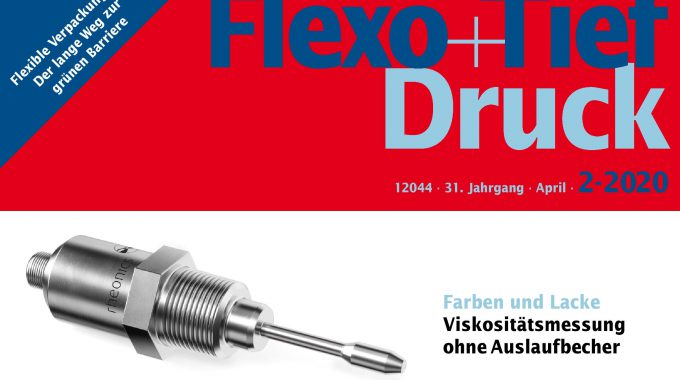
Flexo+Tief Druck publication: Measurement of color viscosity with rheonics viscometers
Introduction
The manual color viscosity measurement with the DIN cup 4 is due to a lack of better alternatives the standard in flexo and gravure industry. Bert Verweel (Maasmond) & Dr. Joe Goodbread (Rheonics) came up with a better solution to address the concerns of the traditional technique.
The Dutch paper manufacturer Maasmond had already tried many different sensor to measure the color viscosity: rotational, falling ball, falling piston and sound wave sensors. All the sensors have one thing in common: You need a DIN viscosity measuring cup for your calibration with a 4 mm outlet opening. This published article discusses a new approach for the regulation of the color viscosity in printing press. Rheonics sensors intend to replace the flow cups with better control on viscosity.
Co-owner of Maasmond, in December 2017 came in contact with Rheonics GmbH to offer him a new sensor.
“After extensive tests, in June 2018, we were preparing to equip all eight printing units of our CI flexographic printing machine with the sensor SRV from Rheonics. However, our printers typically used DIN cup 4 to work. We have therefore developed a formula which are supplied by the SRV sensor measured values (unit: mPaS) and are converted to corresponding expiry times of measuring cup. Today, the printers don’t need even one flow cup to the set point for setting the automatic viscosity control system & to determine an important parameter such as viscosity. ”
– Bert Verweel, Maasmond
The current generation of Flexo and Gravure printing machines with a very high degree of automation and are to reduce set-up time with numerous, automatic assistance systems:
- 100% web inspection
- Print delivery of anilox rollers and printing form, register control
- Inline spectral color measurement
A significant variable in the printing process is the color viscosity. It will still be with a unit measured that determined manually becomes. In many cases automatic viscosity regulator manually calibrated with the measuring cup, since the machine operator does it is used to in “cup seconds” to think. This is often done manually viscosity calibration carried out on the press not performed or only inaccurately. The reasons given are “That is too time consuming”, “The measuring cups are dirty” or “not available”. But the Color viscosity is crucial parameter of the print quality decisively determined. If it is not set correctly, flow behavior varies and the layer thicknesses of the colours. In addition, this leads to a disproportionate increase of color consumption.