Introduction
Polymers have gone from being cheap substitutes for natural products to providing high-quality options for a variety of industrial applications due to their low cost, range of properties (high chemical resistance, high temperature resistance, high strength-to-weight ratio) and ease of processing. They are used as film packaging solid moulded forms for automobile body parts, TV cabinets, aircraft parts, foams for coffee cups and refrigerator insulation, fibers for clothing and carpets, adhesives, rubber for tires and tubing, paints and other coatings and a lot of other applications.
Polymer extrusion is extremely energy intensive, and the real-time monitoring of energy consumption and melt quality has become extremely necessary to meet new carbon regulations and survive in the highly competitive plastics market.
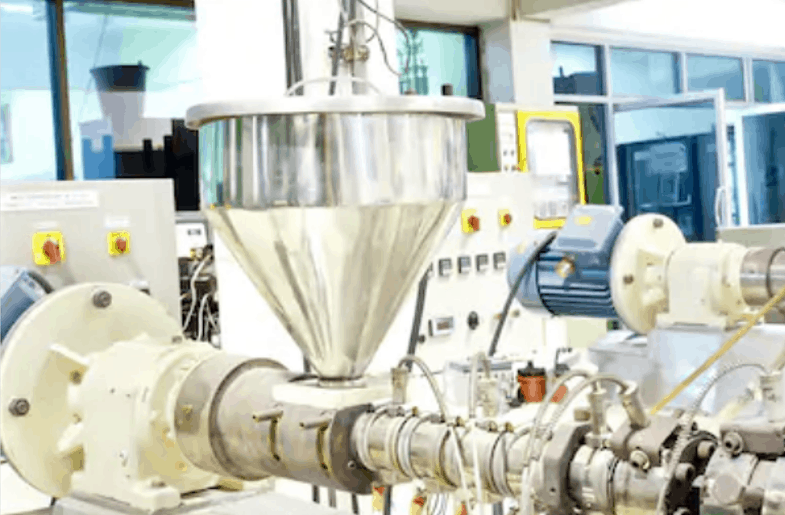
Application
Polymers undergo injection moulding, compression moulding, or extrusion – all of which require forcing a polymer into a shape. The processing is however energy-intensive. In UK, the electricity costs for plastics processing amounts roughly to £350 million per annum. A reduction in electricity usage would result in huge savings and significant reduction in environmental burden.
The energy consumed during the polymer processing can be divided into two aspects: the high-level energy management system and the low-level machinery control. For the high-level energy management system, around 30% reduction in energy use can be achieved by process management and maintenance. Without the right process management, non-optimal operating setting like thermal heating, cooling and the processing speed in case of polymer extrusion process contribute to enormous energy wastage.
The density and viscosity of polymer melts are very important physicochemical parameters in a polymer manufacturing process. They are very significant factors affecting the production cost and profitability of the manufacturing process. Polymers undergo injection moulding, compression moulding, or extrusion – all of which require forcing a polymer into a shape.
In-line characterization of materials is showing an increased popularity among researchers working to improve the performance of many existing manufacturing processes as well as new processes. The benefits associated with the application of these techniques can be directly related to improved quality and reduced production costs. Rheology measurements can be used for material characterisation, determination of processability and as input data for computer simulations. Rheology has advantages over other methods because of its sensitivity to certain aspects of the structure such as high molecular weight tail and branching. In many instances, rheological characterization is a lot faster than its counterparts.
In the extrusion process, product density is most critical factor affecting production costs and overall profitability of the manufacturing process. A reduction in density reduces raw material costs. However, if the product density is kept too low, it degrades mechanical properties and geometrical accuracy. Therefore, a critical balance is essential in order to lower material costs while maintaining adequate strength and accuracy. Density of PVC foam can be controlled by varying the type and amount of compound additives, processing parameters (temperature, screw speed) or both.
The main purpose of adjusting operating settings continuously is to guarantee a consistent melt quality. Research has shown that the melt viscosity is probably the best indicator of melt quality (Cogswell, 1981). For more viscous materials, more force is to be provided and adjustment of other conditions be made, like temperature. Manufacturers must carefully understand this information to ensure proper conditions and best use of resources. For optimizing the operating settings, a real-time monitoring of melt viscosity is required.
Challenges
Single-screw and twin-screw extrusion are the most widely used extrusion techniques. Plastic granules are pushed by a screw moving from the feed zone to the die, and granules melt with heat from shear stress and barrel heating.
Application related
Most polymeric materials exhibit extremely complicated behaviour, particularly in case of polymer melts. The application demands measurements in very difficult conditions – at high pressure (50-100 MPa) and high temperature (about 150-300°C). In HPHT, there is high risk of accuracy and reliability issues.
Problems with process monitoring with motor power consumption
Few plastic processing companies monitor motor power consumption of the extruder motor to investigate melt stability, final product quality and also energy efficiency. However, there are few challenges with this technique:
- Installation of power meters for each extruder is expensive, and mathematical models based on process settings might be a better alternative
- Existing models are highly dependent on the geometry of extruder and polymer materials, it is difficult to use the same model on different use-case without re-training
Problems with process monitoring with melt pressure
In the industry, the melt-pressure near the screw tip is usually accepted as the main indicator of melt quality. Few limitations with this technique:
- The pressure is known to be proportional to the screw speed, however it is also slightly affected by the melt temperature, screw geometry and the polymer material being processed.
- Unstable melt pressure causes fluctuations to the throughput and variations in the final product quality.
Limitations of traditional viscosity measurement techniques
The rheological behaviour of most polymeric materials is quite complex. The viscosity is both shear and thermal history dependent. Often, the polymer viscosity is measured off-line. A sample of polymer compound is melted and put into a special capillary tube (glass viscometer) or by incorporating a capillary tube mounted parallel to the extruder in case of online measurements. Both techniques involve long time delays resulting from the time required for the melt to flow through the transit lines and the capillary. In some cases, viscometers are mounted on the extrusion lines which measure the stress on the die wall by measuring the pressure drop along a slit or capillary and the flow rate is measured by an extra flow meter. Although these methods produce viscosity measurements more relevant to the extrusion process, the flow meter often disturbs the melt stream thus altering the original flow characteristics.
Conventional mechanical and electro-mechanical viscometers designed primarily for laboratory measurements are difficult to integrate into the control and monitoring environment. The current methodology of testing in off-site labs in not optimal and expensive due to the logistical challenges of shipping and high fixed costs. The complex changes taking place inside an engine or compressor often cannot be determined from a routine oil sample because the data represented by such a sample simply reflects a snapshot of the oil’s condition at the time the sample is taken and the conventional instrumentation may be affected by shear rate, temperature and other variables.
Why is real-time online rheology measurement important?
There are several motivational benefits from cost, environmental, and logistical perspectives to on-line real time viscosity monitoring in polymer production process. It is an excellent tool for materials characterization and miscellaneous troubleshooting purposes. Key benefits are as follows:
Economic and logistical advantages, reduced production costs: On line viscosity analysis would reduce the number of samples sent to off-site laboratories, and the involved costs. Continuous outputs from onsite analyses would also reduce shipping labour/costs and sampling error.
Rheology measurements can help troubleshoot during polymer processing and reduce errors:
- Sharkskin: Materials that are not very shear thinning are prone to sharkskin at relatively lower throughput rates. The viscosity information of material at the processing temperature (in the lip region) can be essential to reduce shear stress, increase die temperature or use additives that promote slippage and avert the defect.
- Bubble instability in film blowing: Low melt strength of material can cause this defect. Extensional viscosity and/or melt strength values of materials can be used to compare bubble stability of different materials and choose the right material for the application. Cooling can help lower bubble temperature and thereby increase melt strength.
- Poor blending of two polymers: When the viscosity difference between two polymers to be blended is large (e.g. over 5 times), blending is extremely difficult because the shear stress exerted by the matrix on the higher viscosity dispersed phase is not large enough to cause breakup. Corrective action would be to use a matrix of higher viscosity.
Improved final product quality: The rheological measurements from the raw material and the final product can characterize product properties like impact resistance, optics, warpage, brittleness etc. Continuous monitoring can help detect any modification or degradation that might occur during the extrusion process.
Reduced Energy use: For optimizing the operating settings, a real-time monitoring of melt viscosity is required. Optimal use of resources and electricity in production with tight control over the processes is ensured with real-time inline rheological measurements.
Increased worker safety: Other factors such as health and safety requirements for working with solvents, consideration for the environment and the need for specialist personnel to carry out these tests (which must be carried out in a laboratory) add to the high popularity of the solvent-free method.
Faster response times: In-situ viscosity (and density) analysis would reduce/eliminate the delay between sampling and receiving a response from the laboratory.
Environment: Utilisation of resources can be maximised through on-line monitoring systems, thus resulting in reduced wastage which is good for the environment. Enhanced sustainability through reduced emissions.
Rheonics' Solutions
Automated, real time in-line viscosity measurement is critical to polymer production. Rheonics offers the following solutions, based on a balanced torsional resonator, for process control and optimisation in the polymer processing:
- In-line Viscosity measurements: Rheonics’ SRV is a is a wide range, in-line viscosity measurement device with inbuilt fluid temperature measurement and is capable of detecting viscosity changes within any process stream in real time.
- In-line Viscosity and Density measurements: Rheonics’ SRD is an in-line simultaneous density and viscosity measurement instrument with inbuilt fluid temperature measurement. If density measurement is important for your operations, SRD is the best sensor to cater to your needs, with operational capabilities similar to the SRV along with accurate density measurements.
Automated in-line viscosity measurement through SRV or an SRD eliminates the variations in sample taking and lab techniques which are used for viscosity measurement by the traditional methods. The sensor is located in-line so that it continuously measures the viscosity (and density in case of SRD). Using an SRV/SRD for process monitoring can improve productivity and increase profit margins. Both the sensors have a compact form factor for simple OEM and retrofit installation. They require no maintenance or re-configurations. Both the sensors offer accurate, repeatable results no matter how or where they are mounted, without any need for special chambers, rubber seals or mechanical protection. Using no consumables, SRV and SRD are extremely easy to operate.
Compact form factor, no moving parts and require no maintenance
Rheonics’ SRV and SRD have a very small form factor for simple OEM and retrofit installation. They enable easy integration in any process stream. They are easy to clean and require no maintenance or re-configurations. They have a small footprint enabling Inline installation in any process line, avoiding any additional space or adapter requirement.
High stability and insensitive to mounting conditions: Any configuration possible
Rheonics SRV and SRD use unique patented co-axial resonator, in which two ends of the sensors twist in opposite directions, cancelling out reaction torques on their mounting and hence making them completely insensitive to mounting conditions and flow rates. These sensors can easily cope up with regular relocation. Sensor element sits directly in the fluid, with no special housing or protective cage required.
Instant accurate readouts on process conditions – Complete system overview and predictive control
Rheonics’ software is powerful, intuitive and convenient to use. Real-time viscosity can be monitored on a computer. Multiple sensors are managed from a single dashboard spread across the factory floor. No effect of pressure pulsation from pumping on sensor operation or measurement accuracy. Unaffected by shock, vibrations or flow conditions.
Easy installation and no reconfigurations/recalibrations needed
Replace sensors without replacing or reprogramming electronics, drop-in replacements for both sensor and electronics without any firmware updates or calibration coefficient changes. Easy mounting. Screws into ¾” NPT thread in ink line fitting. No chambers, O-ring seals or gaskets. Easily removed for cleaning or inspection. SRV available with flange and tri-clamp connection for easy mounting and dis-mounting.
Low power consumption
24V DC power supply with less than 0.1 A current draw during normal operation
Fast response time and temperature compensated viscosity
Ultra-fast and robust electronics, combined with comprehensive computational models, make Rheonics devices one of the fastest and most accurate in the industry. SRV and SRD give real time, accurate viscosity (and density for SRD) measurements every second and are not affected by flow rate variations!
Wide operational capabilities
Rheonics’ instruments are built to make measurements in the most challenging conditions. SRV has the widest operational range in the market for inline process viscometer:
- Pressure range up to 5000 psi
- Temperature range from -40 up to 200°C
- Viscosity range: 0.5 cP up to 50,000 cP
SRD: Single instrument, triple function – Viscosity, Temperature and Density
Rheonics’ SRD is a unique product that replaces three different instruments for viscosity, density and temperature measurements. It eliminates the difficulty of co-locating three different instruments and delivers extremely accurate and repeatable measurements in harshest of conditions.
Clean in place (CIP)
SRV (and SRD) monitors the clean-up of lines by monitoring the viscosity (and density) of the solvent during the cleaning phase. Any small residue is detected by the sensor, enabling the operator to decide when the line is clean for purpose. Alternatively, SRV provides information to the automated cleaning system to ensure full and repeatable cleaning between runs, unlike in case of glass capillaries.
Superior sensor design and technology
Sophisticated, patented 3rd generation electronics drive these sensors and evaluate their response. SRV and SRD are available with industry standard process connections like ¾” NPT and 1” Tri-clamp allowing operators to replace an existing temperature sensor in their process line with SRV/SRD giving highly valuable and actionable process fluid information like viscosity besides an accurate measurement of temperature using an in-build Pt1000 (DIN EN 60751 Class AA, A, B available).
Electronics built to fit your needs
Available in both an explosion-proof transmitter housing and a small-form factor DIN rail mount, the sensor electronics enables easy integration into process pipelines and inside equipment cabinets of machines.
Easy to integrate
Multiple Analog and digital communication methods implemented in the sensor electronics makes connecting to industrial PLC and control systems straightforward and simple.
ATEX & IECEx Compliance
Rheonics offers intrinsically safe sensors certified by ATEX and IECEx for use in hazardous environments. These sensors comply with the essential health and safety requirements relating to the design and construction of equipment and protective systems intended for use in potentially explosive atmospheres.
The intrinsically safe and explosion proof certifications held by Rheonics also allows for customization of an existing sensor, allowing our customers to avoid the time and costs associated with identifying and testing an alternative. Custom sensors can be provided for applications that require one unit up to thousands of units; with lead-times of weeks versus months.
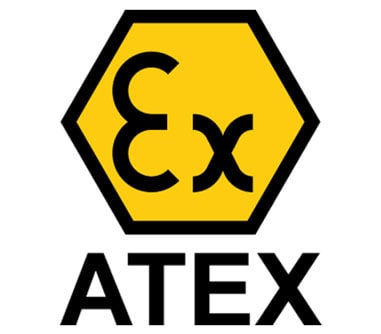
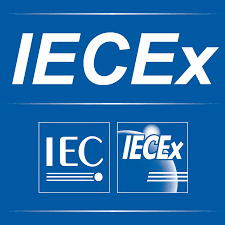
Implementation
Directly install the sensor to your process stream to do real time viscosity and density measurements. No bypass line is required: the sensor can be immersed in-line, flow rate and vibrations do not affect the measurement stability and accuracy. Optimize decision making process by providing repeated, consecutive, and consistent tests on the fluid.
Rheonics Instrument Selection
Rheonics designs, manufactures and markets innovative fluid sensing and monitoring systems. Precision built in Switzerland, Rheonics’ in-line viscometers has the sensitivity demanded by the application and the reliability needed to survive in a harsh operating environment. Stable results – even under adverse flow conditions. No effect of pressure drop or flow rate. It is equally well suited to quality control measurements in the laboratory.
Suggested product(s) for the Application
• Wide viscosity range – monitor the complete process
• Repeatable measurements in both newtonian and non-newtonian fluids, single phase and multi-phase fluids
• All metal (316L Stainless Steel) construction
• Built in fluid temperature measurement
• Compact form-factor for simple installation in existing process lines
• Easy to clean, no maintenance or re-configurations needed
• Single instrument for process density, viscosity and temperature measurement
• Repeatable measurements in both newtonian and non-newtonian fluids, single phase and multi-phase fluids
• All metal (316L Stainless Steel) construction
• Built in fluid temperature measurement
• Compact form-factor for simple installation in existing pipes
• Easy to clean, no maintenance or re-configurations needed