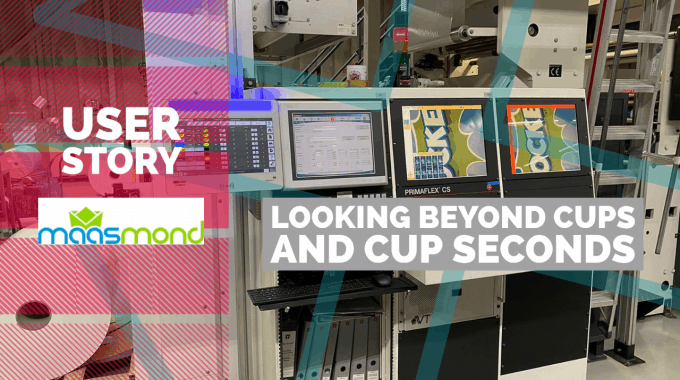
Maasmond BV achieves accurate printing color accuracy and consistency with Rheonics SRV and RPS InkSight system
DETAILS
Application
Printing quality control in flexographic printing and laminating units.
Challenge
- Cup viscosity measurements do not have the accuracy to counter viscosity related printing issues inside the press with simplicity
- Manual calibration of viscometers with a cup or some kind of reference is tedious and inefficient
Solution
- The Rheonics SRV viscometer gives ultra-stable, repeatable and accurate measurements without needing any re-calibration
- Apart from superior printing quality control, the sensor gives a lot of insights into the behavior of inks thus transforming the quality control operations to a whole new level.
- With the RPS InkSight, fully automatic printing quality control is made possible with extreme simplicity and intuitiveness
USER
Company: Maasmond BV
Location: Oostvoorne, Netherlands
Contact Person: Bert Verweel, Director & Owner
About the company
Maasmond is a family owned company (founded in 1969) with a 50 years’ experience in converting of paper and plastics. For the converting of food and non-food packaging’s and labels we have a broad range of modern narrow and wide-web flexographic printing presses (UV and solvent based inks), laminating (water and solvent based adhesives), slitting die-cutting and perforating machines. Maasmond produces a wide range of high-quality labels and flexible packaging which adhere to the highest food packaging standards.
- Could you please tell us about your company and its operations? How long has your company been in experience?
Response:
Maasmond is a family owned company (founded in 1969) with a 50 years’ experience in converting of paper and plastics. For the converting of food and non-food packaging’s and labels we have a broad range of modern narrow and wide-web flexographic printing presses (UV and solvent based inks), laminating (water and solvent based adhesives), slitting die-cutting and perforating machines. Maasmond produces a wide range of high-quality labels and flexible packaging which adhere to the highest food packaging standards.
- How and when did you come to know about Rheonics Printing Solution (RPS)?
Response:
I had been looking for replacement viscosity sensors for a few years. In December 2017, I came across website of Rheonics and what immediately appealed to me is the compactness, robustness (withstand high pressures and abrasive environments) and accuracy. In January 2018, during 2 days we tested a few sensors and we immediately realized that this sensor is phenomenal in terms of accuracy and stability. During these tests, we varied the amount of solvent and even the influence of retarder and accelerator could be registered.
- Prior to deploying the RPS, what were the main challenges you were facing and needed to solve?
Response:
The disadvantage of all existing sensors on the market is that they always have to be manually calibrated with a cup to have some kind of reference. Often when preparing and adjusting a color, the first question was is the viscosity correct and is the sensor calibrated. At that time, the viscosity of colors varied a lot (deviating values due to non-calibration), while now we work with fixed values and are therefore much faster on colour. The dosing of solvents was coarse causing a considerable viscosity deviation.
- Were you able to solve the challenges?
Response:
The biggest challenge was getting used to the mPa.s unit because we have been working with Din Cup “unity” for decades. In the beginning we converted mPa.s to Cup seconds, but soon we decided that this is nonsense, we have a sensor that works with the correct unit with repeatable values so let’s use it. Sensor has also given us a lot of extra knowledge about the behaviour of inks, even dare to say more than the ink suppliers know.
- What value did this system bring in terms of print quality, productivity, savings and ROI?
Response:
Just because of the accuracy of sensor and control, the viscosity is maintained extremely accurately during production, dE-values have become more constant and more accurate. For example: for repeat order, we use residual ink and dose the missing amount of ink and we can actually maintain the same viscosity value as the first time the color was printed. This gives a lot of confidence among the printers. Due to the knowledge gained and the behaviour of the ink on the substrates on which we print, we know which values for the viscosity must be adhered to, which saves a lot of time, reduces scraps and wastage (due to manual testing and setups).
The increased confidence on control over print quality with the RPS has enabled us to take on higher margin and higher quality jobs where the brand owners have very strict color specifications. We have a customer and a competitor who also supplies foil, its dE2000 values are between 4-5, ours below 2. Our selling price is higher than the competitor and in this case price determines the quality. We always strive for low dE2000 values in order to keep the quality level as high as possible and making it difficult for the competition. The system has other advanced capabilities such as the ability to detect the fouling/plugging of the printing line. These intelligent functionalities of RPS InkSight extends the lifetime of our printing presses by at least 2 years.
The system functionalities extend to effective fault analysis and troubleshooting. Last week, we experienced ‘Ghosting’ on our print jobs – which is mostly caused by failure of the anilox to consistently supply sufficient ink throughout the printing process. We solved this the problem by adding ethyl acetate (ensures that the ink dissolves well and dries faster) to the ink in a number of steps. Viscosity went down from 45 to 32 mPa.s. The viscosity in mPa.s has dropped sharply, however, if it were to be measured with a cup, no major change could be measured, maybe 0,5-1 s. Cups do not have the accuracy to effectively counter such issues inside the press with the simplicity and intuitiveness the RPS system empowers our operators.
The Dutch government requires to keep track of and proof how many solvent emissions Maasmond has, for which we must do emissions measurements and have solvent balance administration. We have seen the last 2 years that the consumption of solvents decreases, especially in 2020 we see a huge decrease. In that year, the laminator was equipped with the viscosity control of Rheonics, which resulted in a reduction of 21% of ethyl acetate.
- How easy/difficult was it to commission the RPS in your process? What are your comments about the functioning and usability of the system and software? Was it easy for your operators to understand and adapt to it?
Response:
Actually, the soft- and hardware are plug and play.
A key feature of the Rheonics SRV viscometer is its ease of integration inline which means lower installation costs and efforts. The SRV makes no demands on how it is installed. Due to the compact dimensions of the sensor, it hardly takes up any space. It does not generate any resistance in the supply line and it also keeps the sensor clean at all times. Vibrations caused by pulsations from pump or machine don’t have influence on the sensor, which is a major competitive edge over other similar systems. For example, with inkspec, the sensors must be set up in an isolated manner, otherwise vibrations (even the sensors mutually influence the measurement of each individual sensor) which is clearly visible at the machines where the inkspec sensors are used. This takes up a lot of space and makes installation expensive.
Last year we installed second RPS on the laminator, operators just needed a brief explanation. Operators were used thinking in cup seconds and once used to the new unit they know exactly what they are doing. The viscosities of 2-component adhesives are low and can deviate very quickly due to the high evaporation rate of ethyl acetate. The RPS InkSight software shows real-time what the viscosity is and the control provides compensation for the actual evaporation. Here, too, it applies that for different substrates certain viscosities must be used for the adhesive and that is now perfectly possible. What struck me is that the adhesives are prepared more accurately, at least the amount of ethyl acetate that has to be added to the recipe. The software immediately shows when too much or too little is being dosed, which was not the case before. Also, during operation when fresh adhesive is added to the bucket the operator sees what happens and it has become a challenge to prepare the adhesive as accurate as possible.
- Is there anything about the technology of the Rheonics solutions that you would like to specifically highlight? How accurately and reliably do these solutions perform inside the press in terms of your process goals?
Response:
When purchasing new sensors, my goal was to have accurate, compact sensors with little maintenance. In terms of accuracy and reliability the sensor and control have exceeded our expectations/goals and has led to improvements in color quality, efficiency and automation. After having evaluated, analysed, tested different solutions and technologies for printing quality management, I think RPS is an extremely valuable addition to our press – it makes the control of the most important variable – ‘ink viscosity’ super easy, intuitive and revolutionary in terms of accuracy. It sets a new benchmark in terms of accuracy. RPS is at least 10-15 times more accurate than other existing, leading ink viscosity controls in the market.
We print on a fairly large diversity of foils and paper, where different viscosities have to be handled and with the experience we have now tells us how much an ink has to be diluted for a certain colour strength. Often, we use a certain which is used to print on different substrates whereby different viscosities have to be used, for example printing on certain color on paper (high viscosity is needed) and this same color is used for printing on foil (relative low viscosity). We record for each order, per color the viscosity and which anilox cylinder was used, so we exactly know which viscosity to handle to have the correct color density resulting in faster setup time.
Another practical advantage with RPS is that very small amounts of solvent are dosed during the viscosity control to compensate for the actual evaporation. Most other systems require fairly large amounts of ink in the can to avoid viscosity fluctuation caused by dosing large amounts of solvent with relatively large periods. Large amount of ink causes stabilisation of the viscosity. In case of the RPS, amounts of up to 10 g are dosed. To be able to pump the ink through the system, we need at least 4 kg of ink and sometimes we only have 4.5 kg left as residual ink, while the viscosity has remained stable all the time because very small quantities are dosed. This means that less ink has to be prepared for an order and less residual ink is created. This also makes the RPS unique, keeping small amounts of ink at a constant viscosity.
In case of manually calibrated viscosity controls operators will often be inclined to use a different anilox cylinder with a different volume or by using varnish to influence the color strength resulting in longer setup times.
This ensures that we have actually achieved a kind of standardization printing colors on the different substrates. This saves a lot of time. With manually calibrated systems this is hard to do. Any operator needs to have the discipline to calibrate sensors before setup of the press and often does not have the time to do so.
- In your opinion, does the RPS deliver any unique proposition to the printing companies? Do you think Rheonics will be able to make an impact in the flexo printing industry with the RPS?
Response:
Firstly, it is the only sensor that has been calibrated from the supplier and then never needs to be calibrated again. With this sensor it is possible to store viscosity values, making automation possible. The most important variable is measured with sensors that does not need to be manually calibrated for each setpoint, which eliminates operator caused errors.
A good comparison of the Rheonics sensors with sensors available on the market is a laser distance meter and determining the depth of a well by dropping a stone and measuring the time it takes when it hits the bottom. With rock and clock, the well has a depth of 21,3 seconds, in case the well is not deep enough the guy with clock says “dig another 0,5 seconds” or in case of Rheonics, dig with an accuracy of a few mm.
If I speak to the salesman/technician of the ink and there are problems with a customer, it is almost in all cases because viscosity of the ink is much viscous. Even with colleagues when an error is detected during printing, it is usually that too much solvent is dosed in ink, which decreases the coloring strength.
One of the reasons everyone accepts that viscosity is expressed in seconds is that there were no “reliable, reproducible” sensors measuring in the correct unit, so there was no alternative.
I believe the RPS system elevates safety standards and automation possibilities inside the press and sets a new benchmark for printing companies in terms of quality, profitability, color precision and accuracy, ink and solvent consumption management, operators’ knowhow and control and environmental impact. I am certain that it’s going to make a mark in the Flexo printing industry, it brings the most crucial printing variable i.e. ink viscosity to the fingertips of the printers. Rheonics RPS and SRV sensor systems bring in the following significant advantages and unique proposition:
Technical advantages: Press automation, quality control, efficiency, accuracy & environment
- Much tighter, more accurate (by 10-15 times at least) control on ink quality when compared with other equivalent systems in market.
- Faster setup time and accurate color density – aided by experience and sensor repeatability, load job configuration functions of software
- Temperature compensated viscosity: lesser worries about seasonal variations, or any factor that can affect temperature (and so viscosity)
- Compensation for evaporation: tight control and ‘fine resolution’ of solvent addition in small steps – all leading to savings of solvent and ink
- Reduces setup time and setup scrap – operators can re-run a previously loaded job using the ‘Save job’ and ‘Load job’ functionality which reduces the wastage
- Effective fault analysis and troubleshooting – most issues in printing related to color and quality are attributed to the viscosity issues. The data from the sensors and the RPS system ensures efficient fault detection, comprehensive root cause analysis and effective corrective actions in a simple and intuitive way.
- Reduced solvent emissions and reduced scraps & wastages compared to manual handling and setups.
- Reduction in drying time and savings from reduced need for solvent recovery due to optimum usage of solvent in ink.
Installation and Usability
- Compact size: small footprint in press, unaffected by environment – vibrations etc. Other similar systems needs a significant installation effort and footprint inside the press. We just needed to install the sensor directly in the ink hose, using a off-the-shelf ¾” Tee.
- Software is intuitive, easy to use, valuable. On top of it, it is helpful in aiding operators’ knowhow about viscosity and color strength correlations – they now have a smart way of understanding, experimenting to enhance knowledge about behaviour of inks – helpful in current and future jobs. The software is made in collaboration with operators, which has resulted in a very user-friendly interface. Every now and then an operator wants to see how the viscosity has behaved during production of an order, how stable it was.
Profitability
- Savings in solvent and ink consumption (also record keeping of solvent consumption): Tighter control leads to lower solvent and ink consumption due to the innovative algorithm + system superiority.
- Reduced setup times leads to productivity improvement and capabilities to finish more print jobs in same time.
- Ability to take higher quality & higher margin jobs (dE<2) boosting profitability and giving a competitive edge
Some images of the RPS InkSight system
- Rheonics SmartView console integrated in printing machines
- Some pictures showing the SRV viscometers inline installation inside the press
- Standalone control cabinet
All Rheonics products are designed to withstand harshest process environments, high temperature, high level of shock, vibrations, abrasives & chemicals.
Related Articles
FTA Flexo Magazine features a Rheonics user case study – “Viscosity Standardization: One Printer’s Approach”
Flexographic printing focused magazine - Flexo (https://www.flexography.org/flexo-magazine/) publishes an in depth article showcasing the Rheonics SRV viscometers and the RPS InkSight Multi-Station Ink Control solution at a customer location in Netherlands. Find the link to the the publication.
Viscosity Standardization in Flexographic Printing
In the history of our company we have applied every type of viscosity sensor: rotational, falling ball, falling piston and acoustic wave. The similarity between these sensors is that they are all calibrated with a cup, in our case the DIN cup with a 4 mm outlet. In itself this worked well and due to lack of a better alternative…