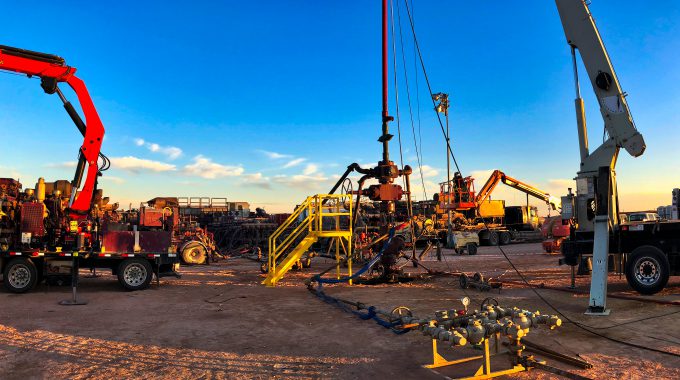
Getting Frac Fluid Rheology Right!
Application
Hydraulic fracturing (also called as fracking, fracing, hydrofracturing) involves high-pressure injection of ‘fracing fluid’ (primarily water, containing sand or other proppants suspended with the aid of thickening agents) into a wellbore to create cracks in the deep-rock formations through which natural gas, petroleum, and brine will flow more freely. The main functions of these fluids are to open/propagate the fractures and transport proppants into the fractures. This technique has been used by the oil and gas industry as a way to boost hydrocarbon production since 1947.
The tremendous increase in hydrocarbon productivity resulting from the vast network of fractures created during the process has made it economically feasible for the oil and gas industry to tap into the vast hydrocarbon resources in previously undeveloped tight unconventional reservoirs.
Why is viscosity important in well fracking?
The fluid that is used to pump down the well to accomplish the high pressure frack is mixed with proppant (usually fine sand) on the surface before going to the high-pressure pumping system. The fluid has to be able to hold the proppant in solution until it gets to the perforations down hole in the well where it goes out into the formation. Proppants form a thin layer between the fracture faces to keep the fractures open at the end of the fracturing process. Without proppants, the fractures will close after the pumping of fracturing fluids under high pressure is ceased, resulting in minimal or no gain of hydrocarbon productivity. Usually, viscous hydraulic fracturing fluids (e.g., polymers or gels) are required to ensure proper proppant transport and the even distribution of proppant along the fractures.
Therefore, getting the viscosity of the fluid/sand mix to the right point is critical to ensure that the important function of fracturing fluid to carry and transport proppants into the fracture is achieved.
Rheonics' solutions for continuous inline viscosity measurements
Rheonics in-line viscometer and density meter are built by a team that cut its teeth on building the worlds first commercially available downhole density and viscosity sensor. The Frac fluid viscosity and density sensors are built to operate reliably in the high pressure and high flow rate environment encountered in fracking operations.
SRV and SRD are non-nuclear sensors, one of its kind that can be installed directly at the frac fluid mixing pump and injection pumps. With these sensors, frac fluid can be monitored continuously through the complete mixing, pumping and backflow operations. Installing the sensors at rig-sites is straightforward with variety of available flow through adapters, extended arms for installation in tanks, etc.
In addition, the SRV and SRD
- Operates across the complete viscosity range including from water to the viscosifier gel
- High pressure operation – operational to 5000 psi and even 10,000 psi (700 bar)
- High temperature operation to 550 °F (300 °C)
24x7x365 assistance in easy and low-cost implementation from the team that designed the sensor.
Rheonics’ SRD has all features of the SRV along with additional density measurements. It is a unique product that replaces three different instruments with one single instrument for viscosity, density and temperature measurements. It eliminates the difficulty of co-locating different instruments and delivers extremely accurate and repeatable measurements in harshest of conditions.
Improve Production with Optimized viscosity
Whether it is hybrid guar based linear gel frac fluids or viscous slickwater, getting the viscosity correct increases the amount of proppant you can transport to the fracture. Operators have reported production improvement of 35% and higher from increased proppant concentration, operation efficiency of running a controlled frac fluid injection and reduced stage spacing that comes from better control on fracing operations.
- Increase production and ROI
- Improve operational efficiency by using an aggressive pumping schedule
- Reduce stage spacing
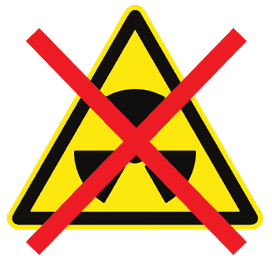
Rheonics FracRight Software
Rheonics’ FracRight software monitors and controls the density and viscosity of the frac fluid giving the operator fine control over the consistency of the frac fluid rheological characteristics. The system operates using single touch lock-in of the frac fluid property and ensures consistent fluid is pumped down the well through-out the operation. Communication over ethernet, wireless and modbus enables seamless transmission of information from FracRight to customer PC or Cloud.
Rheonics in Oil & Gas
Rheonics is a leader in harsh environment density and viscosity monitoring and control. It provides oil & gas industry with high-pressure high-temperature sensors and solutions that are used in cementing, reservoir analysis, drilling mud monitoring & control, sand level detection in separators and frac fluid rheology optimization.
ATEX and IECEx Compliance
SRV and SRD are intrinsically safe sensors certified by ATEX and IECEx for use in hazardous environments. These sensors comply with the essential health and safety requirements relating to the design and construction of equipment and protective systems intended for use in potentially explosive atmospheres. The intrinsically safe and explosion proof certifications held by Rheonics also allows for customization of an existing sensor. Custom sensors can be provided for applications that require one unit up to thousands of units; with lead-times of weeks versus months.
Rheonics SRV & SRD are both ATEX and IECEx certified. (Read more)
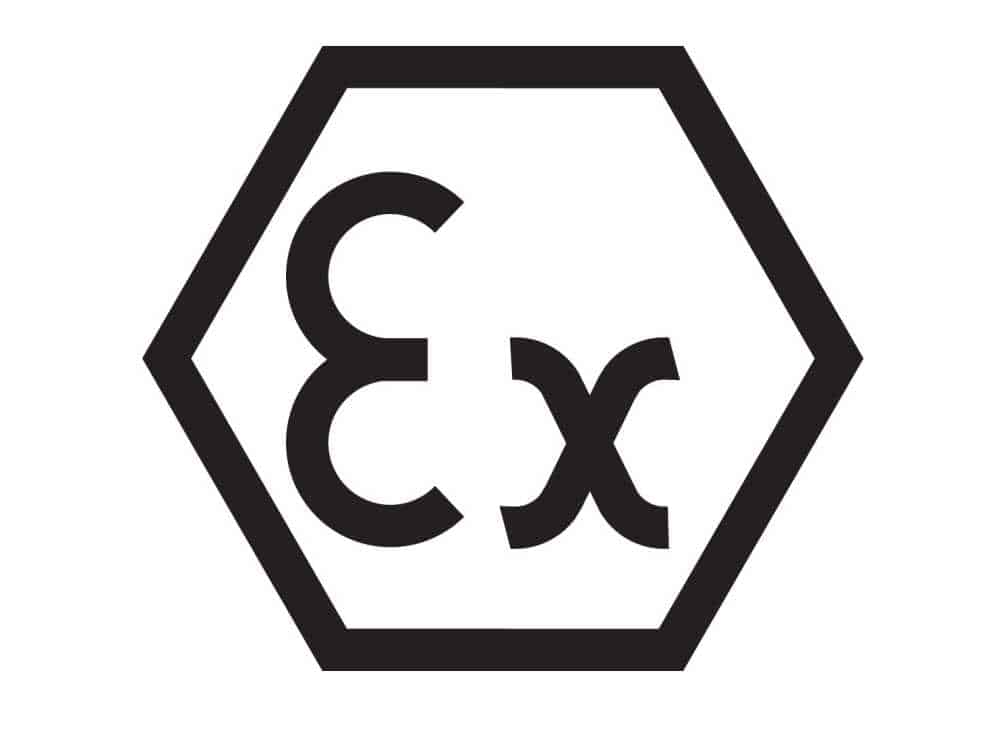
Rheonics density meters and viscosity meters are available as probes and flow-through systems for installation in tanks, process lines and reactors. All Rheonics products are designed to withstand harshest process environments, high temperature, high level of shock, vibrations, abrasives & chemicals.