Introduction
Viscosity testing of cosmetics and personal care products is extremely important for quality control in their production. Analyzing the viscosity at various shear rates to simulate the sample’s processability during production as well as application behaviour to ensure customer satisfaction is one of several test methods in quality control. The difference between top quality cosmetic creams and general cosmetic creams lies not so much with the difference in the product’s functional components but more with differences in their rheological properties (there are of course, high end cosmetic creams which include medicinal components).
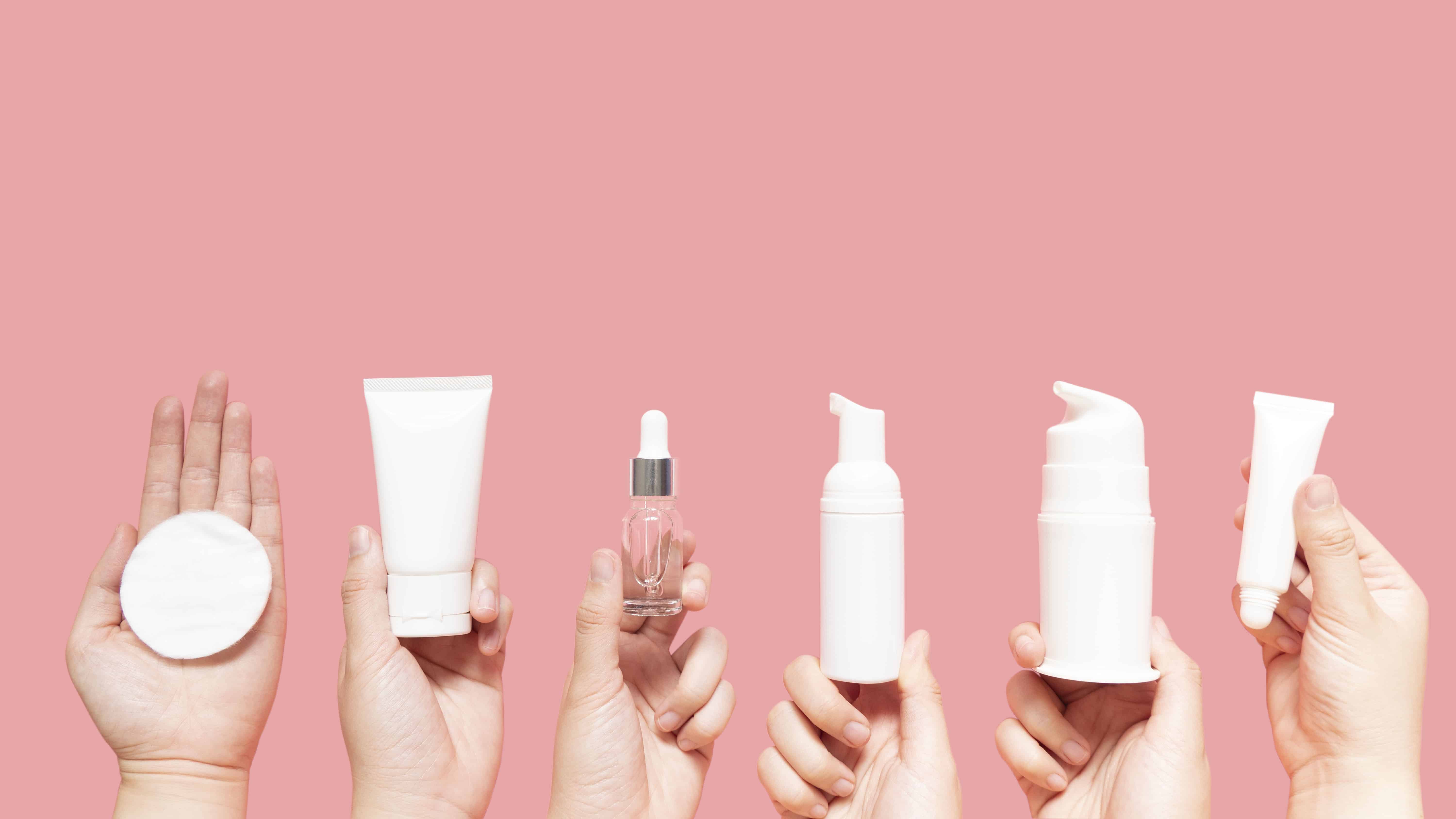
Especially in this time of rising material costs, the increasing number of competitors, the higher expectations of the customer and the desire to produce top-quality products in a more environmentally conscious way, chemical and cosmetic companies can make a lot of profit with an (in-line) viscometer. Along with fluctuations of costs of raw materials, applications of personal care industry (cosmetics) need to counter challenges related to efficiency, lead time, and capacity utilization. Additionally, continuous innovations and developments from manufacturers around the consistency, permeation on skin and textures is one of the key focus areas for chocolate manufacturers. Industry leaders are moving towards adoption of more advanced technologies such as automation, industrial internet of things (IIoT) and simulation techniques to stay lean and competitive in terms of both quality and costs.
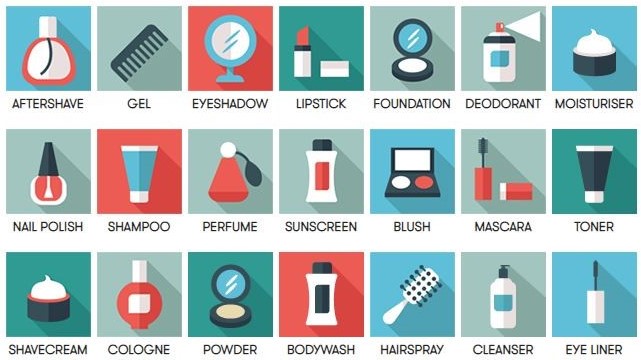
- Wide range viscosity measurement (also density with SRD) with built in fluid temperature measurement
- Hermetically sealed, all 316L stainless steel wetted parts
- Stable and repeatable measurements in non-Newtonian fluids like paints and coatings
- Small form-factor for simple installation in existing flow lines and nozzle heads
- Easy integration with existing data acquisition systems using digital and analog data communication
- Smart self-detection of sensing element cleanliness, easy to clean and verify calibration
Application
Cosmetic products are designed to integrate a variety of attributes, including essential functions (e.g. helping the skin appear vibrant, providing moisture retention), taste preferences (e.g. fragrance, color), usability, and so forth. How do rheological properties relate to such aspects? Typical examples are the use of viscosity measurements to control factors associated with achieving desired application comfort for creams and obtaining good coating results with manicures and lipsticks (including temperature characteristics, etc.).
Whatever the reason behind the product’s design, it is critical to customer satisfaction to maintain a consistent and controlled quality of viscosity across production lines. Further, viscosity can impact a cosmetic product’s chemical stability in its packaging over time. Therefore, given the many reasons why viscosity is important to the overall quality of cosmetic products, measuring viscosity has become key to successful cosmetic production companies.
The quality of a cosmetic product, in the same way as to other kind of products, is initially defined by the manufacturer that chooses the features that a product should present. On the other hand, the quality control of a product aims to verify if all of these defined features are in accordance with the standard definitions and if it will be maintained during the shelf life of the product.
The quality control of cosmetics is important to ensure the efficacy and safety of products and its raw-materials. efficient, low cost and rapid methods to assay cosmetics’ quality control are a priority owing to the explosive growth that cosmetic industries have witnessed worldwide. Rheology – which studies the flow and deformation of fluids – can be applied by the cosmetic industry to the evaluation of cosmetics’ quality control in an efficient manner. Rheology has found extensive use in research laboratories and industries as a tool for characterizing ingredients and products, and to predict the performance of products and consumer acceptance.
Quality control of cosmetics
Rheology has been widely used because, by means of this tool, the researcher can determine physicochemical properties of a product. Specifically, in relation to the quality control of cosmetics, specifically, rheology can be applied to help in determining the stability of products by means of the apparent viscosity measured periodically in a determined period exposing the samples to stress conditions (high and low temperatures, solar irradiation), and to monitor the flow characteristics during the shelf life or in the stability assay of a product. Majority of cosmetic industries use viscometers to guarantee that the viscosity of different batches of a product is maintained. In addition, the rheology can be used to evaluate the stability over the time by dynamic and oscillatory rheological measurements and the release of active principles. Additionally, viscosity measurement of raw materials for cosmetic products are also vital for quality control.
Release profile and permeation of cosmetics products in the skin
The transdermal absorption of topically administered drugs depends on the rate of release and the permeability of them into the skin and also of the viscosity of the formulation. Thus, it is possible to say that different categories of products should present peculiar rheological properties inherent to its application. In this way, the rheology can influence the diffusion coefficient, altering the release and permeation of cosmetics active substances. Some authors have related the influence of rheological characteristics on the release profiles and consequently in the permeation of active substances in the skin; thus, the addition of thickening agents or attainment of a weak-gel because of physical entanglement of polymer chains must be considered in the choice of cosmetics bases. Thus, rheology can help in the assay of release and permeation in the skin.
Consistency and texture of the cosmetic products and its sensorial effects
Viscosity and thickening agents are an important element of cosmetic formulation, offering the opportunity to change viscosity, improve rheological properties and modify the product aesthetics linked to consumer perception. From a consistency test, four parameters can be evaluated: index of viscosity, consistency, firmness and cohesiveness. How does viscosity affect texture and consistency? Consistency is a textural property related to the amount of product felt between fingertip and skin. It relates to the ‘firmness’, ‘thickness’ or ‘viscosity’ of a liquid or fluid semi-solid. The higher the index of viscosity, the more resistant to withdrawal is the sample. This is an indicator of the cohesiveness and also the consistency or viscosity of the sample.
Viscosity control is especially effective in product control related to the application sensation of creams and emulsions. Emulsions are liquids which contain water droplets dispersed in oil or oil droplets dispersed in water and are a typical type of substance from the rheological point of view. Creams are a category of emulsions with special properties where the application of a certain amount of force results in a rapid fall in viscosity. What this means is that when the cream is applied to the skin, it becomes more spreadable. The normal high viscosity of the cream changes instantly to a lower viscosity when subjected to a force which allows it to be spread easily while providing a sensation of smoothness.
Real time process monitoring and control across all production runs
After rheological characterisation is carried out and the formulation composition is finalised, the production engineers need to achieve the following across the cosmetics manufacturing process:
- Inline process monitoring & control throughout the production/mixing steps
- Complete quality consistency across the run and across all batches of production
Development of new cosmetics products
For those developing cosmetics, it is necessary for serious developers to operate both a viscometer to isolate any compound instabilities or weaknesses, ensure product reliability and performance, and guarantee consistency and quality of lines for consumers and other stakeholders. The best viscometers will be able to give high-precision readings in only moments and offer easy-to-use functions, including absolute values, simplified clean-up, mobility, and broad measurement ranges. The initial investment costs become drastically lower with the machine’s versatility.
Modern methods of product design and manufacturing attempt to quantify such “sensory computer” judgments in order to achieve standardization in product development and production. Measured rheological values including viscosity are convenient and usable indicators for this purpose. As polymers are used extensively in cosmetics there are naturally many opportunities for the involvement of rheology technology. One interesting example is lipstick. Long wearing lipstick has been around for several years. Formerly, lipstick was generally made of oils with color pigments mixed in. Such lipsticks were designed to be easy to apply but came with a downside as they tended to leave lipstick traces on surfaces where lips had touched. Since then lipstick manufacturers have each devised various methods to create long lasting lipstick with research in polymers – which mostly involves rheological characterizations.
So, in a short way, viscosity characterisation is a valuable tool in cosmetics industry due to the following reasons:
- Quality control of cosmetics
- Used in the stability tests, in the comparison between competing samples
- Used in the comparison between an original product and a product with an alteration in a constituent
- Real time process monitoring and control across all production runs
- Assists in development of new products, i.e. to develop cosmetic with rheological characteristics which indicate stability
The three parameters of most importance in rheology which need to be defined are shear stress, shear rate and viscosity. Rheological characteristics could be used to evaluate and to predict the stability of cosmetic products and could be applied to compare competing products in the market and to assay if a change in the composition will cause alterations that could be perceived by the consumer.
Why is viscosity management critical in cosmetics & personal care products industry?
The broad and significant factors which make viscosity management critical in cosmetics & personal care products industry:
Maximum compliance with products specifications & quality: Personal care products must comply with finished product specifications and any appropriate compendial requirements. Continuous inline viscosity monitoring can help attain desired rheological properties for a final defined product texture and ease of application.
Reduce processing errors: Viscosity control can help alleviate the frequency of miscues – sticking and picking, twinning, peeling, splitting, cracking, roughness, blistering, bridging and surface erosion.
Texture, consistency, skin-permeation properties: Controlling the viscosity is the key to the right properties & consistency because that is the factor subjected to the highest variability. Rheological properties are mainly influenced by particle size distribution and ingredients composition, which in turn affects final texture and melting profile and also plays a significant role on process in cosmetics industry.
Better design of product packaging: In addition to quality control, knowing the viscosity of a (semi) finished product helps to organize the production process efficiently and to reduce costs. For example, a better flow through tubes can take place and dispensers can be adjusted to the right force to induce flow without the package becoming overfilled.
Reduce costs and improve profit margins: Mixing with incorrect viscosity harms more than just effectiveness of the tablet. Poor viscosity management drives up usage of ingredients, affecting the profit margins.
Waste: Materials rejected due to poor quality can be reduced with proper viscosity management.
Efficiency: Eliminating manual viscosity control frees operators’ time and enables them to focus on other tasks.
Compliance: Perhaps to a greater degree than other industries, pharmaceutical and personal care industry demands the highest levels of quality. The need to achieve target properties is non-negotiable when it comes to regulatory codes of this industry.
To ensure consistent high-quality and uniform processing, the change in viscosity through-out the process stream is monitored in real time, making measurements from a baseline rather than simply measuring absolute values, and making automatic viscosity adjustments by adjusting ingredients and temperature to keep it within specified limits.
Process Challenges
Due to the non-Newtonian characteristic of chocolates, the shear rate (and consequently the viscosity) needs to be corrected for any geometry used to make the measurements, except for those made in an “absolute” viscometer, of which the cone-and-plate and the torsional plate are the only examples. The narrow-gap Couette viscometer is a close approximation, which requires a fine hand to set up, is prone to operator error, and is not usually indicated for industrial situations.
Existing laboratory viscometers are of little value in process environments because viscosity is directly affected by temperature, shear rate and other variables that are very different off-line from what they are in-line. Traditionally, operators have measured the viscosity of fully-formulated system using the efflux cup. The procedure is messy and time-consuming, particularly if the solution needs to be filtered first. It is pretty inaccurate, inconsistent and non-repeatable even with an experienced operator. Rotational techniques are more bothered by process fluctuations or vibrations and flow changes. In addition, the technology is less easy to integrate into the process. Often the entire process needs to be adjusted to make an in-line measurement possible.
Some companies use thermal management systems to keep point-of-application at a determined optimal temperature to achieve constant viscosity. But temperature is not the only factor affecting viscosity. Shear rate, flow conditions, pressure and other variables including raw material variability can affect in process viscosity. Temperature controlled systems also have high energy consumption, high system costs, long installation times and a large footprint physically and environmentally.
Rheonics' Solutions
Automated in-line viscosity measurement and control is crucial to control the ink viscosity. Rheonics offers the following solutions, based on a balanced torsional resonator, for process control and optimization in the production process:
- In-line Viscosity measurements: Rheonics’ SRV is a is a wide range, in-line viscosity measurement device with inbuilt fluid temperature measurement and is capable of detecting viscosity changes within any process stream in real time.
- In-line Viscosity and Density measurements: Rheonics’ SRD is an in-line simultaneous density and viscosity measurement instrument with inbuilt fluid temperature measurement. If density measurement is important for your operations, SRD is the best sensor to cater to your needs, with operational capabilities similar to the SRV along with accurate density measurements.
Continuous inline real time viscosity monitoring & control solutions can be used to achieve complete process control during manufacturing and quality consistency across the run and various batches of production. Once the lab technicians define the composition and approve the sample, Rheonics inline viscosity monitoring and control systems ensure that the whole batch meets the defined specifications and are exactly the same as approved in the laboratory with the press of just a button! The same consistency is achieved across all the batches of production, thus reducing rejects and scrapped quantities.
Automated online viscosity measurement through SRV or an SRD eliminates the variations in sample taking and lab techniques which are used for viscosity measurement by the traditional methods. The sensor is located in-line so that it continuously measures the formulated system viscosity (and density in case of SRD). Consistency is achieved through automation of the dosing system through a controller using continuous real-time viscosity measurements. Using an SRV in process line, efficiency is improved improving productivity, profit margins and environmental goals. Both the sensors have a compact form factor for simple OEM and retrofit installation. They require no maintenance or re-configurations. Both the sensors offer accurate, repeatable results no matter how or where they are mounted, without any need for special chambers, rubber seals or mechanical protection. Using no consumables, SRV and SRD are extremely easy to operate with zero maintenance.
Rheonics' Advantage
Compact form factor, no moving parts and require no maintenance
Rheonics’ SRV and SRD have a very small form factor for simple OEM and retrofit installation. They enable easy integration in any process stream. They are easy to clean and require no maintenance or re-configurations. They have a small footprint enabling Inline installation in ink lines, avoiding any additional space or adapter requirement on the press and on ink carts.
High stability and insensitive to mounting conditions: Any configuration possible
Rheonics SRV and SRD use unique patented co-axial resonator, in which two ends of the sensors twist in opposite directions, cancelling out reaction torques on their mounting and hence making them completely insensitive to mounting conditions and ink flow rates. These sensors can easily cope up with regular relocation. Sensor element sits directly in the fluid, with no special housing or protective cage required.
Instant accurate readouts on conditions – Complete system overview and predictive control
Rheonics’ software is powerful, intuitive and convenient to use. Real-time viscosity can be monitored on a computer. Multiple sensors are managed from a single dashboard spread across the factory floor. No effect of pressure pulsation from pumping on sensor operation or measurement accuracy. No effect of vibration.
Easy installation and no reconfigurations/recalibrations needed
Replace sensors without replacing or reprogramming electronics, drop-in replacements for both sensor and electronics without any firmware updates or calibration coefficient changes. Easy mounting. Screws into ¾” NPT thread in ink line fitting. No chambers, O-ring seals or gaskets. Easily removed for cleaning or inspection. SRV available with flange and tri-clamp connection for easy mounting and dis-mounting.
Low power consumption
24V DC power supply with less than 0.1 A current draw during normal operation
Fast response time and temperature compensated viscosity
Ultra-fast and robust electronics, combined with comprehensive computational models, make Rheonics devices one of the fastest and most accurate in the industry. SRV and SRD give real time, accurate viscosity (and density for SRD) measurements every second and are not affected by flow rate variations!
Wide operational capabilities
Rheonics’ instruments are built to make measurements in the most challenging conditions. SRV has the widest operational range in the market for inline process viscometer:
- Pressure range up to 5000 psi
- Temperature range from -40 up to 200°C
- Viscosity range: 0.5 cP up to 50,000 cP
SRD: Single instrument, triple function – Viscosity, Temperature and Density
Rheonics’ SRD is a unique product that replaces three different instruments for viscosity, density and temperature measurements. It eliminates the difficulty of co-locating three different instruments and delivers extremely accurate and repeatable measurements in harshest of conditions.
Achieve the right print quality, cut down costs and enhance productivity
Integrate an SRV/SRD in the process line and ensure colour consistency throughout the printing process. Achieve constant colours without worrying about colour variations. SRV (and SRD) constantly monitors and controls viscosity (and density in case of SRD) and prevents overuse of expensive pigments and solvents. Reliable and automatic ink supply ensures that presses run faster and saves operators’ time. Optimise the printing process with an SRV and experience lesser reject rates, lesser wastes, fewer customer complaints, fewer press shut downs and material cost savings. And at the end of it all, it contributes to a better bottom line and a better environment!
Clean in place (CIP)
SRV (and SRD) monitors the cleanup of the ink lines by monitoring the viscosity (and density) of the solvent during the cleaning phase. Any small residue is detected by the sensor, enabling the operator to decide when the line is clean for purpose. Alternatively, SRV provides information to the automated cleaning system to ensure full and repeatable cleaning between runs.
Superior sensor design and technology
Sophisticated, patented 3rd generation electronics drive these sensors and evaluate their response. SRV and SRD are available with industry standard process connections like ¾” NPT and 1” Tri-clamp allowing operators to replace an existing temperature sensor in their process line with SRV/SRD giving highly valuable and actionable process fluid information like viscosity besides an accurate measurement of temperature using an in-build Pt1000 (DIN EN 60751 Class AA, A, B available).
Electronics built to fit your needs
Available in both an explosion-proof transmitter housing and a small-form factor DIN rail mount, the sensor electronics enables easy integration into process pipelines and inside equipment cabinets of machines.
Easy to integrate
Multiple Analog and digital communication methods implemented in the sensor electronics makes connecting to industrial PLC and control systems straightforward and simple.
Implementation
Directly install the sensor to your process stream to do real time viscosity and density measurements. No bypass line is required: the sensor can be immersed in-line, flow rate and vibrations do not affect the measurement stability and accuracy. Optimize mixing performance by providing repeated, consecutive, and consistent tests on the fluid.
Rheonics Instrument Selection
Rheonics designs, manufactures and markets innovative fluid sensing and monitoring systems. Precision built in Switzerland, Rheonics’ in-line viscometers has the sensitivity demanded by the application and the reliability needed to survive in a harsh operating environment. Stable results – even under adverse flow conditions. No effect of pressure drop or flow rate. It is equally well suited to quality control measurements in the laboratory.
Suggested product(s) for the Application
- Wide viscosity range – monitor the complete process
- Repeatable measurements in both Newtonian and non-Newtonian fluids, single phase and multi-phase fluids
- Hermetically sealed, all stainless steel 316L wetted parts
- Built in fluid temperature measurement
- Compact form-factor for simple installation in existing process lines
- Easy to clean, no maintenance or re-configurations needed
- Single instrument for process density, viscosity and temperature measurement
- Repeatable measurements in both newtonian and non-newtonian fluids, single phase and multi-phase fluids
- All metal (316L Stainless Steel) construction
- Built in fluid temperature measurement
- Compact form-factor for simple installation in existing pipes
- Easy to clean, no maintenance or re-configurations needed