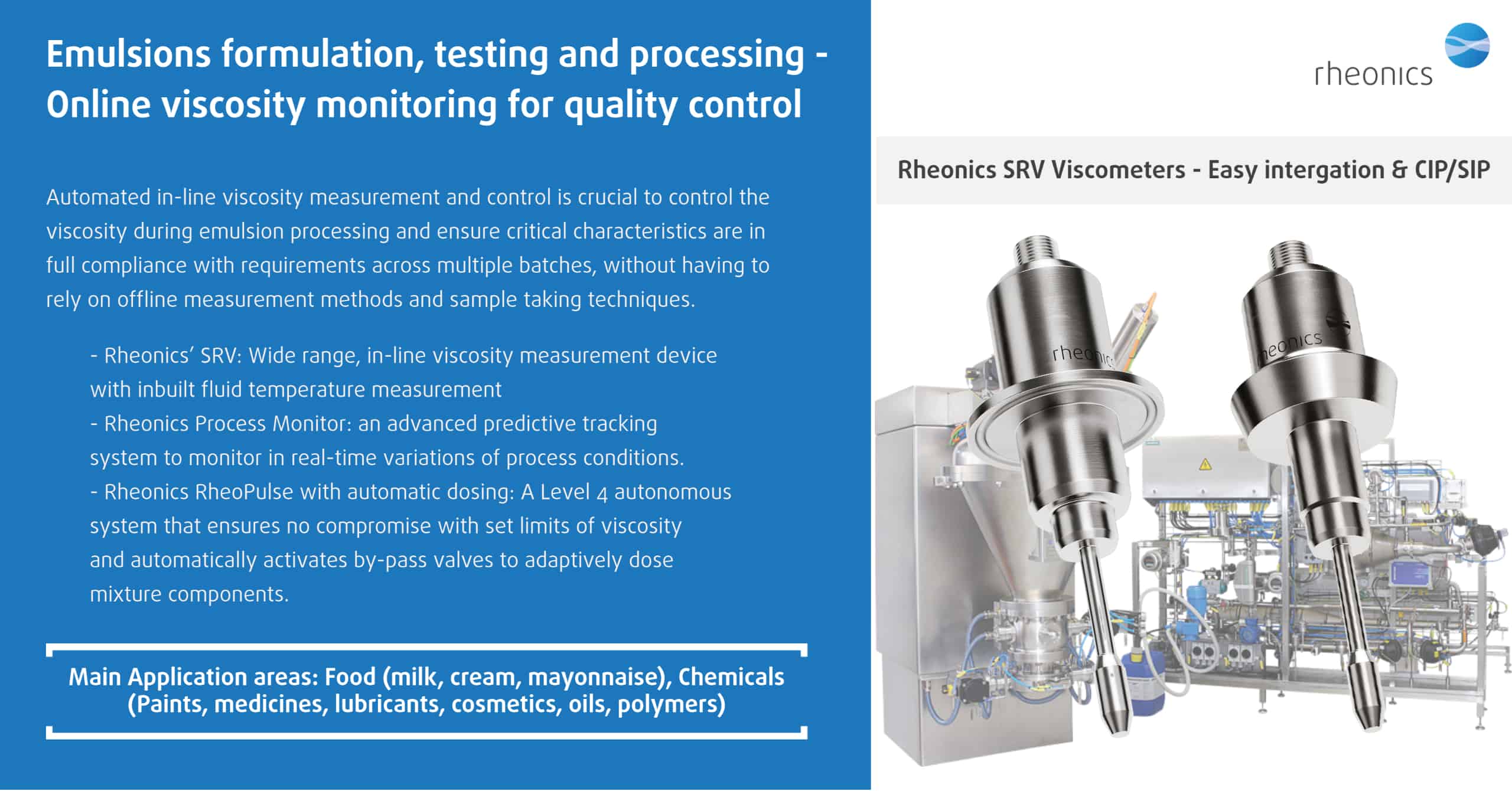
Rheonics' Advantage
Compact form factor, no moving parts and require no maintenance
Rheonics’ SRV and SRD have a very small form factor for simple OEM and retrofit installation. They enable easy integration in any process stream. They are easy to clean and require no maintenance or re-configurations. They have a small footprint enabling Inline installation in any process line, avoiding any additional space or adapter requirement.
Hygienic, sanitary design
Rheonics SRV and SRD are available in tri-clamp and DIN 11851 connections besides custom process connections.
Both SRV & SRD conform to Food Contact Compliance requirements according to US FDA and EU regulations.
High stability and insensitive to mounting conditions: Any configuration possible
Rheonics SRV and SRD use unique patented co-axial resonator, in which two ends of the sensors twist in opposite directions, cancelling out reaction torques on their mounting and hence making them completely insensitive to mounting conditions and flow rates. Sensor element sits directly in the fluid, with no special housing or protective cage requirements.
Instant accurate readouts on production quality – Complete system overview and predictive control
Rheonics’ RheoPulse software is powerful, intuitive and convenient to use. Real-time process fluid can be monitored on the integrated IPC or an external computer. Multiple sensors spread across the plant are managed from a single dashboard. No effect of pressure pulsation from pumping on sensor operation or measurement accuracy. No effect of vibration.
Inline measurements, no bypass line is needed
Directly install the sensor in your process stream to do real time viscosity (and density) measurements. No bypass line is required: the sensor can be immersed in-line; flow rate and vibrations do not affect the measurement stability and accuracy.
Easy installation and no reconfigurations/recalibrations needed – zero maintenance/down-times
In the unlikely event of a damaged sensor, replace sensors without replacing or re-programming electronics. Drop-in replacements for both sensor and electronics without any firmware updates or calibration changes. Easy mounting. Available with standard and custom process connections like NPT, Tri-Clamp, DIN 11851, Flange, Varinline and other sanitary and hygienic connections. No special chambers. Easily removed for cleaning or inspection. SRV is also available with DIN11851 and tri-clamp connection for easy mounting and dis-mounting. SRV probes are hermetically sealed for Clean-in-place (CIP) and supports high pressure wash with IP69K M12 connectors.
Low power consumption
24V DC power supply with less than 0.1 A current draw during normal operation.
Fast response time and temperature compensated viscosity
Ultra-fast and robust electronics, combined with comprehensive computational models, make Rheonics devices one of the fastest, versatile and most accurate in the industry. SRV and SRD give real-time, accurate viscosity (and density for SRD) measurements every second and are not affected by flow rate variations!
Wide operational capabilities
Rheonics’ instruments are built to make measurements in the most challenging conditions.
SRV is available with the widest operational range in the market for inline process viscometer:
- Pressure range up to 5000 psi
- Temperature range from -40 up to 200°C
- Viscosity range: 0.5 cP up to 50,000 cP (and higher)
SRD: Single instrument, triple function – Viscosity, Temperature and Density
Rheonics’ SRD is a unique product that replaces three different instruments for viscosity, density and temperature measurements. It eliminates the difficulty of co-locating three different instruments and delivers extremely accurate and repeatable measurements in harshest of conditions.
Manage emulsion preparation processes more efficiently, cut down costs and enhance productivity
Integrate an SRV in the process line and ensure consistency over the years. SRV constantly monitors and controls viscosity (and density in case of SRD) and activates valves adaptively for dosing the mixture constituents. Optimise the process with an SRV and experience fewer shutdowns, lower energy consumption, lesser non-compliances and material cost savings. And at the end of it all, it contributes to a better bottom line and a better environment!
Clean in place (CIP) and Sterilization in place (SIP)
SRV (and SRD) monitors the cleanup of the fluid lines by monitoring the viscosity (and density) of the cleaner/solvent during the cleaning phase. Any small residue is detected by the sensor, enabling the operator to decide when the line is clean/fit for purpose. Alternatively, SRV (and SRD) provides information to the automated cleaning system to ensure full and repeatable cleaning between runs, thus ensuring full compliance to sanitary standards of food manufacturing facilities.
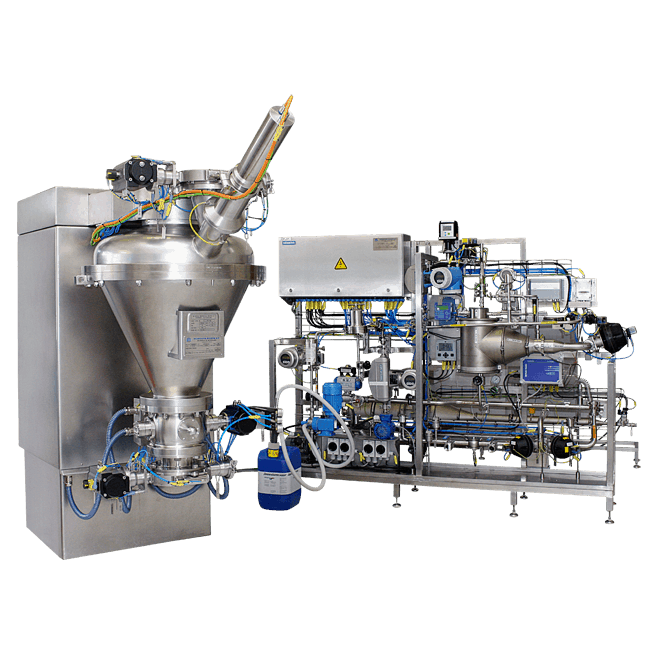
Superior sensor design and technology
Sophisticated, patented electronics is the brain of these sensors. SRV and SRD are available with industry standard process connections like ¾” NPT, DIN 11851, Flange and Tri-clamp allowing operators to replace an existing temperature sensor in their process line with SRV/SRD giving highly valuable and actionable process fluid information like viscosity besides an accurate measurement of temperature using an in-build Pt1000 (DIN EN 60751 Class AA, A, B available).
Electronics built to fit your needs
Available in both a transmitter housing and a small-form factor DIN rail mount, the sensor electronics enables easy integration into process lines and inside equipment cabinets of machines.
Easy to integrate
Multiple Analog and digital communication methods implemented in the sensor electronics makes connecting to industrial PLC and control systems straightforward and simple.
Analog and Digital Communication Options
Optional Digital Communication Options
ATEX & IECEx Compliance
Rheonics offers intrinsically safe sensors certified by ATEX and IECEx for use in hazardous environments. These sensors comply with the essential health and safety requirements relating to the design and construction of equipment and protective systems intended for use in potentially explosive atmospheres.
The intrinsically safe and explosion proof certifications held by Rheonics also allows for customization of an existing sensor, allowing our customers to avoid the time and costs associated with identifying and testing an alternative. Custom sensors can be provided for applications that require one unit up to thousands of units; with lead-times of weeks versus months.
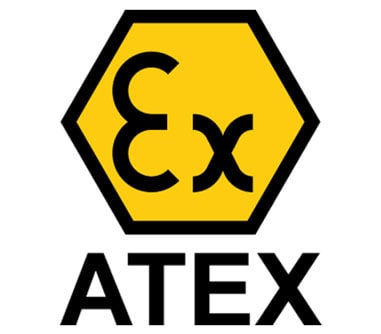
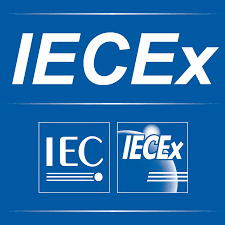
Implementation
Directly install the sensor in your process stream to do real-time viscosity and density measurements. No bypass line is required: the sensor can be immersed in-line; flow rate and vibrations do not affect the measurement stability and accuracy. Optimize mixing performance by providing repeated, consecutive, and consistent tests on the fluid.
In-line Quality control locations
- In tanks
- In the connecting pipes between various processing containers
Instruments/Sensors
SRV Viscometer OR an SRD for additional density
Rheonics Instrument Selection
Rheonics designs, manufactures and markets innovative fluid sensing and monitoring systems. Precision built in Switzerland, Rheonics’ in-line viscometers and density meters have the sensitivity demanded by the application and the reliability needed to survive in a harsh operating environment. Stable results – even under adverse flow conditions. No effect of pressure drop or flow rate. It is equally well suited to quality control measurements in the laboratory. No need to change any component or parameter to measure across full range.
Suggested product(s) for the Application
- Wide viscosity range – monitor the complete process
- Repeatable measurements in both Newtonian and non-Newtonian fluids, single phase and multi-phase fluids
- Hermetically sealed, all stainless steel 316L wetted parts
- Built in fluid temperature measurement
- Compact form-factor for simple installation in existing process lines
- Easy to clean, no maintenance or re-configurations needed
- Single instrument for process density, viscosity and temperature measurement
- Repeatable measurements in both newtonian and non-newtonian fluids, single phase and multi-phase fluids
- All metal (316L Stainless Steel) construction
- Built in fluid temperature measurement
- Compact form-factor for simple installation in existing pipes
- Easy to clean, no maintenance or re-configurations needed