Capsules are a solid oral dosage form used for the delivery of medical drugs, vitamins, minerals, and other health-related ingredients. They are widely preferred for their portability and accurate dosing, especially compared to less practical options like liquid, powder, or paste formulations. As consumer demand increases, capsules have become a preferred format across both pharmaceutical and nutraceutical markets. Among these, gelatin capsules remain the most popular, with gelatin used as the key gelling agent.
Table of Content
- Introduction
-
The importance of viscosity and density in Gelatin capsule
production - Key applications
- Process Conditions and Best Practices
-
Rheonics Type-SR Inline Sensors
Overview - References
Introduction
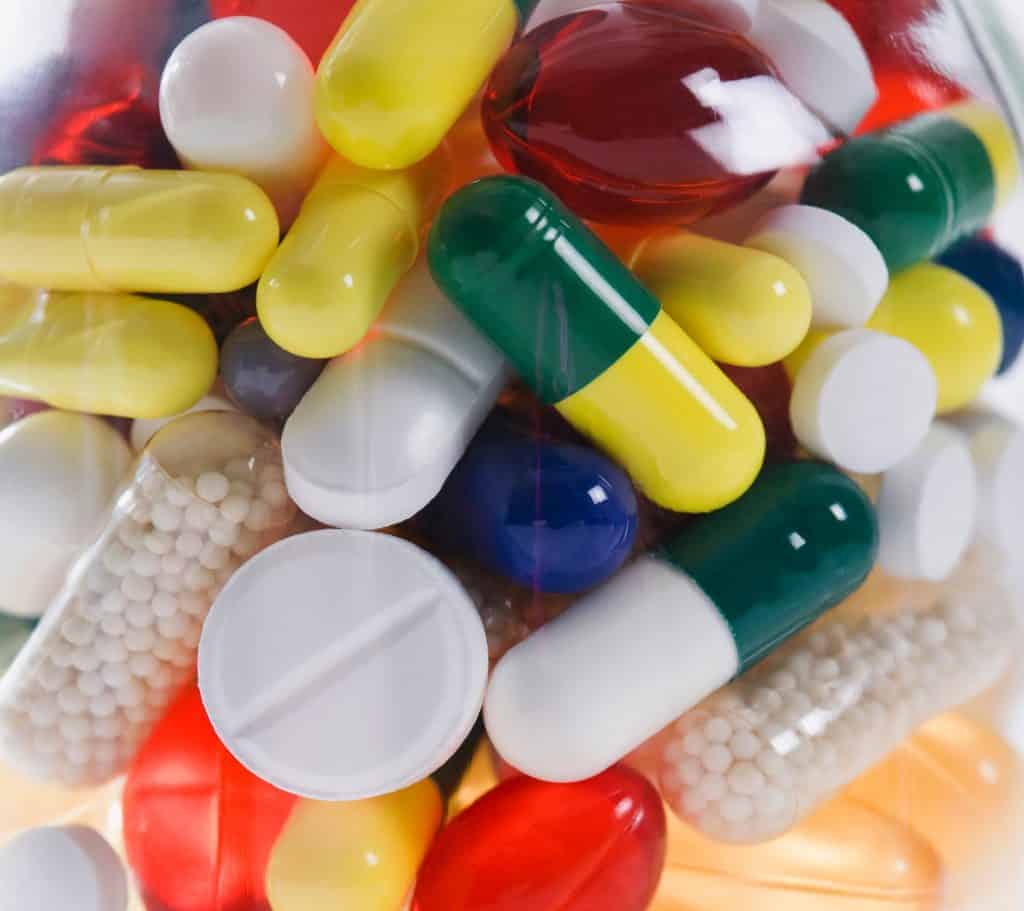
Figure 1 – Capsules for dosage of medical drugs, vitamins, minerals, and other health-related ingredients
Gelatin capsules are produced in two main forms: hard capsules (hardcaps) and soft gelatin capsules (softgels), each requiring distinct manufacturing techniques. Both methods require precise control over gelatin properties to ensure capsule integrity, dosing accuracy, and reliable performance in automated equipment.
Usually, traditional lab-based sampling is used, but these provide occasional insights that are not able to capture real-time changes in fluid properties. On the other hand, inline measurements give continuous and real-time visibility of the process, allowing to have faster control response.
The importance of viscosity and density in Gelatin capsule production
SRV Inline Viscosity Meter
Rheonics SRV measures a wide range of viscosity and temperature in real-time and is suitable for installation in tanks to monitor mixing processes and in pipelines for continuous measurement of flowing fluid. Rheonics SRV is compatible with high-speed mixing processes and is unaffected by the presence of bubbles in the fluid or external vibrations.
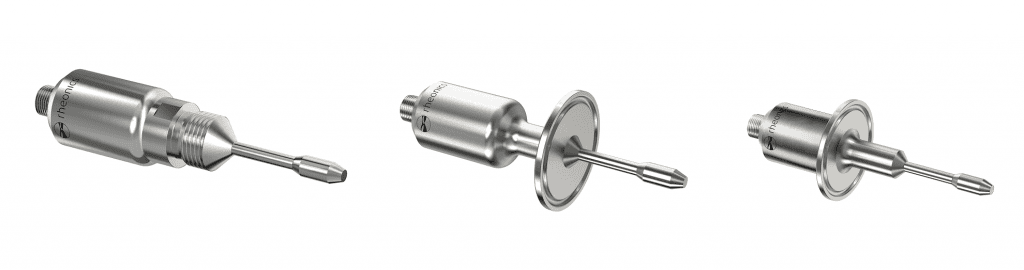
Figure 2 – Rheonics SRV sensor Versatility in installation options
Viscosity measures a fluid’s resistance to flow. In capsule manufacturing, it affects shell formation, ribbon consistency, and sealing integrity of capsules. Viscosity monitoring directly affects:
- Wall Thickness and Coating Control: In hard capsules, viscosity indicates how much gelatin attaches to mold pins, impacting shell thickness and uniformity.
- Product Consistency: For both hard and soft capsules, stable viscosity ensures uniform capsule dimensions and weight.
- Defect and Leakage Prevention: Many physical defects, like star ends, poor seals, and leakage, are caused by improper viscosity monitoring.
SRD Inline Density and Viscosity Meter
Rheonics SRD adds density to viscosity and temperature measurement in real time. It is best suited for installation in pipelines and tanks with a constant and low mixing speed. Adding density to the measurements allows further fluid concentration calculations; however, it has a narrower measurement viscosity range compared to the SRV, and high concentrations of bubbles can add noise to readings due to the density measurement. SRD is also not affected by external vibrations.
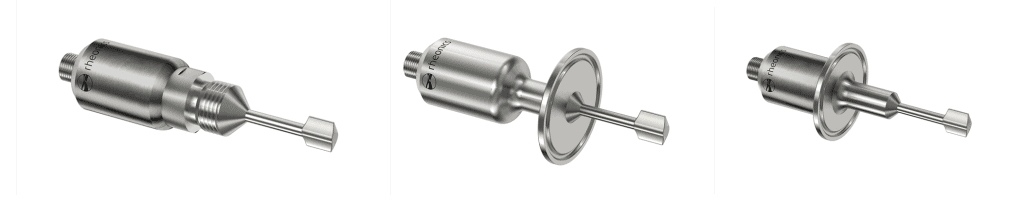
Figure 3 – Rheonics SRD sensor Versatility in installation options
Density refers to the mass of a material per unit volume. In gelatin capsule production, it is directly related to the concentration and formulation of the fill material or gelatin solution. Density monitoring directly affects:
-
Formulation Accuracy: In gelatin solutions, density reflects the concentration of gelatin and additives. Major deviations may indicate ingredient errors or air entrainment.
- Dosage Control in Fill Materials: For softgel capsules, the density of the liquid fill formulation directly impacts dose accuracy and content uniformity.
Key applications
As mentioned before, gelatin capsules are produced in two main forms, hard capsules (hardcaps) and soft gelatin capsules (softgels), each requiring distinct manufacturing techniques.
Hard Gelatin Capsules: Manufacturing by Dip Coating

Figure 4 – Hard gelatin capsules (Hardcaps)
Figure 4 shows some hard gelatin capsules, or hardcaps, which are composed of two cylindrical shells: a body and a slightly wider cap that fits over it. These capsules are produced through a process illustrated in Figure 5, where stainless steel pins are dipped into a gelatin solution to form the capsule halves. After drying and trimming, the two halves are joined and later filled with powdered or granulated drugs.
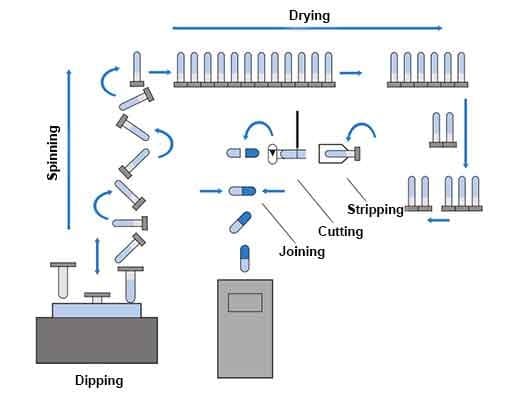
Figure 5 – Hardcaps manufacturing process diagram
Gelatin Solution Preparation and Dip Coating
The process begins with gelatin being dissolved in demineralized water and heated to produce a concentrated gelatin solution. Colourants and pigments are also added to achieve the final appearance of the capsule. During this stage, the viscosity of the gelatin solution after mixing is a critical parameter that directly affects downstream manufacturing quality and batch consistency.
Figure 6 indicates how Rheonics sensors can be installed in the mixing tank to continuously monitor viscosity and temperature with the SRV, and density, viscosity, and temperature with the SRD. Alternatively, if available, these can be placed in a recirculation line to ensure homogeneity during mixing.
Once the target viscosity and concentration are reached, the solution is transferred to the dipping section. As also shown in Figure 6, after mixing, SRV or SRD sensors can also be installed in the outlet or transport line to monitor the solution during transfer. The gelatin bath can also be equipped with sensors to ensure batch consistency or verify quality during this process. During dipping, stainless steel pins on rotating bars are fully submerged in the gelatin solution to form the capsule halves.
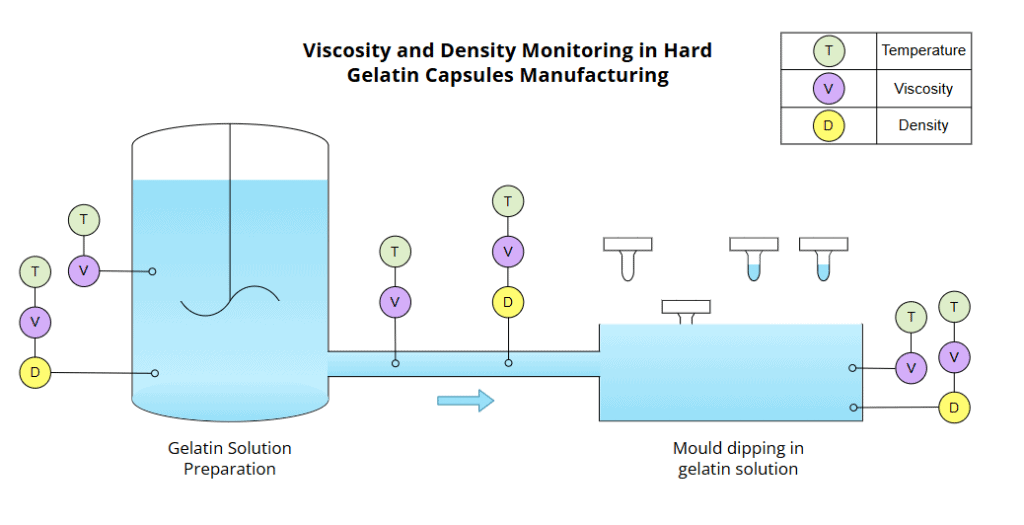
Figure 6 – Hard Gelatin Capsules manufacturing
Monitoring gelatin viscosity and density is essential to achieve uniform coating thickness and minimize variability in hard capsule production.
Post-Coating Stages
After dip coating, the capsule shells undergo several finishing steps to ensure quality and usability:
- Drying: Coated pins pass through a controlled-temperature and humidity furnace to remove moisture and set the gelatin.
- Stripping & Trimming: The dried capsule halves are removed from the pins, trimmed to uniform length, and automatically joined into complete capsules.
- Printing: Key information such as dosage, branding, or identification is printed on the capsule surface.
- Testing: Capsules are subjected to quality control checks to ensure proper size, strength, and shelf life.
- Packaging: Finally, the capsules are conventionally packaged for easy handling and distribution.
Softgel Capsules: Manufacturing by Rotary Die Process

Figure 7 – Soft gelatin capsules (Softgels)
Soft gelatin capsules, or softgels, are single-piece, hermetically sealed shells designed to contain liquid or semi-solid fills, as illustrated in Figure 7. They are typically produced using the rotary die encapsulation process, shown in Figure 8, a continuous operation in which two gelatin ribbons are formed, filled with the desired formulation, and sealed simultaneously between rotating dies. This method enables high production efficiency and consistent capsule quality, but it requires precise control of gelatin preparation and fill product to ensure proper sealing, uniform shape, and accurate dosing.
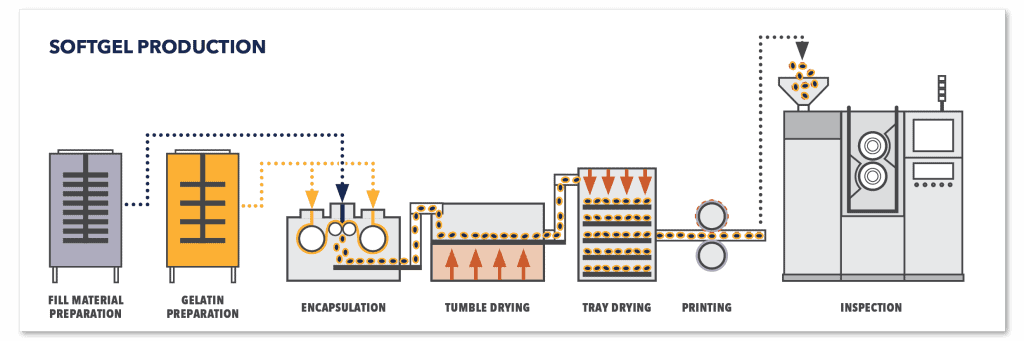
Figure 8 – Softgels manufacturing process diagram
Gelatin Solution Preparation and Encapsulation by Rotary Die Process
Similar to hardcaps, softgel production begins with the preparation of a molten gelatin mass with purified water, but with the addition of plasticizers, such as glycerin or sorbitol, to give the particular elasticity required by Softgel covers. The formulation may also include colorants, opacifiers, or flavoring agents.
Figure 9 shows how Rheonics sensors can be installed in the mixing tank to continuously monitor viscosity and temperature with the SRV, and density, viscosity, and temperature with the SRD. These sensors can also be installed in recirculation loops to maintain formulation homogeneity or in outlet lines to monitor conditions during transfer to the encapsulation machine.
Once the desired gelatin properties are achieved, the solution is transferred to a casting deposit and then cast onto a large, cooled rotating drum to form a uniform ribbon. The same process is repeated on the opposite side to form a second uniform ribbon. As also shown in Figure 9, Rheonics sensors can be positioned in the casting deposits system to verify gelatin mass consistency before ribbon formation and sealing.
At the end, both ribbons converge at the rotary die, where they are filled with liquid or semi-solid material and hermetically sealed into capsules in a single continuous step. Sensors can also be installed independently to monitor fill product to check correct formulation or consistency to ensure proper injection and dosage into the rotary die.
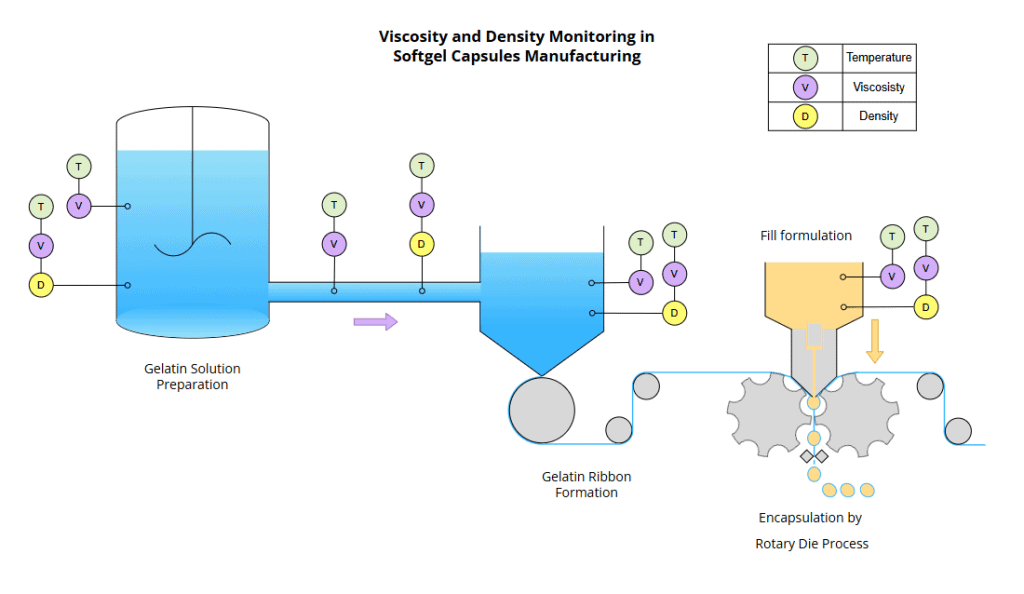
Figure 9 – Soft Gelatin Capsules manufacturing
Given the sensitivity of the rotary die process to gelatin behavior, real-time monitoring of viscosity and density is critical to ensure reliable sealing, prevent leakage, and maintain consistent capsule dimensions in softgel manufacturing.
Post-Encapsulation Stages
- Drying: The freshly formed softgels require drying to remove excess moisture and achieve their final hardness and stability.
- Testing: Capsules are subjected to quality control checks to ensure proper size, strength, and shelf life.
- Packaging: Finally, the capsules are conventionally packaged for easy handling and distribution.
Process Conditions and Best Practices
Before indicating some considerations for these applications, it is important to mention some key installation considerations for both Rheonics sensors, SRV and SRD.These have the same resonator across all their variants, with installation requirements related to the sensing area of the probes (shadowed red areas, Figure 10), which are:
SRV Installation Requirements
- The area should be free of deposits or obstructions
- The area should be completely immersed in the fluid of interest.
SRD Additional Installation Requirements
In addition to the two SRV requirements above, the SRD sensor has two additional considerations:
- Maintain thermal stability when the fluid and the external environment have a temperature gradient greater than 15°C. (Only for SRD, more information here: Maintaining the SRD’s temperature balance for high-density accuracy)
- Align the sensing tip with the fluid flow direction as shown in Figure 11. (Only for SRD, more information here: SRD fluid end orientation)
These conditions can be reviewed in more detail in the next article, SRV and SRD Suitable Installations.
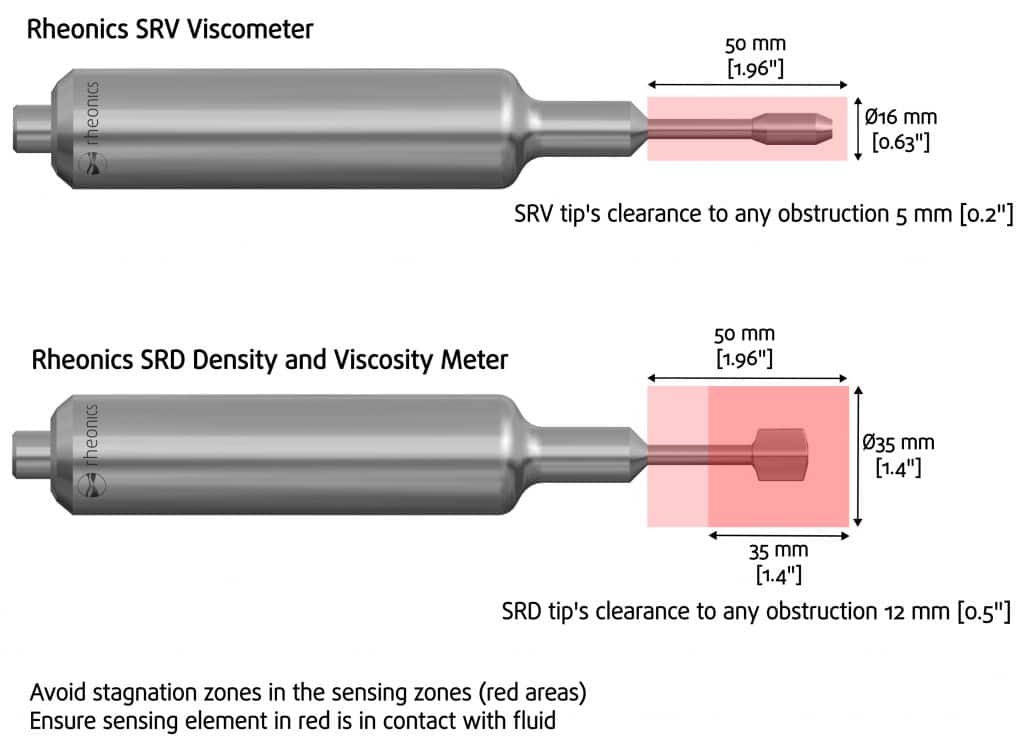
Figure 10 – Type-SR sensors Installation considerations

Figure 11 – SRD recommended tip orientation
As an example inFigure 12, an SRV long-insertion probe is shown installed in a gelatin solution preparation tank to monitor viscosity in real-time. Follow this article for more tank installation examples and drawings, Density and Viscosity Sensor installation in tank roofs or lids.
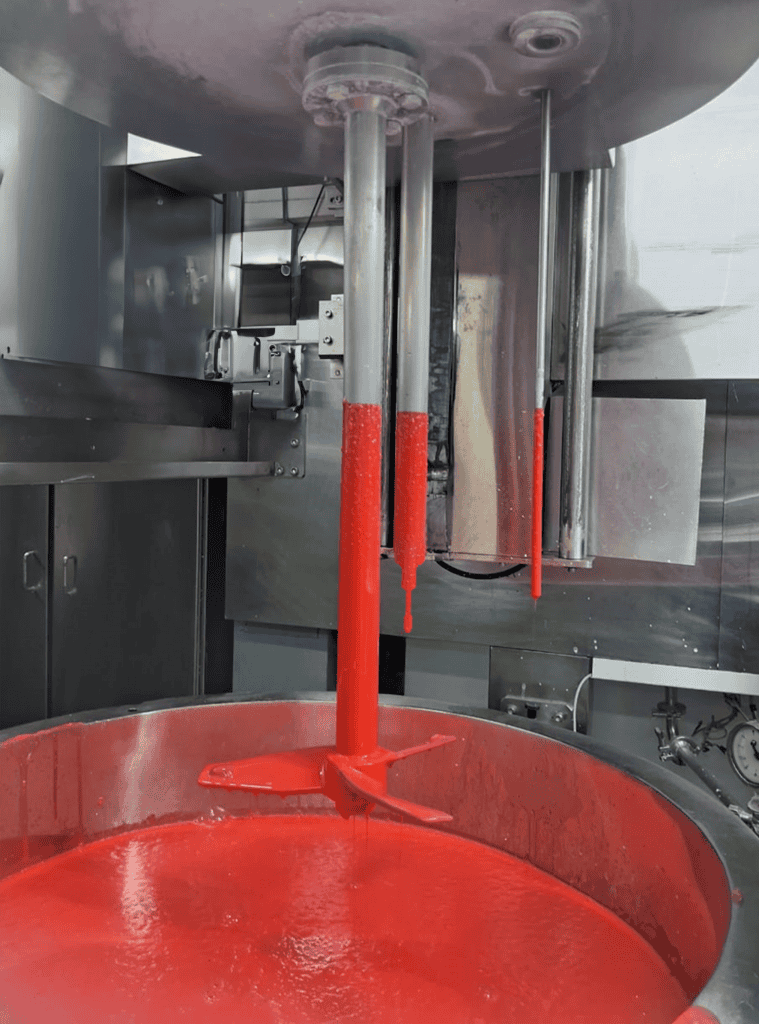
Figure 12 – SRV sensor on Gelatin Solution tank
The following considerations are important to follow for good performance:
Cleaning Process and CIP/SIP Procedures
Periodic cleaning of the SRV or SRD sensor might be necessary to ensure long-term accuracy. Gelatin solutions tend to form sediment or solid deposits that can adhere to the sensor tip and distort readings, especially in high-viscosity conditions. For more information on cleaning procedures, see How to clean your Rheonics probe?.
Additionally, the mechanical design of the sensors is hygienic by default, making the sensors suitable for Clean-in-Place (CIP) and Sterilize-in-Place (SIP) procedures. An optional hygienic certification is also available.
Moving Parts and Obstructions
Gelatin solutions are often prepared in mixing tanks with mechanical components such as stirring arms or paddles. It is essential to ensure sufficient clearance between the sensor and any moving parts to avoid interference or damage.
Particles and Bubbles
Rheonics sensors can handle the presence of micron-sized soft particles with minimal impact on measurement accuracy. Any signal noise introduced by these particles is effectively filtered by the sensor electronics. However, larger particles may cause noise or spikes in the readings and should be considered when analyzing measurement trends.
Regarding bubbles, the SRV sensor is not affected by the presence of bubbles in the fluid. In contrast, the SRD sensor, which measures both viscosity and density, is not recommended to be used with high concentrations of bubbles since this may lead to measurement inaccuracies, as the density measurement is more sensitive to these.
Rheonics Type-SR Inline Sensors Overview
Rheonics Type-SR sensors (SRV and SRD) measure viscosity, density, and temperature in line for process monitoring and control. The SRV measures viscosity and temperature, while the SRD provides density in addition.
These sensors are factory calibrated and do not need recalibration over their operational lifetime. However, clients may require calibration or verification for instruments used in their industry as part of their Quality Control. Optional re-adjustments or offset corrections can be performed if needed to match specific references. For more details, see Calibration of inline process viscometer SRV in field and factory.
Rheonics sensors technology is based on a balanced torsional resonator (BTR). This patented technology has a significant advantage over competitors since it allows the sensors to be compact, lightweight, and unaffected by external vibrations.
Rheonics SRV and SRD sensors are proven solutions in pharmaceutical and nutraceutical manufacturing applications. In gelatin capsule production, they provide real-time measurements of critical parameters for both hard and soft capsule processes. Continuous inline measurements improve batch-to-batch consistency, reduce waste, and enhance process stability.
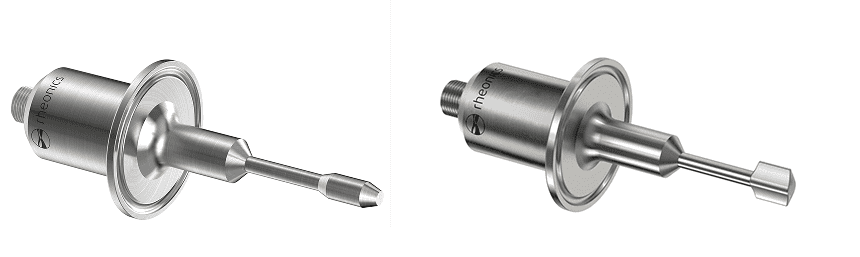
Figure 13 – Rheonics Inline Viscometer (SRV), and Density and Viscosity Meter (SRD) short probe variants with 1.5” Tri-Clamp connection
Hygienic certification
Type-SR probes, as previously mentioned, come with a mechanical hygienic design by default, making them suitable for sanitary applications. If needed, probes can also be supplied with hygienic certification from recognized organizations, such as EHEDG and 3-A.
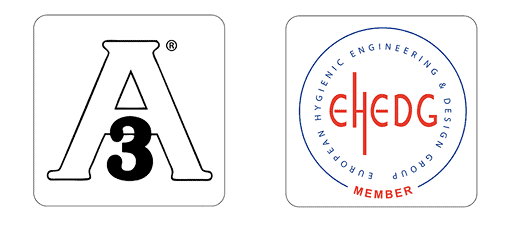
Figure 14 – Hygienic certifications available for Rheonics Sensors
For more details, visit Rheonics hygienic and sanitary installation.
Accesories
Rheonics offers dedicated hygienic adapters. For example:
Weldolet for G1/2” Type-SR sensors
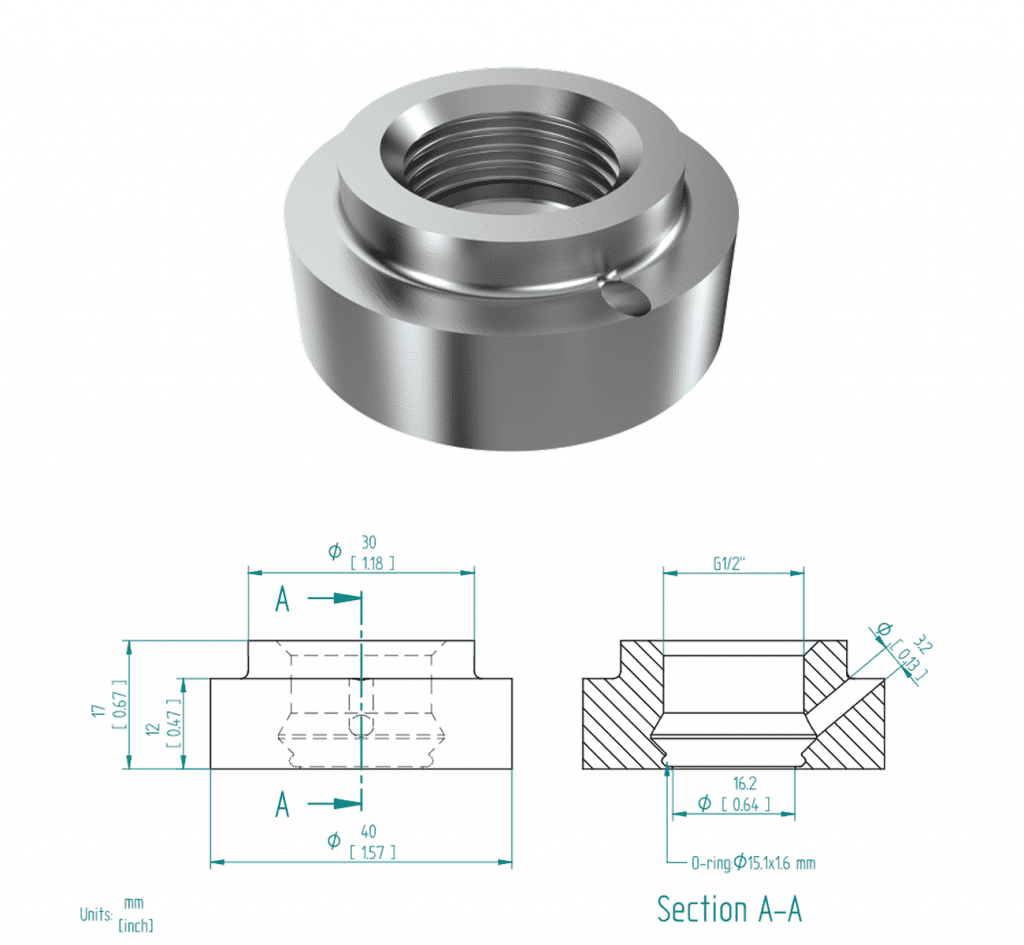
Figure 15 – HAW-12G-OTK Dimensions
Hygienic adapter weldolet for the SRV-X1-12G and SRD-X1-12G, sensors with a 1/2” G thread process connection. For more information, see HAW-12G-OTK.
HPHT Hygienic Flow Cell
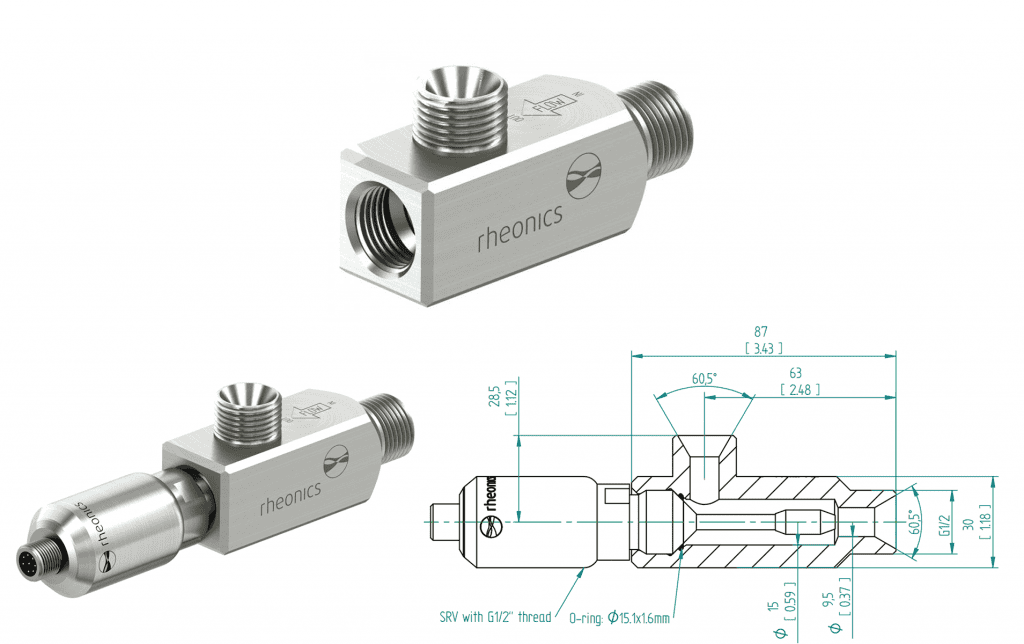
Figure 16 – SRV-X1-12G Dimensions
Inline hygienic flow cell for high-pressure and temperature applications, available only for the SRV-X1-12G, viscometer with a G 1/2” thread process connection.For more information, see HPT-12G.
FET-XXT
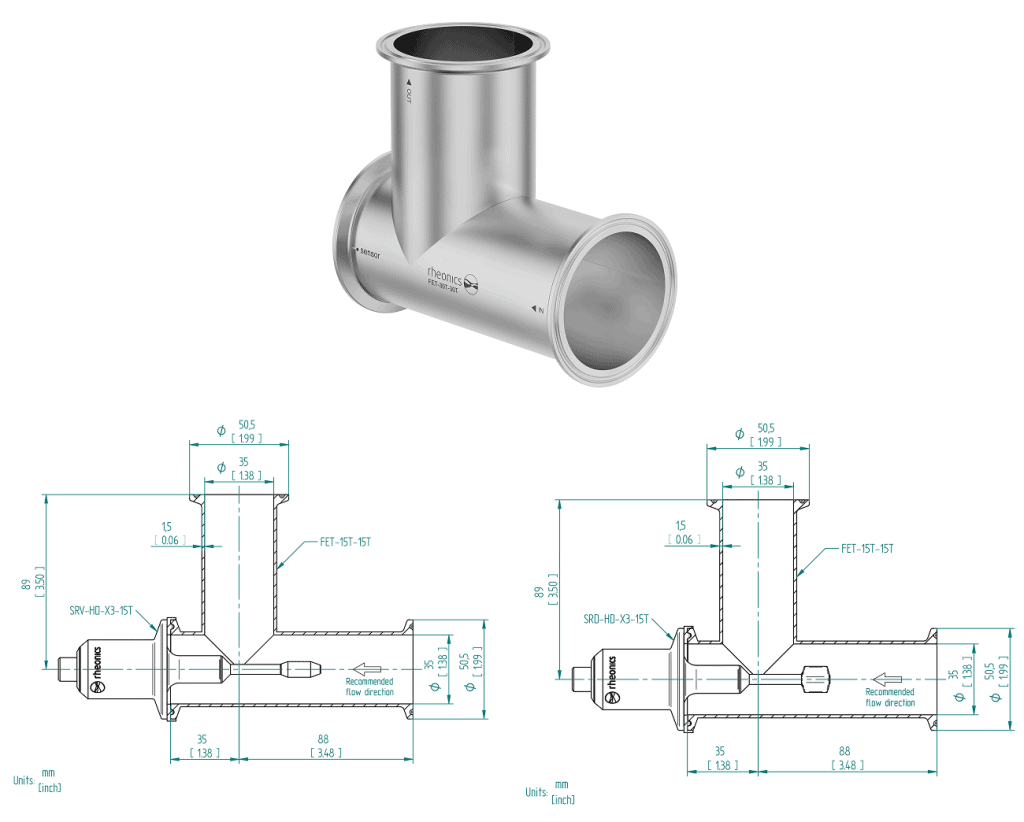
Figure 17 – FET-XXT Dimensions
A line of elbow or tee cell with a shortened port for a Tri-Clamp installation for the SRV-X3 and SRD-X3, sensors with a Tri-Clamp process connection. It is offered in different sizes, like 1.5”, 2”, 3”, 4”, and others. Rheonics delivers it with a Clamp and Clamp Seal for the sensor probe. For more information, see FET-XXT.
These accessories enable reliable installation and performance in hygienic systems. For more accessory options, please follow Rheonics Sensor Accessories.
References
[1] Gelita. “Gelatin Capsules – All you need to know”. https://www.gelita.com/es/node/1252
[2] Gelita. “Hard Capsules – All you need to know”. https://www.gelita.com/en/Hard-Capsules
[3] Adinath International. “Hard Gelatin Capsule Manufacturing Process Step by Step”. https://www.adinath.co.in/hard-gelatin-capsule-step-by-step-manufacturing-process/
[4] Pharma Excipients. “The Ultimate Guide to Soft Gelatin Capsule Manufacturing”. https://www-pharmaexcipients-com.translate.goog/news/gelatin-capsule-manufacturing/?_x_tr_sl=en&_x_tr_tl=es&_x_tr_hl=es&_x_tr_pto=tc
[5] Sensum. “Reasons for the most common Softgel defects”. https://www.sensum.eu/posts/common-softgel-capsule-defects/