Application
Customer application of the Rheonics SRV sensor to measure batter viscosity in a batter mixing and coating system is an established and widely used method to ensure batter consistency.
Customers have traditionally relied on rotational viscometers to measure viscosity of batter in their labs. This has created a significant volume of data that customers desire to use to establish batter viscosity in their process lines using the SRV.
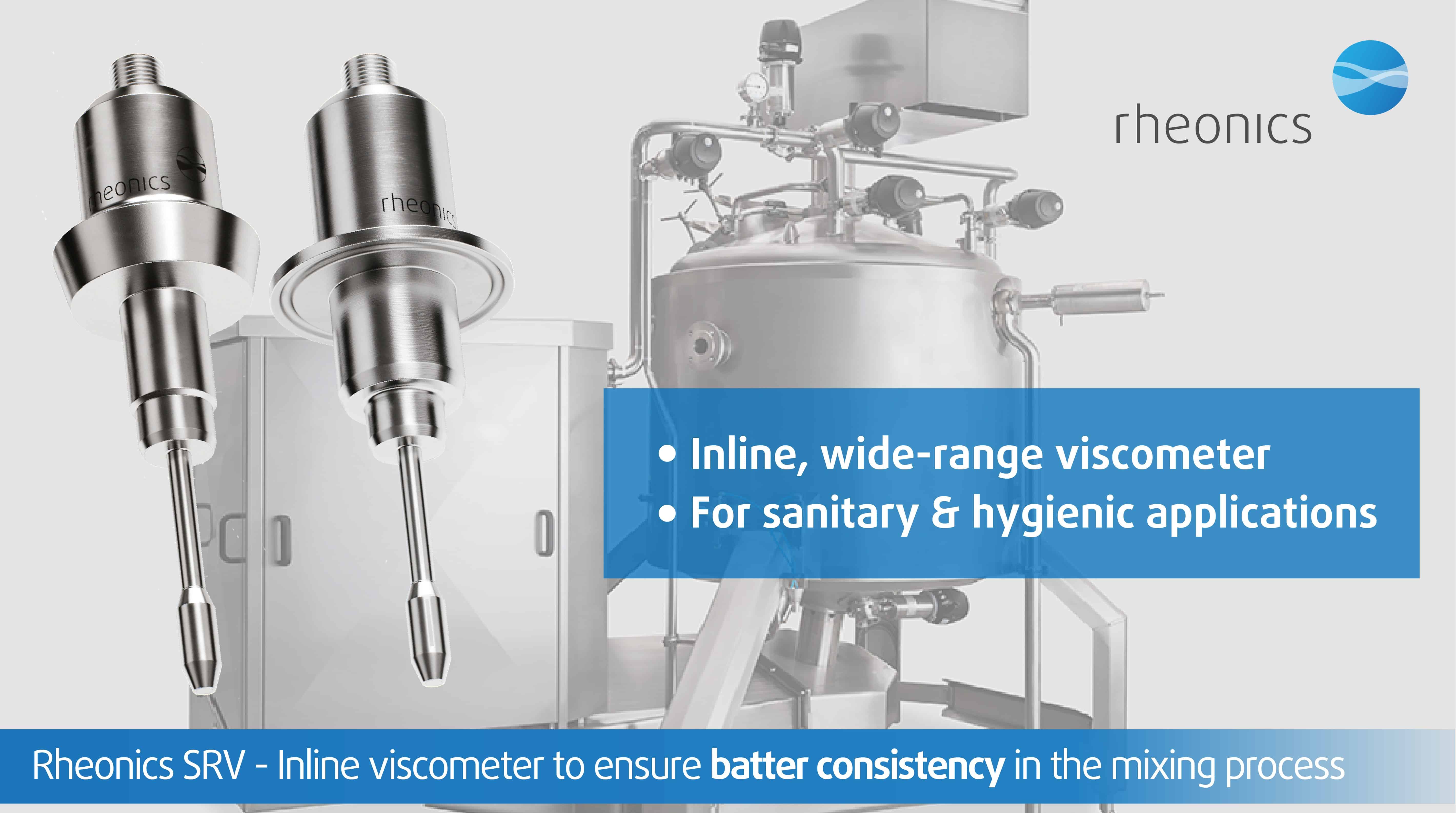
Purpose of the case study
To investigate if a correlation is possible between Rotational viscometer measurements and SRV inline measurements.
Rotational Viscometer Measurements
Brookfield LV is a commonly used laboratory rotational viscometer in food applications. Brookfield supplies following information about spindles and ranges, the appropriate spindle needs to be deployed for the measurements depending on the viscosity range.
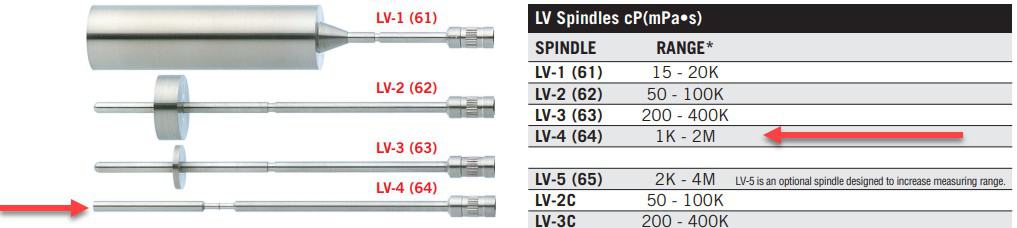
Fig.1. Brookfield information about spindles and applicable viscosity
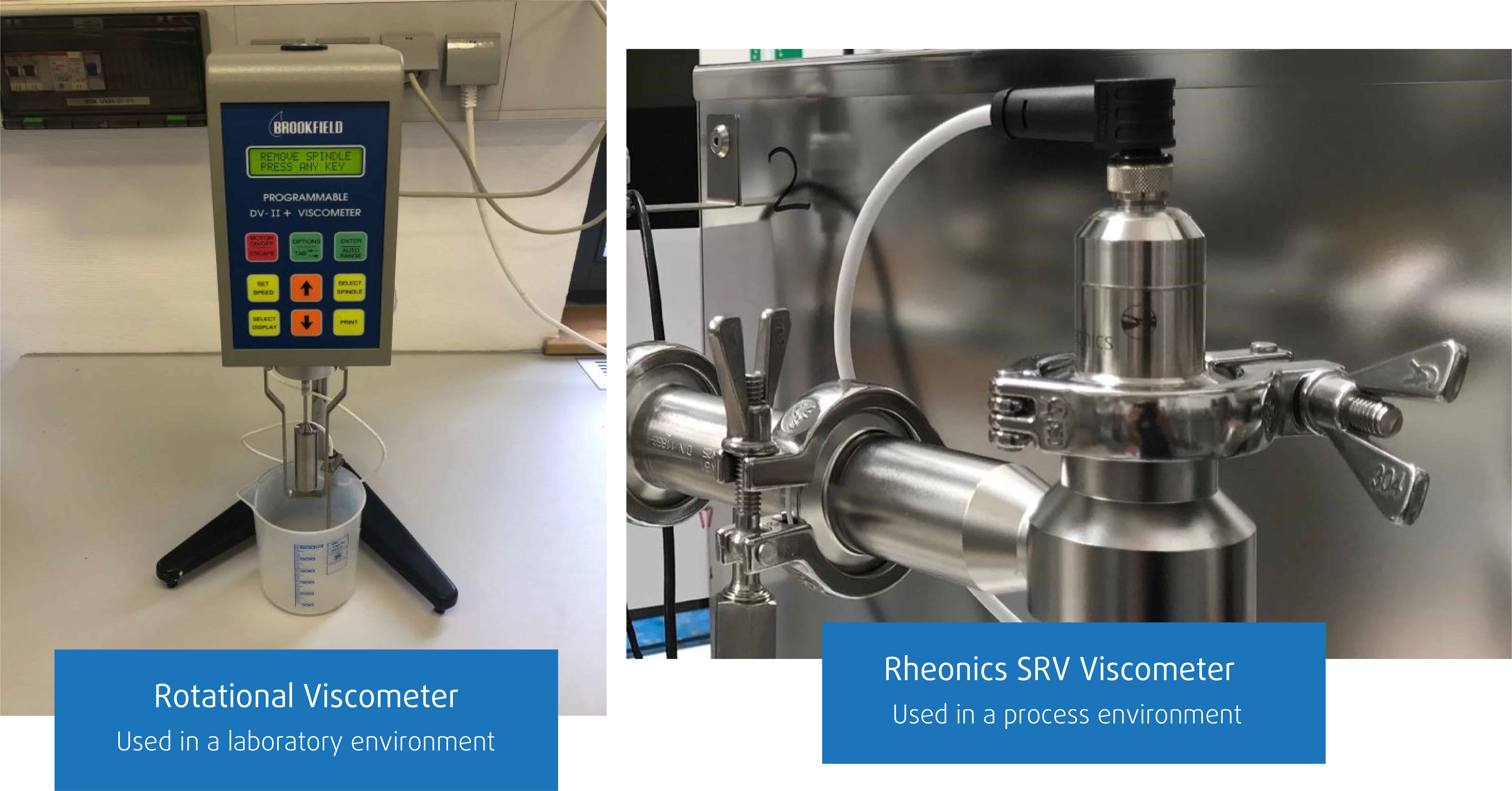
Fig.2. Applicability of the Rheonics SRV viscometer in process conditions
Batter mixing & viscosity measurements
A mixture of flour and a commercial batter mix (Knorr Panier-Mischung) was added to water with continuous stirring with an impeller mixer until a homogeneous and moderately viscous mixture was obtained. All measurements were conducted at room temperature (ca. 25 °C).
Measurements with original/undiluted batter mixture
The following viscosity as a function of viscometer spindle speed was obtained:
Table.1. Brookfield viscosity measurements with the prepared flour-batter-water mix
RPM | Viscosity (cP) |
100 | 2200 |
60 | 2600 |
50 | 2800 |
30 | 3400 |
20 | 3700 |
12 | 4400 |
SRV readings in stirring vessel: Static 80 cP.; while stirring, 150 CP.
Measurements after first dilution of batter
A small amount of water was added and the measurements repeated:
Table.2. Brookfield viscosity measurements with the prepared flour-batter-water mix after the first dilution step
RPM | Viscosity (cP) |
100 | 1100 |
60 | 1300 |
50 | 1400 |
30 | 1900 |
20 | 2200 |
12 | 2900 |
SRV reading in stirring vessel while mixing was 66 cP, with same value for static measurement.
Measurements after second dilution of batter
A second dilution with water was made and the following viscosity readings were obtained:
Table.3. Brookfield viscosity measurements with the prepared flour-batter-water mix after the second dilution step
RPM | Viscosity (cP) |
100 | 620 |
60 | 700 |
50 | 730 |
30 | 880 |
20 | 960 |
12 | 900 |
During mixing, the SRV reading was 40 cP; static reading was 33 cP.
Batter viscosity measurement data analysis
All data sets of indicated viscosity as a function of LV-4 spindle speed were plotted:
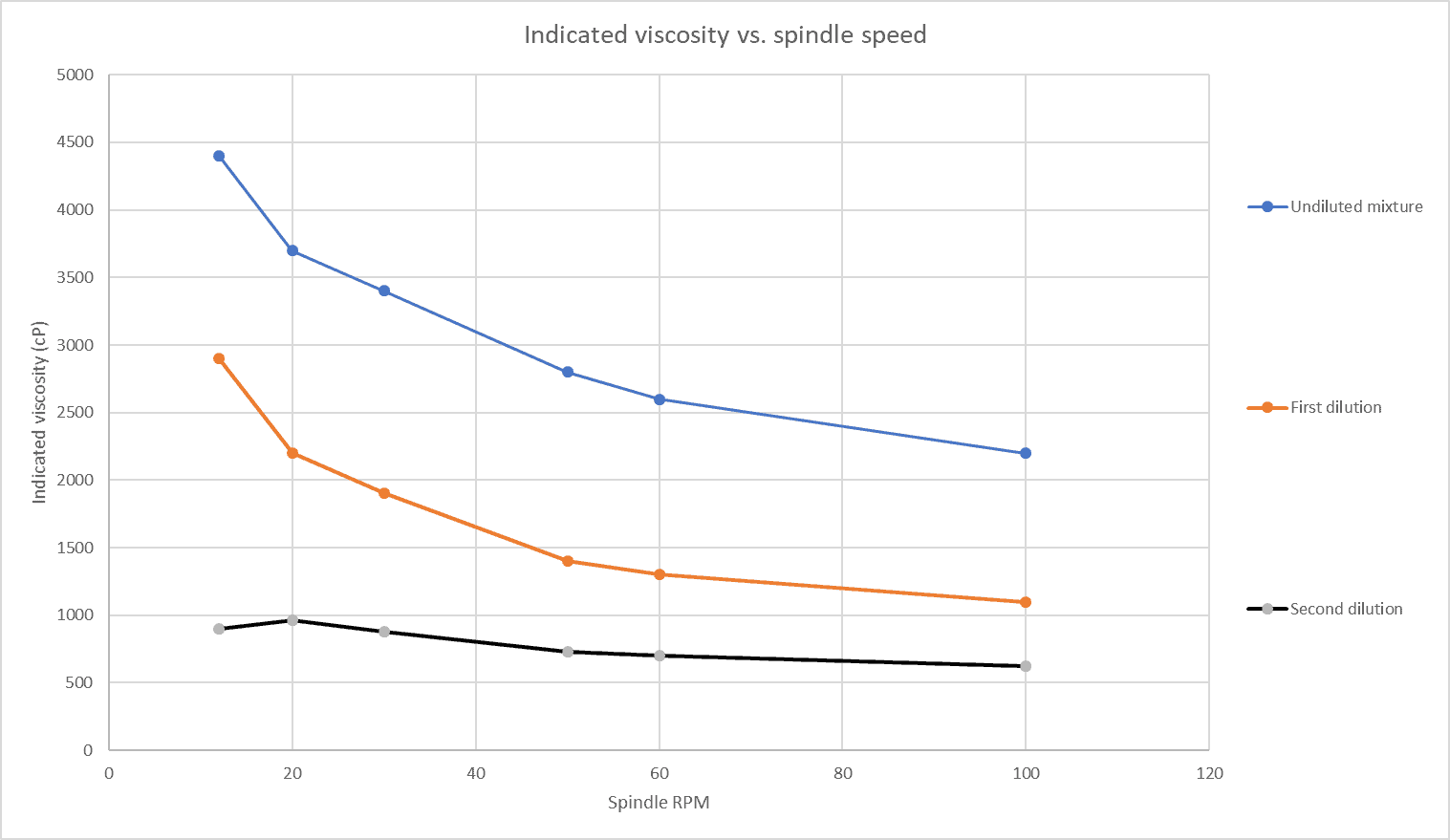
Fig.3. Brookfield viscosity measurements with the prepared flour-batter-water mix, with sequence of dilution steps
In addition, Rheonics SRV viscosity was plotted as a function of Brookfield viscosity for both the static and dynamic (in mixer). Measurements with the SRV were compared with Brookfield measurements at 100 RPM.
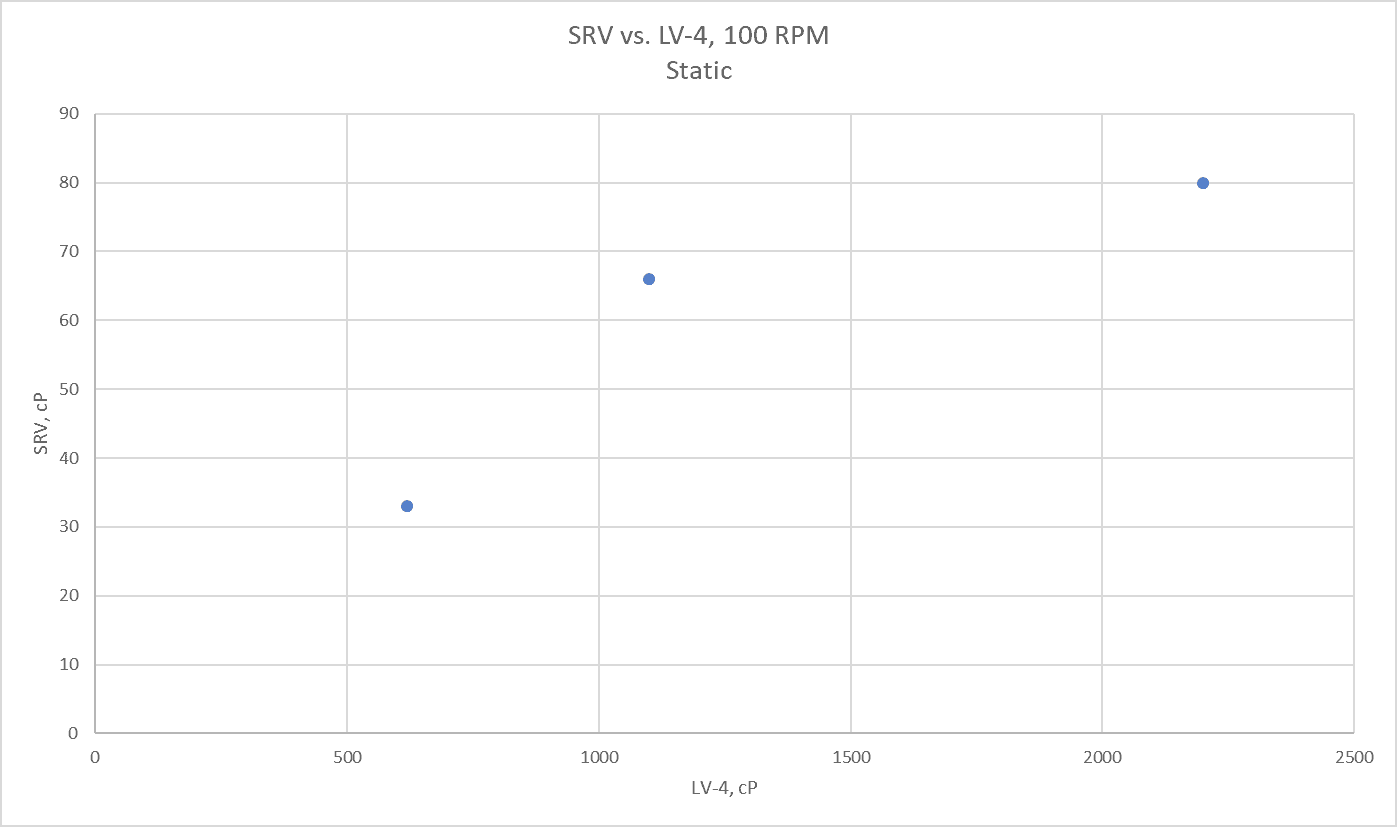
Fig.4. Rheonics SRV viscosity was plotted as a function of Brookfield viscosity, for static use
Static SRV measurements do not correlate well with LV-4 readings:
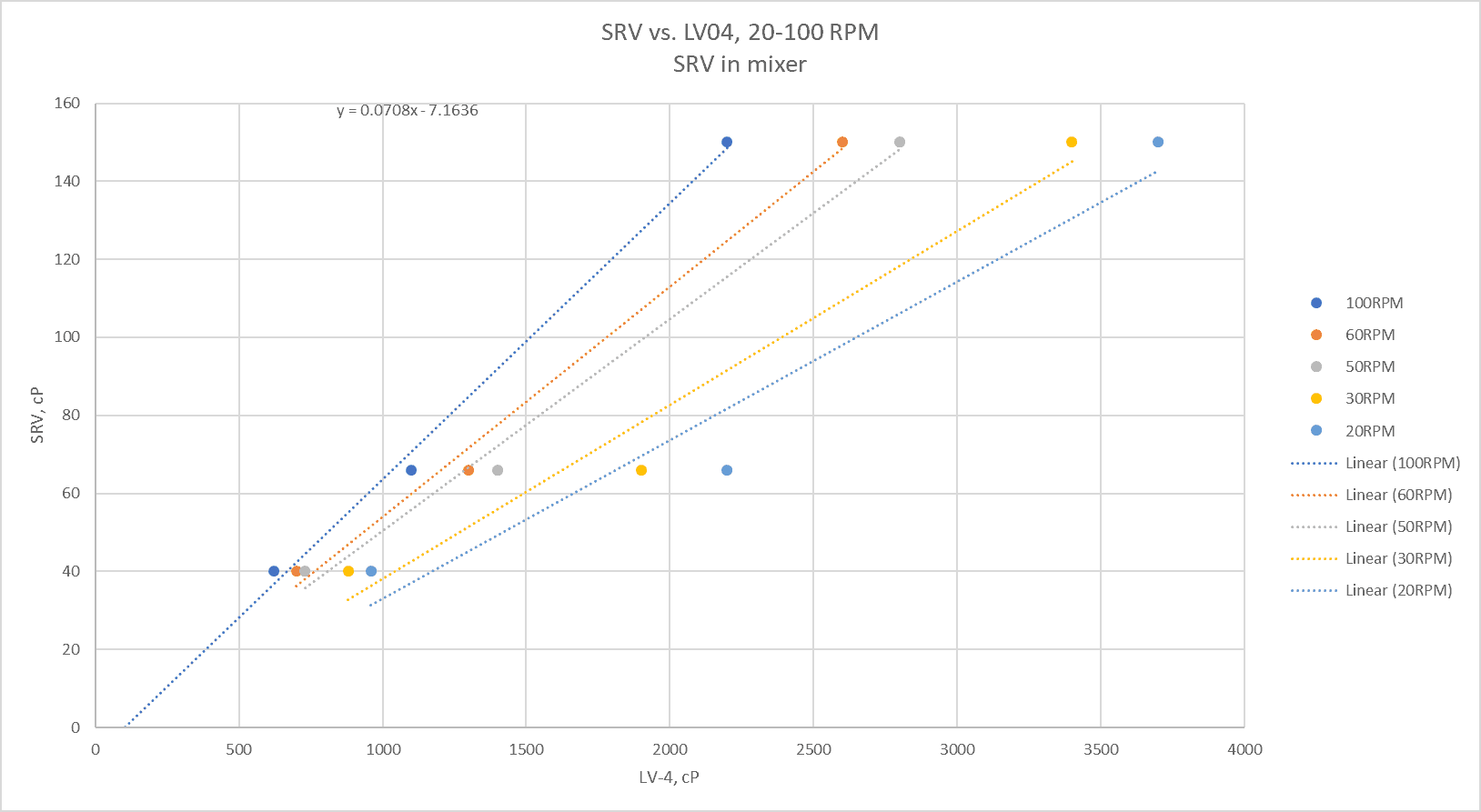
Fig.5. SRV static readings are plotted against LV-4 readings for all spindle speeds
For the dynamic case, a linear regression line described the relationship between Brookfield and SRV readings with reasonable accuracy.
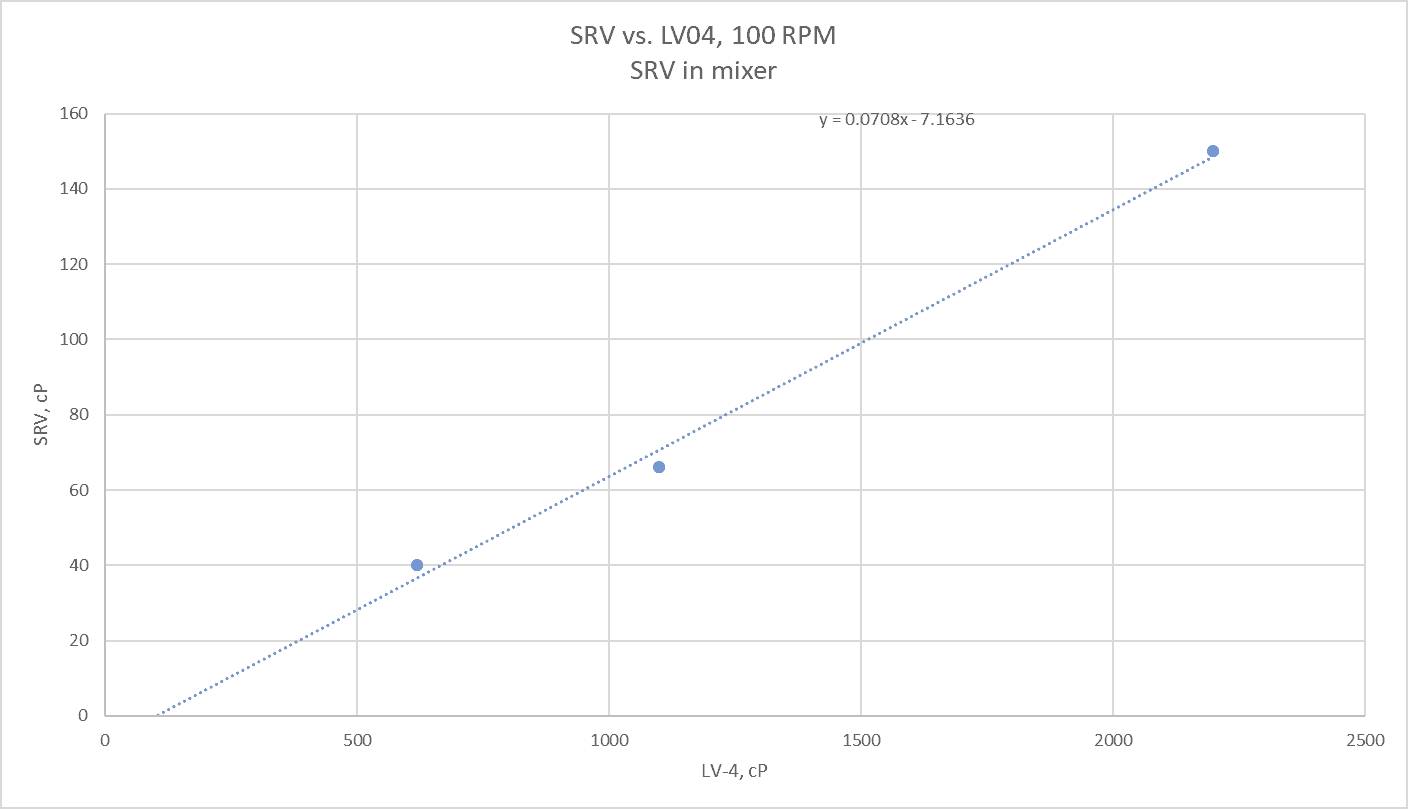
Fig.6. Rheonics SRV viscosity was plotted as a function of LV-4 viscosity, for dynamic case
If SRV dynamic readings are plotted against LV-4 readings for all spindle speeds, it is seen that the best linear fit is obtained for the highest speeds on the LV-4:
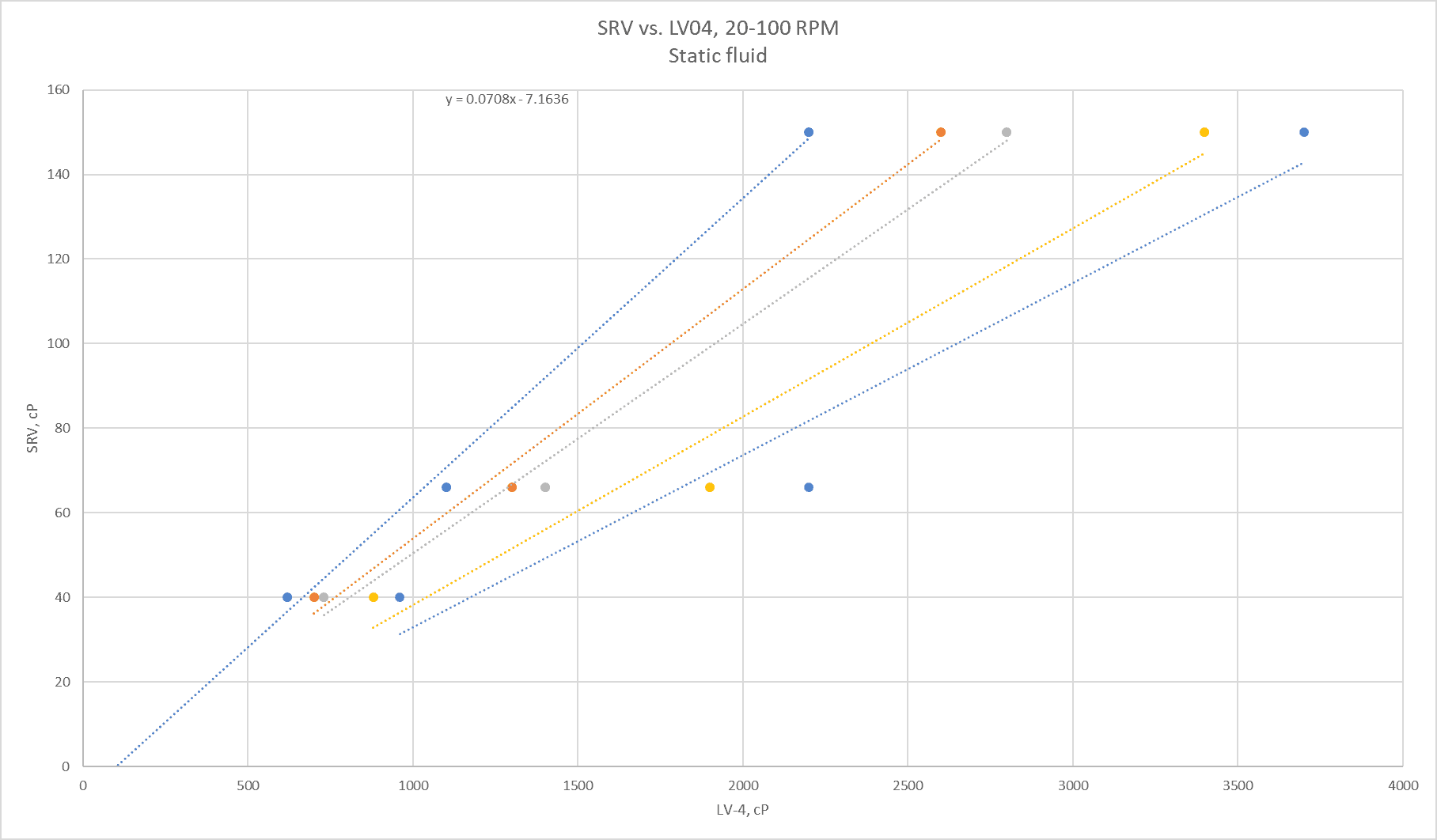
Fig.7. SRV dynamic readings are plotted against LV-4 readings for all spindle speeds
Analysis & Conclusion
Rotational viscometer measurements on a batter mix consisting of white flour mixed with a commercial batter mix shows repeatable spindle speed dependence. These data, particularly those taken at the highest spindle speeds, and therefore the highest shear rates correlate well with the readings from the Rheonics SRV while it is immersed in batter flowing past the sensor.
A correlation between lab viscometer (Brookfield LV) and SRV can be achieved by selecting any specific RPM on the rotational viscometer but it was better to select a higher RPM on the rotational viscometer to get a linear relation between the lab and process values.
Additional characteristics of SRV, inline process viscometer that ensures your lab rheological measurements can be used to control the manufacturing processes during production are:
- sanitary, hygienic connections
- CIP (clean-in-place)
- extremely high repeatability to give accurate
- inter-sensor reproducibility allows reuse of the same correlation across multiple plants
- sub-micron vibration amplitudes that do not affect fluid structure giving you accurate measurement of the fluid itself
- easy installation directly in process line, no need of by-pass, no disruption to flow
- robust sensor made of 316L stainless steel with sealed connections (IP69K) to support high temperature, high pressure, acidic and alkaline cleaning
- zero maintenance
- high ROI (return-on-investment)
Rheonics Instrument Selection
Rheonics designs, manufactures and markets innovative fluid sensing and monitoring systems. Precision built in Switzerland, Rheonics’ in-line viscometers has the sensitivity demanded by the application and the reliability needed to survive in a harsh operating environment. Stable results – even under adverse flow conditions. No effect of pressure drop or flow rate. It is equally well suited to quality control measurements in the laboratory. No need to change any component or parameter to measure across full range.
Suggested product(s) for the Application
- Wide viscosity range – monitor the complete process
- Repeatable measurements in both Newtonian and non-Newtonian fluids, single phase and multi-phase fluids
- Hermetically sealed, all stainless steel 316L wetted parts
- Built in fluid temperature measurement
- Compact form-factor for simple installation in existing process lines
- Easy to clean, no maintenance or re-configurations needed
- Single instrument for process density, viscosity and temperature measurement
- Repeatable measurements in both newtonian and non-newtonian fluids, single phase and multi-phase fluids
- All metal (316L Stainless Steel) construction
- Built in fluid temperature measurement
- Compact form-factor for simple installation in existing pipes
- Easy to clean, no maintenance or re-configurations needed