- Real-time inline viscosity measurement in cardboard production is essential for continuous quality control, avoid waste and optimize energy consumption.
- Starch glue exhibits complex rheological behavior and its viscosity is not very stable across different batch. A viscosity measurement instrument is crucial to measure and optimize application of starch glue while ensuring consistent pseudoplastic and thixotropic behavior.
- Viscosity is an important indicator of PSD (Particle Size Distribution) – a property that affects flexibility, strength and usability.

Corrugated market – fast growing driven by eCommerce
Corrugated Board Industry is fast growing at a CAGR of more than 4% with volumes of more than 115 million tons valued in excess of $176 billion in 2019.
Packaging made from corrugated board is considered environmentally friendly and sustainable. It contains only natural raw materials (wood pulp, starch glue, and 80% recycled paper) and is therefore 100 percent renewable, recyclable and biodegradable. Even the process of processing and printing corrugated board is environmentally friendly because the inks are mainly water-based.
There are many types of boxes made by the corrugating industry, ranging from lightweight micro-flute up to heavy-duty multi-wall boxes. Low-cost, high-performance cardboard boxes are a versatile means of packing many different types of products, including machinery, electrical goods, fruit and vegetables, as well as a means of providing information and advertising about the contents.
Corrugated boxes must meet multiple demands, but it all starts with the production of a strong, flat board on the corrugator.
As important as the choice of papers is, the adhesive and its application are crucial to getting the best corrugated board at the end of the corrugating machine. To be effective on a wide variety of boards, glues must be versatile while maintaining quality bonding and high productivity. Adhesion between the liners and medium must be strong to provide strength and cushioning to protect the contents from the outside world and allow the box to maintain integrity through its life cycle.
All starch adhesives are based on a special property of starch: when subject to heat, starch slurry undergoes an extremely rapid increase in viscosity as the starch granules gel. This high viscosity, developed at a critical temperature, leads to the phenomenon of tack.
As the correct viscosity is crucial to the proper functioning of the starch, viscosity control can help improve the consistency and performance of these adhesives in many corrugated cardboard products such as:
- Shipping cases
- Corrugated sheets
- Retail merchandising
- Automotive and industrial packs
- Food packaging
- Product showcases
Product Showcases (Source: BCI)
What is the need for process control in corrugated board production?
Following paper production, corrugated board is the second largest application of non-food starches globally, where it is used as an adhesive between the fluting and liners. Many starch glues contain unmodified native starch, along with additives such as borax and caustic soda. Gelatinized starch carries uncooked starch slurry and prevents sedimentation. Such a glue is called an opaque SteinHall adhesive.
The production of modern corrugated packaging | Fefco
The glue is applied on the medium flute tips, after which the other paper component known as the liner is brought into contact and bonded. This is then dried under high heat, which causes the rest of the uncooked starch in the glue to swell/gelatinize. This gelatinization provides the final setting reaction making the glue a fast and strong adhesive for corrugated board production.
White Paper – Corrugated Box and Starch (tuthillpump.com)
The quality and integrity of the product inside the box relies on the stability of the packaging. And a box’s ability to protect the contents inside often depends on the strength and proper application of the adhesive.
Starch application viscosity control solutions help to ensure that each batch of adhesive has the right consistency and that it is applied in the right quantities and positions during the gluing of the flutes to the liners. An inline viscometer is used to optimize and consistently maintain the correct starch thickness for the adhesive layer.
The following problems may arise in your cardboard manufacturing process if you use manual viscosity measurement methods or other approaches that do not control viscosity adequately:
- Soft board
- Streak of heavy glue
- Washboard appearance
- Leaning corrugations
- Spotty adhesion
- Loose edges
- Blisters
- Unglued components
- Slinging or dribbling
Manual viscosity measurements using a cup in the production floor
Importance of viscosity and density monitoring and control to ensure high quality starch adhesion
Corrugated paperboard production depends highly on adhesion, which has the greatest impact on its quality. It is the quality of starch glue that ultimately determines the quality of adhesion. Viscosity is an important metric of starch glue, and the amount of viscosity directly affects the adhesion of corrugated boards. Stable viscosity is the only way to ensure good adhesion properties of starch glue.
Components and production of starch adhesives
When the viscosity of starch/adhesive is outside the optimal range, it creates imperfections and reduces the quality of the intermediate and end products. An adhesive with sufficient viscosity will prevent blankets and papers from being impregnated, thereby improving their quality.
Most recipes for starch glue for corrugated plants consist of:
- Starch
- Borax
- Caustic
- Water
These ingredients are mixed and heated to achieve a target viscosity. Factors affecting starch viscosity are type and quality of starch, oxidant dosage and oxidation time, oxidation temperature, dosage of gelatinizer NaOH (Sodium Hydrooxide), borax dosage, water ratio and storage temperature, time and environment. With so many parameters and constituents to get right during starch production/formulation, it pays back quickly to monitor the end-product (starch) to ensure batch consistency.
Viscosity is an important indicator of the particle size distribution. Changes in the particle size distribution can affect properties such as density, rheology and layer thickness. Properties related to particle size distribution in starch are, for example, the flexibility, strength and usability of the (corrugated) cardboard.
The starch glue belongs to the polymer product family. There are two types of glucose polymers in starch: linear and helical amylose and branched amylopectin. Depending on the plant, starch contains 20% to 25% amylose and 75% to 80% amylopectin. Since amylose fractions aren’t truly soluble in water, they eventually form crystalline aggregates by hydrogen bonding – a process called retrogradation or setback, which makes viscosity unstable. It exhibits complex rheological behavior. Inline viscosity monitoring can catch when the starch formulation has gone bad or is non-optimal for application.
Graph 1 illustrates the viscosity evolution of a starch-based glue after it has been applied onto the flute tips and brought into contact with the liner. (Source: Roquette)
Why automate incoming material inspection and application of adhesives, glues, paste and hot melts?
There are many different types of adhesives, including viscous liquids, paste, crystalline and amorphous solids. Furthermore, adhesives are typically packaged in cartridges, pails, drums, totes, pellets, and blocks. It is critical for a production process to have a steady flow of adhesive from the adhesive container into the dispensing equipment to keep it running continuously. Hot melt adhesives are solids at room temperature, so they are usually removed manually from boxes by scooping and then added to melting equipment to be dispersed during the melting process.
If not carefully monitored, manual handling creates additional tasks for operators, runs the risk of contamination during handling, and leaves open the possibility of spills or even process downtime. A steady consumption of hot melts also minimizes the heat history of the adhesive, which enables maximum performance and quality in the production process.
Benefits of viscosity automation in corrugating process
Solutions that automate adhesive delivery are gaining popularity as more manufacturers realize the benefits and quick ROI, including:
- Efficiency: The highly precise nature of automated equipment ensures the right amount of adhesive is delivered to match the process demand.
- Reliability: Automated feeders ensure a consistent flow of the correct adhesive to the production line, independent of shift patterns, downtime, production speeds. An inherently closed system also avoid contaminants, reduces waste, and minimizes equipment maintenance.
- Safety: By using auto-feed systems, and eliminating manual handling of hot melt adhesives, you reduce the potential exposure to high temperature materials and equipment.
- Decreased operational costs: Less operator time spent monitoring and filling adhesive tanks with less chance of errors or downtime.
- Digitalization: Equipment monitoring sensors provides additional process data enabling optimization and problem identification to improve efficiency.
Rheonics’ solutions for quality control and assurance of starch glue in packaging
Automated in-line viscosity measurement and control is crucial to control the viscosity during manufacturing process and ensure critical characteristics are in full compliance with requirements across multiple batches, without having to rely on offline measurement methods and sample taking techniques. Rheonics offers the following solutions for process control and optimisation,
Viscosity & Density Meters
- In-line Viscosity measurements: Rheonics’ SRV is a is a wide range, in-line viscosity measurement device capable of detecting viscosity changes within any process stream in real time.
- In-line Viscosity and Density measurements: Rheonics’ SRD is an in-line simultaneous density and viscosity measurement instrument. If density measurement is important for your operations, SRD is the best sensor to cater to your needs, with operational capabilities similar to the SRV along with accurate density measurements.
Integrated, turnkey quality management
Rheonics offers an integrated turn-key solution for quality management made of:
- In-line Viscosity measurements: Rheonics’ SRV – a wide range, in-line viscosity measurement device with in-built fluid temperature measurement
- Rheonics Process Monitor: an advanced predictive tracking controller to monitor and control in real-time variations of process conditions
- Rheonics RheoPulse with automatic dosing: A Level 4 autonomous system that ensures no compromise with set limits of viscosity and automatically activates by-pass valves or pumps to adaptively dose mixture components
The SRV sensor is located in-line so it continuously measures the viscosity (and density in case of SRD). Alerts can be configured to notify operator of necessary action or the entire management process can be fully automated with RPTC (Rheonics Predictive Tracking Controller). Using an SRV in an manufacturing process line, results in improved productivity, profit margins and achieves regulatory conformance. Rheonics sensors have a compact form factor for simple OEM and retrofit installation. They require zero maintenance or re-configurations. The sensors offer accurate, repeatable results no matter how or where they are mounted, without any need for special chambers, rubber seals or mechanical protection. Using no consumables and not requiring re-calibration, SRV and SRD are extremely easy to operate resulting in extremely low lifetime running costs.
Once the process environment is established, there is usually little effort required to maintain the integrity consistency of the systems – operators can rely on the tight control with Rheonics production quality management solution.
Watch Rheonics SRV in action on a laminator using water based adhesive
Superior sensor design and technology
Sophisticated, patented electronics is the brain of these sensors. SRV and SRD are available with industry standard process connections like ¾” NPT, DIN 11851, Flange and Tri-clamp allowing operators to replace an existing temperature sensor in their process line with SRV/SRD giving highly valuable and actionable process fluid information like viscosity besides an accurate measurement of temperature using an in-build Pt1000 (DIN EN 60751 Class AA, A, B available).
Electronics built to fit your needs
Available in both a transmitter housing and a small-form factor DIN rail mount, the sensor electronics enables easy integration into process lines and inside equipment cabinets of machines.
Easy to integrate
Multiple Analog and digital communication methods implemented in the sensor electronics makes connecting to industrial PLC and control systems straightforward and simple.
Analog and Digital Communication Options
Optional Digital Communication Options
ATEX & IECEx Compliance
Rheonics offers intrinsically safe sensors certified by ATEX and IECEx for use in hazardous environments. These sensors comply with the essential health and safety requirements relating to the design and construction of equipment and protective systems intended for use in potentially explosive atmospheres.
The intrinsically safe and explosion proof certifications held by Rheonics also allows for customization of an existing sensor, allowing our customers to avoid the time and costs associated with identifying and testing an alternative. Custom sensors can be provided for applications that require one unit up to thousands of units; with lead-times of weeks versus months.
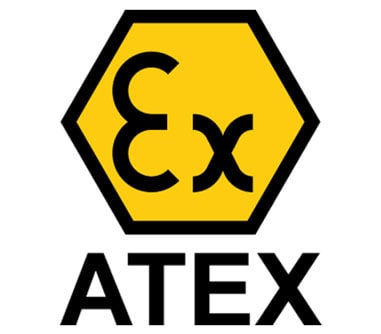
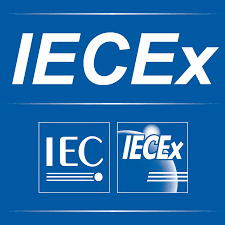
Implementation
Directly install the sensor in your process stream to do real-time viscosity and density measurements. No bypass line is required: the sensor can be immersed in-line; flow rate and vibrations do not affect the measurement stability and accuracy. Optimize mixing performance by providing repeated, consecutive, and consistent tests on the fluid.
Rheonics SRV and RPS Controller Deployed in a laminator press
Rheonics Instrument Selection
Rheonics designs, manufactures and markets innovative fluid sensing and monitoring systems. Precision built in Switzerland, Rheonics’ in-line viscometers and density meters have the sensitivity demanded by the application and the reliability needed to survive in a harsh operating environment. Stable results – even under adverse flow conditions. No effect of pressure drop or flow rate. It is equally well suited to quality control measurements in the laboratory. No need to change any component or parameter to measure across full range.
Suggested product(s) for the Application
- Wide viscosity range – monitor the complete process
- Repeatable measurements in both Newtonian and non-Newtonian fluids, single phase and multi-phase fluids
- Hermetically sealed, all stainless steel 316L wetted parts
- Built in fluid temperature measurement
- Compact form-factor for simple installation in existing process lines
- Easy to clean, no maintenance or re-configurations needed
- Single instrument for process density, viscosity and temperature measurement
- Repeatable measurements in both newtonian and non-newtonian fluids, single phase and multi-phase fluids
- All metal (316L Stainless Steel) construction
- Built in fluid temperature measurement
- Compact form-factor for simple installation in existing pipes
- Easy to clean, no maintenance or re-configurations needed