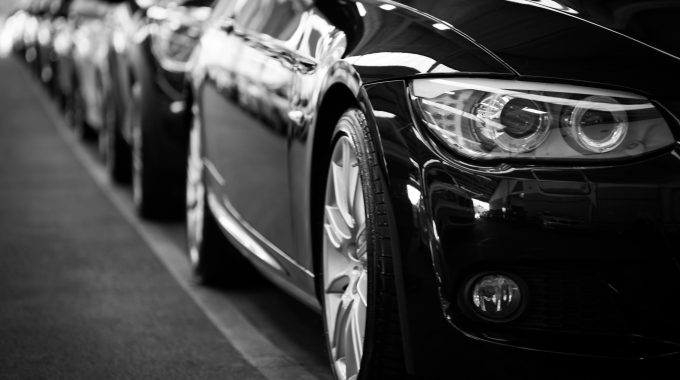
Solutions for automotive painting and coating quality control and optimization
Process Challenges
Automotive companies and coaters recognize the need to monitor viscosity, but making that measurement outside laboratory has challenged process engineers and quality departments over the years. Existing laboratory viscometers are of little value in process environments because viscosity is directly affected by temperature, shear rate and other variables that are very different off-line from what they are in-line. Measuring viscosity on factory floor with traditional instrumentation like flow cups, dip cups and bubble viscometers is slow, labour intensive, time consuming and prone to inaccuracies.
In spray painting applications, some companies use thermal management systems to keep point-of-application at a determined optimal temperature to achieve constant paint viscosity. But, temperature is not the only factor affecting viscosity. Shear rate, flow conditions, pressure and other variables can affect viscosity changes as well. Temperature controlled systems also have long installation times and a large footprint.
Application insights
Broad and significant issues with viscosity management in automotive painting include:
- Paint Transfer Efficiency
- Coating Deposition
- Finished surface qualities
- Environmental and workplace safety
To ensure consistent high-quality coating, the change in paint viscosity through-out the process stream is monitored in real time, making measurements from a baseline rather than simply measuring absolute values, and making viscosity adjustments by adjusting solvents and temperature to keep it within specified limits.