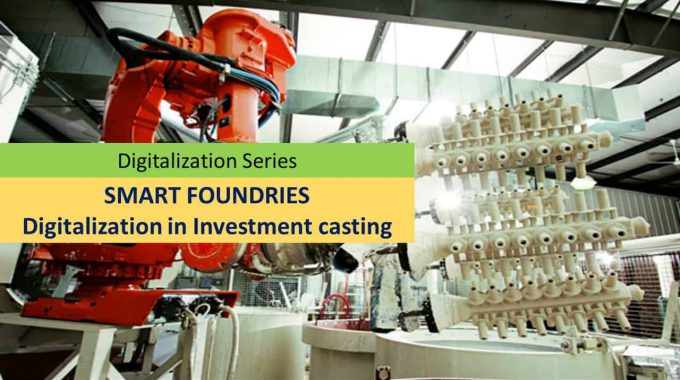
Smart foundries – drivers for casters’ embrace of Industry 4.0 and digitalization
Application
Many parameters can alter the ceramic slurry quality in investment casting across batches – Temperature and humidity fluctuations, mixing equipment condition, substrates, solvents, formulations, line-integration, machine interactions and time of mixing. In foundries, the downtimes and delay in deliveries involved due to rejects can hurt the profitability seriously. But what if there was a system which can continuously monitor the product quality and consistency, and could take corrective actions automatically and adaptively without disrupting the whole operation?
Technologies required to deliver such transformational changes in the foundry now exist. Once the manufacturer invests in process monitoring equipment, the current industrial control systems are well developed to be able to use the viscosity data from the processes effectively for operations in multiple different ways.
Steps of the Investment Casting Process explained. Video Source: Signicast | https://www.signicast.com/knowledge-center/videos
Shell building in ceramic slurry – viscosity is crucial to getting reliable slurry
Ceramic shell, formed by dipping the wax assembly multiple times in the ceramic slurry is critical to achieving precise, reproducible parts. To ensure consistent shells, it is vital to have consistent ceramic slurry. Viscosity is one of the key properties of the ceramic slurry which defines the overall thickness and adhesion of the multiple coats during shell formation. After coating, the ceramic shell is fired to attain ultimate strength, dimensions and morphology as finished products. Yields of usable products are dependent on reliable shells.
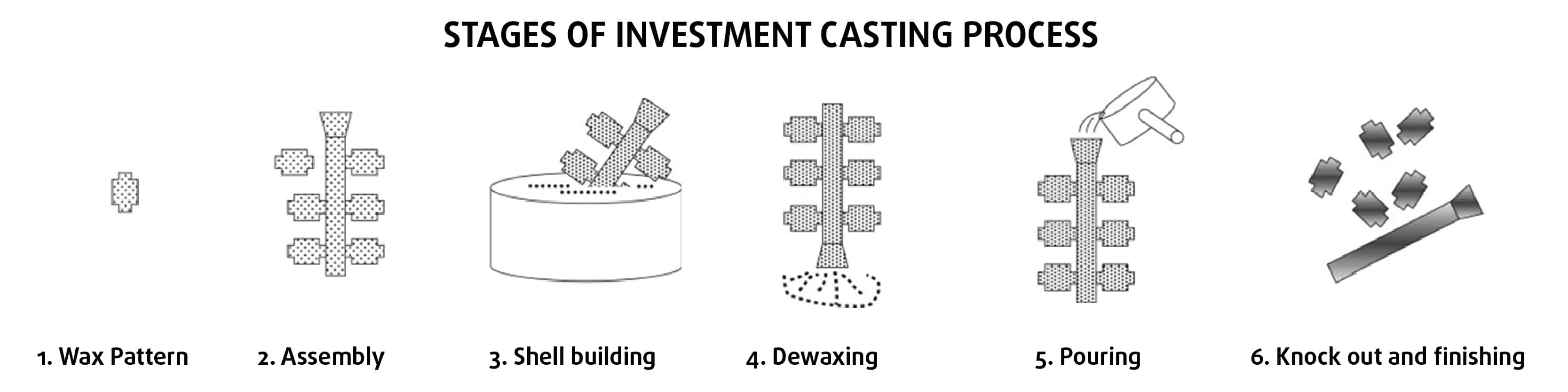
Investment casting process; adapted from Yamagata (2005)
Related Application Note
Monitoring and controlling viscosity of ceramic slurries in investment casting
Investment castings are one of the most popular production methods for metal parts today. Investment casting process, also termed as a lost wax process, is relatively simple, which enables rapid production rates while ensuring consistent dimensional accuracy. Parts that are typically made by investment casting include those with complex geometry such as turbine blades or firearm components. High temperature applications…
Drivers for manufacturers embrace of Industry 4.0
The key value drivers of embracing real-time inline viscosity monitoring equipment by manufacturers and system integrators operating in ceramic slurry coating for shell building are the following:
Automated corrective actions for ensuring product consistency. Closed control loops through sensor-based, in-line quality inspection reduce waste and increase yield through early process deviation detection, root cause analysis, and automatic correction.
More agility in dealing with new product variants in production, compliance and product provenance. Casting manufacturers get a more accurate picture of how the new slurry formulations will behave and how they might need to adjust current systems and control parameters.
Big data provides robust evidence to base decisions for greater efficiency. The data provided by the process monitoring equipment enables them to tweak various process parameters and optimise the manufacturing process. Interconnection and information transparency allow for operators to make decisions both inside and outside of production facilities, thus enabling decentralization of decisions.
Higher customer satisfaction and adapting to customer requests. Industry 4.0 solutions can impact casting companies by driving closer interactions with their customers. The technology, data, and information that can help transform manufacturing operations can also make processes and systems more responsive to customer needs.
Key benefits of Rheonics Viscosity and Density meters in food applications to support the factory digitalization and Industry 4.0 adoption
With huge application areas and growing demand from the end-use sectors, this industry is looking for new ways to improve efficiency, lead time, and capacity utilization. Industry leaders across sectors are moving towards adoption of more advanced technologies such as automation, industrial internet of things (IIoT) and simulation techniques. Inline viscosity monitoring solutions can help investment casters achieve advanced process control over the slurry preparation (mixing) and coating process to build top-quality and defect-free shells with more real-time insights into their processes; and reap the benefits of Industry 4.0 and automation such as reduction in lead times, enhance capacity utilisation, reduce scraps and wastes and optimize efficiency.
The sensors – SRV and SRD are being used in slurry tanks for the investment casting application across the globe. These sensors have undergone internal testing, experiments and qualification procedures for operation with fluids generally used in this application. Our in-house application engineering team gives machine builders advanced knowhow to achieve seamless integration of our sensors in their system and help provision casting quality control data to their end users through on-premise, edge or cloud connectivity.
Unique benefits with the Rheonics inline online viscometer SRV for slurry mixing and coating applications include:
- Operates accurately in almost all coating systems with a broad range of composition/formulations
- Maintains the set slurry viscosity in mixing tanks regardless of temperature and humidity fluctuations, mixing equipment condition, substrates, solvents, formulations or dosing of colloidal silica, water and/or polymers, wetting agents, anti-foaming agents, and refractory flours
- Rugged, hermetically sealed sensor head. Sensor probe can be cleaned inline with all standard CIP/SIP processes, or with a wetted rag manually, without the need for disassembly or re-calibration
- No moving parts to age or foul with sediment
- Insensitive to particulate matter; no narrow gaps to foul with particulates
- All wetted parts are 316L stainless steel – no corrosion problems
- Certified under ATEX and IECEx as intrinsically safe for use in hazardous environments
- Wide operational range and simple integration – Sensor electronics and communication options make it extremely easy to integrate and run in industrial PLC and control systems
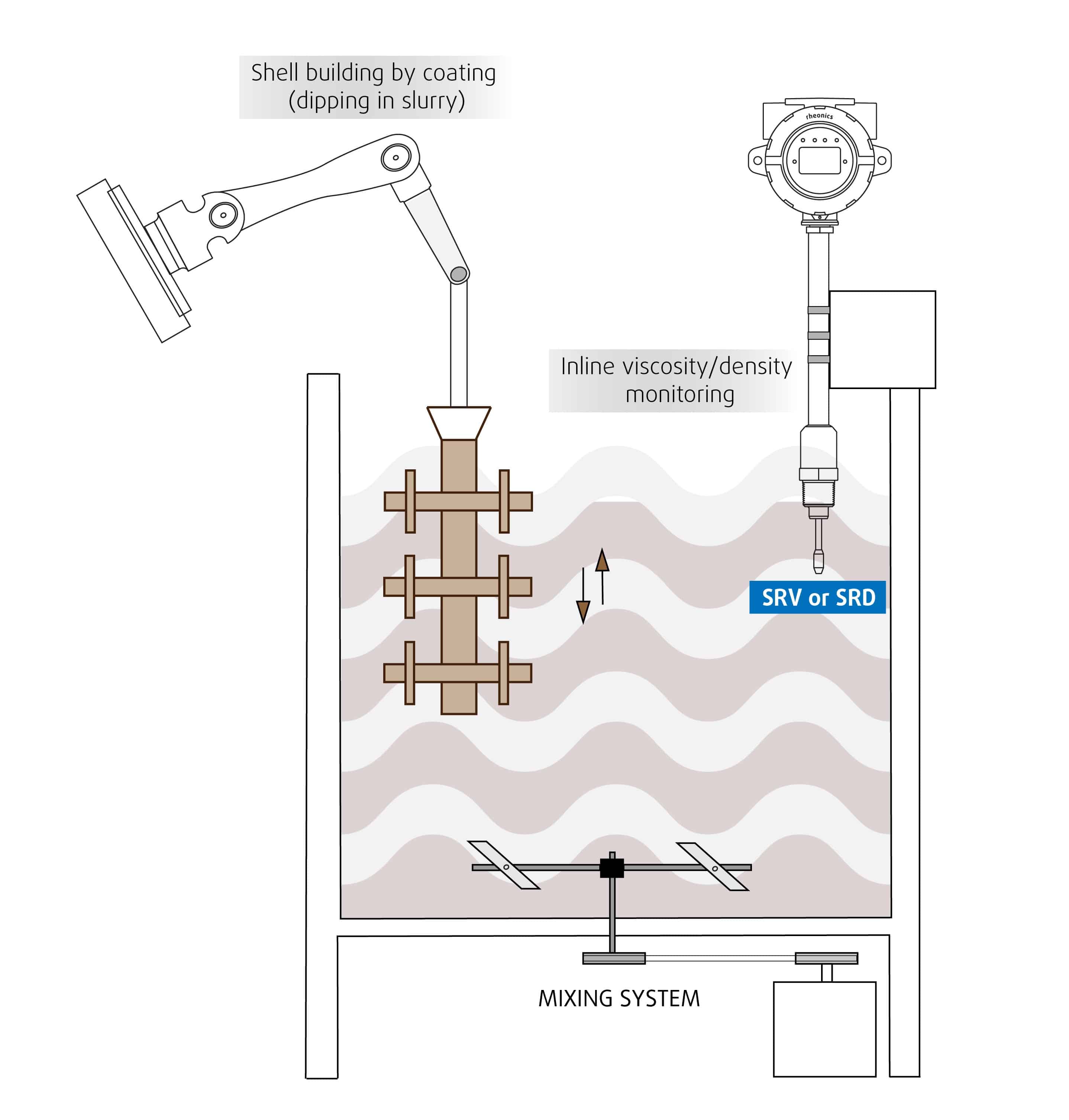
Rheonics density meters and viscosity meters are available as probes and flow-through systems for installation in tanks, process lines and reactors. All Rheonics products are designed to withstand harshest process environments, high temperature, high level of shock, vibrations, abrasives & chemicals.