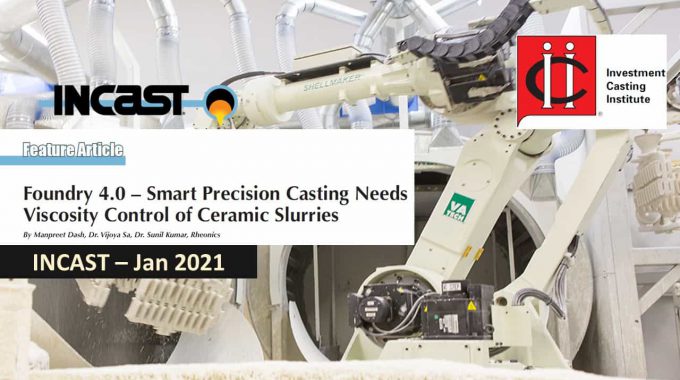
INCAST features Rheonics – “Foundry 4.0 – Smart Precision Casting Needs Viscosity Control of Ceramic Slurries”
Overview
Investment casting industry focused magazine – INCAST Mag (https://www.investmentcasting.org/current-issue.html) publishes a feature article covering the Rheonics inline viscometer SRV and the integrated solution – Rheonics Slurry Monitoring and Control System. The article discusses why slurry viscosity is critical in shell building and how it can monitored and controlled for building top quality, defects-free shells even under varying temperatures and evaporation conditions through automation.
Find the link to the the publication.
To download the full article, please use the link below.
Introduction
Ceramic Slurry for Shell Building – Viscosity is Crucial to Getting Reliable Slurry
Viscosity control can help alleviate the frequency of defects in the coating process – sticking and picking, twinning, peeling, splitting, cracking, roughness, blistering, bridging, surface erosion and reduce poor flow characteristic which lead to poor shell build resulting in casting defects. With continuous online viscosity monitoring, shell formation can be controlled more effectively, therefore significantly improving the metallurgical properties of the final product.
A good slurry composition alone cannot guarantee production of smooth and defect free shell if the slurry is prepared in an inadequate manner. Slurry quality control is one of the most important operations of the investment casting process, with viscosity control of the slurry being key to ensure compliance. Inline viscosity management with the Rheonics sensors can help alleviate most common issues like ceramic inclusion, crack, distortion, flash, misrun, shrinkage, slag inclusion and cold shut that can negatively impact the quality of final products.
Smart Foundries – Drivers for Casters’ Embrace of Industry 4.0 and Digitalization
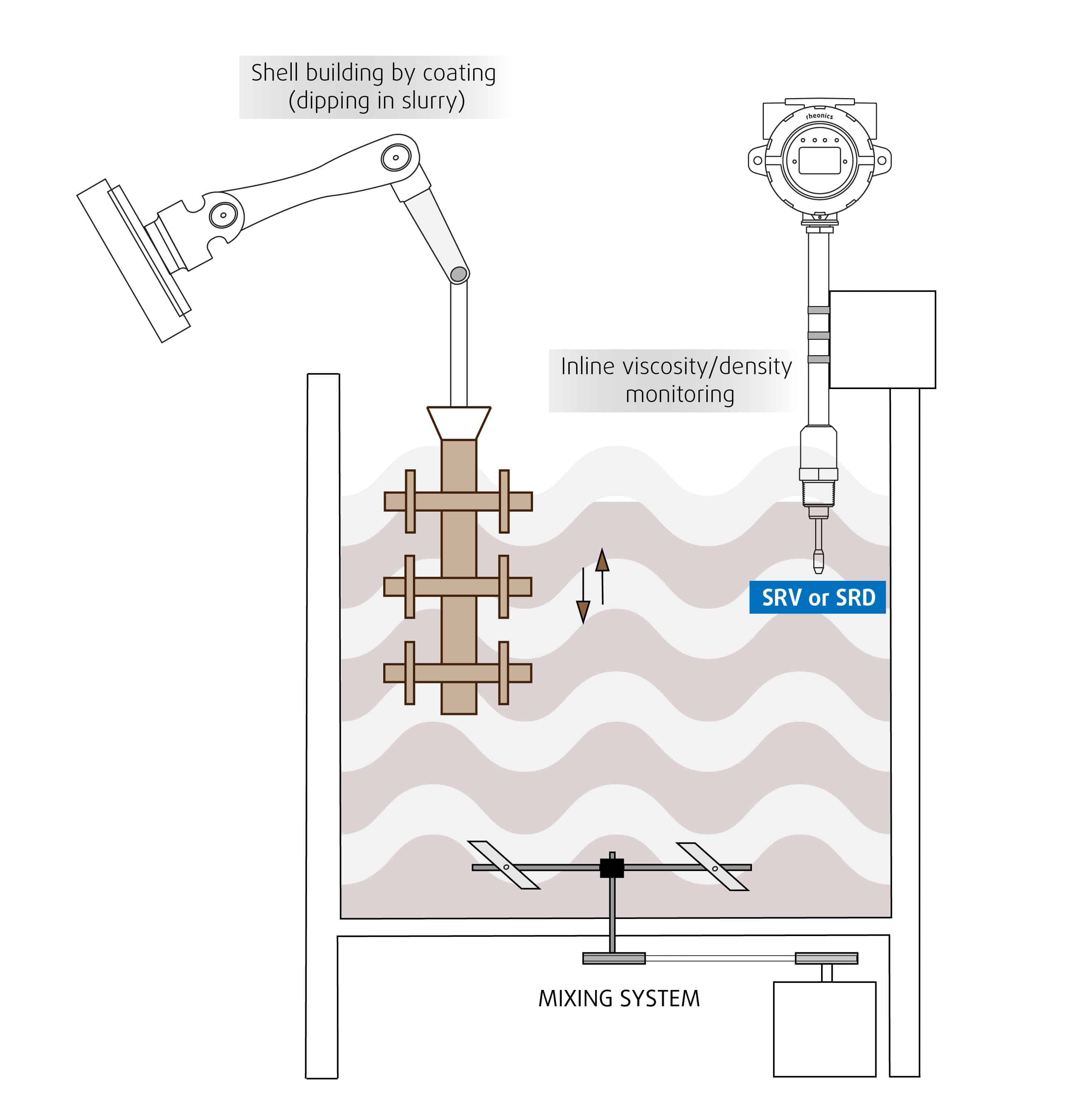
The key value drivers of embracing real-time inline viscosity monitoring equipment by manufacturers and system integrators operating in ceramic slurry coating for shell building:
Automated corrective actions for ensuring product consistency. Closed control loops through sensor-based, in-line quality inspection reduce waste and increase yield through early process deviation detection, root cause analysis, and automatic correction.
More agility in dealing with new product variants in production, compliance and product provenance. Casting manufacturers get a more accurate picture of how the new slurry formulations will behave and how they might need to adjust current systems and control parameters.
Big data provides robust evidence to base decisions for greater efficiency. The data provided by the process monitoring equipment enables them to tweak various process parameters and optimise the manufacturing process. Interconnection and information transparency allow for operators to make decisions both inside and outside of production facilities, thus enabling decentralization of decisions.
Higher customer satisfaction and adapting to customer requests. Industry 4.0 solutions can impact casting companies by driving closer interactions with their customers. The technology, data, and information that can help transform manufacturing operations can also make processes and systems more responsive to customer needs.
To know more about why food manufacturers are looking to integrate automation solutions in their production/factory floors, please read our article titled – “Smart foundries – drivers for casters’ embrace of Industry 4.0 and digitalization”
Unique advantages with the Rheonics SRV sensors
Rheonics sensors have built-in temperature measurement, permitting the temperature of the batter to be monitored at the point of application. This permits the viscosity readings to compensated for temperature, which is essential for ensuring consistent production through typical daily and seasonal temperature variations.
There are many benefits to using an inline viscosity sensor like the SRV for batter mixing and coating applications. and some include:
- Operates accurately in almost all coating systems with a broad range of composition/formulations
- Maintains the set slurry viscosity in mixing tanks regardless of temperature and humidity fluctuations, mixing equipment condition, substrates, solvents, formulations or dosing of colloidal silica, water and/or polymers, wetting agents, anti-foaming agents, and refractory flours.
- Rugged, hermetically sealed sensor head. Sensor probe can be cleaned inline with all standard CIP/SIP processes, or with a wet rag manually, without the need for disassembly or re-calibration
- All wetted parts are 316L stainless steel – no corrosion problems
- Certified under ATEX and IECEx as intrinsically safe for use in hazardous environments
- Wide operational range and simple integration—Sensor electronics and communication options make it extremely easy to integrate and run in industrial PLC and control systems.
To explore more about our solutions for ceramic slurry quality control, please read the application note.
Monitoring and controlling viscosity of ceramic slurries in investment casting
Investment castings are one of the most popular production methods for metal parts today. Investment casting process, also termed as a lost wax process, is relatively simple, which enables rapid production rates while ensuring consistent dimensional accuracy. Parts that are typically made by investment casting…
Conclusion
With huge application areas and growing demand from the end-use sectors, this industry is looking for new ways to improve efficiency, lead time, and capacity utilization. Industry leaders across sectors are moving towards adoption of more advanced
technologies such as automation, industrial internet of things (IIoT) and simulation techniques. Inline viscosity monitoring solutions help investment casters achieve advanced process control over the slurry preparation (mixing) and coating process to build top-quality and defect-free shells with more real-time insights into their processes; and reap the benefits of Industry 4.0 and automation such as reduction in lead times, enhance capacity utilization, reduce scraps and wastes and optimize efficiency.
Key takeaways:
- Inline viscosity control with the SRV and Rheonics Slurry Monitoring & Control system enables continuous viscosity control, making necessary dilutions in real time. Slurry quality in shell building is guaranteed regardless of temperature fluctuations, mixing equipment condition, formulations, process step interactions and mixing time parameters.
- Rheonics SRV and Production Monitoring and Control system control true temperature-compensated viscosity, which is essential for ensuring consistent shell building through typical daily and seasonal temperature variations.
Using the SRV sensor in slurry mixing results in improved productivity, profit margins and regulatory compliance.
Once the process parameters are established, there is little effort required to maintain the integrity of the process. Operators can rely on the tight control provided by the Rheonics slurry quality management solution and reap benefits not only in production, but also the product R&D stage when the formulation parameters are established. This enables the operator to gain competitive advantage as production is scaled up to meet increasing demand.