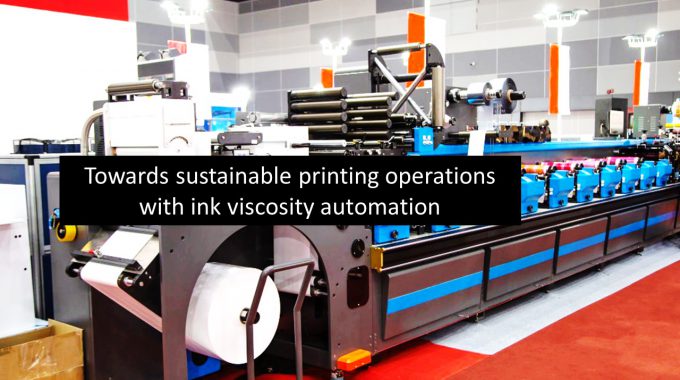
Achieving sustainability goals in printing with complete viscosity automation solutions
Achieving sustainability goals in printing with complete viscosity automation solutions
Concerns about the economy, technological threats, and unclear futures have all contributed to a print confidence crisis. Add to that quickly shifting consumer expectations and media options, and you have an industry that has been on the defensive for some years. However, a change is in the works. Print is redefining itself to be a more dynamic force in a multichannel communications landscape than ever before.
Years of upheaval have compelled printers to improve their processes, reduce waste, and increase process automation and efficiency. Print is a highly sustainable and effective media due to its streamlined process management and reliance on a renewable resource. Rising environmental consciousness is causing ecologically conscious media consumers to emphasis on print.
However, market uncertainty can be exacerbated by sophisticated new media possibilities, digital technology deployments, and green aspirations. Many printers are carefully investigating new ways of conducting business, adopting digital technologies to accommodate changing client expectations, because investment choices in such a context can be dangerous. Successful printers are changing their companies to assist clients in channel leveraging and aligning economic and environmental aims.
Inline ink viscosity automation solutions contribute to sustainability goals
Reliable viscosity automation solutions ensure that only minimal and extremely precise amounts of solvents are used for ink viscosity adjustments. When used with an integrated control system and software, it also keeps records of all solvent additions to enable evaluation and optimization of solvent consumption patterns.
Customers using the Rheonics viscosity automation solutions have reported about 40% reduction in solvent consumption and total emissions.
Evidence of impact on sustainability
Reduction in solvent consumption
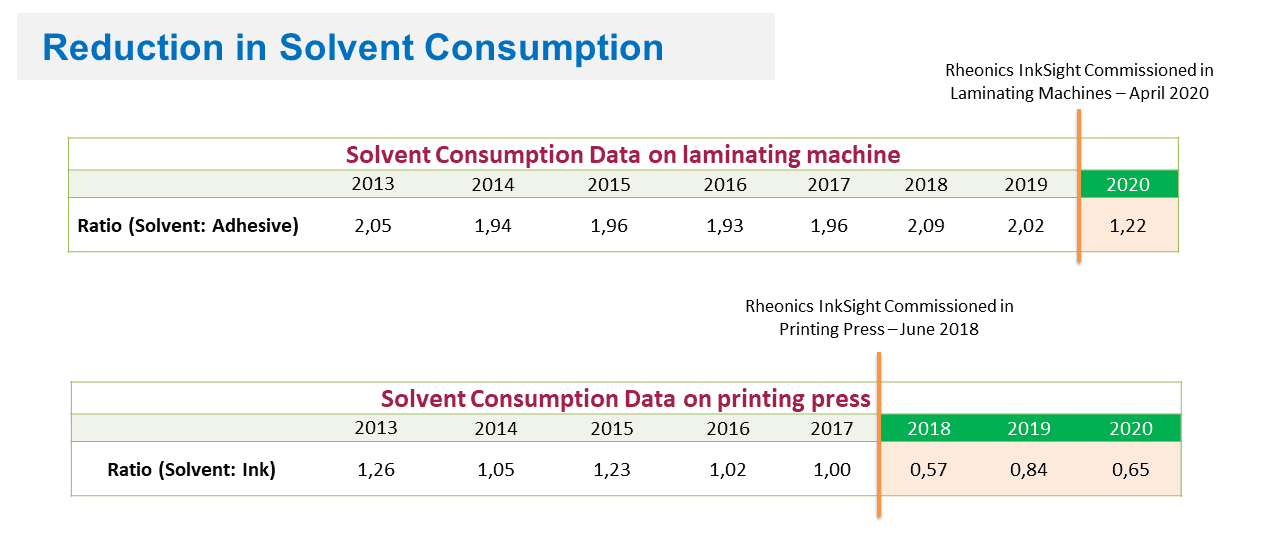
Solvent consumption per unit adhesives & per unit ink data reported by a customer after commissioning of Rheonics InkSight (Source – Maasmond B.V. Netherlands)
Note: There is a ~ 40% reduction in solvent consumption after InkSight system integration in customer application.
Reduction in emissions
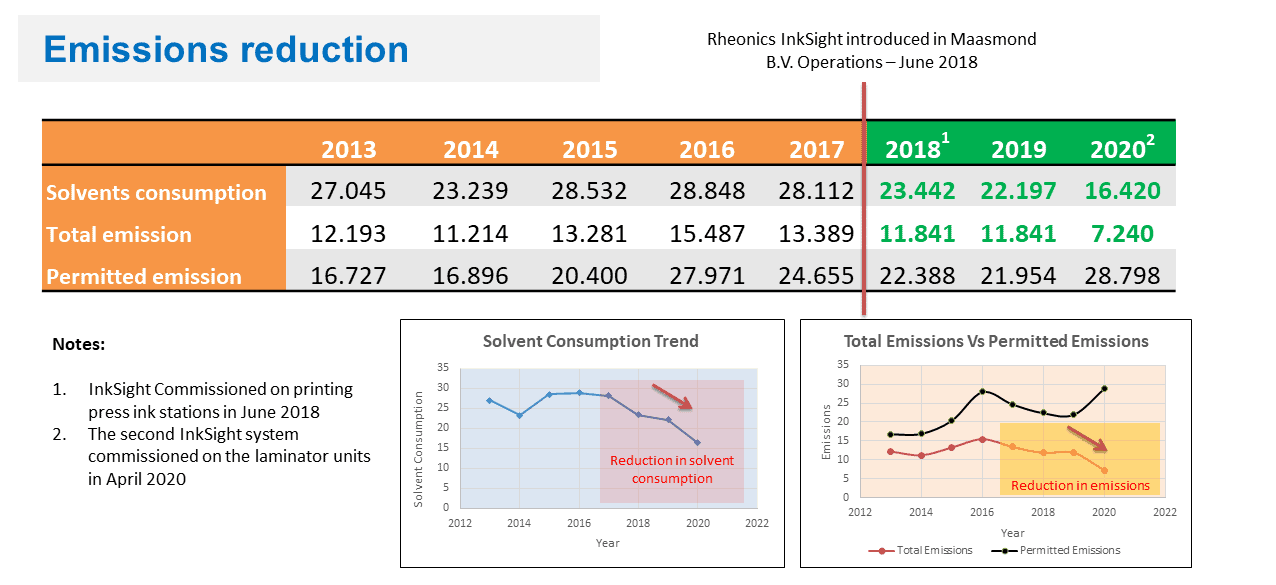
Solvent consumption and emissions data reported by a customer after commissioning of Rheonics InkSight (Source – Maasmond B.V. Netherlands)
Future of printing: Focus on the environment
Roadmap of printing companies calls for safer, environment friendly, sustainable operations.
- Continuous improvement cycles to minimize solvent consumption in printing operations to reduce volatile organic compounds (VOCs) and air pollutants (HAPs)
- Transitioning away from solvent–based inks to water–based inks, since solvent-based inks contain high concentration of VOC and require higher energy in application(drying)
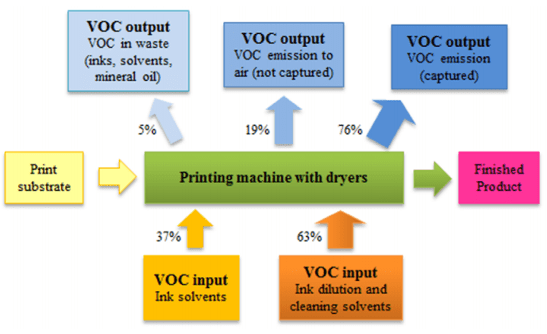
VOC input and output during the printing process. Source: Environmental impact of printing inks and printing process, Journal of Graphic Engineering and Design, Volume 11 (2), 2020. http://doi.org/10.24867/JGED-2020-2-011
Voice of customers: reliable autonomy saves environment & money
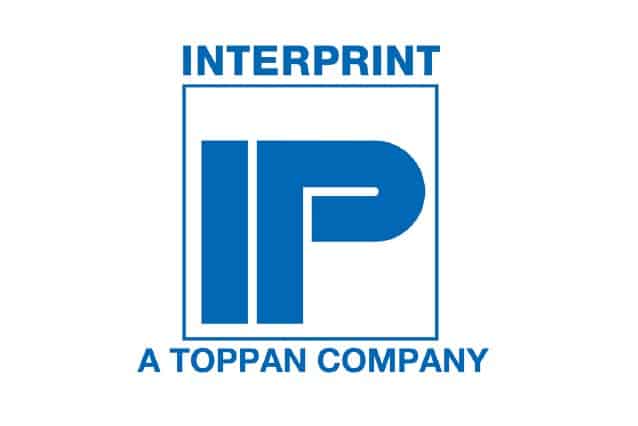
Todd Luman, Manager
“The InkSight sensor held the viscosity over the duration of the entire order within 0.5 cP. The other print stations that were not being controlled the operator had to chase the color and adjust the ink thorough out the run while the print unit the InkSight controller was in ran flawlessly… Time and time again the result were outstanding!”
“we have had several occasions where we did not have a press crew to run the press at night so instead of shutting the press down and washing up we opted to leave the viscosity control system on with the cylinders in the press spinning and the ink circulating through the system. We came in the next morning and we were able to start right back up…” [completely eliminating setup scrap and time]
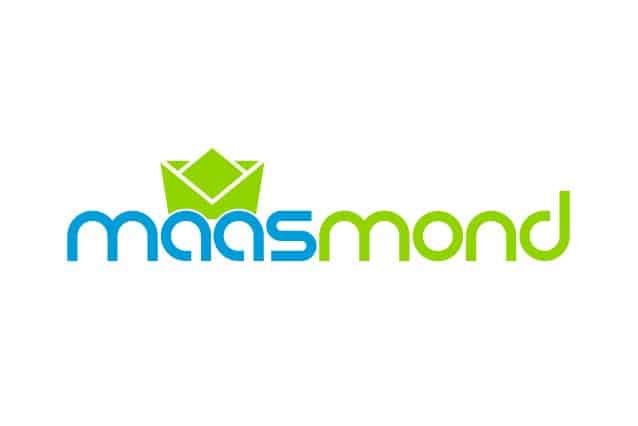
Bert Verweel, Owner
“We have seen the last 2 years that the consumption of solvents decreases, especially in 2020. In that year, the laminator was equipped with the viscosity control of Rheonics, which resulted in a reduction of 21% of ethyl acetate consumption. We also keep a record of emissions since the Dutch government requires us to keep track and proof of it. We have been able to achieve a reduction in our emissions by at least 40% using this system.”
All Rheonics products are designed to withstand harshest process environments, high temperature, high level of shock, vibrations, abrasives & chemicals.
Key user benefits of the RPS InkSight
RPS places the focus on print quality instead of measurement skills.
Achieve best in class print quality, dramatically reduce setup time and optimise use of pigments and solvents. Improve productivity and efficiency through complete automation of color control on your press.
- Single click, intuitive control of ink viscosity
- Reduce setup time and eliminate setup scrap by loading previously saved job configurations, enabling consistent print quality in repeat jobs with minimal efforts for production
- Robust, maintenance free viscosity sensor eliminates need for re-calibration or cleaning by operators
- Better print quality: Tighter, more accurate color density and dE control across the complete run
- Edge over competitors by undertaking higher margin – higher quality print jobs made possible with the RPS InkSight system
Rheonics wins the prestigious Swiss Product Excellence Awards 2021
It’s an incredibly proud moment for all to announce that the Rheonics has been awarded the prestigious 2021 Swiss Product…
Rheonics InkSight Technical Webinar – Color Excellence Through Tight Viscosity Control, a 2021 FTA Technical Innovation Award Winner
Topic Color Excellence Through Tight Viscosity Control, a 2021 FTA Technical Innovation Award Winner Date & Time September 16 @…
FTA Flexo Magazine features Rheonics FTA Technical Innovation Award winning Technology – “Excellence via Viscosity Control”
Flexographic printing focused magazine - Flexo (https://www.flexography.org/flexo-magazine/) publishes an in depth article showcasing the Rheonics SRV viscometers and the RPS…
Rheonics InkSight and SRV technology wins the FTA Technical Innovation Awards 2021
It’s an incredibly proud moment for all of us here at Rheonics to announce that the Rheonics’ InkSight technology has been…