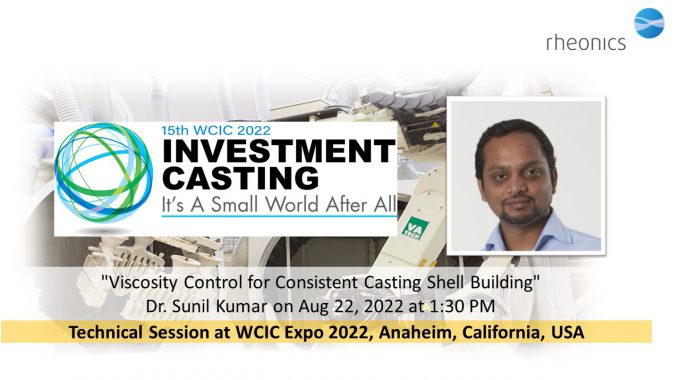
Rheonics Technical Session & Booth at WCIC Expo, Investment Casting Institute – August 2022 at Anaheim, California, USA
Abstract (Technical Session)
Quality of casting shells is dependent on the viscosity of the shell-building slurry. This has two principal reasons: First, the viscosity is directly related to the solids content of the slurry and reflects shifts in its composition through evaporation of the liquid component. Second, the performance of the slurry is directly related to its flow characteristics. The thicker the slurry – the higher its viscosity – the slower it runs off the form and the thicker the layer that it deposits. If the viscosity is too low – the slurry is too thin – it flows off the form too quickly, and the deposited layer is too thin. Since shells are formed from multiple layers, any deviations of slurry viscosity can contribute to failures of quality and performance of the shells, which can, in turn, lead to defects in the parts cast in the shells.
In order to control viscosity, it is necessary to measure it. The accuracy of control – how well the viscosity of a slurry can be set and maintained throughout the casting process – depends on the accuracy and repeatability, but also the ease of use, of the chosen measurement. The traditional measurement method is the flow cup, which measures viscosity as the number of seconds required by the slurry to run out of the cup. This measurement is not suited for continuous, repetitive monitoring of viscosity, nor is it particularly accurate.
A robust balanced torsional resonator based inline viscometer brings accurate, repeatable and continuous monitoring of slurry viscosity during shell building. An integrated slurry viscosity tracking and control system is used to apply the viscometer’s measurements toward maintaining constant slurry viscosity during slurry preparation and shell building, despite evaporation losses, temperature changes and other influences that can cause unwanted changes to the shell quality. The inline viscometer and the integrated control system can, in addition, support the growing trend toward full shell-room automation, by reducing an important source of variability in the otherwise highly automated shell-building process.
Visit Us at Booth 222
Rheonics inline viscosity and density meters enable real-time monitoring and control of investment casting slurry properties to produce the best possible shell and casting quality. Viscosity and density of casting slurry are crucial to ensuring both the quality of the shell and the final castings for which it is used. Rheonics sensor put essential online quality control tools in the operators’ hands to optimize both the shell building and casting processes.
Realtime measurements give the operator valuable information about how the slurry will perform during the shell-building process, including factors like surface finish, strength, and ultimately, yield of top-quality castings.
Rheonics sensors let the operator adjust slurry parameters both during mixing and shell building, with individualized measurements for each layer as the shell is built up. In combination with the Rheonics SlurryTrack system, slurry properties can be automatically controlled without manual intervention, freeing operators to focus on their central job – to make the best shells and castings possible, despite variations in raw materials, mixing processes, and aging of the slurry. SlurryTrack is a standalone complete solution for ceramic slurry management that also integrates slurry measurement data into industrial SCADA systems thanks to a broad selection of built-in data interfaces. Full traceability of every shell is now at the fingertips of floor operators, production supervisors, and quality control personnel.
Highlights at WCIC
At the ICI world conference, Dr. Sunil Kumar and Dr. Joe Goodbread present a talk on the Realtime viscosity control for consistent shell building on Monday, August 22, 2022 in afternoon session.
During the EXPO, we invite you to come have an in-depth look at the underlying technology. At the exhibition, we will present the inline viscometer SRV, inline density and viscosity meter SRD and the SLURRYTRACK integrated system.
To learn more, visit us at Booth 222.
In investment casting slurry viscosity is an important process parameter. Keeping slurry viscosity within the proper range throughout the coating step is central to forming a uniform coating thickness and desirable shell properties, as well as avoiding some of the most common shell defects. Our technical presentation, will cover the following:
- Overview of the shell building process
- How are shell properties affected by ceramic slurry viscosity?
- Why viscosity management is important in shell building?
- Types of shell defects that can be alleviated with viscosity control during the mixing process
- Process monitoring and control challenges – issues with traditional viscosity measurements
- Why investment casters are embracing Industry 4.0, data-driven processes and digitalization
- An inline sensor for simple integration in the slurry preparation drum
- An overview of the SlurryTrack system: Data and insights from the sensor and a custom software
- Unique advantages, technical specifications, and in-depth experimental analysis on the suitability of inline sensors for ceramic slurries
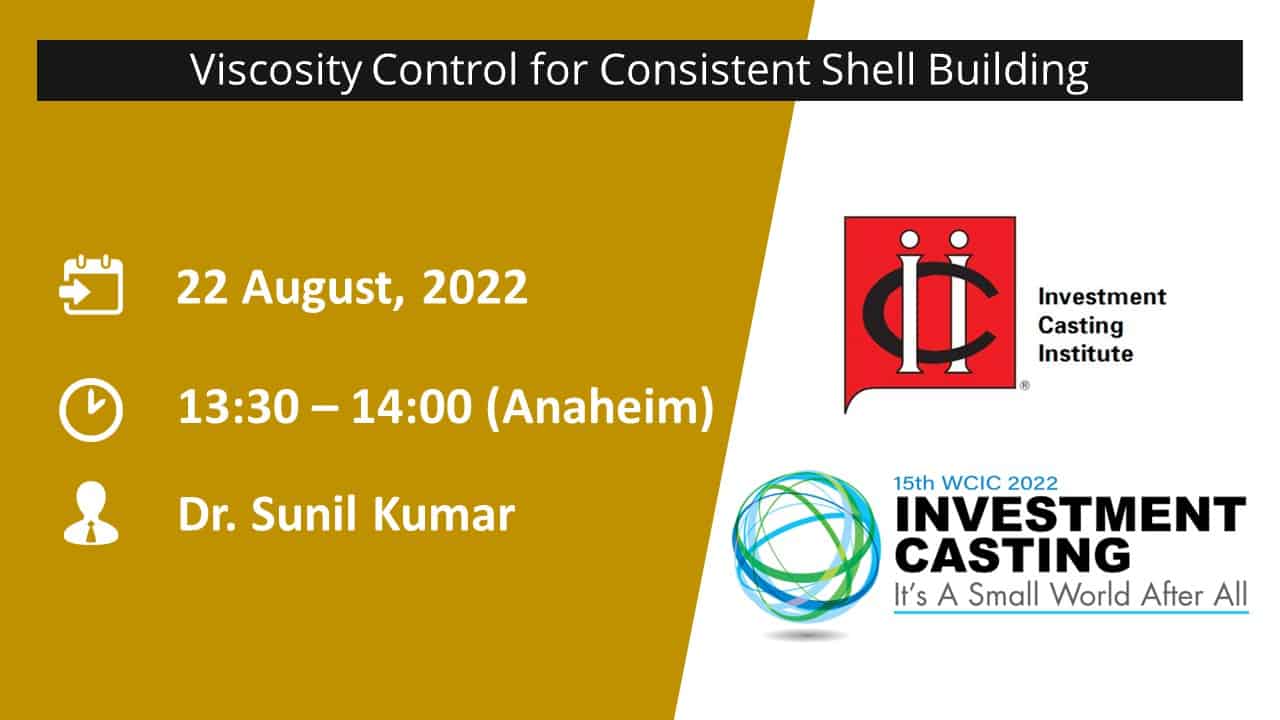
Speaker
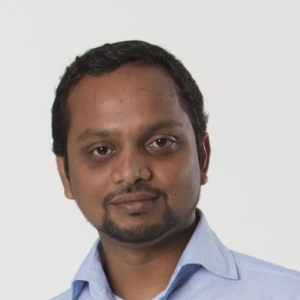
Dr. Sunil Kumar
CEO @ Rheonics
Sunil Kumar has extensive experience in the sensors and energy sector, having worked in a variety of roles in engineering and research in his early career. Most recently Sunil worked at Baker Hughes where he led global engineering for drilling Services. Sunil founded companies in US and UK that successfully commercialized innovative products. He graduated with Bachelors in Aerospace from Indian Institute of Technology, Kharagpur, Masters in Mechanical engineering from University of California, Irvine and Ph.D in Electrical engineering from Imperial College, London where he developed the Seis-SP seismometer that is part of the main payload for the NASA Insight mission to Mars. He is a prolific inventor with over 25 patents and multiple peer reviewed papers. Sunil’s vision of creating sensors for fluid property measurement that revolutionizes in-line process monitoring, control and optimization serves as the charter for rheonics.
Explore Rheonics' developments in this Industry
Rheonics’ InkSight wins 2022 Technology of the Year AIMCAL Awards
Association of International Metallizers, Coaters and Laminators (AIMCAL), founded in 1970, is a global nonprofit trade association representing converters of metallized, laminated and coated flexible substrates and their suppliers. AIMCAL announced Rheonics InkSight as a winner of the 2022 AIMCAL Award in the “Technology of the Year” category. Rheonics InkSight is a breakthrough multi-station ink viscosity & color control system…
AIMCAL’s Converting Quarterly Magazine features Rheonics Technology – “Ink viscosity optimization and automation – The key to quality, efficiency and sustainability in printing and coating”
Web processing & finishing focused magazine - Converting Quarterly (https://www.convertingquarterly.com/) publishes an in depth article about how SRV revolutionizes ink viscosity management in gravure printing and enables "getting it right the first time". In this article, readers can understand how printers improve color quality, reduce setup time and scrap and achieve sustainability in their operations with complete automation of ink…
Rheonics awarded Sustainable Innovation Packaging – Innovation Prize 2021 by European Rotogravure Association
Rheonics wins a Sustainable Packaging Innovation Award by the European Rotogravure Association. Dr. Sunil Kumar received the award at the Annual & Packaging and Decorative Gravure Conference in Thessaloniki, Greece on 21-23 September, 2021. “Gravure – the sustainable print process” was the theme of the conference, which pointed out an encouraging perspective for gravure’s future. Our viscosity automation technology ensures…
FTA Flexo Magazine features Rheonics FTA Technical Innovation Award winning Technology – “Excellence via Viscosity Control”
Flexographic printing focused magazine - Flexo (https://www.flexography.org/flexo-magazine/) publishes an in depth article showcasing the Rheonics SRV viscometers and the RPS InkSight Multi-Station Ink Control solution and how it enables excellence in color control in printing. Find the link to the publication.