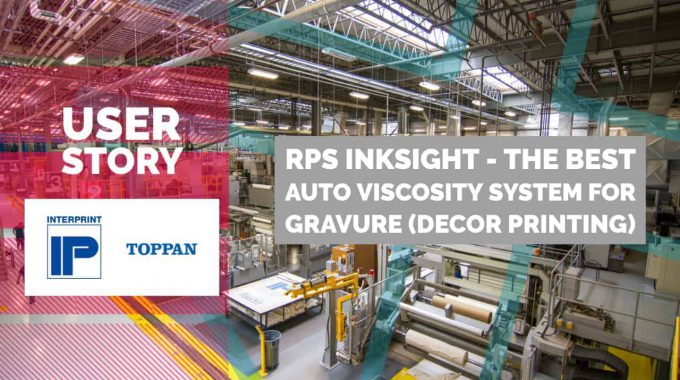
Interprint, Inc. optimizes and automates printing operations in the decorative gravure market segment with the RPS InkSight auto viscosity control
DETAILS
Application
Printing quality control in the decorative gravure market segment – flooring, counter tops, paneling, cabinets.
Challenge
- Cup viscosity measurements do not have the accuracy to counter viscosity related printing issues inside the press with simplicity
- Skilled printers left/promoted off press and the skill level of new printers diminished, making viscosity management with cups unreliable.
- With other automatic viscosity management systems, the operators lost confidence in the performance of these systems (incorrect dosing) and basically stopped using them.
Solution
- The Rheonics SRV viscometer gives ultra-stable, repeatable and accurate measurements without needing any re-calibration
- InkSight sensor was positioned in print unit which is the most critical for design aesthetics, color and due to the very light tonal scale prone to print issues if the ink is not controlled, monitored and maintained. The RPS InkSight and SRV sensor held the viscosity over the duration of the entire order within 0.5 cP.
- With the RPS InkSight, fully automatic printing quality control is made possible with extreme simplicity and intuitiveness.
- Set it and forget it operation- The operators have full confidence in this system, we have had several occasions where we did not have a press crew to run the press at night so instead of shutting the press down and washing up we opted to leave the viscosity control system on with the cylinders in the press spinning and the ink circulating through the system. We came in the next morning and we were able to start right back up.
USER
Company: Interprint, Inc.
Location: Pittsfield, MA 01201, USA
Contact Person: Todd Luman, Laser Engraving Manager
About the company
INTERPRINT (part of TOPPAN group) is one of the world´s leading decor printers. Interprint produces with 30 production presses with a total capacity of 1.7 billion square metres at 8 production sites in Germany, the United States, Poland, Malaysia, China, Russia and Brazil and has approximately 1,300 employees worldwide. It is headquartered in Arnsberg, North Rhine-Westfalia / Germany.
Interprint decorate the surfaces of numerous materials in the segment of derived timber products, including living room, kitchen and bathroom furniture, laminate flooring and for interior furnishing in trains, ships or in the recreational vehicle industry. Interprint operates in the decorative Gravure market segment. Their product range is flooring, counter tops, interior/exterior paneling, cabinets and other like applications. Their décors decorate the surfaces of numerous wood-based panels that are processed into furniture and flooring and used for interior finishing. They are a 100% water based ink printer with full coverage continuous tone-on-tone designs printing on various saturating grade base papers and a variety of film substrates for wide web printing (ranging in width from 4’- 8’).
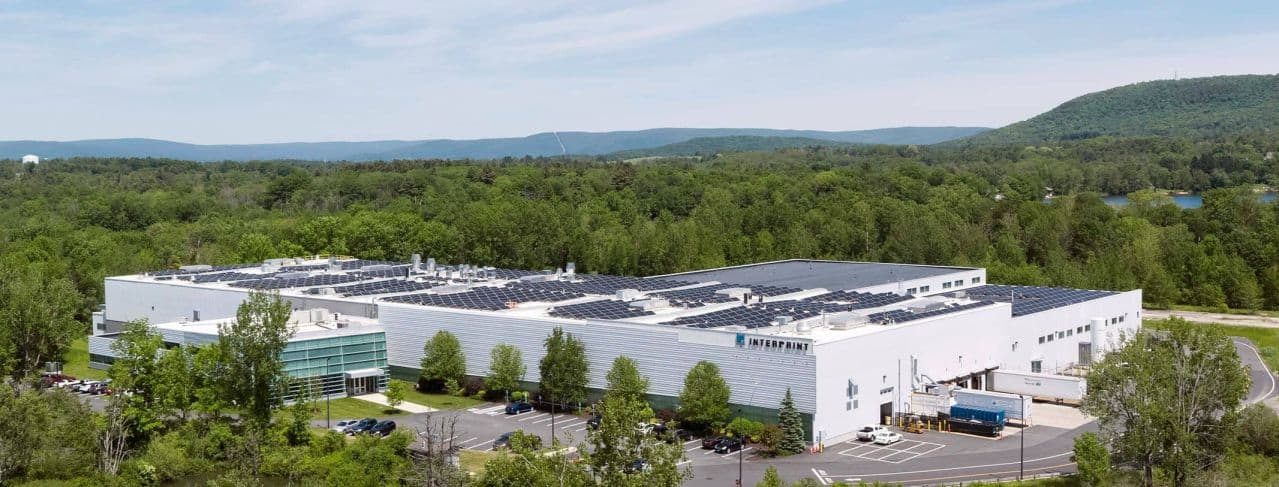
Interprint, Inc. Pittsfield, MA, USA location operating in the gravure printing market segments for decor printing and thermoplastic foils (Image Source: Interprint USA)
USER TESTIMONIAL
At Interprint we operate in the decorative Gravure market segment. Our product range is flooring, counter tops, interior/exterior paneling, cabinets and other like applications. We are a 100% water based ink printer with full coverage continuous tone-on-tone designs printing on various saturating grade base papers and a variety of film substrates for wide web printing (ranging in width from 4’- 8’).
In past years, prior to incorporating an auto viscosity process control system we had a pressroom full of experienced printers who lived and died by the viscosity value they measured with a #4 Frikmar viscosity cup. Due to the skill level of our print-staff at this time it was a hard sell to get them to buy into having an auto viscosity system control the quality of their ink. It is worth mentioning the size of our ink delivery vats. These are 750- 1000 Liter in ground vats (large quantity of ink).
As the years past and skilled printers left or were promoted off of the press, the skill level of new printers diminished also the auto viscosity control systems available in the market place advanced.
In 2013-14 we purchased our first auto viscosity control system and immediately saw a positive impact on color stability. As we progressed and invested in more of these systems for our other presses we began to run into some inconsistencies and performance issues. It reached the point where the operators got burnt too many times by the system incorrectly dosing and washing out the color. Over time, the operators lost confidence in the performance of these systems and basically stopped using them. (You can image how frustrating this is to have an investment of this size sit idle).
In 2017 we had an opportunity to test a demo unit of the Rheonics RPS InkSight on one of our print stations. The production order was for 44 rolls of 2.1 meter wide PVC (3000 meters per roll of film). The InkSight sensor was positioned in our last print unit which is the most critical for design aesthetics, color and due to the very light tonal scale prone to print issues if the ink is not controlled, monitored and maintained. The RPS InkSight sensor held the viscosity over the duration of the entire order within 0.5 cP. The other print stations that were not being controlled the operator had to chase the color and adjust the ink thorough out the run while the print unit the RPS controller was in ran flawlessly. We were fortunate enough to be able to hold onto the sensor for several months to allow us the ability to run the gamut of our testing across our different product/ink segments. Time and time again the result were outstanding!
Set it and forget it operation– The operators have full confidence in this system, we have had several occasions where we did not have a press crew to run the press at night so instead of shutting the press down and washing up we opted to leave the viscosity control system on with the cylinders in the press spinning and the ink circulating through the system. We came in the next morning and we were able to start right back up.
– Todd Luman, Laser Engraving Manager, Interprint, Inc.
In 2018 we were investing in a new press build and it was a no brainer that the new press was to be equipped with the Rheonics RPS inkSight viscosity control. Since this time, we have had the opportunity to gain more user experience with the system and can report the operators are fully vested in the InkSight. We have found several key process advantages to using this system over our other viscosity control system.
Advantageous for the RPS sensor
- Ease of use
- Do not need to calibrate for every use as did our other system require.
- Temperature compensation for predictive logic precise dosing.
- Set it and forget it operation– The operators have full confidence in this system, we have had several occasions where we did not have a press crew to run the press at night so instead of shutting the press down and washing up we opted to leave the viscosity control system on with the cylinders in the press spinning and the ink circulating through the system. We came in the next morning and we were able to start right back up.
- Another key feature is the reporting and event tracking, this is key for us to monitor and see how the system performed over the run.
Lastly with any new product we purchase a big part of the investment decision and future product purchases has to do with the type of technical support provided by the manufacturer. The technical support offered by Rheonics software engineer Maybemar has been outstanding, easily accessible, responsive and extremely competent.
In conclusion, I would highly recommend considering the Rheonics RPS InkSight for a Technical innovation award. In my professional opinion, there is not another viscosity control system on the market place today that can match the results we have experienced to date with the Rheonics RPS sensor. It is a new technology that separates itself from the others. In stating this, I am not saying the other viscosity controllers in the market place are bad by any means, they do work and work well however I have not had the same level of performance as displayed by the Rheonics RPS controller due to their technology product advancements.
– Todd Luman, Laser Engraving Manager, Interprint, Inc.
USER TESTIMONIAL
Some images of the RPS InkSight system
- At Interprint, the Software has been integrated in the press HMI
- Some pictures showing the SRV viscometers inline installation inside the press in the ink delivery system
All Rheonics products are designed to withstand harshest process environments, high temperature, high level of shock, vibrations, abrasives & chemicals.
Related Articles
Rheonics InkSight and SRV technology wins the FTA Technical Innovation Awards 2021
It’s an incredibly proud moment for all of us here at Rheonics to announce that the Rheonics’ InkSight technology has been selected by Flexographic Technical Association for the prestigious 2021 FTA Technical Innovation Award. For over 20 years, the FTA Technical Innovation Award has recognized the most innovative and impactful technologies for the ever-evolving package printing and converting industry. The recipients of…
FTA Flexo Magazine features a Rheonics user case study – “Viscosity Standardization: One Printer’s Approach”
Flexographic printing focused magazine - Flexo (https://www.flexography.org/flexo-magazine/) publishes an in depth article showcasing the Rheonics SRV viscometers and the RPS InkSight Multi-Station Ink Control solution at a customer location in Netherlands. Find the link to the the publication.