Fluid cooling systems are an essential component in data center technology. As the power density of data center processors increases, coolant performance becomes a critical link in the reliability and lifetime of processors and other essential components.
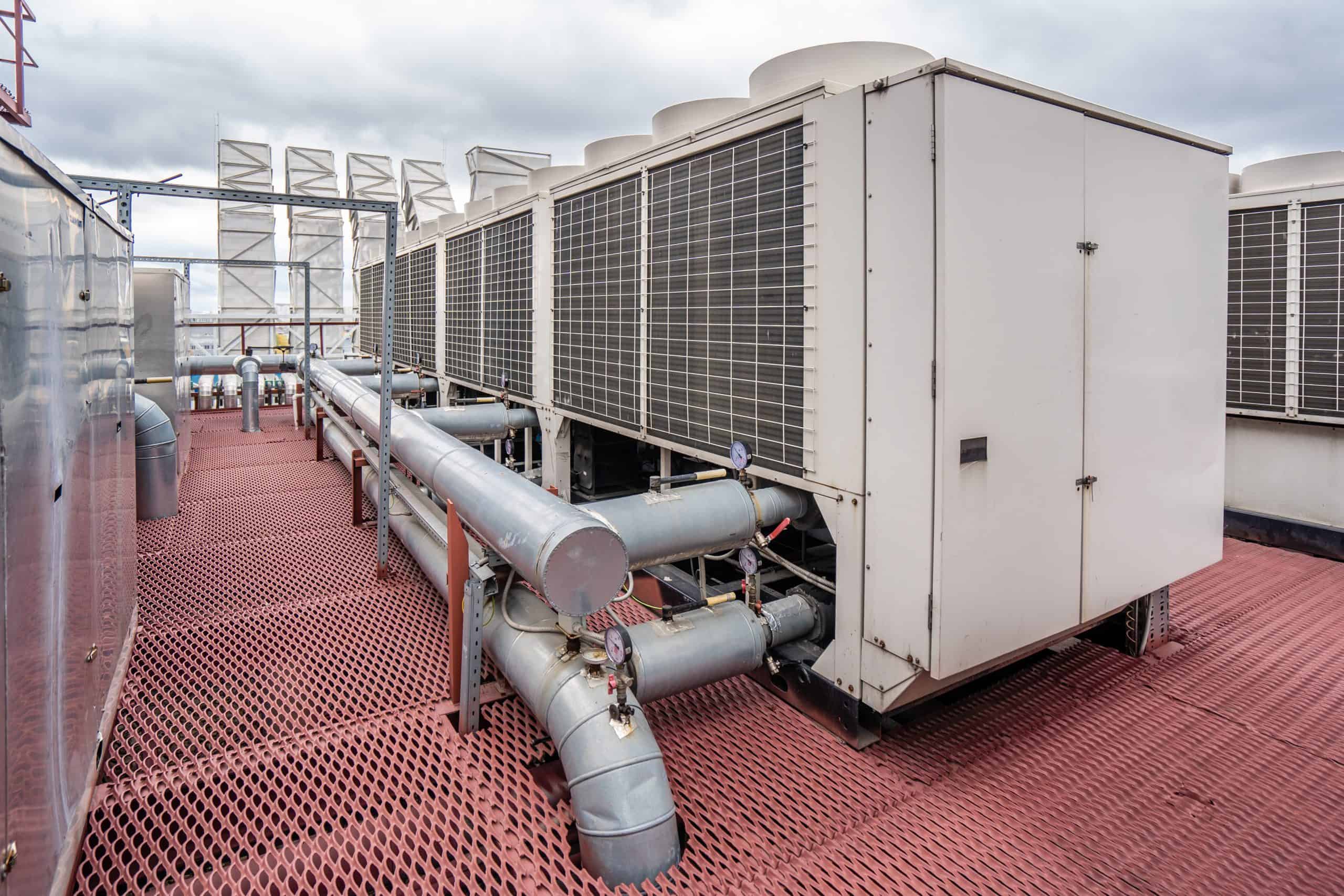
Figure 1: Refrigerant Machine.
Table of Content
- Measurements of glycol-based cooling systems
- Glycol concentration monitoring with SRV
- Detection of deposition and coolant degradation
- Rheonics advantages over other systems
- Outlook
- Communication and Integration
1. Measurements of glycol-based cooling systems
The most widely used coolants are solutions of glycols and water, together with degradation and corrosion inhibitors to prevent coolant failures and corrosion of electronic and piping systems. Therefore, accurate and sensitive monitoring of glycol-based coolant condition is a crucial link to ensure the reliability and stability of equipment.
There are several methods currently used for monitoring of coolant condition. They measure two critical aspects of coolant properties:
- Glycol concentration can be measured by:
- Viscosity, which varies strongly with concentration
- Optical refractometry, which measures the index of refraction of the coolant, which is also dependent on glycol concentration
- Glycol degradation can be measured by:
- Laboratory chemical analysis to detect expected degradation products
- pH measurements to detect potentially corrosive acids in degradation products
- Electrical conductivity measurements to detect ionic degradation products
Optimal monitoring of coolant condition should be a continuous online process whose reliability and stability should be maintained without calibration over the lifetime of the sensor.
Rheonics SRV is a compact, robust inline viscosity sensor that can reliably monitor viscosity and temperature of coolants directly in the coolant line. It can also detect and quantify material deposited by coolant, that give an early indication of corrosion products, biofilm formation, and other degradation processes.
Figure 2: Dimensions SRV Inline Viscometer G1/2″ Thread.
Figure 3: SRV mounted in HPT-12G for coolant line
SRV is exceptionally stable. Its factory calibration remains valid over its 25+ years of lifetime, therefore never requiring recalibration. Its resolution is better than 1% of viscosity reading. Reproducibility of readings is also better than 1%, making it perfect for tracking both short- and long term trends in coolant properties with a high degree of confidence. SRV incorporates a high accuracy temperature sensor immersed directly in the coolant that enables robust and accurate temperature compensation of viscosity readings. SRV further incorporates a self-checking function that indicates if the sensor has accumulated any deposits on its surface, from, for instance, corrosion products or adherent biofilms that can indicate chemical or biological degradation. Deposition checking functions independently of viscosity measurement, and can provide additional, crucial information about coolant condition.
2. Glycol concentration monitoring with SRV
SRV can give an accurate and stable measurement of glycol concentration, one of the most critical properties of a coolant. Maintaining optimal glycol concentration strikes the desired balance between heat transfer performance and corrosion and freezing protection. Early warnings of changes in glycol concentration are essential to the reliability of delicate data center systems.The following chart shows the viscosity of propylene glycol – water mixtures for a wide range of glycol concentrations and temperatures:
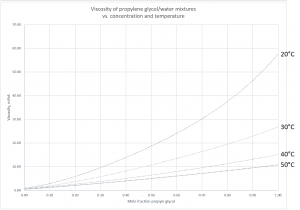
The SRV’s ability to resolve very small changes in viscosity, supported by its temperature compensation capabilities, means that it can supply accurate and stable measurements of glycol concentration despite possible large temperature variations.
3. Detection of deposition and coolant degradation
The stability of the SRV makes it a sensitive detector of any changes in the fluid properties. Both degradation and concentration changes can influence the SRV viscosity readings.As knowledge is accumulated about the effects of degradation on SRV readings, smart algorithms can be developed to differentiate the signatures of the most probably changes to the coolant properties.
4. Rheonics advantages over other systems
The SRV delivers continuous viscosity measurements without operator attention. Laboratory analysis is time- and resource intensive, and can only deliver periodic results, often with a long time lag between sample extraction and final laboratory report.
The SRV is intrinsically stable over years of operation. Electrochemical processes like conductivity and pH measurement can be done online, but stability and accuracy of sensors can be compromised by deposition and degradation of the sensors themselves.
The SRV factory calibration remains unchanged over the 25+ years of lifetime of sensor. Electrochemical sensors need frequent calibration to ensure reliable measurements
The SRV temperature compensation is built into the sensor; conventional evaluation methods usually require an auxiliary temperature measurement in order to compensate for temperature-dependence of the measurement.
5. Outlook
The SRV is capable of detecting changes in the concentration of glycol in coolant systems. It is also capable of detecting deposits caused by contaminants, biofilms, and corrosion products.
As information becomes available about the performance of SRV in actual coolant monitoring environments, the Rheonics support team is positioned to develop smart alert systems to warn of changes in coolant properties
Continuous measurements under varying conditions make extensive data available about the sensor’s response to changes. When changes are seen in the SRV output and deposit detection, this can trigger laboratory tests to determine the source of these changes. Taken together with the SRV data signature, these will provide inputs to machine learning algorithms that can more accurately evaluate trends in viscosity and deposition that, in turn, can provide a more accurate understanding of coolant performance and lifetime.
6. Communication and Integration
Rheonics SRV sensor includes the powerful electronics called SME – Sensor Module Electronics. Rheonics SME handles the measured data from the probe, transforms it to readable values, and transmits it through multiple industrial protocols, such as the analog 4-20 mA signals and more robust digital protocols like Profinet, Modbus RTU and TCP, Ethernet/IP, HART, etc. which makes the sensor very easy to integrate into local monitoring or control systems.
Clients can rely on the Rheonics Integration Team for assistance with communication settings and, if needed, remote configuration, to ensure a smooth integration.